Choosing a forging components manufacturer for your product can be long and complex. Currently, there are so many options of forging companies to choose from that you can become overwhelmed by the choosing process. Finding a great product at a reasonable price is possible, mainly when you have found the right partner that has shown results in their prior work.
There are numerous factors to consider when choosing the right forging parts manufacturer, and it’s not a decision you should take lightly. But by taking your time and asking the right questions, you can find a partner to help you craft the solution you need. And given the importance of forging parts in so many industries, making sure that you work with an experienced partner is just a critical step in the process.
An Overview of Forging
Forgings are metal parts created by shaping metal using localized compressive forces. They are typically made from steel, aluminum, and other metals that can withstand high-stress levels. Forgings are used in various applications because they offer several benefits over other metal parts. For example, forgings:
- Are more potent and more durable than castings or other types of metal parts.
- Can be made to precise tolerances, ensuring a consistent and high-quality end product.
- It can be designed to incorporate complex shapes and features that would be difficult or impossible to achieve with other manufacturing methods.
There are several different methods of forging, including hammer forging, press forging, and roll forging. The specific method will depend on the size and shape of the part being made and the type of metal used. Forgings are used in various industries, including aerospace, automotive, construction, and energy. They are found in products such as aircraft landing gear, car engines, and crankshafts, as well as in infrastructures such as bridges and buildings.
Forging Benefits
When strength and durability are critical, forged products have a significant advantage over die cast parts. A fundamental difference between forging and casting is that when metal is forged, its structural grain changes. Recrystallizing forged parts can significantly improve impact and shear strength over raw or cast materials. This is a time-saving method because expensive alloys are no longer needed. Some other added advantages are :
- Fatigue Strength : Forged components are less likely to fatigue, meaning they can withstand severe operating conditions longer than other parts.
- Tensile Strength : University of Toledo researchers discovered that forged parts have 26% higher tensile strength than similar cast iron parts. As a result, forged steel parts can withstand much greater stresses without fracturing.
- Versatility : Castings and forgings are both approaches to shaping metal into a desired form. The way they accomplish this process, however, is different.
- Uniformity : Due to the higher degree of uniformity and structural integrity, forged components generally have longer lifespans than cast ones.
Forging Disadvantages
- Forged metal surfaces tend to oxidize quickly due to high temperatures
- Secondary operations are complex during hot forging
- Capital costs are higher





- Must follow rigorous personal and equipment safety procedures.
- Limited to simple forms
- Close tolerances are hard to keep
Forging Industrial Applications
Many industries, including aerospace and aviation, increasingly use forged metal components. For example, forged components are used in aerospace engines and landing gear. Forged parts can be made stronger and stiffer than cast ones, so they’re often used for structural applications like car engines and frames. They also tend to have better damping properties than cast or machined parts, which are sometimes used in suspension systems like transmissions.
Industries involved with boat or railroad construction, including shipbuilding and repair, often find forged parts the best choice for their products. They’re designed to ensure that the parts last as long as possible under heavy loads in harsh operating conditions. Forged metal makes them durable, unlike brittle castings.
Forged fittings and valves are commonly used for heavy-pressure applications because of their strength and durability. The oil and gas industry has unique equipment needs that must be met to keep operations running smoothly.
Machined custom metal parts are more durable and require less downtime for replacement. Heavy loads and harsh operating conditions can cause equipment to fail in mining and construction. Forged parts can be strong enough to withstand these forces.
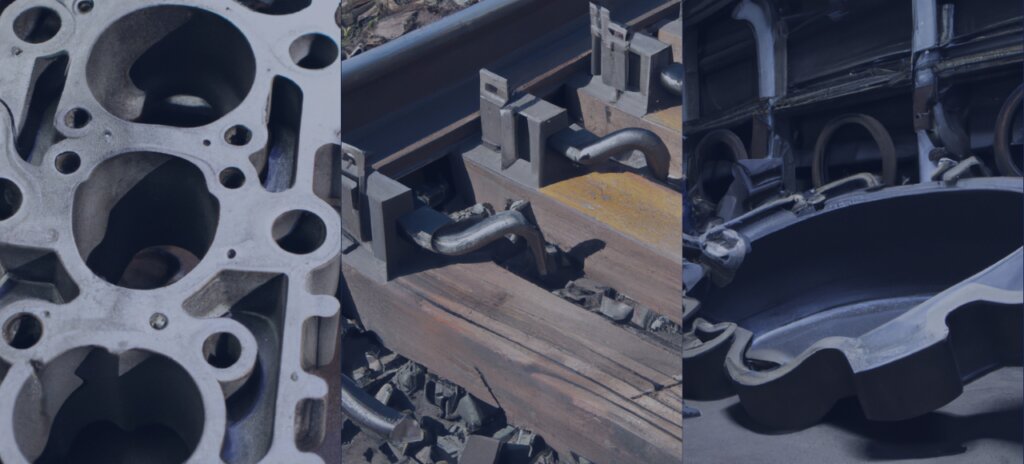
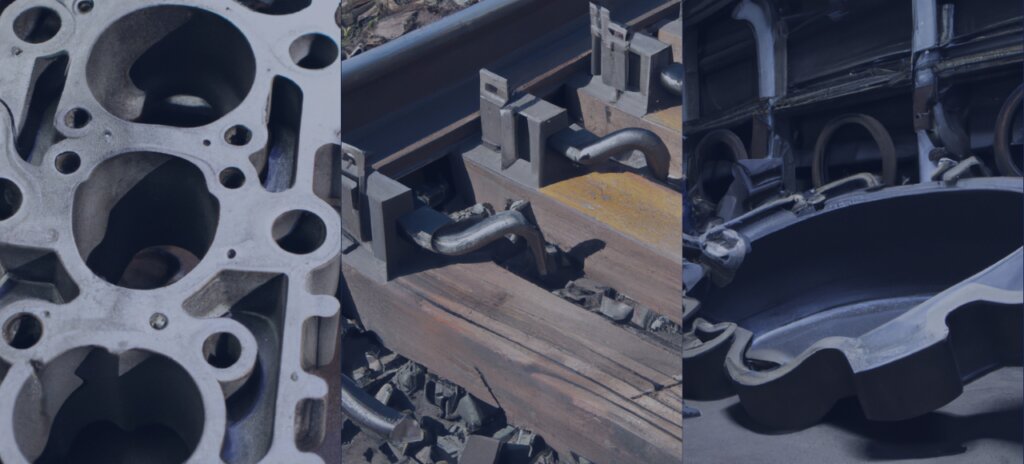
If you are looking for solid forging components manufacturing partners, consider partnering with Zetwerk. At Zetwerk, we look to form long-term partnerships and combine our forging expertise with your vision to create the forging parts you need. We have extensive forging experience and offer a wide range of forging services tailored to our customers’ needs. With unlimited creative possibilities, while staying within budget, we have the expertise to create the perfect forged components for you. Call us today to find out how we can help you meet your metalworking needs.




