A forging press is a machine that uses a vertical ram to apply controlled pressure to a die holding a workpiece. This forging manufacturing process is similar to drop forging but uses slow pressure instead of repeated blows. The slow movement of the ram allows it to penetrate deeper into the workpiece, causing the workpiece to undergo uniform plastic deformation.
Zetwerk provides high-quality Forged Components and all secondary operations.
Submit the relevant part drawings, 3D files, and other information by clicking on the button below.





There are mainly four types of forging press
- Mechanical Forging Press: A mechanical forging press is a stationary device that uses controlled, even pressure. In contrast to a hammer press, which uses one strike and then quits, it uses several hits in a single lengthy motion. This increases efficiency and safety by removing the need to draw the ram out between each strike. Mechanical Forging Industrial presses squeeze metal sheets and rods between dies with a lot of mechanical force in order to mold them into specific forms. The metal is heated, sandwiched between two cold dies, and compressed using ram force until the desired shape is achieved. Plastic deformation, a lower necessity for draught angles, less energy consumption, and longer tool lives due to less stress placed on the die are all advantages of mechanical presses versus power hammers.
- Screw Forging Press: The screw forging press is said when rotational energy from a flywheel is converted into a ram’s linear motion to power the screw press. This ram action ceases deforming the workpiece (forging) when all of its energy has been used. It is possible to employ a variety of different techniques to achieve your goals, including using a variety of different types of specialized software. Vertically mounted driving wheels are continuously turned in friction drive machinery. The driving wheels are moved to allow one wheel to engage the primary flywheel and propel the ram downward during a downstroke. The flywheel, screw, and ram stop when all of the energy is expended during the stroke.
- Heading Forging Press: The heading forging press is also called an Upsetter, and in the forging process known as upsetting, elevated rims or flanges are created on the workpieces. This procedure involves hammering (upsetting) the workpiece between two cavities of dies that move vertically and horizontally to reduce the metal cross-section. The punch moves forward during the upsetting process and pushes the stock into the die cavities. The movable die glides to its open position at roughly 60% of its full stroke, releasing the forging. Afterward, the forging may be moved to the downtake for additional operation during one heat cycle. Specific forgings require many passes after upsetting to be finished. They are put into a metal tote box for cooling and shipment after being fed via the machine’s throat.
- Hydraulic Forging Press: Hydraulic presses use high-pressure hydraulic systems to exert pressure on a piston’s top. The press then depresses downward, giving the object being held inside the die the required profile. Ingots, billets, components, or formed materials can be stamped or rolled into various forms and lengths using hydraulic presses. The forging hydraulic press extremely idle ram speed and prolonged die contact time prevent it from being utilized frequently for conventional hot forging. To forge materials other than steel, they are generally employed in open die forge applications and for vast tonnage applications. Because of their sluggish squeezing operation, these machines are perfect for isothermal forging applications.
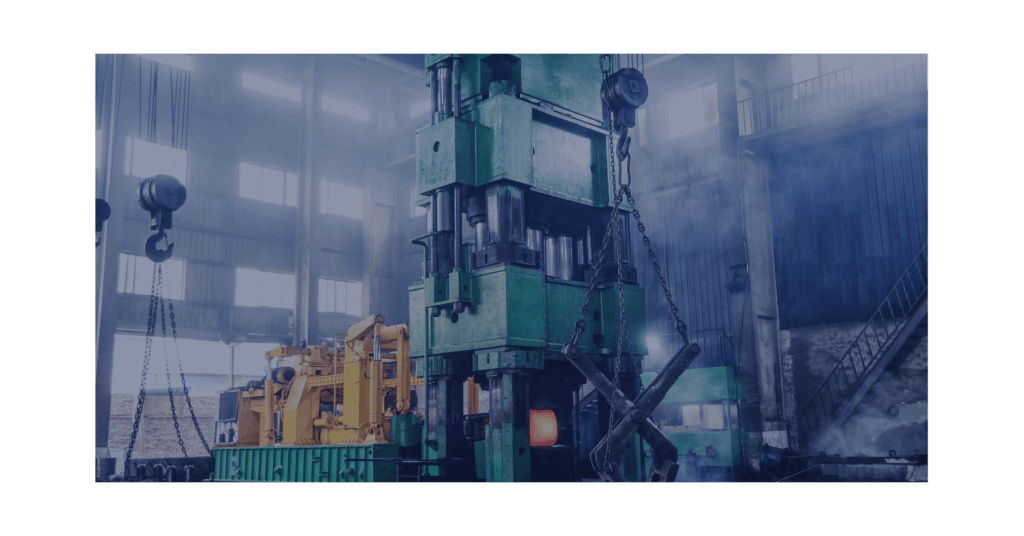
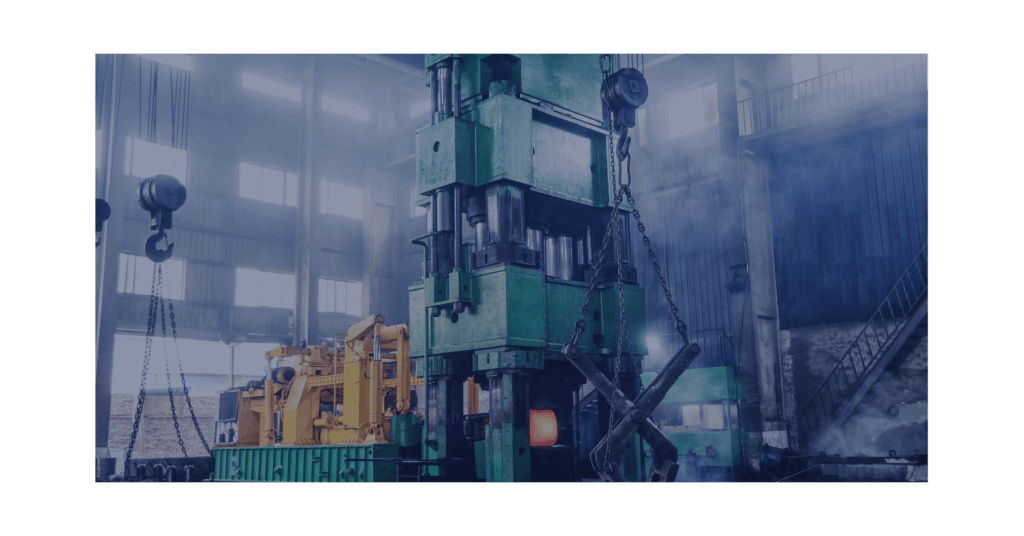
Why is high pressure required in Steel Forgings?
Compression at incredibly high pressure is used to create custom steel forging. It has less surface porosity, a finer grain structure, a higher tensile strength, a longer fatigue life/strength, and more excellent flexibility than any other steel processing. It is harder and more durable than cast iron and different kinds of steel.
The process involved in Steel Forging
Strength and ductility are both benefits of steel forging. Steel has a lower melting point than other materials, making it more brittle and prone to breakage. Due to the plasticity of steel, when properly processed, steel forging enables a billet of steel to be permanently formed without cracking. To heat the steel to a suitable temperature for forging, a forge furnace, forge oven, or induction heating system is required. The heat cycle and the deformation process result in metallic recrystallization and grain refining. The forged steel product that results from this is strengthened, especially in terms of impact toughness.
How does Aluminum Forging help in Cost Reduction?
Custom aluminum forging uses quick infrared heating to produce high-quality parts, which improves the material’s physical qualities, such as fatigue life, fine-grain aluminum metallurgy, and hardenability. To further enhance these traits, the process has created exclusive techniques and procedures that also help reduce costs by less energy consumption. The pure form of aluminum is worn when corrosion resistance is more important than strength in the final product. The best-known feature of aluminum is how lightweight it is. Due to a microscopic oxide coating on the surface, it does not oxidize quickly in the air. Due to its low weight, excellent corrosion resistance, and malleability, aluminum is the most commonly used metal in the industry





Why is Forging Aluminum better than Casting Aluminum?
Metal is compressed into higher strength during the forging manufacturing process, which involves heating and applying tremendous pressure to the metal. The substance becomes cast when it is put into the mold and cooled. Since the beginning of time, when tools were initially manufactured from materials like bone and stone, it is one of the oldest manufacturing methods still in use today. From its fundamental manufacturing process, casting and forging differ from one another. Casting has to pour the material into a mold at temperatures below its melting point to solidify, whereas forging requires heating and pressure. So, forging aluminum has significant advantages in producing the final component with great strength, flexibility, and a better surface finish. The forging process also gives an upper hand to better lead time and reduced cost compared to the casting process.
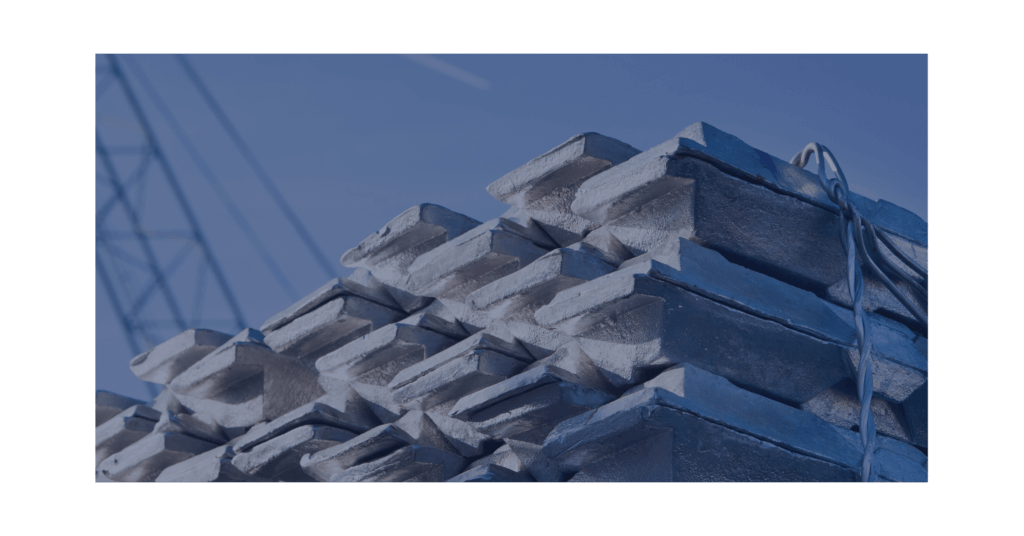
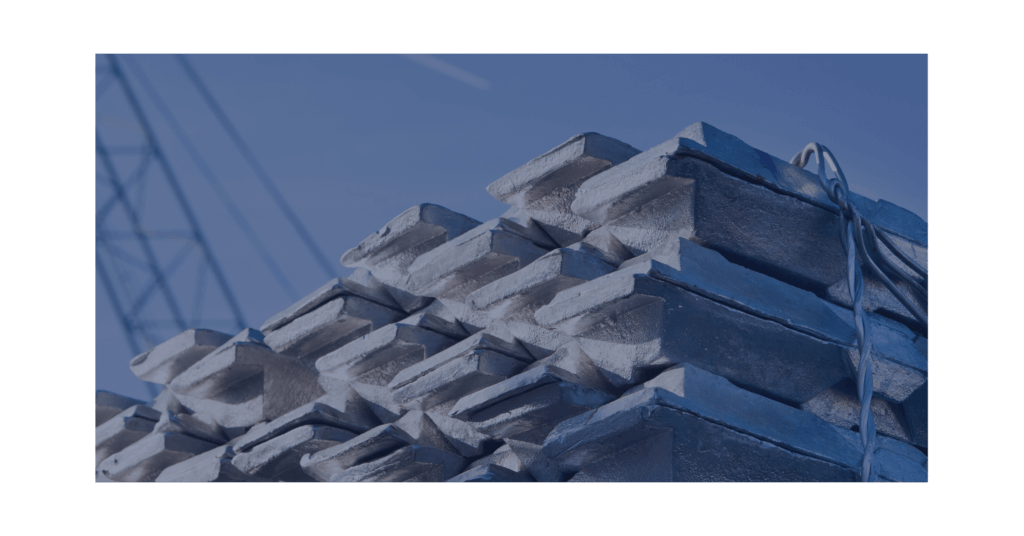
Ultimately, your business’s best forging presses company will depend on your specific needs and requirements. It’s essential to research and choose a forging company with the capabilities and experience to meet your needs and produce high-quality products.




