Precision sheet metal fabrication is a critical process that plays a crucial role in various industries, including aerospace, medical devices, and electronics manufacturing. From design to the final product, precision fabrication ensures accuracy, durability, and high quality.
Precision metal component production in low volumes benefits industries such as aerospace, medical devices, and electronics manufacturing. In this blog, we will explore the precision sheet metal fabrication process and its advantages.
Precision Sheet Metal Fabrication Process: An Overview
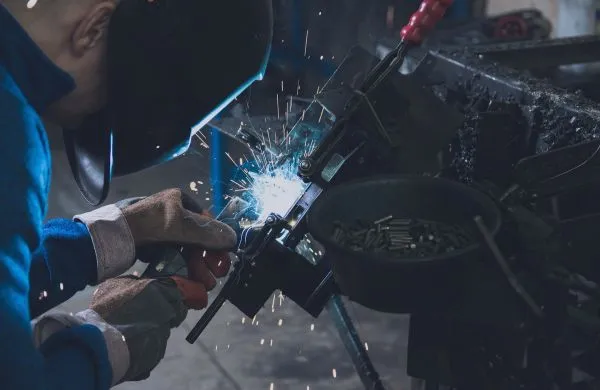
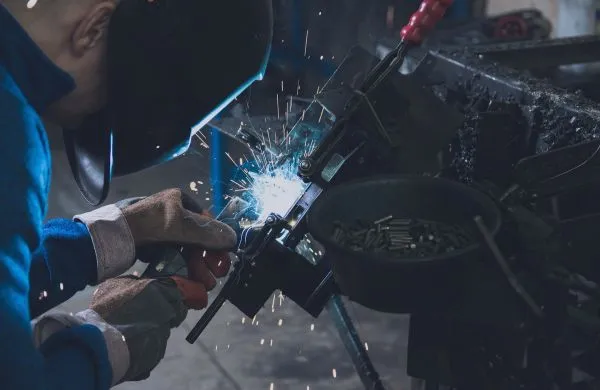
The precision sheet metal fabrication process involves producing precise sheet metal components for vehicles. The process begins with design, followed by cutting, forming, joining, finishing, quality control, and packing.
#1. Design Phase
The design phase begins with creating detailed technical drawings and blueprints using Computer-Aided Design (CAD) software. Engineers and designers consider factors such as desired shape, dimensions, material selection, structural integrity, safety standards, and manufacturing feasibility.
#2. Cutting Process
Sheet metal is cut into the desired shape and dimensions using various techniques such as laser cutting, waterjet cutting, or plasma cutting. These methods allow for precise cuts and minimize material waste.
#3. Forming Process
The sheet metal is bent, shaped, and formed using techniques like bending, roll forming, or stretch forming. These processes give the sheet metal components their desired geometry and dimensional accuracy.
#4. Joining of Metal Sheets
Different sheet metal pieces are joined together to create the final product. This can be done through techniques like welding, riveting, or adhesive bonding.
The choice of joining method depends on factors such as the material type, strength requirements, and design considerations.
#5. Finishing the product
The finished sheet metal components undergo surface treatments and finishes to enhance their appearance and durability.
This can involve processes like painting, powder coating, or anodizing. Surface treatments also help protect the components from corrosion and wear.
#6. Quality Control
Throughout the fabrication process, quality control and inspection are essential to ensure that each component meets the required standards and accuracy. Measurements and inspections are performed to verify dimensional accuracy and surface quality.
#7. Assembly Process
The packaged components are then assembled into the final vehicle. This process involves combining the newly manufactured sheet metal components with other components, such as engines, transmissions, and brakes.
Precision sheet metal fabrication in the auto industry involves a meticulous process from design to the final product, ensuring that high-quality, durable, and aesthetically pleasing sheet metal components are produced and used in vehicles.
Advantages Of Precision Sheet Metal Fabrication Process
- High Accuracy: Precision sheet metal fabrication ensures tight tolerances and high accuracy in the production of complex metal parts. This process utilizes advanced equipment and techniques to consistently achieve precise measurements, resulting in high-quality products.
- Customization Flexibility: Sheet metal fabrication allows for customization and the production of unique designs. This process enables manufacturers to create parts and components tailored to specific requirements, such as size, shape, and functionality.
- Material Versatility: Precision sheet metal fabrication works with a wide range of materials, including stainless steel, aluminum, brass, copper, and various alloys. This versatility allows for the production of parts with different mechanical properties, corrosion resistance, and aesthetic finishes.
- Cost-Effectiveness: Compared to other manufacturing methods, precision sheet metal fabrication can be cost-effective, especially for medium to high-volume production. The process minimizes material waste and efficiently utilizes raw materials, reducing overall production costs.
- Fast Turnaround Time: With advanced machinery and optimized workflows, metal fabrication offers fast turnaround times. This enables manufacturers to meet tight deadlines and quickly respond to market demands.
- Complex Geometry: Sheet metal fabrication allows for the production of intricate and complex shapes. Through techniques like bending, forming, cutting, and welding, manufacturers can create parts with curves, angles, and other intricate features.
- Strength and Durability: Precision sheet metal fabrication results in products that are strong, durable, and capable of withstanding demanding conditions. The use of high-quality materials and precise manufacturing processes ensures the strength and reliability of the fabricated parts.
- Consistency and Reproducibility: The use of automation and advanced machinery in precision sheet metal fabrication ensures consistent and reproducible results. This is crucial for industries that require identical parts for assembly or replacement.
Key Takeaways
Precision sheet metal fabrication requires careful planning and attention to detail. Understanding design principles like bending techniques, critical dimensions, and K-factor is crucial. Bend radius, orientation, and flange length are also important considerations.
This is why design engineering is critical in the sheet metal manufacturing process. Collaboration between engineers and fabricators is key to project success, meeting requirements accurately, reducing waste, and saving time and costs.
Experience the excellence of maximized manufacturing with Zetwerk. Our commitment to quality, advanced technology, streamlined processes, and dedicated team ensure superior results.
Choose Zetwerk for reliable and high-quality customized solutions that meet your specific requirements. Zetwerk helps you achieve precision in sheet metal fabrication projects by implementing cutting-edge methodologies and adhering to stringent design guidelines.




FAQs
Designing for precision sheet metal fabrication requires careful consideration of material properties, machine capabilities, tolerances, and cost. Some of the design tips include the right dimensioning and mechanical specification, rigidity and flexibility, and avoiding complexity that may increase fabrication time and cost.
Precision sheet metal fabrication is widely utilized in industries such as automotive, aerospace, electronics, telecommunications, medical devices, and construction.
Material selection plays a crucial role in precision sheet metal fabrication. The choice of materials depends on factors like desired mechanical properties, corrosion resistance, and cost-effectiveness.
To ensure manufacturability in precision sheet metal fabrication, several factors should be considered, including design complexity, tolerances, bend radius, tooling requirements, and finishing options.
Achieving high-quality results in precision sheet metal fabrication requires attention to detail, accurate measurements, skilled craftsmanship, and the use of advanced tools and equipment.