Roll Forming
Steel, the backbone of modern construction and manufacturing, comes in various forms to suit different applications. Among the multitude of steel processing techniques, roll forming stands as a versatile method for shaping steel into desired profiles. Two primary methods employed in this process are hot rolling and cold forming. Each method has its unique characteristics, advantages, and applications. In this blog post, we will embark on a journey to explore the significant differences between hot rolled and cold formed steel roll forming processes.
Understand Steel Roll Forming
Before diving into the distinctions between hot and cold methods, let’s first understand the fundamental concept of steel roll forming.
Definition of Roll Forming
Roll forming is a continuous metal forming process that involves passing a long strip of steel through consecutive sets of rolls. Each roll set progressively shapes the steel into the desired profile or cross-section. The process often begins with a coil or sheet of steel, and it ends with a precisely formed component.
The Role of Steel in Roll Forming
Steel is the material of choice for roll forming due to its exceptional strength, versatility, and durability. It can be easily manipulated during the roll forming process, making it suitable for creating a diverse array of products, from structural components to decorative trim.
Hot Rolled Steel Roll Forming Process
Hot rolling is one of the traditional methods for shaping steel. It involves heating steel to high temperatures and then passing it through a series of rolls.
Explanation of Hot Rolling
Hot rolling begins with a steel billet or slab heated to around 1,700 degrees Fahrenheit (926 degrees Celsius) or higher. The extreme heat makes the steel malleable, allowing it to be shaped without cracking or breaking. The red-hot steel is then passed through rolling mills, which gradually reduce its thickness and shape it into the desired profile.
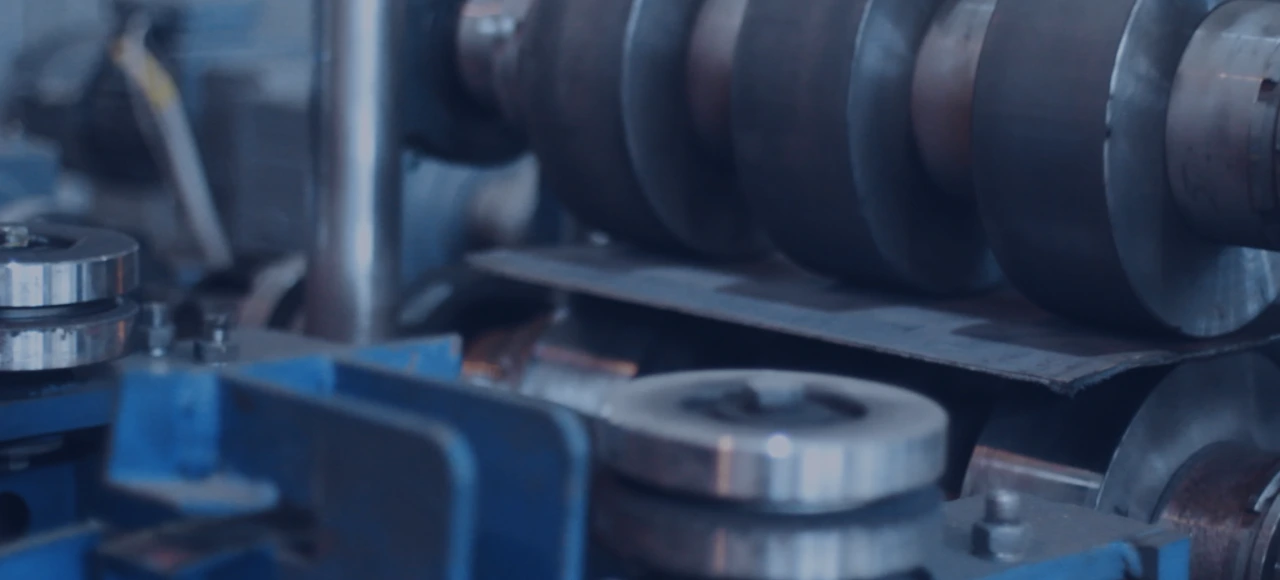
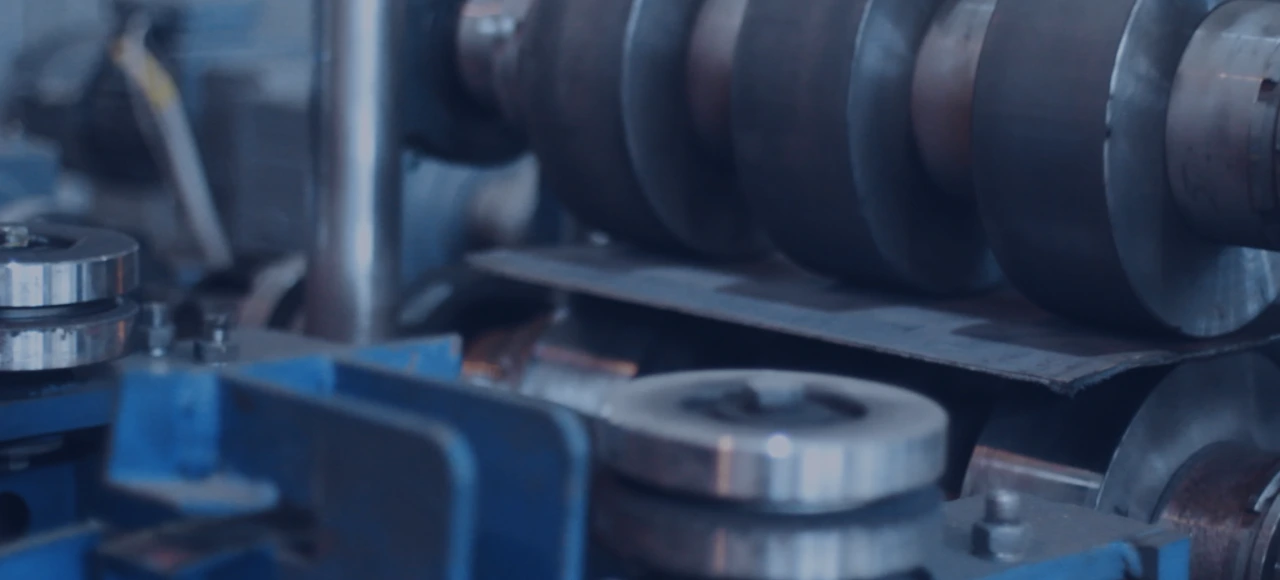
Key Characteristics of Hot Rolled Steel
Hot rolled steel exhibits several distinct characteristics:
- Uniform Grain Structure: The hot rolling process results in a uniform grain structure, which contributes to the material’s strength and ductility.
- Lower Tolerances: Hot rolled steel may have less precise tolerances compared to cold-formed steel, making it suitable for applications where exact dimensions are not critical.
- Surface Finish: The surface of hot rolled steel often has a rough, scaly texture due to the scaling that occurs during the heating process.
Advantages and Disadvantages
Advantages of Hot Rolled Steel
- High Strength: Hot rolled steel tends to have higher tensile and yield strengths compared to cold-formed steel.
- Cost-Effective: The hot rolling process is generally more cost-effective for large production runs.
- Versatility: Hot rolled steel can be used in a wide range of applications, from structural components to railroad tracks.
Disadvantages of Hot Rolled Steel
- Less Precise Dimensions: Hot rolled steel may not achieve the same level of dimensional accuracy as cold-formed steel.
- Surface Quality: The rough surface finish may require additional processing or finishing for certain applications.
- Limited to Simple Shapes: Hot rolling is better suited for simpler cross-sectional shapes.
Applications in Industry and Construction
Hot rolled steel finds application in numerous sectors, including the construction of skyscrapers, bridges, and heavy machinery. Its strength and affordability make it a popular choice for structural components in large-scale projects.
Cold Formed Steel Roll Forming Process
Cold forming, as the name suggests, involves shaping steel at or near room temperature without the need for extreme heat.
Explanation of Cold Forming
Cold forming typically starts with cold-rolled steel sheets or coils. These materials are already in a state where they can be easily formed. The steel is fed through a series of rolls that gradually shape it into the desired profile. Unlike hot rolling, cold forming does not involve the use of heat to soften the steel.
Key Characteristics of Cold Formed Steel
Cold formed steel exhibits its own set of characteristics:
- Precise Tolerances: Cold-formed steel can achieve tighter dimensional tolerances, making it ideal for applications where precision is critical.
- Smooth Surface Finish: The absence of scaling results in a smoother surface finish compared to hot rolled steel.
- Consistency: Cold forming ensures consistent material properties throughout the production process.
Advantages and Disadvantages
Advantages of Cold Formed Steel
- High Precision: Cold-formed steel is known for its precise dimensions and consistent quality.
- Excellent Surface Finish: The smooth surface finish often eliminates the need for additional finishing processes.
- Complex Shapes: Cold forming can create intricate and complex cross-sectional profiles.
Disadvantages of Cold Formed Steel
- Reduced Strength: Cold-formed steel may have lower tensile and yield strengths compared to hot rolled steel.
- Increased Costs: The cold forming process can be costlier for small production runs due to the need for specialized equipment.
- Limited to Certain Shapes: Cold forming is particularly well-suited for more intricate and precise shapes.
Applications in Industry and Construction
Cold formed steel is commonly used in industries that require high precision and consistent quality. It finds applications in manufacturing industries, automotive components, and architectural elements that demand exact specifications.
Comparing Hot Rolled vs. Cold Formed Steel
Now that we’ve explored the characteristics, advantages, and disadvantages of both hot rolled and cold formed steel, let’s make a side-by-side comparison.
Features | Hot Rolled Steel | Cold Formed Steel |
Material Properties | Higher tensile and yield strengthsUniform grain structureLess precise tolerancesRough surface finish | Lower tensile and yield strengthsPrecise tolerancesSmooth surface finishConsistent material properties |
Manufacturing Processes | Involves high-temperature heatingGradual reduction of thicknessBetter suited for simple shapes | Shaped at or near room temperatureAchieves tight dimensional tolerancesSuitable for intricate and complex profiles |
Cost Considerations | Cost-effective for large production runsEconomical for simpler shapes | Costlier for small production runsJustifiable cost for precision and complex shapes |
Environmental Impact | Higher energy consumption due to heatingGreater potential for material waste | Lower energy consumptionReduced material waste due to precision |
Selecting the Right Method
The choice between hot rolled and cold formed steel depends on several factors, including:
- Application Requirements: Consider the specific needs of your project. Are precise dimensions critical, or is strength the primary concern?
- Production Volume: For large production runs of simpler shapes, hot rolling may be more cost-effective. Cold forming is often justified for precision and small quantities.
- Material Properties: Evaluate whether the tensile and yield strengths of the chosen steel align with project requirements.
- Complexity of Shapes: If your project involves intricate and complex profiles, cold forming may be the preferred method.
- Cost Analysis: Conduct a thorough cost analysis to determine the most economical approach for your project.
Future Trends and Innovations
The world of steel roll forming is not static. Emerging technologies and sustainability concerns are shaping the future of steel processing.
Emerging Technologies in Steel Roll Forming
- Advanced Materials: Research continues to develop high-strength, lightweight steel alloys for various industries.
- Automation and Robotics: The integration of automation and robotics is streamlining the roll forming process, improving efficiency and reducing costs.
Sustainability and Eco-Friendly Practices
- Recycling: The steel industry is increasingly focused on recycling and repurposing steel, reducing the environmental impact.
- Energy Efficiency: Efforts are underway to minimize energy consumption in both hot rolling and cold forming processes.
The Evolving Role of Steel in Modern Construction
As construction practices evolve, steel continues to be a crucial component in sustainable and innovative building designs. From high-rise buildings to eco-friendly structures, steel remains at the forefront of modern construction.
In conclusion, the choice between hot rolled and cold formed steel roll forming processes is not a one-size-fits-all decision. Each method has its own strengths and weaknesses, making them suitable for specific applications. Understanding the nuances of hot and cold forming, considering project requirements, and conducting cost analyses are essential steps in selecting the right method.
As the steel industry advances, we can expect to see further innovations, particularly in the realm of sustainability and energy efficiency. Steel, in its various forms, will continue to shape our world, serving as the foundation for the buildings, infrastructure, and products that define our modern lives. Whether hot or cold, steel roll forming remains an indispensable process in manufacturing and construction.




FAQs
The key difference lies in the temperature during shaping. Hot rolled steel is formed at high temperatures (usually above 1,700°F or 926°C), while cold formed steel is shaped at or near room temperature. This temperature variance affects material properties, tolerances, and surface finishes.
Hot rolled steel is an excellent choice when strength and cost-effectiveness are crucial. It’s commonly used in applications like structural components, railroad tracks, and large-scale construction projects.
Cold formed steel is ideal for applications that demand precise dimensions, consistent quality, and complex cross-sectional shapes. Industries like automotive manufacturing and architectural design often favor cold formed steel.
Cold formed steel tends to have a lower environmental impact due to reduced energy consumption (no need for high-temperature heating) and less material waste (thanks to tight tolerances).
Yes, both types of steel can be recycled. Recycling is a sustainable practice that helps conserve resources and reduce the carbon footprint of the steel industry.