Stainless steel fabrication plays a crucial role in contemporary design and engineering, from the construction of tall skyscrapers to the creation of intricate machinery. Its flexibility and adaptability are limitless, serving as a fundamental building block for both creativity and practicality in a wide range of uses. Stainless steel can be bent, cut, welded, and manipulated into intricate shapes, making it an essential material for many applications. In this blog, we’ll discuss the stainless steel fabrication techniques, shedding light on the processes that transform raw stainless steel into functional, aesthetically pleasing structures.
What Is Stainless Steel?
Before we explore stainless steel fabrication techniques, it’s essential to understand what stainless steel is. Stainless steel is a corrosion-resistant alloy composed primarily of iron, with chromium as its crucial alloying element. The inclusion of chromium (typically at least 10.5%) creates a thin, passive layer of chromium oxide on its surface, which acts as a shield, protecting the metal from rust and corrosion.
Depending on the specific composition, stainless steel can exhibit varying levels of resistance to corrosion and rust, making it ideal for a wide range of applications.
Cutting Techniques
Cutting stainless steel is often the first step in the fabrication process. There are several methods for cutting stainless steel, depending on the thickness of the material and the desired precision
- Shearing: Shearing involves using a guillotine-like machine to cut stainless steel sheets. It is best suited for thin sheets and is a cost-effective method for straight cuts.
- Plasma Cutting: The plasma-cutting process involves a high-velocity jet of ionized gas to melt and remove material. This technique is excellent for cutting through thick stainless steel and creating intricate shapes.
- Laser Cutting: It is a precise and efficient method that uses a laser beam to cut stainless steel. It is ideal for intricate designs and fine details.
- Waterjet Cutting: The process involves a high-pressure jet of water mixed with abrasive particles to cut stainless steel. It is a versatile method that can cut through various thicknesses and materials without generating heat.
Bending and Forming Techniques
Stainless steel’s flexibility allows it to be bent and formed into numerous shapes, making it suitable for various applications in construction and manufacturing. Standard techniques for bending and forming stainless steel fabricator include:
- Press Brake Bending: Press brake is a machine that uses a punch and die to bend stainless steel sheets. It is precise and repeatable, making it suitable for creating straight, angled, complex bends.
- Roll Bending: Roll bending, or plate rolling, involves passing stainless steel through a series of rollers to create curved or cylindrical shapes. It’s commonly used in applications like pipe and tube manufacturing.
- Hydraulic Press Forming: Hydraulic presses exert tremendous force to deform stainless steel into the desired shape. This method is suitable for forming significant, heavy components.
- Spinning: Spinning is a precision technique to create conical or symmetrical shapes by rotating a metal disc against a form or mandrel.
Welding Techniques
Stainless fabrication is renowned for its weldability, critical for joining multiple pieces to create complex structures. Various welding techniques are employed in stainless steel fabrication, depending on the specific requirements
- TIG (Tungsten Inert Gas) Welding: TIG welding is a versatile method that uses a non-consumable tungsten electrode and inert gas shielding. It produces clean and aesthetically pleasing welds, making it suitable for applications where appearance matters.
- MIG (Metal Inert Gas) Welding: MIG welding involves a consumable wire electrode and inert gas shielding. It is faster than TIG welding and is commonly used for thick sections and high-production applications.
- Resistance Spot Welding: Resistance spot welding involves passing an electric current through the stainless steel sheets to be joined, causing them to melt and fuse. It’s an efficient method for joining thin materials.
- Submerged Arc Welding: Submerged arc welding uses a granular flux to protect the weld from the atmosphere. It’s commonly used for thick stainless steel fabricator sections and is ideal for high deposition rates.
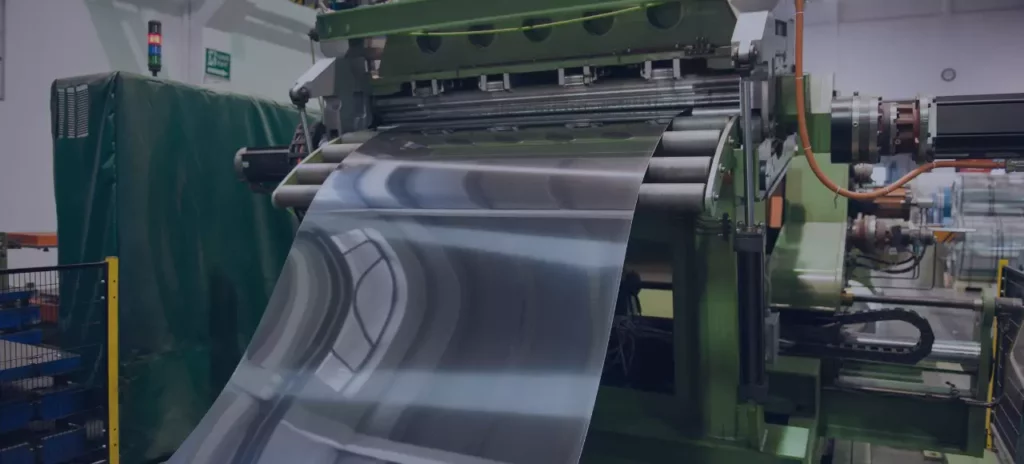
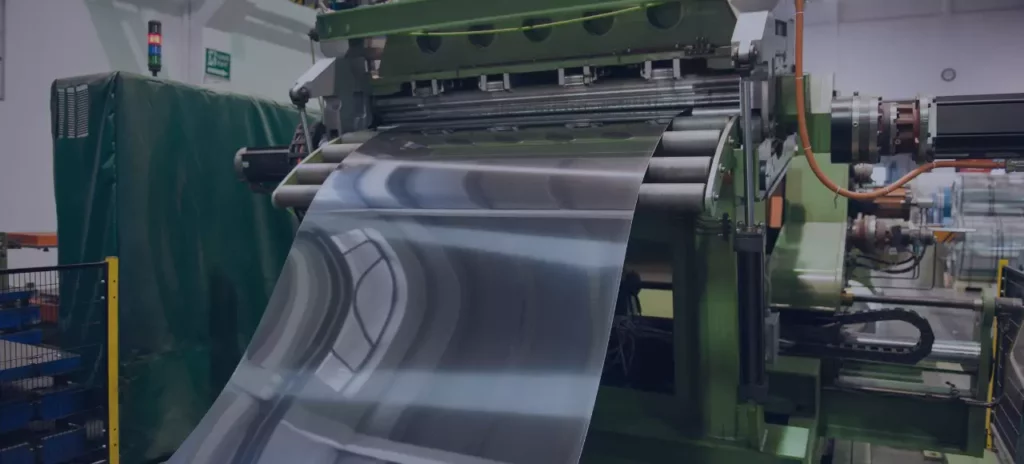
Finishing Techniques
To ensure the final product not only meets functional requirements but also looks appealing, stainless steel often undergoes finishing processes
- Polishing: Polishing enhances the stainless steel’s luster and removes surface imperfections. It can range from a satin finish to a mirror-like, highly reflective finish.
- Passivation: Passivation is a chemical treatment that removes iron from the surface, promoting the formation of a corrosion-resistant chromium oxide layer. This process is crucial for maintaining stainless steel’s corrosion resistance.
- Electropolishing: Electropolishing is an electrochemical process that removes a thin material layer from the surface, leaving a smooth and highly reflective finish.
- Design Considerations: Effective stainless steel fabrication requires careful consideration of design aspects. These include material selection, thickness, and tolerance requirements. Design engineers must also account for factors such as thermal expansion, which can affect the fit and function of the final product.
Applications of Stainless Steel Fabrication
Stainless steel’s exceptional qualities and the vast array of fabrication techniques have led to its extensive use in numerous industries
- Architecture and Construction: Stainless steel’s aesthetic appeal and durability make it a popular choice for architectural elements like handrails, facades, and structural components.
- Food and Beverage Industry: Stainless steel’s resistance to corrosion and ease of cleaning make it ideal for equipment used in food processing, such as tanks, conveyor systems, and countertops.
- Medical Devices: Stainless steel is used in medical devices, instruments, and equipment due to its biocompatibility, strength, and corrosion resistance.
- Aerospace: The aerospace industry employs stainless steel for its strength-to-weight ratio, resistance to high temperatures, and corrosion resistance.
- Automotive: Stainless steel is usually used in automotive exhaust systems, body panels, and other components due to its resistance to corrosion and high-temperature operation.
At its core, stainless steel fabrication is turning concepts into tangible, real-world products. Modern fabricators, such as Zetwerk, are dedicated to achieving this with meticulous accuracy and efficiency, all while upholding the most rigorous quality standards for your stainless steel fabrication project.




FAQs
Stainless steel is an alloy mainly made of iron and chromium, which forms a protective layer to resist corrosion and rust. Its popularity in fabrication stems from its durability, corrosion resistance, and aesthetic appeal.
Various cutting techniques are used for stainless steel, including shearing, plasma cutting, laser cutting, and waterjet cutting. The choice of method depends on the thickness of the stainless steel and the desired precision.
TIG welding, MIG welding, resistance spot welding, and submerged arc welding are standard techniques for joining stainless steel components. Each method offers specific advantages based on the application.
Stainless steel achieves its polished finish through polishing, passivation, and electropolishing. A glossy finish not only enhances aesthetics but also maintains the corrosion-resistant chromium oxide layer, ensuring longevity.
Stainless steel fabrication finds applications in various industries, including architecture and construction, food and beverage, medical device manufacturing, aerospace, and automotive. Its properties make it an ideal choice for multiple applications.