Among all the metal components producing techniques, metal stamping is the quickest, most reliable, and most effective way to produce intricate shapes from metal sheets. Sheet metal stamping is a cold-forming process that turns sheets of metal into valuable parts or components utilized in the industrial sector. This process uses dies and stamping presses to transform the metal sheet into different shapes. Once the metal is fed into a press, the die is pressed into or through the metal with tremendous force to give it the desired form.
Metal stamping is a complex process that uses a series of steps like blanking, punching, bending, and piercing. In this blog, we will discuss the different techniques used in the process of metal stamping in detail.
The Basics of Sheet Metal Stamping
Before delving into advanced techniques, it’s essential to grasp the fundamentals of sheet metal stamping. At its core, sheet metal stamping is a manufacturing process in which a metal sheet is formed into a desired shape or profile using a die and a press. This process is widely used in aerospace, automotive, electronics, and construction industries due to its efficiency, precision, and cost-effectiveness.
The basic steps of sheet metal stamping include:
- Blanking: Cutting a flat piece of sheet metal into a specific shape or size.
- Punching: Creating holes or other features in the metal.
- Bending: Shaping the metal using dies to achieve the desired geometry.
- Drawing: Pulling the metal into a die to create a three-dimensional shape.
Sheet Metal Stamping Techniques
Now that we’ve established the foundation let’s explore advanced sheet metal stamping techniques that can elevate your B2B purchasing decisions and product development strategies.
Progressive Die Stamping
- Progressive die stamping is an advanced method that produces complex parts with multiple features in a single pass. This technique is highly efficient, eliminating the need for various operations. In a progressive die setup, a metal strip is fed through a series of stations, each performing a specific operation, such as cutting, bending, or forming.
- This results in a finished part with precision and consistency, making it ideal for high-volume production. B2B buyers should consider progressive die stamping when they require intricate components with tight tolerances, as it minimizes material waste and reduces production time.
Deep Drawing
- This technique of sheet metal stamping is used to create cylindrical or box-like components from sheet metal. It involves drawing a flat metal sheet into a three-dimensional shape utilizing a punch and die set. This process is commonly employed in manufacturing items such as beverage cans, automotive fuel tanks, and kitchen sinks.
- Understanding the nuances of deep drawing is crucial when sourcing products that demand precise geometry and structural integrity. Materials selection, lubrication, and tooling design are all critical factors to consider when opting for deep drawing.
Hydroforming
- Known as one of the most versatile and advanced sheet metal stamping processes, Hydroforming is a technique that utilizes high-pressure fluid to shape metal. In this process, a blank sheet is placed inside a die, and water or hydraulic fluid is injected at high pressure to force the metal into the die cavity.
- Hydroforming is known for its ability to produce complex and lightweight parts with exceptional strength-to-weight ratios. Industries like aerospace and automotive should explore hydroforming when seeking cost-effective solutions for components that require intricate designs and superior performance.
Laser Cutting
- Laser cutting is a precision technique using a high-energy laser beam to precisely cut or engrave sheet metal. This advanced method offers several advantages, including minimal material waste, high speed, and the ability to create intricate patterns and designs. Laser cutting is widely used in producing electronics enclosures, signage, and automotive components.
- Industries must consider laser cutting for projects that demand intricate, fine-detail work, such as electronic enclosures and decorative panels. It’s also a suitable option for rapid prototyping and low-volume production runs.
Electromagnetic Forming
- EM forming, or electromagnetic forming, is an advanced and non-contact custom sheet metal stamping technique that uses electromagnetic forces to shape metal sheets. An electromagnetic coil induces a magnetic field in the sheet metal, causing it to deform and rapidly take on the desired shape.
- This technique is particularly advantageous for B2B buyers in the aerospace and defense sectors, where the ability to produce lightweight, high-strength components with minimal tool wear is essential.
Advanced Materials and Alloys
- As technology advances, so do the materials used in sheet metal stamping. B2B buyers should stay abreast of developments in advanced materials and alloys that offer improved strength, corrosion resistance, and lightweight properties.
- Examples include high-strength steel, aluminum alloys, and titanium. Selecting the suitable material for your project can significantly impact your stamped components’ performance, durability, and cost-efficiency.
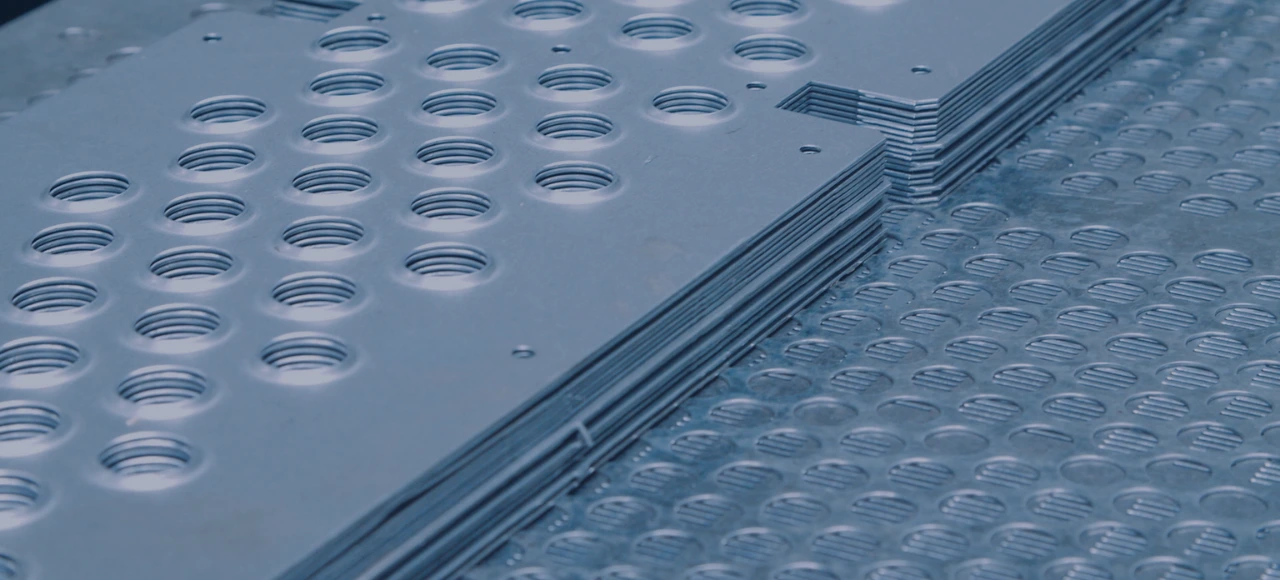
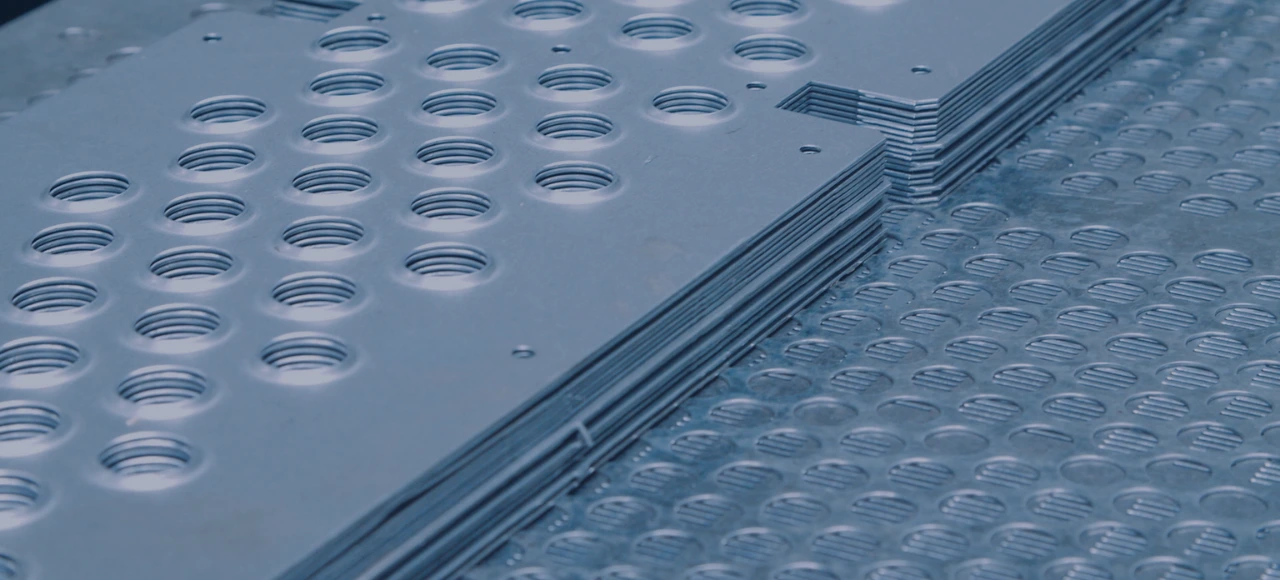
Fine Blanking
Fine blanking is a cutting technique that delivers exceptional precision and edge quality. It is ideal for producing parts with extremely tight tolerances and smooth edges. Fine blanking combines shearing and blanking processes, resulting in parts that require minimal post-processing. Industries like aerospace, medical devices, and electronics can benefit from fine blanking when seeking components that demand high accuracy, such as gears, sprockets, or connector components.
Tandem Stamping
Tandem stamping involves multiple presses operating in tandem to manufacture large and complex parts. This technique is particularly advantageous for B2B buyers in the automotive industry, where the demand for large body panels and structural components is prevalent. Buyers can produce significant, intricate components cost-effectively while maintaining consistency and quality by utilizing tandem stamping.
Tool Coatings and Surface Treatments
Enhancing tooling with advanced coatings and surface treatments can significantly improve the durability and performance of stamping dies. Various coatings, such as DLC (Diamond-Like Carbon) and TiAlN (Titanium Aluminum Nitride), reduce friction, wear, and adhesion, prolonging die life and reducing maintenance costs.
Computer-Aided Design (CAD) and Simulation
Incorporating computer-aided design (CAD) and simulation software into the sheet metal stamping process is critical. These tools allow for virtual prototyping and analysis of the stamping process before physical tooling is created. Simulation helps identify potential issues, optimize designs, and reduce the likelihood of costly errors during production.
If your industry demands precision parts of the highest quality, you need a stamping company that adheres to the strictest quality standards. Talking about quality, Zetwerk has been a trusted stamped parts manufacturer of precision tools for global enterprises since its inception. The company specializes in crafting intricate components for cutting-edge technological applications. To learn more about sheet metal stamping services, please visit Contact Zetwerk for Services and Company Information now.




FAQs
Advanced custom sheet metal stamping techniques offer increased precision, reduced material waste, improved efficiency, and the ability to produce complex components in a single operation. They also provide better control over tolerances and quality.
Selecting the correct technique depends on factors like the complexity of the part, required tolerances, material choice, production volume, and budget. Collaborating with an experienced supplier and conducting a thorough analysis of your project’s requirements will help you make an informed decision.
Advanced sheet metal stamping process techniques can be applied to various materials, including multiple grades of steel, aluminum, titanium, and specialty alloys. The choice of material depends on factors like strength, weight, corrosion resistance, and cost considerations.
Advanced techniques like progressive die stamping and fine blanking can reduce material waste and energy consumption, making them more sustainable options. Additionally, some materials used in custom sheet metal stamping, such as aluminum, are recyclable, further contributing to sustainability goals.
To maintain quality and consistency, working with reputable suppliers with a track record of producing high-quality stamped components is essential. Implementing quality control measures, such as inspection and testing, can help ensure that components meet your specifications throughout production. Additionally, ongoing communication and collaboration with your supplier are vital in addressing any issues promptly.