Shaping and Forming Techniques for Custom Sheet Metal Parts
Sheet metal is an exceedingly versatile material that can be molded and fashioned into infinite components and parts. Customized sheet metal components are utilized in a vast array of industries, ranging from construction and manufacturing to consumer goods. Various shaping and forming procedures are employed to manipulate the metal into the correct shape in order to manufacture these components.
Sheet metal stamping is a standard process for forming metal by utilizing a press to drive the metal into a die. This procedure can generate components with delicate features and close tolerances. Using a brake press, the metal is bent along a straight line using the bending process. Bending is frequently utilized to create U-shaped or angled components. Forming is another procedure used to fabricate sheet metal components to order. The metal is shaped using a mix of heat and pressure. Roll forming is a standard metal shaping technique that uses a succession of rollers to shape the metal into the desired form gradually. Deep drawing is a procedure that uses a punch and die to form the metal into a cup or other three-dimensional shape.
Welding is a crucial step in shaping and forming bespoke sheet metal components. The metal is heated to the point of melting, and two or more pieces are fused together. Welding is used to creating unique sheet metal parts in various shapes and sizes, such as brackets, flanges, and enclosures. Over time, the instruments used to shape and create specialized sheet metal components have evolved. In the past, metalworkers relied on manual techniques and hand-powered tools to shape metal. Today, computer-controlled machines and advanced software have revolutionized the metal fabrication industry in the US as well as globally, making it possible to produce complex custom sheet metal parts with greater precision and speed.
In conclusion, the techniques used for shaping and forming custom sheet metal parts significantly impact the final product. Understanding the various methods, tools, and materials involved in metal fabrication is crucial for producing high-quality custom sheet metal parts that meet the specific needs of each application.
Materials and finishes commonly used for custom sheet metal parts
Custom sheet metal parts are fabricated from various materials, each possessing distinct features and characteristics. The choice of material will rely on the product’s intended application and aspects such as cost, durability, and strength. Among the most often employed materials for custom sheet metal products are:
- Steel: Due to its strength and durability, steel is a common material for custom sheet metal goods. Additionally, it is quite affordable, making it a cost-effective choice for various applications. There are numerous ways to finish steel, including painting, powder coating, and galvanizing.
- Aluminum: It is a lightweight and corrosion-resistant material frequently used to fabricate sheet metal products. It is also an excellent conductor of both electricity and heat, making it a perfect material for goods requiring both characteristics. Anodizing is one of the various coatings that may be applied on aluminum to create an attractive, corrosion-resistant surface.
- Copper: Copper is a soft and pliable metal frequently used for sheet metal goods requiring electrical conductivity. It is also highly corrosion-resistant and can be coated with various finishes, such as tin plating and nickel plating, for increased durability and protection.
- Stainless Steel: Stainless steel is a highly corrosion-resistant material frequently utilized for sheet metal items exposed to hostile conditions. It is also a sturdy and durable material that can be coated in various ways, including polishing, to provide a sleek and contemporary look.
In addition to material selection, the finish of custom sheet metal goods is crucial. The purpose of finishes is to preserve metal from corrosion and damage and improve its appearance. Among the most frequent finishes for bespoke sheet metal items are the following:
- Painting: Painting is a standard finish for custom sheet metal goods because it provides a durable and aesthetically pleasing surface. It can be applied using several methods, including spray painting and electrostatic painting.
- Powder Coating: Powder coating is a procedure involving the application of a dry powder coating to the metal’s surface. The powder is then baked, producing a rugged and durable finish.
- Galvanizing: Galvanizing is a procedure that involves zinc coating the metal to prevent corrosion. This finish is frequently applied to items exposed to severe environments.
The selection of material and finish for custom sheet metal products is essential to ensure that they satisfy the unique requirements of each application. Whether you require a robust, durable material for construction or a lightweight, corrosion-resistant material for consumer goods, custom sheet metal products offer a variety of solutions to fit your needs.
The Advantages of Using Custom Sheet Metal: Why it’s the Perfect Material for Your Next Project
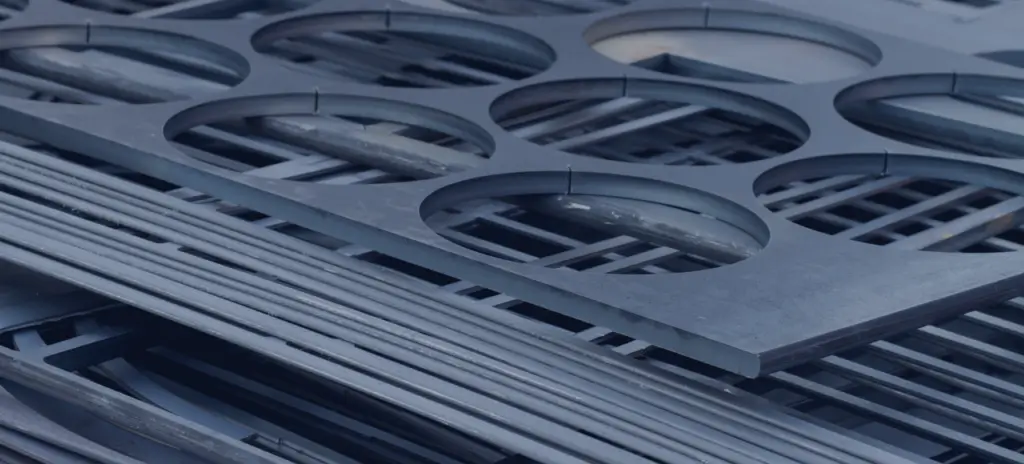
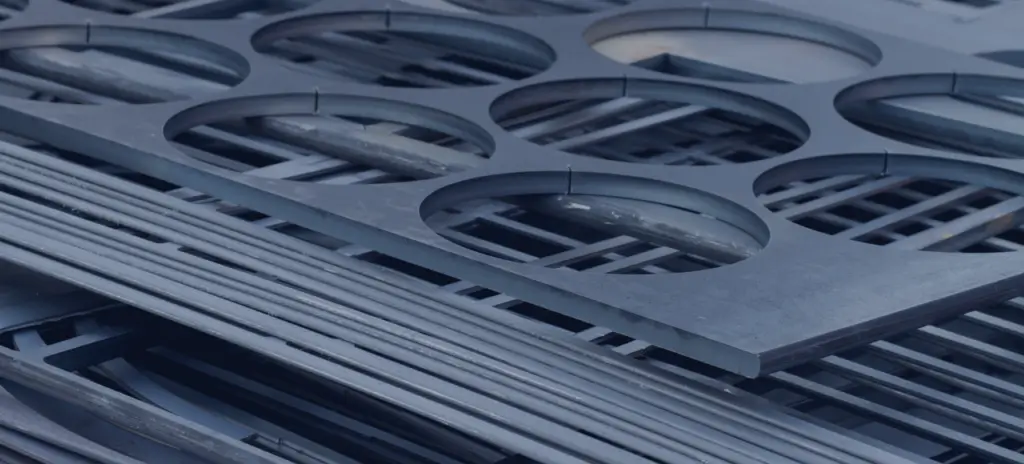
As a result of its multiple advantages, custom sheet metal has become a popular material for a vast array of applications. Among the primary benefits of adopting bespoke sheet metal are:
- Strength and Durability: Custom sheet metal is a durable and robust material that can withstand exposure to harsh environments and intense use. It is also resistant to corrosion, making it an ideal choice for products exposed to moisture, chemicals, and other corrosive elements.
- Cost-Effective: It is widely available and can be manufactured with minimal waste, They are typically a cost-effective alternative for many applications. It eliminates the need for outsourcing to third-party manufacturers, the capacity to create custom sheet metal goods in-house can also reduce the overall cost.
- Lightweight: Custom sheet metal is sometimes light, making it a perfect material for devices that must be portable. Additionally, its modest weight makes it simple to handle and install, minimizing the time and effort required to finish a job.
- Versatility: Custom sheet metal can be completed in numerous ways, including painting, powder coating, and galvanizing. These treatments not only improve the product’s visual appeal but also give further protection against corrosion and other factors.
- Customization: Because bespoke sheet metal can be molded and molded into an infinite number of forms and sizes, it is a versatile material that can be tailored to match the exact requirements of any application. Custom sheet metal enclosures, brackets, and flanges can be designed to satisfy even the most demanding specifications.
Custom sheet metal is a versatile and cost-effective material that provides a variety of advantages for a vast array of applications. Whether you require a robust and resilient material for construction or a lightweight and corrosion-resistant material for consumer products, bespoke sheet metal can provide a practical and aesthetically pleasing solution.
Zetwerk is an industry-leading manufacturer that offers end-to-end sheet metal project solutions. Customer-specific manufacturing, finishing, and assembly services of the highest quality are available from Zetwerk. The innovative technology platform of Zetwerk enables clients to upload their ideas and specifications, obtain quotations more quickly, monitor the progress of their projects, and receive timely delivery updates. We also offer value-added services such as design optimization, material selection, and cost optimization to ensure that our clients’ bespoke sheet metal projects yield the best results. Whether for prototyping, small-scale production or large-scale manufacture, Zetwerk’s efficient and transparent procedures and commitment to quality and dependability make it an excellent partner for clients seeking to bring our custom sheet metal projects to reality.



