Crafting Custom Metal Products: A Journey Through the Fabrication Process
Custom sheet metal fabrication is the creation of metal structures and components by cutting, bending, and assembling sheet metal and plates. This method is used to make metal items that meet specified design standards and needs. Depending on the sort of metal product being manufactured, the process of custom metal fabrication might vary but often includes the following steps:
- Design and Planning: The metal product is designed and planned during the first phase of bespoke metal fabrication. This step entails the creation of blueprints and three-dimensional models of the product, which provide a comprehensive grasp of its size, shape, and structural requirements. During this phase, designers and engineers also determine the project’s required metal and manufacturing procedures.
- Cutting: Following the completion of the design and planning phase, the metal sheets and plates are cut to size. Depending on the type of the metal and material’s thickness, this can be accomplished by various techniques, including sawing, water jet cutting, and laser cutting. This step is essential for assuring the quality and exactness of the final output.
- Bending: The following step entails bending the metal sheets and plates into the desired shape. This can be accomplished using various methods, including press brake bending, roll bending, and manual bending. Bending is a crucial step in the custom metal fabrication process, as it contributes to the product’s final shape.
- Assembly: The next step entails assembling the metal sections and components into the final product. Depending on the metal type and the object’s complexity, this can be accomplished using procedures such as welding, riveting, or bolting. In order to ensure the structural stability and integrity of the finished product, the assembling phase is crucial.
- Finishing: The final phase of bespoke metal fabrication is the product’s finishing, which protects it from corrosion and improves its appearance. Depending on the metal type and the intended final appearance, this may require the application of finishes such as painting, powder coating, or anodizing.
Custom sheet metal fabrication is a complex, multi-step process requiring knowledge and experience to generate high-quality metal products. Manufacturers can ensure the final product’s precision, correctness, and dependability by adhering to each manufacturing step. Custom metal fabrication is a crucial feature of many sectors and is used to make a vast array of products, ranging from major industrial components to simple ornamental metal items.
The importance of design and measurement in custom metal fabrication
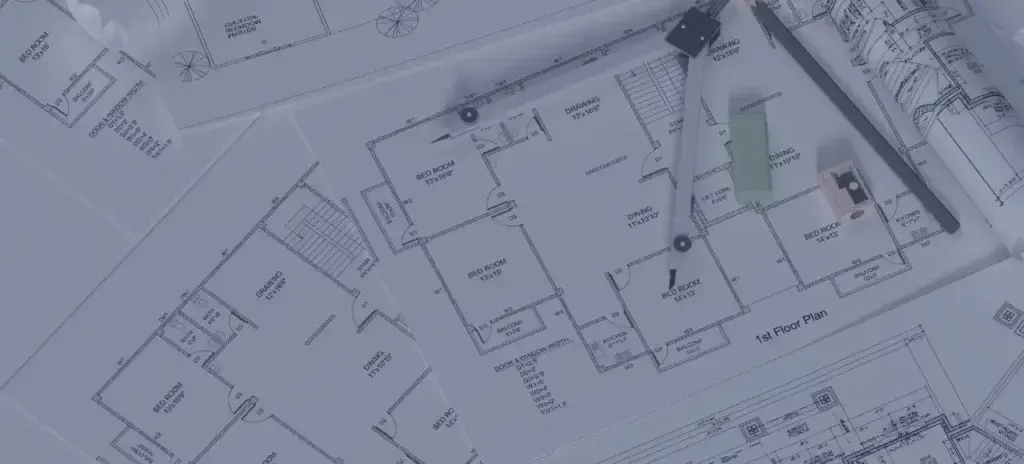
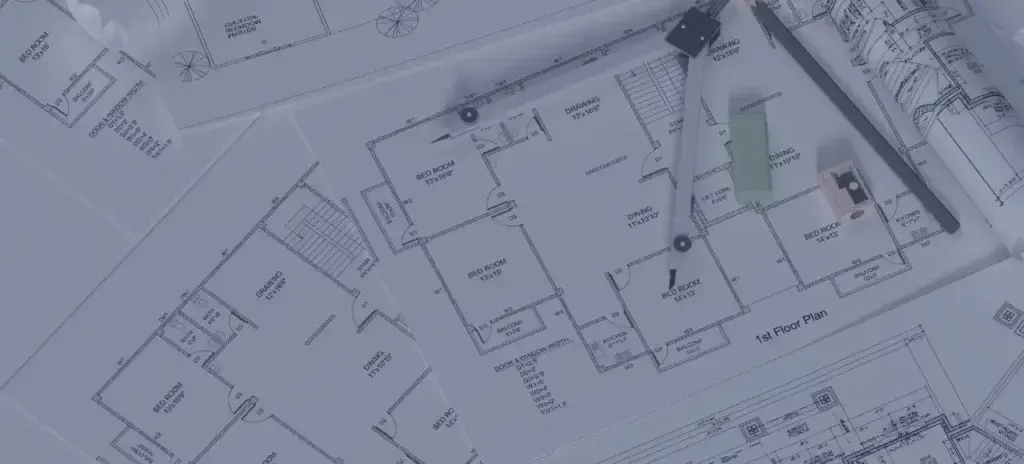
The design phase is the first and most important step in bespoke metal fabrication. The design of the bespoke metal product is crucial to its functionality and aesthetic appeal. The design phase includes the creation of blueprints and three-dimensional models of the product, which provide a comprehensive grasp of its size, form, and structural requirements. In addition to establishing the type of metal and production techniques necessary for the product, the design phase is crucial for determining these factors.
Not only will a well-designed product appear attractive, but it will also be helpful and match the necessary specs. In addition to being a critical part of bespoke metal manufacturing, precise measuring is also essential. This includes measuring the metal sheets, plates, and final product. Accurate measurements guarantee that the metal components are cut to the appropriate size and shape and that the finished product fits together properly. Additionally, precise measurements reduce waste and ensure the product is made efficiently.
Design and measurement play a crucial part in quality control, a crucial aspect of bespoke metal fabrication. Quality control measures ensure that the finished product meets design requirements and standards. This includes inspecting the product’s size, shape, and structural soundness and ensuring that it is free of flaws. Design and measurement are critical elements of custom metal manufacturing.
Producers can ensure quality, accuracy, and dependability by paying close attention to the product’s design and measurements, minimizing waste, and ensuring that the bespoke metal fabrication process is efficient and cost-effective; accurate design and measurement aid in reducing scrap. In bespoke metal fabrication, the significance of design and measurement cannot be emphasized since they are essential components of a successful and high-quality product.





Types of techniques used in custom metal fabrication
Custom metal fabricators produce metal items by cutting, bending, and assembling metal sheets and plates following specified design specifications. Several criteria, such as the type of metal being used, the size and shape of the product, and the desired final result, determine the manufacturing technique employed. Among the most prevalent metal fabrication processes utilized in bespoke metal fabrication are the following:
- Welding: Welding is one of the most extensively used procedures for fabricating metal. It involves heating two metal parts to a temperature that causes them to melt and join together. Welding is an ideal method for fabricating metal objects with high structural stability and strength.
- Cutting: It is the process of dividing metal into distinct forms and sizes. This can be accomplished using various methods, including sawing, water jet cutting, and laser cutting. The process will depend on the metal’s thickness, the type of metal used, and the intended result.
- Stamping: Sheet metal stamping is a manufacturing technique involving a press cutting metal into particular forms. The stamping process is perfect for fabricating unique metal objects with high precision and repeatability.
- Bending: Bending is the technique of bending metal into a particular shape. This can be accomplished using various methods, including press brake bending, roll bending, and manual bending. In bespoke metal fabrication, bending is essential for forming the metal into its final shape.
- Forging: Forging is a metalworking process that includes heating metal to a high temperature and then pressing it into its final shape. Forging is the optimal method for producing unique metal goods that require a high level of strength and durability.
To develop high-quality metal goods, custom metal fabrication involves several metal fabrication techniques. Manufacturers may ensure the finished product’s quality, accuracy, and dependability by selecting the appropriate metal manufacturing method. To create unique metal items that satisfy specific design needs and standards, it is essential to comprehend various metal fabrication procedures. Zetwerk can fulfill your custom metal fabrication project with industry professionals and keep you in real-time project updates till the components reach your place. Zetwerk has the best lead time in the industry and can meet your project requirements. Contact our experts to get a quote for your custom metal fabrication project.




