High-quality materials are the lifeblood of the manufacturing industry. Just like preparing a delicious meal requires fresh ingredients, metal fabrication needs certified, industrial-grade metals to manufacture safe, reliable, and durable machinery. There is no substitute for high-quality materials. However, different projects require different types of raw materials. Some metals work best in specific applications, so selecting the suitable metal becomes crucial to the product design process.
Since it all begins with the suitable material, steel emerges as one of the world’s most versatile and widely used construction materials. Its durability, strength, and malleability make it stand out and an ideal choice for various applications. Two popular manufacturing processes for steel sections are hot rolling and cold forming.
Choosing the right material for your project is crucial because each method has its advantages and disadvantages, which can significantly impact its success. In this blog, we will take a comprehensive look at hot-rolled and cold-formed steel sections, exploring their characteristics, applications, and factors to consider when selecting.
Understanding Hot Rolled Steel Sections
The process of hot rolling involves heating a steel billet or slab to a temperature of approximately 1700 degrees Fahrenheit (927 degrees Celsius) and then passing it through a series of rollers to achieve the desired shape. This process creates hot rolled steel sections, which are known for their unique properties.
Characteristics of Hot Rolled Steel Sections
- Strength and Durability: Hot rolled steel sections are known for excellent strength and durability. The high-temperature rolling process eliminates internal stresses in the steel, making it more resilient to bending and deformation.
- Cost-Effective: Hot rolling is a cost-effective method for producing steel sections in large quantities. This makes hot rolled steel sections a popular choice for applications where cost efficiency is a primary concern.
- Surface Finish: Steel sections fabricated using hot rolling methods typically have a rougher surface finish than cold formed sections. This may be better for applications where aesthetics are essential.
- Tolerance: Hot rolled sections may have slightly larger dimensions and straightness tolerances than cold formed sections. However, these tolerances are generally acceptable for many structural applications.
Applications of Hot Rolled Steel Sections
Hot rolled steel sections find application in a wide range of industries and construction projects, including:
- Structural Steel Frames: Hot rolled I-beams, H-beams, and channels are commonly used in building construction for load-bearing purposes.
- Bridges: Steel created with hot rolling is often used to make the structural components of bridges due to its strength and durability.
- Railway Tracks: The rails used in railway tracks are typically made from hot rolled steel sections.
- Machinery and Equipment: Many heavy machinery and equipment components are fabricated from hot rolled steel due to its strength and cost-efficiency.
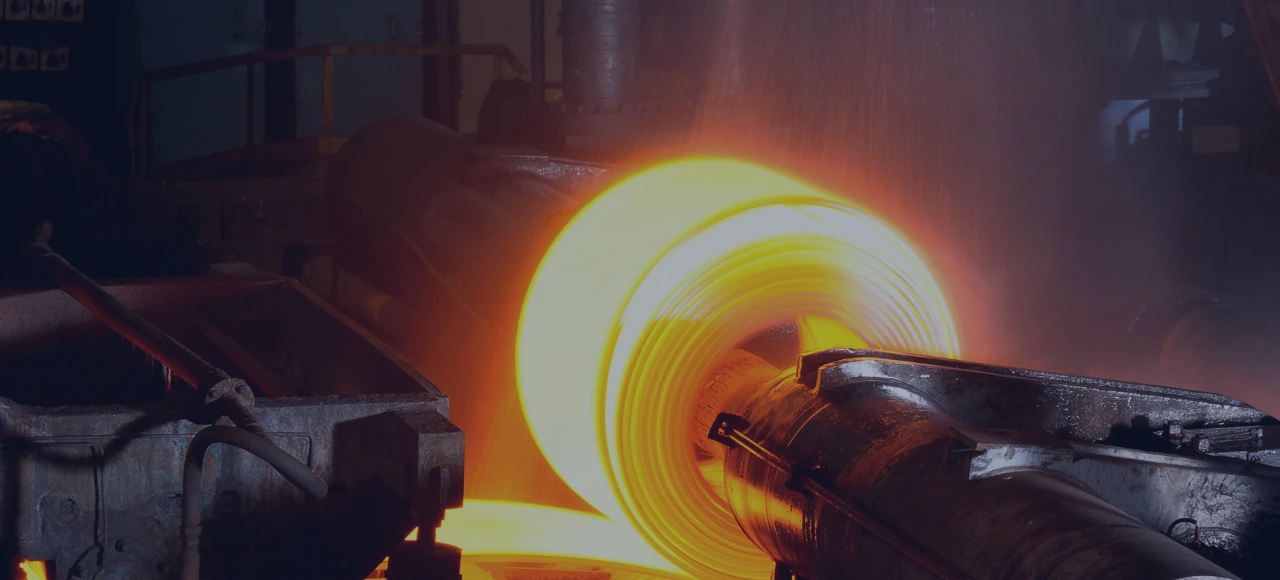
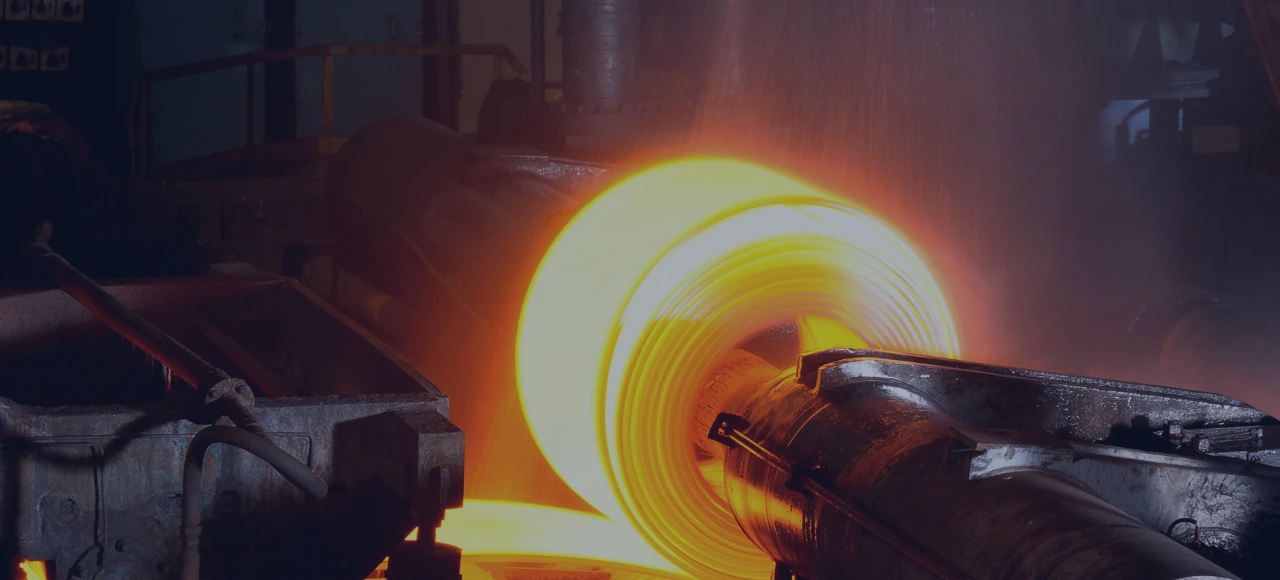
Exploring Cold Formed Steel Sections
In contrast to hot rolling, cold forming involves shaping steel at room temperature. Cold-formed steel sections are produced by bending, folding, or rolling steel sheets or strips without heat. This process results in sections with distinct characteristics.
Characteristics of Cold Formed Steel Sections
- Precision: Structures made from cold rolling allow for greater accuracy in terms of dimensions and shapes. Cold formed sections typically have tighter tolerances compared to hot-rolled sections.
- Smooth Surface Finish: Cold formed sections have a smoother and more aesthetically pleasing surface finish, making them suitable for applications where appearance matters.
- Higher Strength-to-Weight Ratio: The cold forming method can offer a higher strength-to-weight ratio of sections compared to hot rolled ones, making them ideal for applications where weight is a critical factor.
- Cost Considerations: Fabricating sections with cold rolling can be more expensive than hot rolling, especially for small production runs. However, the precision and other advantages may outweigh the cost difference in specific applications.
Applications of Cold Formed Steel Sections
Cold formed steel sections are used in many industries and applications, including:
- Architectural Components: Experts frequently incorporate cold-formed steel sections into their designs for their sleek appearance and exact measurements.
- Automotive Industry: Cold formed steel is used in vehicle components where weight reduction and strength are essential.
- Storage Systems: The precision and strength of cold-formed steel sections make them popular for constructing shelves, racks, and storage systems.
- Infrastructure: Infrastructure projects like highway guardrails and signposts also use cold-formed steel sections.
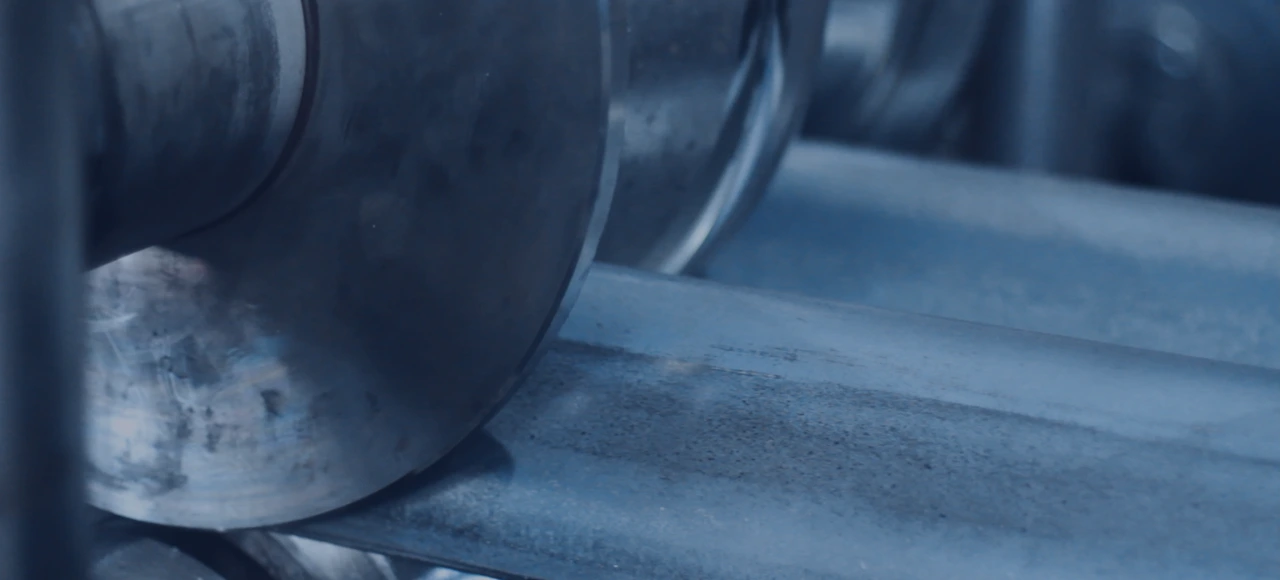
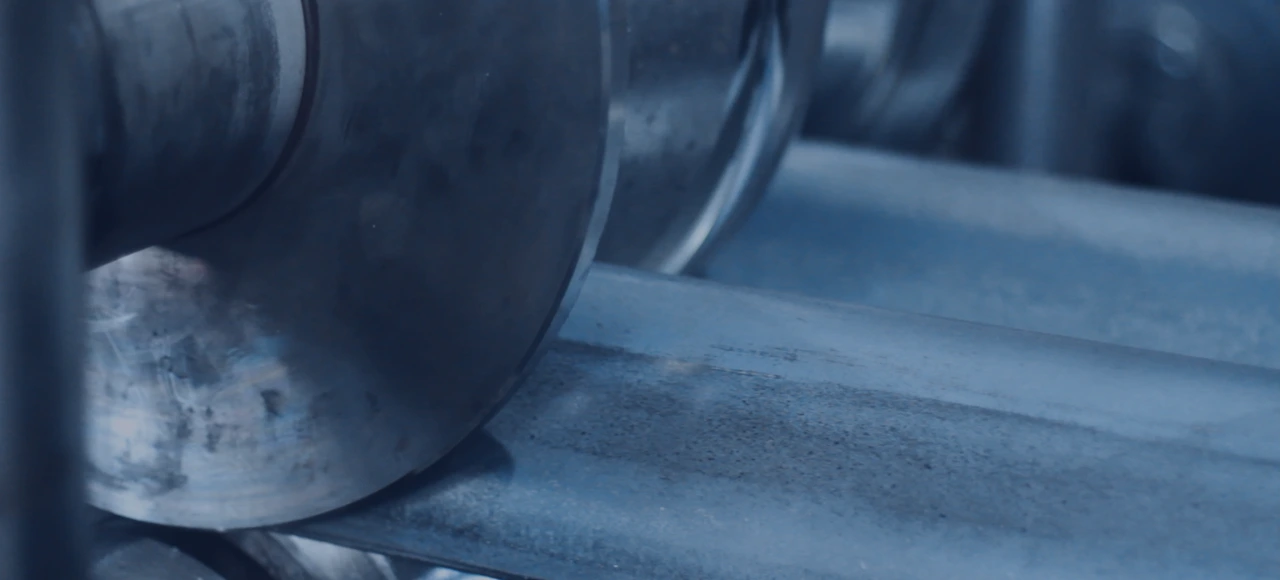
Factors to Consider When Choosing Between Hot Rolled and Cold Formed Steel Sections
Selecting the suitable steel material for your project depends on various factors. Here are some key considerations and insight into the difference between hot rolled and cold formed steel sections:
- Strength Requirements: Consider the structural requirements of your project. Hot rolled sections are known for their superior strength, while cold formed sections may be a better choice when weight reduction is essential.
- Cost Constraints: Evaluate your budget and production requirements. Hot rolled sections are typically more cost-effective for large quantities, while cold formed sections may be suitable for smaller, precision-oriented projects.
- Aesthetics: If the appearance of the steel sections is essential, cold formed sections often offer a smoother and more appealing surface finish.
- Tolerances and Precision: Consider the level of precision required for your project. Cold formed sections are known for their tight tolerances and dimensional accuracy.
- Environmental Conditions: Think about the environment in which the steel sections will be used. Hot rolled sections may be more suitable for outdoor applications due to their durability.
- Lead Time: Evaluate your project’s timeline. Cold forming processes may have longer lead times than hot rolling, impacting project scheduling.
- Regulatory Requirements: Ensure that your choice of steel sections complies with local and industry-specific regulations and standards.
Hot Rolled vs Cold-Formed Steel: What to choose?
- Hot rolled and cold formed steel are two distinct processes in manufacturing steel products, each with its own advantages and applications. The selection between the two depends on the project requirements and structural considerations. Hot rolled steel is known for its strength and durability, making it an excellent choice for heavy-duty construction projects like bridges and structural beams. It is formed at high temperatures, allowing for the creation of larger and thicker sections.
- On the other hand, cold formed steel is produced at room temperature. It is specifically suited for applications that require precision and a high degree of customization, such as lightweight steel framing for residential and commercial buildings. Ultimately, the decision between hot rolled vs. cold-formed steel comes down to the project’s unique needs, budget constraints, and engineering specifications, each offering distinct advantages in different scenarios.
Wrapping Up
In the end, hot rolled and cold-formed steel play pivotal roles in construction, manufacturing, and various industries, offering a testament to this enduring material’s remarkable versatility and adaptability. So, whether your project demands the fiery strength of hot rolled steel or the precision of cold-formed steel, remember that there’s always a choice tailored to your needs in the world of steel.
Zetwerk is one of the leading names in the steel fabrication industry, offering various services, including design, fabrication, installation, and maintenance of sanitary equipment for multiple industries. The team is highly knowledgeable about the complexities of metal fabrication and can guide clients through the material selection process, ensuring the perfect match for their specific needs.




FAQs
The main difference lies in the manufacturing process. Hot rolled steel is produced by heating it to a high temperature and passing it through rollers, while cold formed steel is shaped at room temperature by bending or rolling without heat.
Hot rolled steel is generally more robust than cold formed steel. The high-temperature rolling process eliminates internal stresses, resulting in a material better suited for heavy load-bearing applications.
Yes, there are cost differences. Hot rolled steel sections are often more cost-effective for large quantities due to the efficiency of the hot rolling process. Cold formed sections can be more expensive, particularly for small production runs or projects requiring precision shaping.
Hot rolled steel is well-suited for projects that require exceptional strength and durability, such as structural frames, bridges, and railway tracks. Cold formed steel shines in applications with precision, aesthetics, and a higher strength-to-weight ratio, such as architectural components and lightweight automotive parts, are essential.
Your choice should be based on the specific needs of your project. Consider factors like strength requirements, budget constraints, aesthetic considerations, precision requirements, and the environmental conditions in which the steel will be used. A careful evaluation of these factors will help you determine whether hot rolled or cold formed steel is the better choice for your project.