B2B (business-to-business) manufacturers constantly seek ways to streamline their production processes while maintaining high-quality standards. One method that has gained popularity in recent years is DIY sheet metal stamping. This versatile technique allows manufacturers to produce various metal components in-house, reducing lead times and production costs. In this blog, we will discuss how B2B manufacturers can leverage this technique.
What is Sheet Metal Stamping?
At its core, sheet metal stamping is a metalworking process that involves shaping and cutting sheet metal into various forms and sizes. This process is achieved through specialized equipment, such as stamping presses, dies, and punches. Sheet metal stamping is widely used in manufacturing to create many products, ranging from simple brackets to complex automotive components.
The DIY Approach in B2B Manufacturing
Although many B2B manufacturers depend on outsourcing sheet metal stamping for their business needs, many are now adopting a self-reliant strategy. This approach involves bringing sheet metal stamping capabilities in-house, which offers several advantages:
Precision and Consistency
Sheet metal stampings are known for producing exact and consistent metal parts. Using carefully designed dies ensures that each stamped component is identical. This precision is crucial in industries where precise measurements and tolerances are paramount, such as aerospace, automotive, and electronics manufacturing. Eliminating human error makes metal stamping a preferred choice for producing complex, intricate parts that demand impeccable accuracy.
High Production Speed
Stamping presses can cycle at an impressive rate, producing hundreds or even thousands of parts per minute, depending on the complexity of the component and the type of equipment used. This high production speed allows manufacturers to efficiently meet large production volumes and tight deadlines. As a result, metal stamping is often chosen for mass production of components like brackets, clips, and connectors.
Cost-Effective Production
The combination of precision and speed in metal stamping translates into cost-effective production. The ability to produce many parts quickly lowers labor costs per unit. Additionally, the longevity of the stamping dies means that they can have thousands or even millions of parts before needing replacement, reducing tooling costs in the long run. This cost-efficiency makes metal stamping an attractive option for businesses looking to optimize manufacturing processes and reduce production costs.
Material Utilization
Sheet metal stampings are renowned for their material utilization efficiency. The process involves cutting and forming metal sheets with minimal waste. Manufacturers can optimize material usage by carefully nesting parts within the metal sheet, reducing scrap and minimizing environmental impact. This efficiency in material utilization saves costs and aligns with sustainability goals by reducing waste and energy consumption.
Wide Range of Materials
While metal stamping is often associated with steel and aluminum, it can be used with various metals and alloys, including copper, brass, stainless steel, and even exotic materials like titanium. This adaptability empowers manufacturers to choose the most appropriate material for the application.
Complex Geometries
The process of DIY sheet metal stampings allows for creating intricate and complex geometries that might be challenging or impossible to achieve with other manufacturing methods. Manufacturers can produce components with multiple bends, angles, and features using progressive dies or compound dies in a single operation. This capability is invaluable in industries like automotive, where complex parts are commonplace, and lightweight designs are essential for fuel efficiency.
Enhanced Strength and Durability
Through processes like work hardening, stamping can increase the strength and durability of materials. This is particularly advantageous in applications where components must withstand high-stress levels, such as structural supports in construction or safety-critical parts in transportation.
Consistent Quality
Quality Control is a priority in manufacturing, and metal stamping maintains consistent quality. The automated nature of the process reduces the likelihood of defects or variations in the final product. Quality control measures can be integrated into the stamping process, allowing for real-time monitoring and adjustments, further ensuring the production of high-quality components.
Design Flexibility
Sheet metal stampings offer design flexibility that enables engineers and designers to create innovative products. The ability to manipulate and shape metal sheets provides opportunities for unique designs that meet specific functional and aesthetic requirements. This design flexibility extends to custom tooling, which allows for producing bespoke components tailored to a customer’s needs.
Reduced Lead Times
Given its high production speed and efficiency, metal stamping significantly reduces lead times compared to alternative manufacturing methods. Faster production means that manufacturers can respond more quickly to market demands and changes in product design. This agility is crucial in industries characterized by rapid technological advancements and shifting consumer preferences.
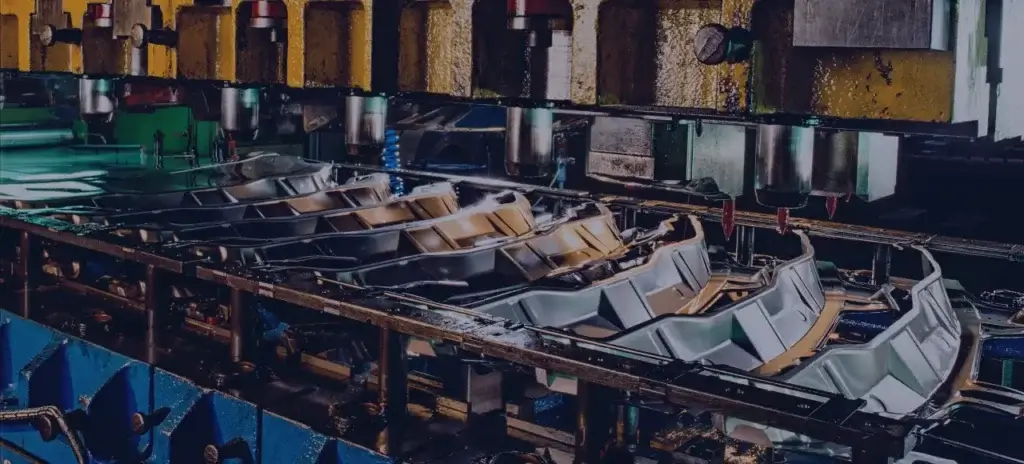
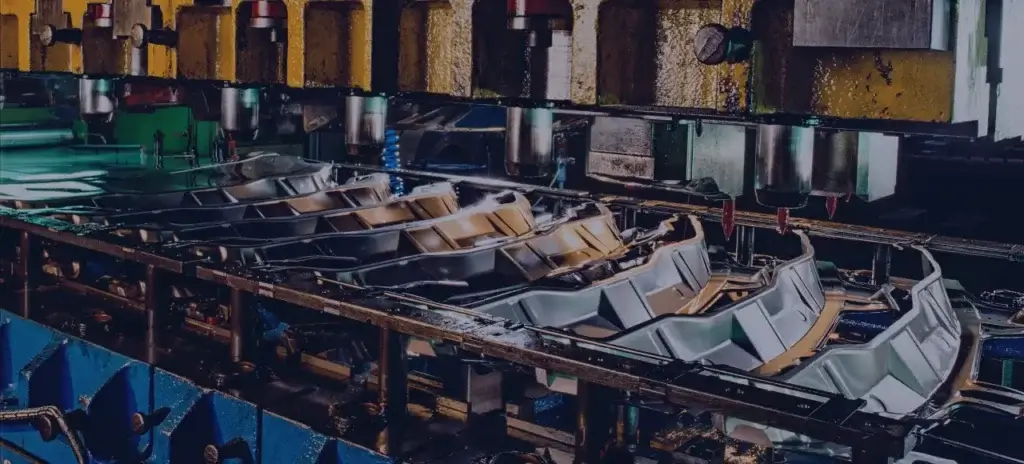
Setting Up Your DIY Sheet Metal Stamping Operation
Initiating an in-house sheet metal stamping operation demands meticulous planning and financial commitment. The following are the essential steps to help you start the process:
Assess Your Needs
Start by evaluating your production requirements. What kinds of metal components do you frequently need? What quantity of parts must be manufactured? A clear grasp of your particular needs will enable you to determine the size and capacity of the stamping equipment you require.
Acquire Equipment
Depending on your requirements, you can opt for mechanical presses, hydraulic presses, or servo presses. The selection of equipment hinges on factors like material thickness, desired precision, and production volume.
Develop Tooling
Tooling refers to the essential components comprising dies and punches used in stamping. You may need to work with tool and die makers to design and manufacture tooling that meets your specifications. Tooling costs can be significant, but they are a one-time investment that pays off over time.
Train Your Team
Proper training is essential to ensure your stamping equipment’s safe and efficient operation. Invest in training programs for your staff or hire experienced operators who are already familiar with sheet metal stamping.
Implement Safety Measures
Sheet metal stamping involves powerful machinery, so safety should be a top priority. Implement comprehensive safety protocols, provide personal protective equipment (PPE), and regularly inspect and maintain your equipment to prevent accidents.
Start Small and Scale
It’s advisable to start with smaller production runs and gradually scale up as you gain experience and confidence in your DIY stamping operation. This allows you to fine-tune your processes and identify potential issues before taking on larger projects.
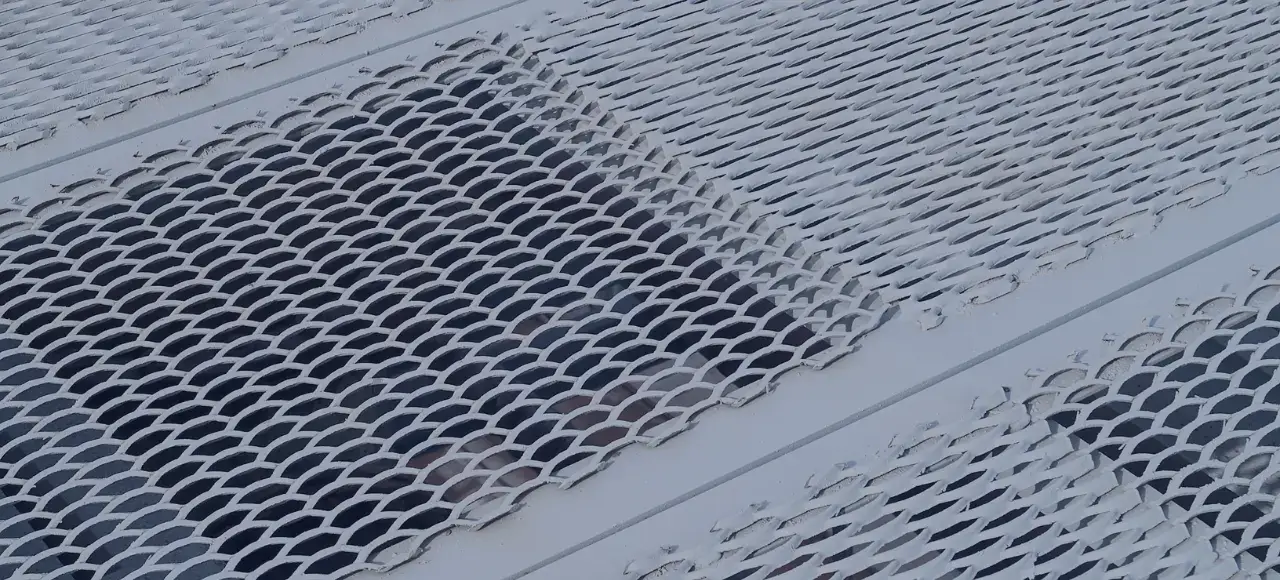
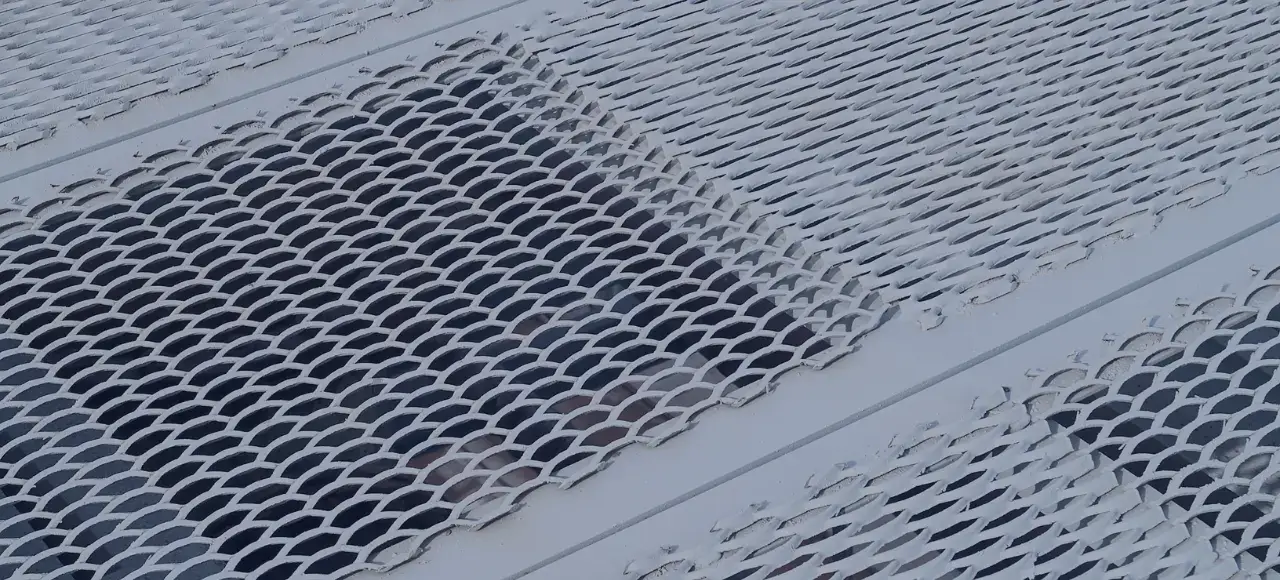
Tips for Successful DIY Sheet Metal Stamping
To ensure the success of your DIY sheet metal stamping operation, keep the following tips in mind:
Material Selection
Selecting the appropriate sheet metal material for your specific application is crucial. Take into account factors like strength, corrosion resistance, and cost. It’s important to note that different metals may necessitate modifications to your stamping process.
Tool Maintenance
Conduct routine inspections and upkeep of your stamping tools to ensure their good condition. Properly maintained tools are essential in ensuring consistent quality and minimizing unexpected downtime.
Quality Control
Implement a robust quality control process to check each stamped component for dimensional accuracy and defects. This will help you identify and address issues early in the production process.
Efficiency Improvement
Always be on the lookout for chances to enhance the efficiency of your stamping operation. This might include fine-tuning tooling, refining press configurations, or embracing lean manufacturing principles.
Compliance and Safety
Keep yourself informed about industry regulations and sheet metal stamping safety standards. Adhering to these guidelines safeguards your workforce and protects you from costly fines and legal complications.
Conclusion
As technology advances, the barriers to entry for DIY sheet metal stamping are becoming more manageable. With the right equipment, training, and dedication, B2B manufacturers can unlock the benefits of this versatile manufacturing process and gain a competitive edge in their industry.
Zetwerk is dedicated to helping DIY enthusiasts with their projects by offering high-quality materials and professional advice. They aim for excellence in engineering, whether the individual is a seasoned metalworker or a beginner. When undertaking sheet metal stamping projects, it is essential to remember that the blueprint is the vision, and passion fuels an individual toward infinite possibilities.




FAQs
Yes, DIY sheet metal stamping can be cost-effective for small and medium-sized manufacturers, especially if they have consistent production needs. While there is an initial investment in equipment and tooling, the long-term cost savings and increased control over the production process can outweigh the upfront expenses.
DIY sheet metal stamping can be applied to a wide range of metals, including steel, aluminum, brass, copper, and various alloys. The choice of material depends on the specific application and its requirements.
Selecting the right stamping press involves considering factors such as material thickness, production volume, precision requirements, and available budget. Consulting with industry experts or equipment suppliers can help you make an informed decision.
Safety is paramount in sheet metal stamping. Essential safety measures include correctly training operators, using personal protective equipment (PPE), conducting regular equipment maintenance, and implementing lockout/tagout procedures to prevent accidental startup.
Yes, one of the advantages of DIY sheet metal stamping is the ability to quickly create custom parts and prototypes quickly. Having in-house stamping capabilities allows manufacturers to iterate designs and efficiently develop new products.