Sheet metal fabrication, a fundamental process in manufacturing, has undergone significant advancements in recent years. These technological innovations have transformed the industry by enhancing precision, efficiency, and sustainability. This detailed article will delve into the critical advancements in sheet metal fabrication, examining their impact on various industries and the broader manufacturing landscape.
Laser Cutting Revolution
- Fiber Laser Cutting: Fiber lasers generate a focused beam of light capable of cutting intricate patterns in various materials. Their energy efficiency and reduced maintenance requirements contribute to sustainability.
- CO2 Laser Cutting: It uses a high-power carbon dioxide (CO2) laser beam to melt, burn, or vaporize materials. This technology is widely used in various industries for cutting, engraving, and etching multiple materials.
- Twin and Multi-beam Lasers: Some laser-cutting machines are equipped with multiple laser heads or beams, allowing for the simultaneous cutting of various parts and increased productivity.
- Fast Piercing and Piercing Detection: Advanced piercing technology reduces piercing time, and some machines have piercing detection systems that automatically adjust parameters for optimal hole quality.
- Precision and Waste Reduction: Laser cutting has drastically improved precision, minimizing material waste. It enables the creation of complex geometries and intricate designs, producing lightweight yet durable components.
CNC Press Brakes For Precision Bending
- Automated Bending: CNC press brakes equipped with advanced control systems allow for automated bending operations. Operators can program desired angles and dimensions, leading to accurate bends, reduced human error, and increased production efficiency.
- Integration with 3D Printing: The integration of 3D printing with CNC press brakes has opened new possibilities. Additive manufacturing enables custom tooling and fixtures, enhancing design flexibility and reducing lead times.
- Multi-axis Press Brakes: Press brakes with multiple axes (typically six or more) provide greater flexibility in forming complex shapes and reduce the need for manual repositioning of the workpiece.
- Augmented reality (AR) and virtual reality (VR): Some manufacturers have started using AR and VR technologies for training and maintenance. These technologies can assist operators in setting up and operating CNC press brakes effectively.
- Automatic Tool Changing: Some CNC press brakes are equipped with automatic tool changers. These systems can change bending tools automatically, reducing downtime and increasing efficiency.
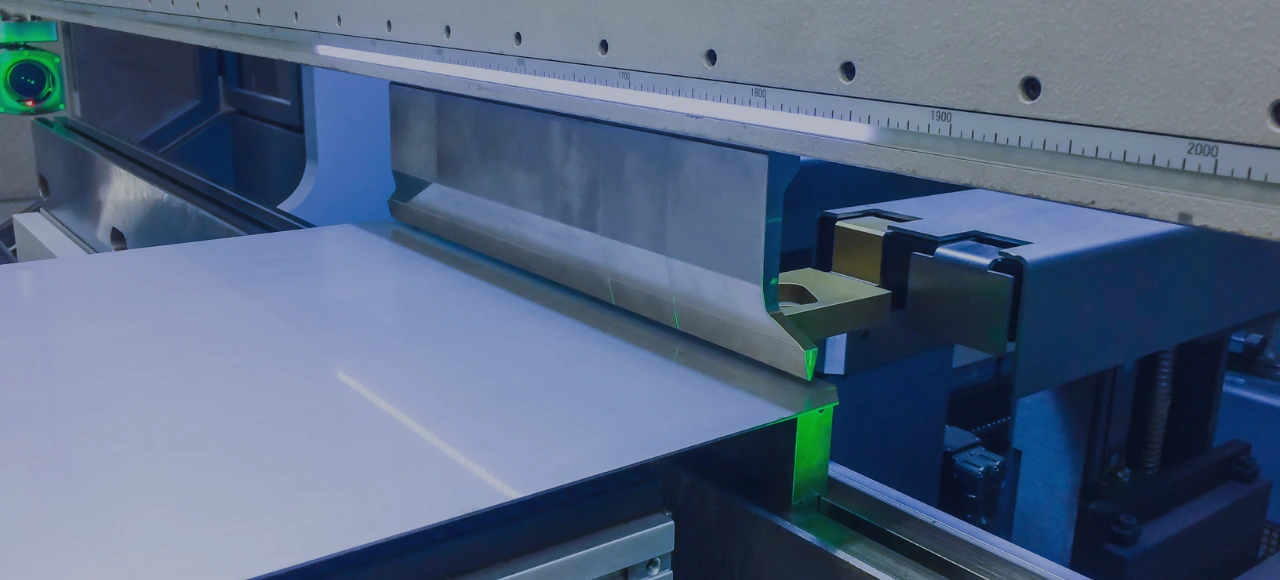
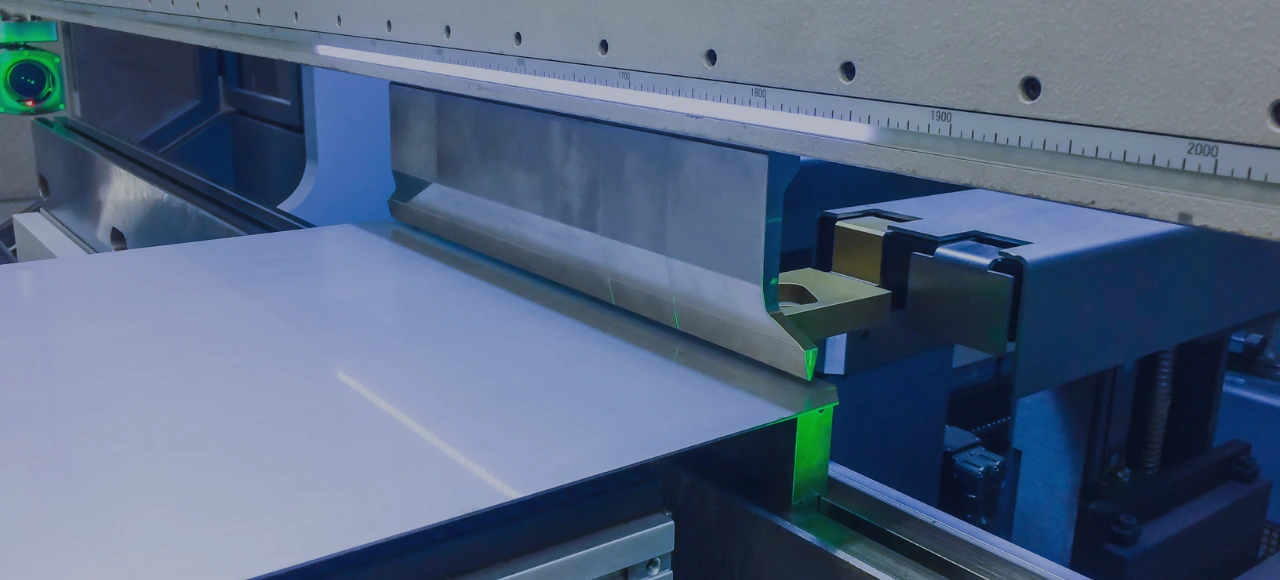
Robotics and Automation
- Robotic Welding Systems: Robotic welding systems have become commonplace, ensuring consistent and high-quality welds. They are precious in applications where welds must meet strict industry standards for strength and integrity.
- Material Handling Robots: Material handling robots optimize the flow of materials throughout the fabrication process. They load and unload sheet metal from machines, transport components between workstations, and enhance worker safety while reducing production bottlenecks.
- Automated Guided Vehicles (AGVs): AGVs are used for moving sheet metal components within the fabrication facility. They can navigate autonomously, optimizing material flow and reducing the need for manual transportation.
- Cobot Integration: Collaborative robots (cobots) work alongside human operators, enhancing safety and productivity. Cobots can perform tasks like pick-and-place, polishing, and quality inspection.
- IoT and Industry 4.0 Integration: Automation systems are increasingly connected to the Internet of Things (IoT) and Industry 4.0 platforms. This allows real-time monitoring, data collection, and predictive maintenance to optimize production.
- Lights-out Manufacturing: Advances in automation have enabled lights-out manufacturing, where fabrication facilities can operate 24/7 without human intervention, significantly increasing production capacity.
Digital Twin Technology
- Process Simulation: Digital twin technology allows manufacturers to create virtual replicas of fabrication processes. It identifies potential issues like collisions or material deformation before they occur, reducing costly mistakes and improving overall process efficiency.
- Product Design and Prototyping: Manufacturers use digital twins to virtually prototype sheet metal components, experimenting with different designs and configurations. This iterative approach saves time and resources during product development.
- Supply Chain Integration: Digital twins can extend beyond the manufacturing facility to include the entire supply chain. This allows for better coordination and visibility, reducing lead times and ensuring on-time delivery of materials and components.
- Predictive Maintenance: By monitoring the performance of equipment and machinery in real-time, digital twins can predict when maintenance is required, which minimizes downtime and prevents unexpected breakdowns.
- Real-time Simulation: Digital twins can provide real-time simulation of manufacturing processes, such as bending, stamping, laser cutting, and welding. Engineers can analyze how these processes affect the final product and adjust to ensure quality and efficiency.
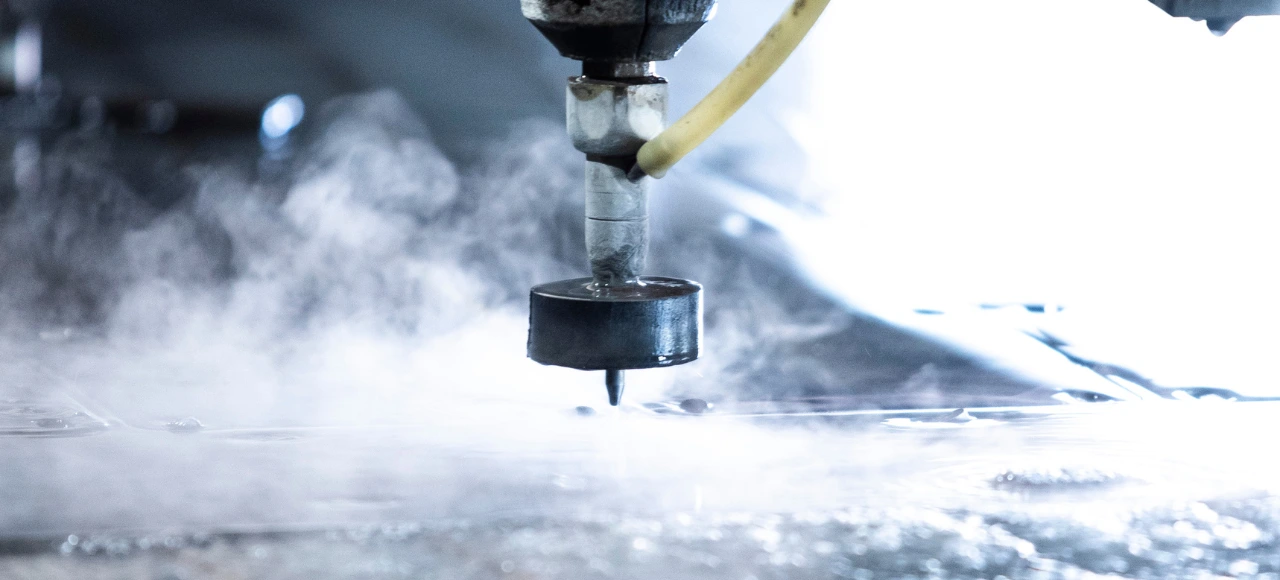
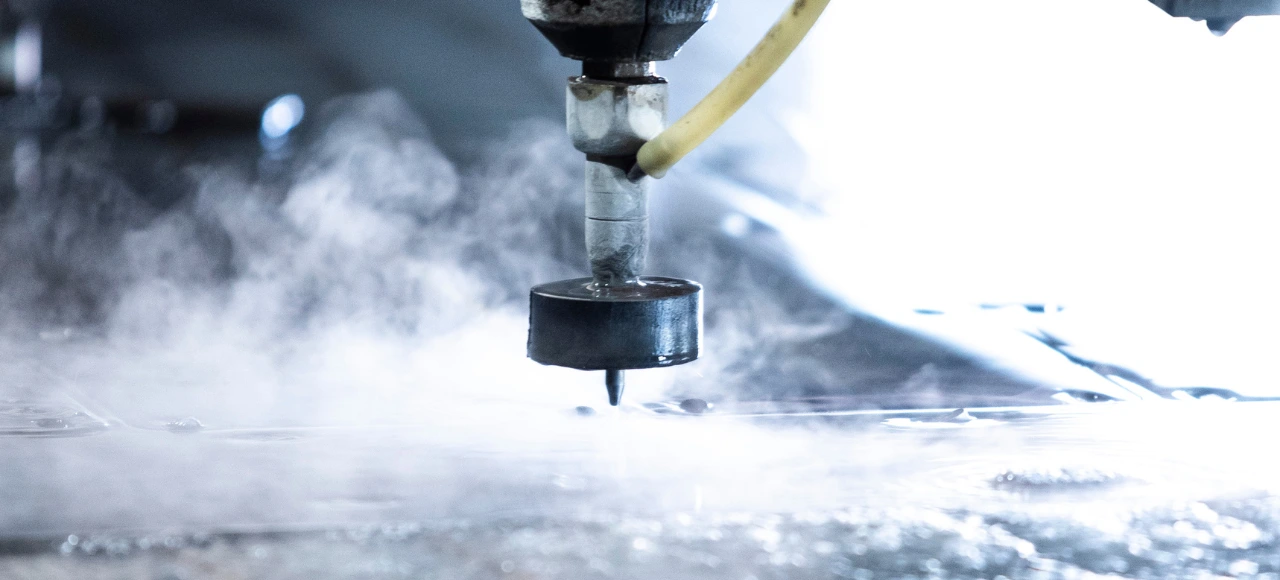
Sustainability and Environmental Responsibility
- Waterjet Cutting: Waterjet cutting is an eco-friendly alternative to traditional methods that produce heat and fumes—high-pressure water jets combined with abrasives cut sheet metal precisely while minimizing energy consumption and environmental impact.
- Lean Manufacturing Principles: Lean manufacturing principles are being applied to reduce waste and improve efficiency. Practices like 5S (Sort, Set in order, Shine, Standardize, Sustain), value stream mapping, and just-in-time production help minimize resource use and waste.
- Green Certifications: Companies are pursuing green certifications, such as ISO 14001 (Environmental Management System) and LEED (Leadership in Energy and Environmental Design), to demonstrate their commitment to sustainability.
- Carbon Footprint Reduction: Reducing carbon emissions often involves optimizing processes, improving energy efficiency, and investing in carbon offset programs.
Impact On Various Industries
- Automotive Industry: Sheet metal fabrication advancements play a pivotal role in the automotive sector. Precision components are crucial for safety and performance, and innovations like laser cutting and robotics contribute to enhanced vehicle quality and design flexibility.
- Aerospace Industry: Aerospace relies on lightweight yet strong materials, making precision in sheet metal fabrication paramount. Laser cutting and CNC press brakes aid in creating complex aircraft components that meet stringent standards.
- Construction and Architecture: Sustainable practices, including recycling and waste reduction, are vital in construction and architectural applications. Using eco-friendly methods like waterjet cutting aligns with modern construction’s sustainability goals.
- Consumer Electronics: Miniaturization and intricate designs in consumer electronics demand precise sheet metal fabrication. Laser cutting and digital twin technology enable the production of compact yet functional electronic components.
- Energy Sector: Renewable energy technologies, such as solar panels and wind turbines, rely on precise sheet metal fabrication for efficient energy capture. Sustainable practices in manufacturing align with the clean energy objectives of this sector.
- Medical Devices: The medical industry requires high precision in fabricating components for medical devices. Advancements like laser cutting contribute to the manufacturing of intricate, life-saving instruments.
Conclusion
Recent advancements in sheet metal fabrication, including technologies like laser cutting, CNC press brakes, robotics, digital twin technology, and sustainable practices, have revolutionized the industry.
FAQs
Laser cutting is commonly used for cutting various metals, including steel, stainless steel, aluminum, and copper. It can also cut non-metal materials like plastics and composites.
Yes, specialized tooling advancements include precision-ground tooling, segmented tooling for complex shapes, and tool coatings to reduce friction and wear, all contributing to precision bending.
Modern CNC press brakes use adaptive bending technology and automatic tool compensation to adjust parameters based on material thickness, ensuring precise bends regardless of variations.
Future trends may include:
Increased use of artificial intelligence.
More excellent connectivity through Industry 4.0 technologies.
Advanced safety features.
More flexible and adaptable automation systems.
A Digital Twin typically consists of a virtual model, data analytics capabilities, real-time sensor data, and connectivity to physical machines and processes.