Supply chains are unequivocally the lifeblood of the manufacturing industry, playing an indispensable role in the overarching business operations and overall profitability. A well-optimized supply chain ensures that goods are produced and delivered with utmost efficiency and cost-effectiveness, regardless of whether these operations are confined to local boundaries or span across the globe.
Each supply chain is unique, made up of a myriad of interconnected activities and processes. These processes encompass various stages, right from the initial phase of sourcing raw materials, to the manufacturing process, and finally to the delivery of the finished product. Each step along this chain needs to be meticulously synchronized and optimized for achieving maximum efficiency.
This is an intricate, complex process that necessitates strategic planning and meticulous execution. For example, in the pharmaceutical industry, the supply chain is extraordinarily complex. It begins with the sourcing of raw materials, extends through the manufacturing and testing of the drug, and ends with delivery to healthcare providers and patients. Each step must be carefully managed to ensure product quality, efficiency, and compliance with regulations.
However, the journey of a supply chain is rarely a smooth one. Disruptions can occur at any stage, from unforeseen logistical problems such as transport strikes or natural disasters, to supplier issues like raw material shortages, or sudden shifts in demand due to market fluctuations or changes in consumer behavior. These disruptions often result in significant delays that can inflate the overall cost of manufacturing. A prominent example of this disruption is the Suez Canal blockage in 2021, which caused massive delays in global shipping, leading to increased costs and disrupted supply chains across various industries.
These challenges underscore the critical importance of cost optimization in supply chains. It’s not just about reducing expenses but also about aligning the supply chain performance with the overall business strategy. By focusing on cost optimization, businesses can build resilient supply chains that can withstand disruptions and maintain operational efficiency. Collaborating with Zetwerk, an industry leader in high-quality production and precision manufacturing, helps you effectively manage potential roadblocks while enabling efficient global component sourcing and manufacturing.
Key Cost Drivers in Supply Chain Management
When discussing cost optimization, various factors are considered. Let’s explore some common elements that disrupt supply chains and elevate costs beyond expected levels.
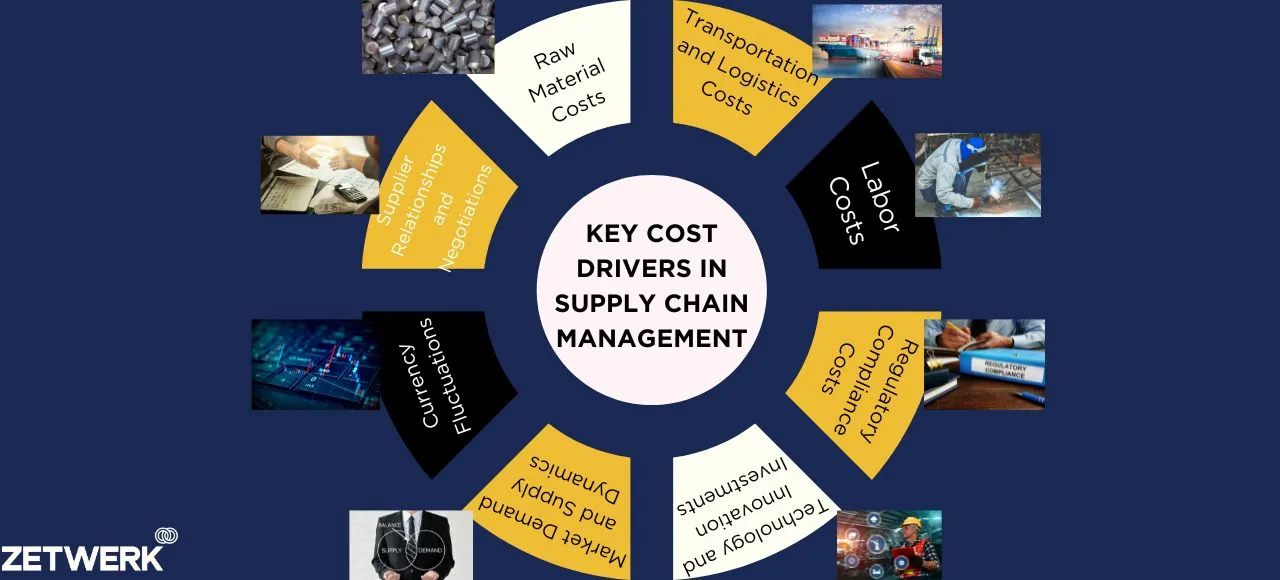
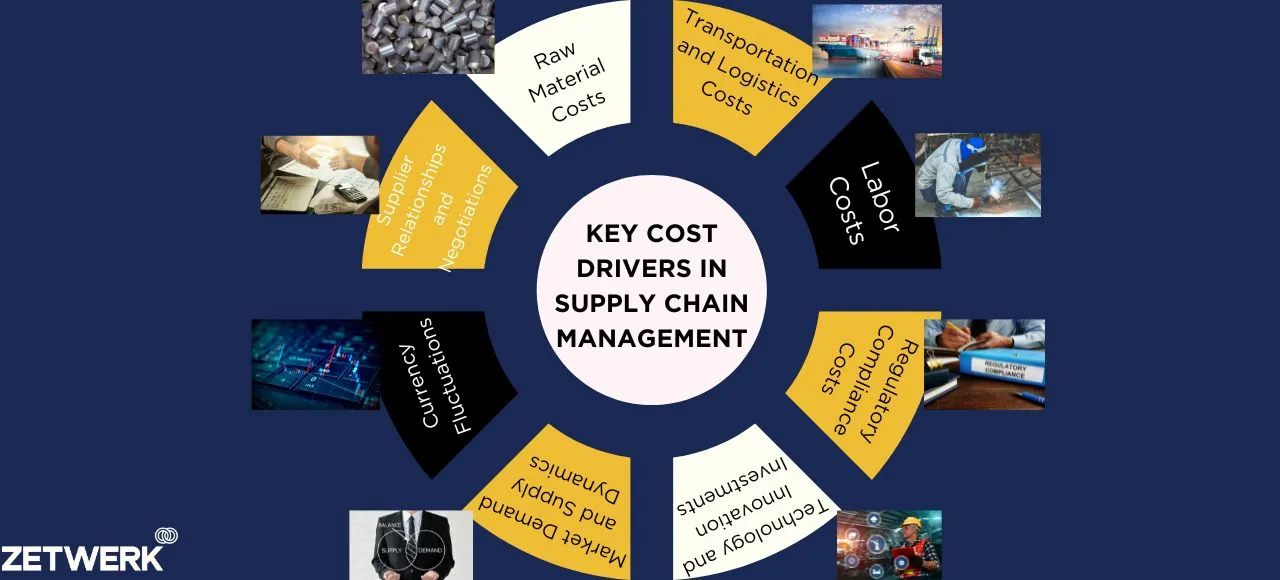
- Raw Material Costs: Raw materials form an integral part of the manufacturing process. Their prices can vary significantly due to shifts in commodity prices, exchange rate fluctuations, and geopolitical events. For instance, an increase in steel prices can directly impact manufacturers who rely on it, raising their production costs. A real-world example of this would be the automobile industry, which depends heavily on steel for car production. Similarly, political instability in regions that supply certain raw materials can affect both their availability and pricing. An example is the volatility in oil prices due to geopolitical tensions in the Middle East.
- Transportation and Logistics Costs: These include expenses related to shipping, freight, and customs duties. The choice of transportation method – whether air, sea, or land – and the chosen routes can significantly influence these costs. For instance, air freight is faster but more costly than sea freight, making it a less cost-effective option for bulk goods. For example, a furniture manufacturer might choose sea freight to transport large quantities to minimize costs. Additionally, changes in fuel prices can drastically affect transportation costs, as seen during the 2008 oil price spike.
- Labor Costs: Labor costs can significantly influence the final cost of a product or service, and these costs vary across regions. For instance, manufacturing in regions with high labor costs increases the overall cost, whereas regions with lower labor costs can reduce it. This is why many companies, such as Apple, outsource production to countries with lower labor costs like China.
- Regulatory Compliance Costs: Complying with various international and local regulations, meeting certification requirements, and maintaining compliance standards can add significant costs. For instance, industries like pharmaceuticals and food and beverages require rigorous testing and certification, incurring additional costs. For instance, a pharmaceutical company must adhere to the stringent guidelines outlined by the FDA in the United States, which can entail substantial costs.
- Technology and Innovation Investments: Incorporating advanced technologies such as automation, robotics, and data analytics into the supply chain initially increases costs but can result in long-term efficiency gains. For example, Amazon’s use of automation in their warehouses reduces manual labor and increases precision, reducing errors and waste in the long run.
- Market Demand and Supply Dynamics: Fluctuations in market demand and disruptions in supply chains can affect prices. A sudden surge in demand for a product can strain the supply chain, leading to increased costs. For example, the demand for personal protective equipment (PPE) during the COVID-19 pandemic led to increased costs. Similarly, a broken supply chain due to unforeseen circumstances can result in increased prices, as seen with many goods during the pandemic.
- Currency Fluctuations: For companies involved in international trade, exchange rate fluctuations can greatly impact costs. If a company imports raw materials and the value of their local currency decreases against the supplier’s currency, the cost of imported goods rises. For example, a British car manufacturer sourcing parts from Europe would have seen costs rise after the Brexit vote caused the pound to fall against the euro.
- Supplier Relationships and Negotiations: Building strong relationships with suppliers and having effective negotiation strategies can influence procurement costs. Long-term partnerships and collaborative approaches often result in better pricing agreements. For instance, a company like Walmart, which consistently orders large quantities from a supplier, might be able to negotiate lower prices due to their loyalty and the assurance of future business.
The factors previously discussed are only a handful out of numerous parameters that significantly impact costs in supply chains. It is absolutely vital for companies to establish a comprehensive visibility into these factors and persistently monitor their variations. Continuous monitoring and adjustment not only aids in cost optimization but also contributes to building resilient supply chains capable of withstanding unforeseen situations.
Strategies for Cost Control
- Supply Chain Visibility: Establishing comprehensive visibility across the entire supply chain allows businesses to identify cost drivers and potential areas for optimization. This involves tracking and monitoring every stage of the supply chain – from the procurement of raw materials, to the manufacturing process, and finally to the delivery of the finished product. By doing so, businesses can identify bottlenecks, inefficiencies, and wastage, and rectify these issues promptly. This reduces the likelihood of costly delays or disruptions. Moreover, visibility allows for better planning and management of resources, which can significantly cut costs. For example, if a business can track and predict raw material usage accurately, it can make more cost-effective purchasing decisions, avoiding overstocking or understocking.
- Cost-to-Serve Analysis: Conducting a cost-to-serve analysis involves understanding the true cost of serving specific markets, customers, or product lines by analyzing all associated costs throughout the supply chain. This comprehensive analysis includes costs related to sourcing, production, transportation, distribution, and after-sales services. By identifying high-cost areas, businesses can devise strategies to reduce these costs and improve profitability. For instance, if the analysis reveals high delivery costs for a particular product line, a business might consider changing its distribution strategy, such as localizing production or sourcing to reduce transportation costs. Additionally, this analysis can reveal if certain customers or markets are more expensive to serve and allow for strategic pricing decisions.
- Risk Management: Implementing risk management strategies is crucial to mitigate potential disruptions and uncertainties that can inflate costs. This includes having contingency plans for supply chain disruptions like raw material shortages, transport strikes, natural disasters, or shifts in demand due to market fluctuations or changes in consumer behavior. A well-prepared business can avoid emergency measures that are often costly and inefficient. For example, having alternative suppliers can prevent production delays when a primary supplier cannot meet demand, while surplus inventory can buffer against sudden demand spikes. Moreover, risk management can involve financial hedging strategies to protect against price fluctuations in commodity prices or exchange rates.
- Continuous Improvement: Businesses should adopt a culture of continuous improvement, which involves consistently seeking opportunities to enhance efficiency, reduce waste, and optimize processes. This commitment to improvement encourages innovation and adaptation, leading to cost savings over time. For example, a company might continuously train its employees to improve their skills, thus increasing productivity and reducing errors. Similarly, a business could regularly review and update its production process to incorporate new technologies or techniques that increase efficiency and reduce waste. This continuous improvement process is often driven by feedback and data, with regular performance reviews and adjustments based on performance metrics.
- Collaboration and Communication: Fostering collaboration and open communication with suppliers, distributors, and other partners can significantly impact cost control. By building strong relationships, businesses can negotiate better pricing, payment terms, and delivery schedules, leading to cost savings. Moreover, partners may collaborate on cost-saving initiatives, such as joint purchasing to leverage volume discounts, or shared logistics to reduce transportation costs. Open communication can also lead to improved supply chain performance, as partners can coordinate better to manage demand fluctuations, prevent disruptions, and solve problems more effectively.
- Technology Adoption: The strategic adoption of technology can significantly contribute to cost optimization in supply chains. Technologies like supply chain management software, analytics tools, automation and robotics, cloud computing, and artificial intelligence can enhance visibility, automate processes, improve decision-making, and increase efficiency. For instance, automation can reduce labor costs and eliminate human errors, while predictive analytics can improve demand forecasting, leading to optimized inventory levels and reduced holding costs. Cloud-based supply chain solutions can improve collaboration and information sharing among partners, while AI and machine learning can provide insights and recommendations for cost savings.
- Benchmarking and Best Practices: Regularly benchmarking your supply chain performance against industry best practices and competitors can provide valuable insights for cost reduction. This involves measuring and comparing key performance indicators such as order cycle time, fill rate, supply chain total cost, and inventory turnover. Benchmarking can reveal areas of underperformance where the business can learn from others to improve efficiency and reduce costs. For example, if a company’s freight costs are higher than industry averages, it might study how others have successfully reduced their freight costs and apply similar strategies.
- Sustainability Considerations: Taking into account the long-term impact of decisions on sustainability can also contribute to cost optimization. While reducing costs is essential, sustainable practices can lead to cost savings over time. For instance, by reducing energy consumption, waste, or carbon emissions, businesses can lower operating costs and potentially gain access to government incentives or avoid fines. Moreover, sustainability can enhance the brand’s reputation and customer loyalty, leading to increased sales. For instance, a company might use recycled materials or reduce packaging to lower material costs, while also promoting its commitment to sustainability to attract environmentally-conscious consumers.
In our discussion, we have delved into several noteworthy strategies that are widely accepted and actively implemented within the industry. These strategies aid numerous companies in their quest to streamline and optimize their supply chains. As an integral part of this process, Zetwerk provides you with unlimited manufacturing capacity and capability, delivering outputs at industry-leading lead times to any part of the globe.
Cost optimization in supply chains is far from being just a cost-saving measure. It is, in fact, a strategic approach that is designed to enhance operational efficiency, improve cash flow, increase competitiveness, and ultimately drive business growth. By leveraging innovative strategies and partners like Zetwerk, businesses are empowered to build robust and resilient supply chains that deliver value at every stage of the process.
Whether it’s a fledgling start-up sourcing components for their first product, or a multinational corporation managing a complex, global network of suppliers and distributors, the principles of cost optimization and efficient supply chain management are universally important. They form the backbone of any successful business operation, ensuring that products are delivered in the most efficient and cost-effective manner possible, thereby promoting sustainable business growth.



