In manufacturing, maintaining quality standards is crucial. Choosing the right partners through the supplier selection process is like forming a strong team. We assess if they can meet needs and ensure top-tier products. This process involves careful steps. In this blog, we explore how quality manufacturing and the supplier selection process collaborate for reliable products.
Understanding Supplier Quality Management
Supplier quality management is crucial in manufacturing. It ensures suppliers meet set requirements consistently. It’s not just about price; it’s building lasting partnerships. Effective management guarantees meeting specs, and timely delivery, and reduces quality risks, avoiding rework. Involving suppliers in design and open communication streamlines the supply chain, enhancing efficiency, innovation, and info flow.
Know About Quality Manufacturing Standards for Supplier Selection Process
Importance of Supplier Performance and Quality Management
Supplier performance and quality are vital in a reliable supply chain. Factors beyond costs impact efficiency and satisfaction. Transaction costs accumulate, affecting procurement expenses. Effective supplier performance management minimizes these costs through streamlined processes, clear communication, and issue resolution. Reliable delivery is crucial for schedules and customer satisfaction, while supplier quality ensures consistent deliveries and process stability.
Understanding the Quality Manufacturing Standards For the Supplier Selection Process
Quality manufacturing standards are pivotal in the supplier selection process, especially in supply chain management. When following the 7-step supplier selection process like manufacturing cost reduction, efficiency and production increase, etc., integrating supplier quality management best practices is essential.
Throughout this process, suppliers are evaluated against strict quality manufacturing standards to ensure consistent, high-quality product delivery. The steps encompass needs assessment, supplier identification, preliminary and comprehensive evaluations, on-site audits, quality performance metrics, and engagement with continuous monitoring.
Supplier quality management best practices underpin each step. This involves aligning product requirements with supplier capabilities, validating claims through audits, and measuring historical performance against quality metrics.
This approach guarantees that suppliers selected not only meet existing quality standards but also exhibit potential for ongoing enhancement. By fostering partnerships with such suppliers, supply chains benefit from resilience and maintained quality standards.
In essence, quality manufacturing principles, supplier selection, and comprehensive quality management practices synergize to minimize risks and enhance supply chain effectiveness, ensuring sustained excellence.
Here are some ASQ Quality Standards
Topic | Standard |
Quality Management | ISO 9000ISO 9001 |
Auditing | ISO 19011 |
Environmental Management | ISO 14000ISO 14001 |
Risk Management | ISO 31011 |
Social Responsibility | ISO 26000 |
Sampling by Attributes | Z1.4 |
Sampling by Variables | Z1.9 |
Food Safety | ISO 22000 |
Key Criteria for Supplier Selection
Selecting suppliers is crucial for top-tier products or services. Cross-functional teams with members from various sectors must define selection criteria aligned with their unique needs. This ensures a holistic evaluation process.
The common supplier selection criteria include:
- Relevant Experience: Look for suppliers with experience in similar projects or industries.
- Quality System Adherence: Prioritize those with strong quality systems and compliance with standards like ISO certifications.
- Capacity and Stability: Ensure suppliers can handle demand fluctuations and possess financial stability to prevent supply chain disruptions.
- Technical Support: The availability of technical support is vital for troubleshooting issues.
- Total Cost Evaluation: Assess both direct and indirect costs, such as transportation expenses.
- Track Record: Consider their history of improving business performance.
Certifications like CSQP, CMQ/OE, CQPA, CQIA, CSSBB, and CSSGB emphasize supplier quality. Suppliers with these certifications inspire confidence in meeting rigorous quality requirements.
Methods for Evaluating Potential Suppliers
Choosing the right supplier involves evaluating their capabilities and compatibility with your organization’s needs. Methods for assessing suppliers include:
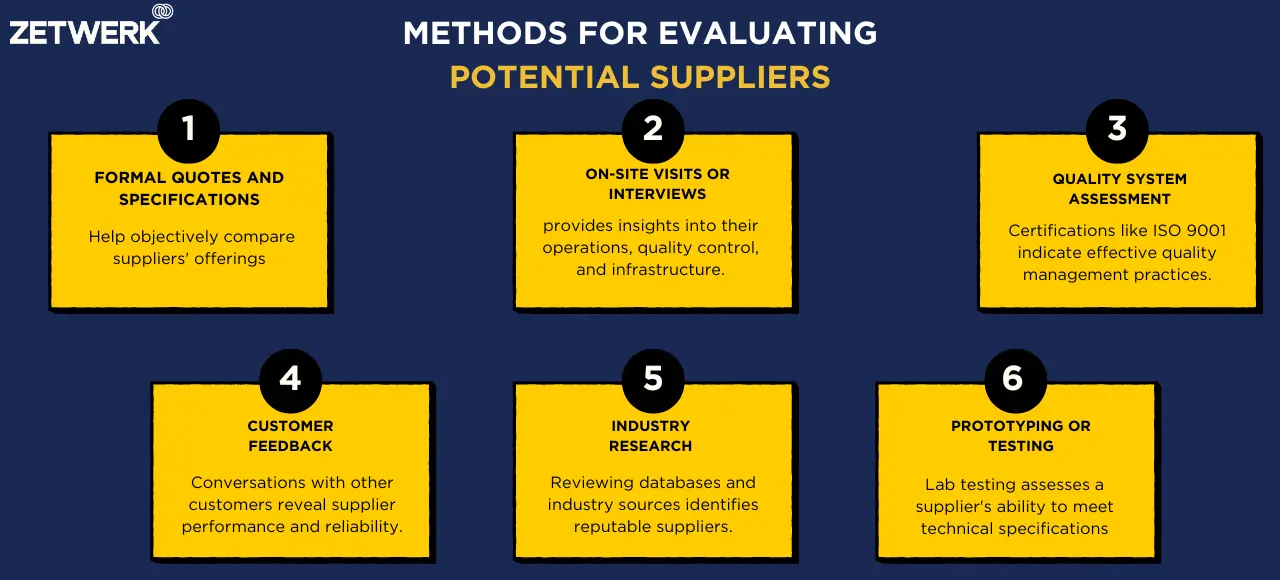
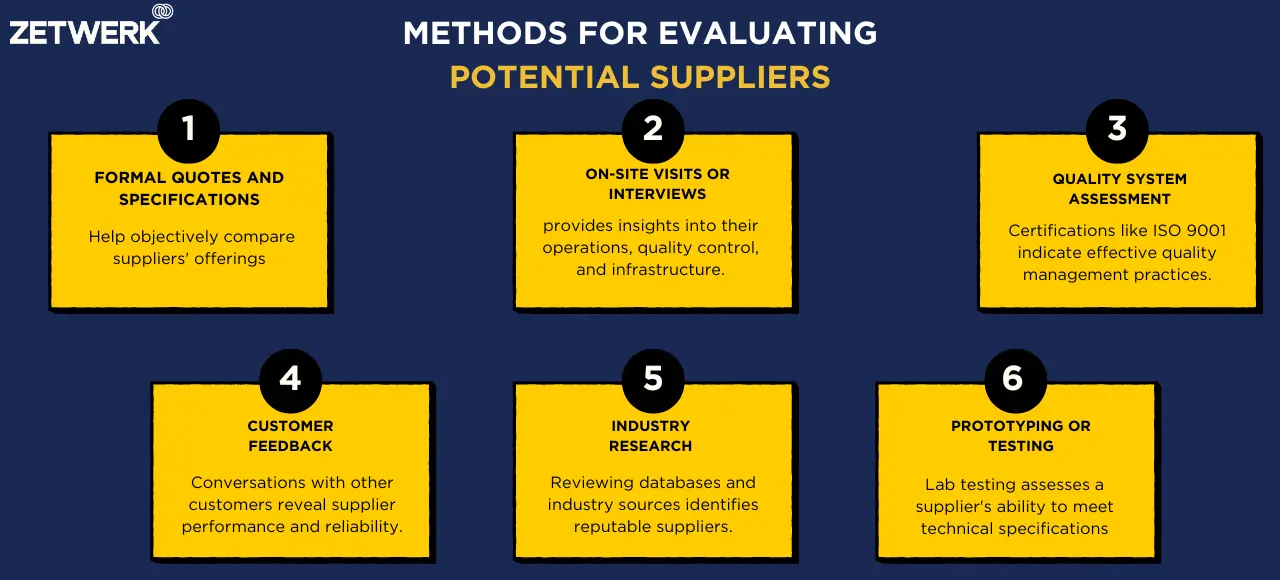
- Formal Quotes and Specifications: Detailed quotes and testing requirements help objectively compare suppliers’ offerings.
- On-Site Visits or Interviews: Meeting suppliers in person provides insights into their operations, quality control, and infrastructure.
- Quality System Assessment: Certifications like ISO 9001 indicate effective quality management practices.
- Customer Feedback: Conversations with other customers reveal supplier performance and reliability.
- Industry Research: Reviewing databases and industry sources identifies reputable suppliers.
- Prototyping or Testing: Lab testing assesses a supplier’s ability to meet technical specifications.
Thorough evaluation ensures the chosen supplier aligns with quality standards, capacity needs, and business goals.
Finishing up
In manufacturing, supplier quality management is crucial for satisfaction and success. Effective practices cut costs and ensure reliable delivery. Picking the right suppliers fuels innovation and savings. Trust-based ties enhance supply chain efficiency.
A strong selection process is vital and aligned with goals. Communication and conflict resolution ensure strong partnerships. Quality standards drive success through supply chain fluidity, excellent products, fair prices, ethics, and innovation.
Explore Zetwerk’s Knowledge Hub for articles on supplier selection quality standards. See how Zetwerk manufacturing services align with these standards to boost your procurement processes.




FAQs
The seven steps in the supplier selection process include determining requirements, creating evaluation criteria, identifying potential suppliers, pre-qualifying suppliers based on fit with requirements, sending formal requests for proposals (RFP), evaluating responses, conducting site visits/interviews/reference checks, and negotiating and contracting with the selected supplier.
Supplier evaluation and selection enhance supply chain management. They ensure quality inputs, competitive prices, reliable deliveries, lower disruption risk, better supplier communication, collaboration, and overall supply chain optimization.
Supplier quality management best practices are setting clear quality requirements, conducting regular audits, establishing strong inspection processes, maintaining open communication for issue resolution, and encouraging continuous improvement through feedback and corrective actions.
Use a scorecard system to transparently rate suppliers based on set criteria. Regularly assess key performance indicators in the supply chain for ongoing improvement and issue resolution.
Monitoring supplier performance is vital for consistent compliance. It ensures suppliers meet quality, delivery, and pricing expectations, while also catching issues early to prevent supply chain disruptions.