What is a Fastener?
In most cases, fasteners will be used to create a connection that is not permanent and can be dismantled without causing any damage to the components it connects. Welding is a technique that allows for the creation of joints that will last. Fasteners are typically crafted from metals like stainless steel, carbon steel, and alloy steel.
Types of Fasteners
- Temporary Fasteners: Temporary fastening is the process of joining components of a machine such that they can be readily separated or reconnected. Nuts, bolts, screws, lock pins, and washers are used for temporary fastening, referred to as fasteners.
- Semi-Permanent Fasteners: A fastener can be damaged but still function as a semi-permanent fastening technique. When the joints have minimal likelihood of opening again, it is used. Such fasteners include rivets and soldering.
- Permanent Fasteners: Permanent fasteners are made to permanently link two materials or components. The components will never separate when a permanent fastening is employed. Examples of permanent fasteners include rivets, welding, soldering, and brazing.
How are washers helpful to fasteners?
Washers have long been used to disperse the load under the bolt head and nut and to prevent damage to the joint surface during tightening. Conventional strength steel surfaces may become indented due to the tension under the face of a standard hexagon-headed nut. Silicon washers are considered to be the best washers in the industry.
Why are Silicon Washers the most useful?
Silicon washers are the best used in many industries because of their flexibility and other usability benefits. Silicone rubber washers are highly effective due to their unique properties. They offer outstanding resistance to ozone, weathering, and fungus. They work well with low compression setups, are resistant to UV light, and can withstand temperatures ranging from -73 C to +200 C. Special-grade silicone gives a broader temperature range between -73 C to +260 C. Silicone is thermally stable as well. These washers are the best alternative when washers need to adhere to strict FDA regulations for food or medical processing requirements.
Advantages of Silicone Washers
- Ozone-resistant : silicone rubber can withstand harsh weather and ozone without losing its suppleness or compressibility.
- Durable : They outperform metal washers in water resistance and are not as susceptible to condensation effects.
- Customization : Shape customization is possible since silicone rubber washers are flexible and can be molded into the necessary shapes and forms. They work best for producing a consistently tight fit and seal between two other pieces because of their flexibility
Industry Application of Silicone Washers
- Mechanical & Aquatic Industry : Silicone washers are round, flat rubber rings with a hole in the center to fit a fastener or let fluids pass through. These spacers can be used to stop leaks, safeguard surfaces, and reduce vibration in a number of applications. Rubber washers provide a better seal than metal washers in many applications because of their strength and flexibility. Silicone washers are used in pools, boats, and other aquatic items that frequently come into touch with water. They can also be used for plumbing, heating, ventilation, and air conditioning systems. Silicone washers are excellent for use as rubber spacers in machinery with regularly moving parts since they also absorb shock.
- Construction Industry : Silicone washers are manufactured for use as wear pads, wear springs, and spacers. They support threaded fasteners in the construction sector and are employed in the manufacturing of compressors. Silicone washers dampen vibration, seal fluid and liquid connections, cushion shocks, and insulate electric motors.
Who are Fastener Suppliers?
Fastener providers are businesses that distribute, produce or supply fasteners. They regularly adapt their operations to meet the needs of specific markets by providing specific fastener types to industries such as the military, construction, and medical applications. Fastener providers may also specialize in odd material types or focus on fasteners of a specific size to target a particular market segment.
Fastener producers employ various production processes to offer consumers fastening technologies, including casting, milling, injection molding, and others. The focus of the company may be on producing bespoke fasteners, materials, or both, or standardized fasteners such as those covered by ASME (American Society of Mechanical Engineers), ANSI (American National Standards Institute), or ISO (International Organization for Standardization). As a result of the low unit prices of these tools, fastener manufacturers routinely produce enormous quantities of components employing casting technology, automated equipment, and control systems to maintain high productivity
What are OEM Fasteners?
OEM (Original Equipment Manufacturer) refers to companies that manufacture goods and then include them as components of finished products that they sell to another company or directly to consumers. This practice is sometimes referred to as value-added reselling because the inclusion of the manufacturer’s products increases the value of the final product by adding features or functionality.
Fasteners of the highest grade, able to withstand various conditions and corrosion-resistant, are needed by numerous industries, including the OEM sector. You might need stainless steel fasteners customized to your projects and uses.
Zetwerk’s Custom OEM Fasteners
Custom fasteners are unique hardware components that are created to fulfill particular needs and specifications. The selection of raw materials, which can include a number of metals such as steel, aluminum, brass, and stainless steel, is usually where the manufacturing process for bespoke fasteners starts. Then, these raw materials are cut to the necessary length and shape using specialized cutting tools like saws and shears.
The custom fasteners are next formed and shaped, involving thread rolling, stamping, hot heading, and cold heading. The hot header includes heating the metal to a high temperature before shaping it, whereas the cold header involves using a press to mold the metal into the desired form. While thread rolling includes rolling threads onto the fastener, stamping entails using a die and press to mold the metal into the desired shape.
The bespoke fasteners undergo heat processing, including hardening, tempering, and annealing, after they have been produced and shaped. In order to increase the strength and hardness of the metal, hardening entails heating it to a scorching temperature and then swiftly cooling it. Later on, to increase the metal’s ductility and toughness, tempering means heating it to a lower temperature. The subsequent heating stage is called annealing, which includes heating the metal to a high temperature and then slowly cooling it to make it more malleable and workable.
The custom fasteners then undergo a finishing procedure involving cleaning, polishing, and coating. Cleaning entails wiping away any debris, oil, or other pollutants from the fasteners’ surface; polishing entails bringing the fasteners’ surface into a smooth state; and coating entails covering the fasteners with a layer of protective material to shield them from corrosion and rust. After the custom fasteners are created, they are examined to ensure they adhere to all standards and specifications.






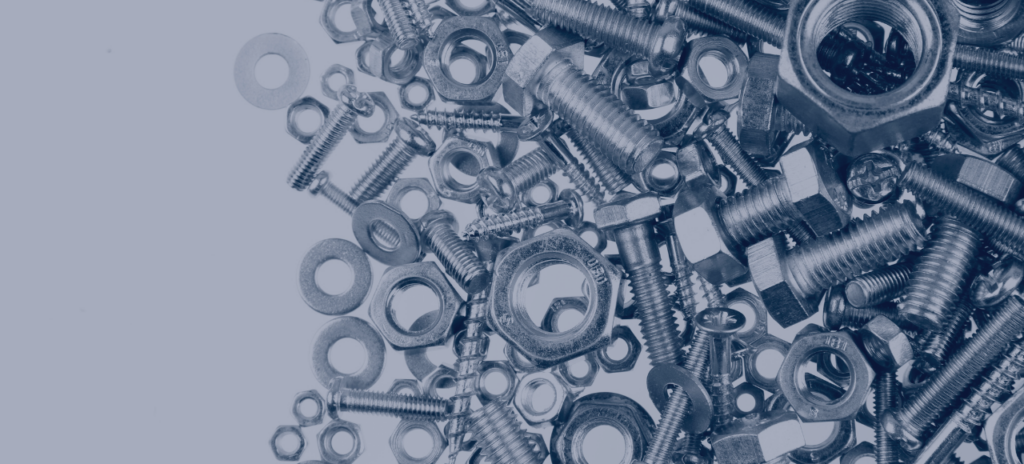
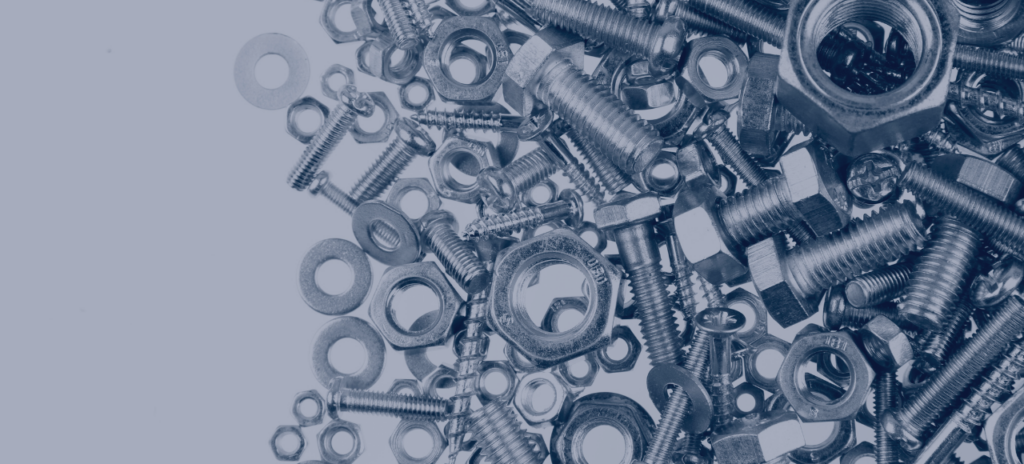