Mounting brackets play a pivotal role in the world of hardware, providing essential support and stability to a wide range of applications across various industries. These often-overlooked components come in diverse shapes, sizes, and materials, each designed for specific purposes. In this comprehensive guide, we’ll explore the world of mounting brackets, shedding light on their significance, types, materials, and manufacturing processes. We’ll also delve into their applications across industries, highlighting their indispensable role.
The Power of Mounting Brackets
- Understanding bracket applications : Mounting brackets encompass a broad spectrum of designs, each meticulously crafted to fulfill specific purposes. Consider adjustable shelving brackets – they empower us to create personalized storage spaces effortlessly. Wall mounting brackets silently ensure that our TVs and speakers are securely suspended, optimizing room layouts. Antenna mounting brackets are designed to facilitate optimal signal reception, while light and solar panel mounting brackets ensure the effective utilization of energy sources. The true power of these brackets lies in their capacity to adapt to diverse needs and functions.
- Precision in the mounting brackets: Approaching the production of mounting brackets from a manufacturing perspective entails precision, attention to detail, and a commitment to quality. These components are typically forged from robust materials such as stainless steel, aluminum, or high-grade plastics. Metal brackets often undergo intricate processes like cutting, stamping, and, in some cases, laser cutting to achieve their desired forms and dimensions. The choice of material and manufacturing methodology directly influences the bracket’s load-bearing capability and overall durability.
- Emphasis Quality Control and Assurance: Reliability is paramount when it comes to mounting brackets. To ensure their dependability, manufacturers employ rigorous quality control protocols. These encompass a range of testing methodologies, including stress tests, load tests, and assessments of corrosion resistance. Through these evaluations, manufacturers guarantee that their brackets can withstand varying degrees of pressure, diverse environmental conditions, and the test of time itself.
Significance of Mounting Brackets
Mounting brackets are the backbone of many structures, providing essential support and stability. They ensure that various hardware components stay securely in place, from shelves and cabinets to machinery and electronic devices. The significance of mounting brackets lies in their ability to:
- Distribute Weight: Brackets evenly distribute weight, preventing structural strain.
- Maximize Space: They allow for efficient use of space, especially in wall-mounted applications.
- Enhance Safety: By securely holding components, brackets prevent accidents and damage.
- Improve Aesthetics: Some brackets are designed to be discreet, enhancing the overall appearance of hardware.
Types of Mounting Brackets
There are different types of brackets based on their shapes, usage and manufacturing process involved. Lets dig deeper in each of these to get better insight of the same:
Mounting Brackets Based on Shapes:
- L-shaped Brackets: L-shaped brackets are widely used for supporting shelves, countertops, and various wall-mounted applications. They come in various sizes to accommodate different load-bearing requirements.
- U-shaped Brackets: U-shaped brackets are designed to hold round objects like pipes, bars, or cables securely. They are often used in industrial settings for cable management.
- T-shaped Brackets: T-shaped brackets offer support from both the top and the bottom. These brackets are commonly used in furniture and shelving applications.
Mounting Brackets Based on Usage:
- Wall-Mounting Brackets: Wall mounting brackets are versatile and designed to hold objects against vertical surfaces. Examples include TV brackets, wall shelves, and bike racks.
- Shelf Brackets: Shelf brackets are specially designed for supporting shelves. They come in various styles, including decorative and concealed options, enhancing aesthetics.
- Ceiling Brackets: Ceiling brackets are used to suspend objects from overhead structures. They are commonly used in lighting fixtures and curtain rod installations.
Mounting Brackets Basis of Application and Load Bearing Capacity
Adjustable Shelving Brackets:
The production of adjustable shelving brackets is a multifaceted process that begins with precision cutting and stamping of sheet metal or steel. Following this, bending machines are employed to achieve the required angles accurately. The critical welding phase joins various components, ensuring both structural strength and load-bearing capacity. Finally, the brackets are finished with techniques like powder coating to enhance their aesthetics, durability, and corrosion resistance. This intricate manufacturing process results in versatile and robust components.
Solar Panel Mounting Brackets
- The manufacturing of solar panel mounting brackets combines innovation and precision. Aluminum, known for its lightweight and corrosion-resistant properties, is a preferred material choice. The process starts with extrusion, where aluminum is pushed through a die to create the bracket’s shape. This method allows for intricate profiles and adjustable features.
- The brackets are designed to accommodate the specific dimensions and angle requirements of the solar panels. Various adjustable mechanisms are integrated into the brackets to ensure optimal solar panel positioning for efficient energy capture. To enhance durability and resistance to environmental factors, surface treatments like anodization are applied. Anodization involves creating a protective oxide layer on the aluminum’s surface, enhancing its corrosion resistance and providing a smooth finish.
- These manufacturing details underline the intricate processes and considerations involved in creating mounting brackets that meet stringent performance, durability, and functional requirements.
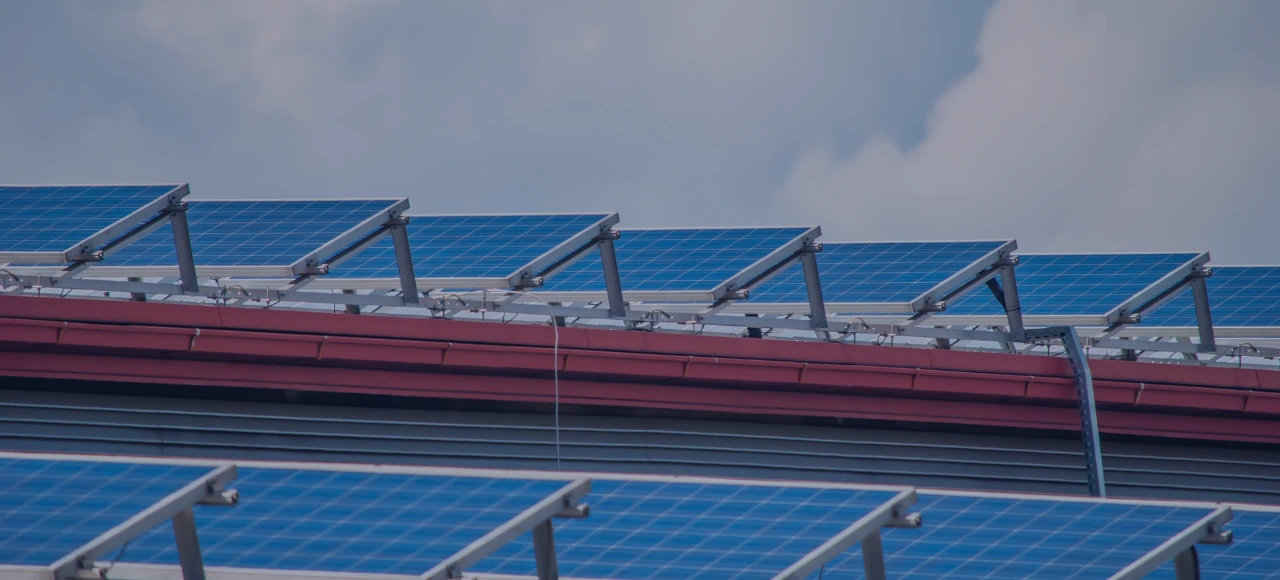
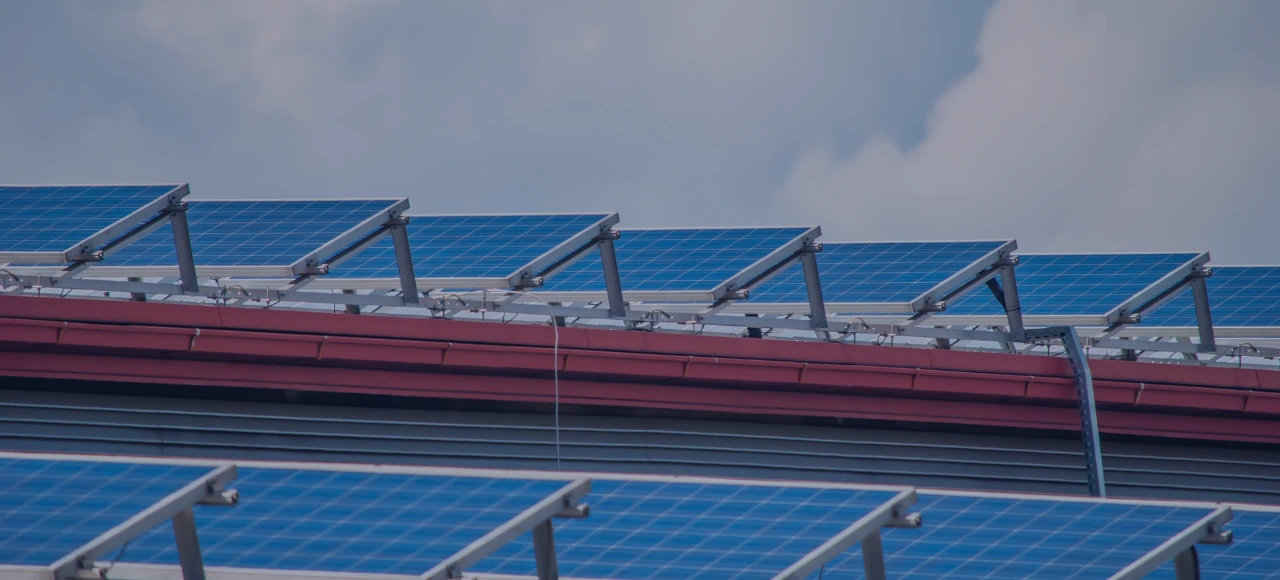
These are just a few examples of mounting brackets, and there are many more specialized brackets available for specific applications. The choice of bracket depends on the intended use, load-bearing requirements, and the characteristics of the item being mounted.
Bracket Type | Typical Applications |
L-shaped Brackets | Wall shelves, countertops |
U-shaped Brackets | Cable management, pipe support |
T-shaped Brackets | Shelving units, furniture support |
Wall-Mount Brackets | TV brackets, bike racks, |
Shelf Brackets | Shelving units, countertops |
Ceiling Brackets | Lighting fixtures, curtain rods |
Antenna Brackets | Telecommunications, broadcasting |
Solar Panel Brackets | Solar panel installations |
Light Mounting Brackets | Outdoor and architectural lighting |
Material Selection for Mounting Brackets
The choice of material for mounting brackets is crucial as it determines their durability, strength, and suitability for specific applications. Common materials include:
- Steel: Known for its robustness, steel brackets are used in heavy-duty applications where strength is paramount.
- Aluminum: Lightweight and corrosion-resistant, aluminum brackets are ideal for outdoor applications.
- Stainless Steel: Highly corrosion-resistant, stainless steel brackets are used in environments where rust is a concern.
- Zinc-Plated Steel: These brackets combine the strength of steel with a protective zinc coating, offering durability and corrosion resistance.
- Other Materials: Depending on the application, brackets can also be made from materials like plastic or composite materials.
Material | Strength | Corrosion Resistance | Weight | Typical Applications |
Steel | High | Varies | Heavy | Industrial, heavy-duty |
Aluminum | Moderate | High | Light | Outdoor, lightweight |
Stainless Steel | High | High | Moderate | Outdoor, corrosive env. |
Zinc-Plated Steel | High | Moderate | Heavy | General-purpose |
Other Materials | Varies | Varies | Varies | Application-specific |
Manufacturing Processes for Mounting Brackets
Mounting brackets are manufactured through various processes, each suited to different materials and designs. Some common manufacturing methods include:
- Metal Stamping: Ideal for producing brackets from sheet metal, metal stamping offers precision and efficiency.
- Die-Casting: Used for making brackets from metals with low melting points, die-casting allows for intricate designs.
- Extrusion: Aluminum brackets are often created through extrusion, which shapes metal by forcing it through a die.
- Welding: For fabricating heavy-duty brackets, welding is employed to join multiple components into a single, sturdy structure.
Conclusion
Mounting brackets are small but essential components that make a big difference in various industries. Understanding their types, materials, manufacturing processes, and applications empowers you to make informed decisions when selecting the right brackets for your projects. With Zetwerk’s assistance, you can access high-quality custom brackets that meet your specific requirements, ensuring the success of your hardware installations.
When it comes to realizing your bracket manufacturing needs across diverse processes, Zetwerk emerges as an invaluable partner. With a commitment to quality, efficiency, and a wide range of manufacturing capabilities, Zetwerk streamlines the process of bringing your bracket designs to life.
Incorporating Zetwerk as your manufacturing partner ensures that your bracket designs are realized with precision, durability, and a focus on quality. Whether your project involves die-casting, sheet metal fabrication, extrusion, or other processes, Zetwerk’s expertise supports your journey from design to the final product. With Zetwerk, your bracket manufacturing needs are not only met but exceeded.




FAQs
Mounting brackets are designed with specific applications in mind. It’s crucial to choose the appropriate bracket tailored to your installation’s requirements.
For outdoor applications, materials like stainless steel and aluminum are often preferred due to their corrosion resistance and durability. Stainless steel, in particular, is highly resistant to rust and can withstand harsh outdoor environments. Aluminum is lightweight, resistant to corrosion, and can be further protected with coatings or anodization for outdoor use. These materials are commonly used for outdoor mounting brackets to ensure long-lasting performance and structural integrity.
It depends on the load-bearing requirements. Heavy-duty brackets are suitable for industrial settings, while lighter ones suffice for residential use.