The quest for efficiency and productivity never ceases in the dynamic manufacturing world. Central to this journey is the concept of lean manufacturing projects. This approach, deeply rooted in maximizing productivity while minimizing waste, has become a pivotal strategy for numerous successful enterprises. A crucial yet often overlooked component in this equation is warehousing.
Understanding Lean Manufacturing
At its core, lean manufacturing is more than just a method—it’s a philosophy. It’s about the relentless pursuit of continuous improvement, always aiming to streamline operations and eradicate inefficiencies. This mindset isn’t confined to the production line; it permeates every aspect of a business, from supply chain management to agile project management in manufacturing.
Principles and Implementation of Lean Manufacturing
Lean manufacturing revolves around several core principles. To gain a deep understanding of lean and its applicability, it’s essential to comprehend these foundational ideas. Here are the principles of lean manufacturing and how it could be implemented:
Principle #1 Value
- At the heart of lean is defining value from the customer’s perspective. What does the customer want? This principle emphasizes understanding and delivering that value.
- Implementation: Begin by surveying customers, gathering feedback, and understanding market demands. Manufacturing projects should then be tailored to these identified needs.
Principle #2 Value Stream Mapping
- This involves mapping out every process involved in production and non-production activities, identifying those that add value and those that do not.
- Implementation: Use advanced tools and software to map the production process. Identify bottlenecks, wasteful processes, and opportunities for optimization.
Principle #3 Continuous Flow
- Aim for an uninterrupted flow of products through the production process, ensuring that products don’t wait around and waste time.
- Implementation: Integrate automation and advanced machinery to ensure a seamless flow of products. This might include robotic arms in assembly lines or AI-driven logistics planning.
Principle #4 Pull Production
- Instead of producing in large batches, produce based on actual demand. This reduces overproduction and inventory costs.
- Implementation: Implement Just-In-Time (JIT) production techniques. This involves closely monitoring inventory and producing goods only when there’s a demand, reducing inventory holding costs.
Principle #5 Perfection
- Constantly strive for perfection by continually identifying and eliminating waste.
- Implementation: Adopt a culture of Kaizen or continuous improvement. Regularly organize Kaizen events where teams identify waste and devise strategies to eliminate it. Using AI can help in predictive maintenance, ensuring machinery operates optimally.
By understanding principles and its implementation, manufacturing projects can be streamlined, waste can be minimized, and maximum value can be delivered to the customer. This essence of lean has allowed numerous manufacturers to transform their operations and achieve unparalleled efficiency.
Supply Chain Optimization in Lean Manufacturing
The supply chain is the backbone of manufacturing. Lean principles applied here can drastically reduce lead times, improve supplier relationships, and ensure a consistent flow of materials. By optimizing the supply chain, manufacturers can respond more rapidly to market changes and reduce costs associated with holding and transporting inventory.
Embracing Agile in Manufacturing
While agile methodologies are traditionally linked with software development, they’ve found a home in the manufacturing sector. Agile project management in manufacturing emphasizes adaptability and swift response. Manufacturers can swiftly pivot in response to changes or unforeseen challenges by segmenting projects into smaller tasks and frequently reassessing priorities.
Significance of the Manufacturing Gantt Chart
Visualization tools, like the manufacturing Gantt chart, are invaluable in project management. This chart offers a visual timeline of a project, showcasing when each task should commence and conclude. It aids in allocating resources and ensures alignment with the project’s objectives and timelines.
Lean Vs. Six Sigma
While lean manufacturing and Six Sigma aim to enhance efficiency and quality, they approach these goals differently. Lean focuses on eliminating waste from superfluous processes, while Six Sigma targets waste arising from process variations. However, when combined, they form ‘Lean Six Sigma,’ a robust methodology that harnesses the strengths of both systems.
Customer-Centric Approach in Lean
While lean manufacturing focuses on reducing waste and improving processes, the end goal is always to deliver more value to the customer. Adopting a customer-centric approach means constantly seeking feedback, understanding market needs, and ensuring that manufactured products align with customer expectations.
Image: Five Lean Principles
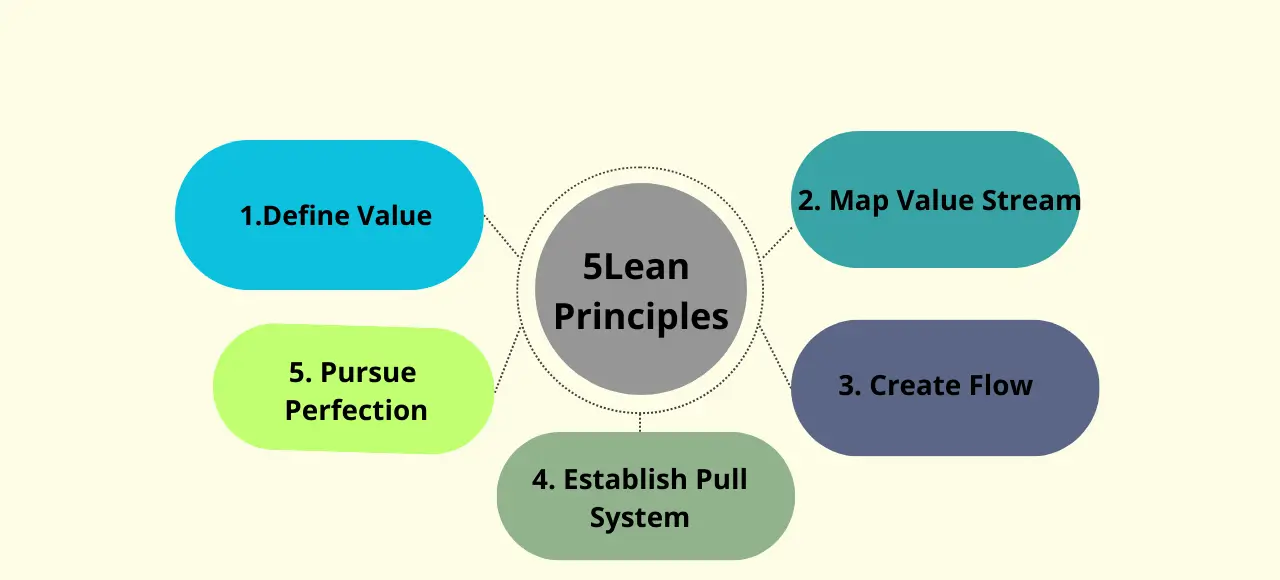
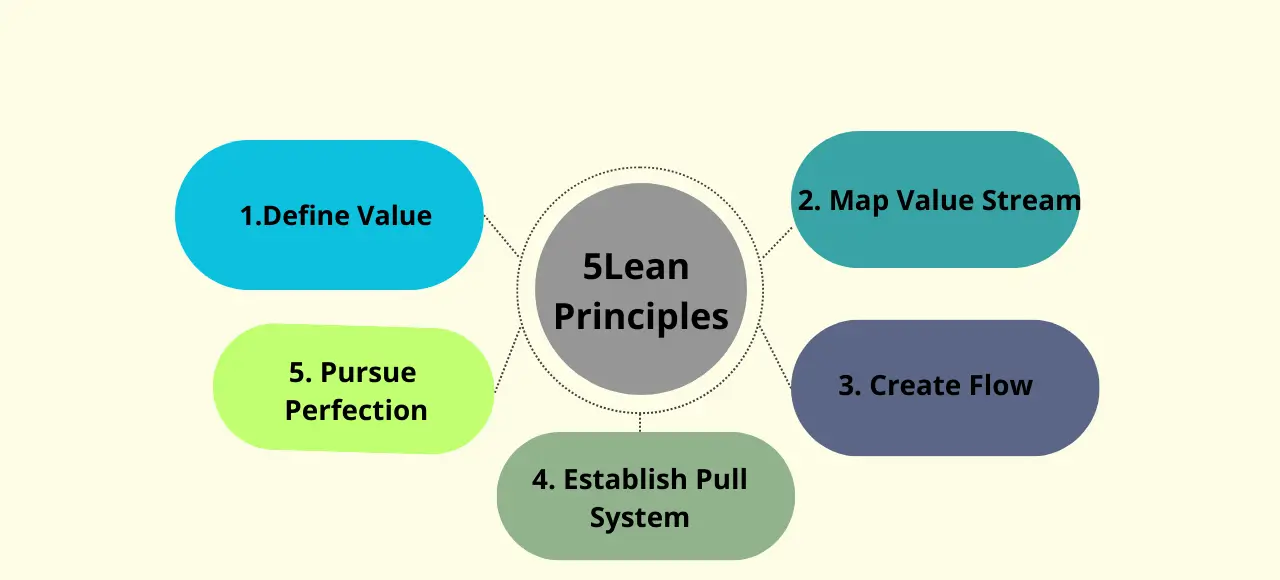
Embracing Industry 4.0 in Lean Manufacturing
- The fourth revolution, Industry 4.0, is making significant waves in the manufacturing sector. Manufacturers are achieving unprecedented levels of automation and smart production by integrating cyber-physical systems, the Internet of Things (IoT), and cloud computing.One of the standout features of Industry 4.0 is real-time data collection. Sensors embedded in machinery and throughout the warehousing process can monitor and relay information instantaneously. This data-driven approach aligns perfectly with lean manufacturing projects, allowing immediate adjustments to reduce waste and enhance efficiency.
- Furthermore, smart factories, a cornerstone of Industry 4.0, are redefining the production process. With interconnected machinery that can communicate and make decisions autonomously, these factories optimize production flows, reduce downtime, and ensure that lean manufacturing principles are upheld to the highest standard.
- Incorporating these advanced technologies not only bolsters the efficiency of manufacturing processes but also positions businesses at the forefront of innovation, ready to meet the challenges of tomorrow.
Sustainability and Lean Manufacturing
In the modern manufacturing landscape, sustainability has emerged as a key concern. Lean manufacturing, emphasizing waste reduction, naturally aligns with sustainable practices. Manufacturers optimize operations by minimizing resource consumption, reducing waste, and contributing to a more sustainable and environmentally friendly production process.
Incorporating Green Practices in Lean
Lean manufacturing’s primary goal is to deliver value to the customer, and today’s consumers are increasingly valuing eco-friendly products and practices. By integrating green practices into lean manufacturing, businesses can reduce their carbon footprint, minimize environmental impact, and cater to a growing market of environmentally-conscious consumers. This includes recycling, using renewable energy sources, and reducing emissions.
Collaborative Work Environments in Lean
A collaborative work environment is crucial for the success of lean manufacturing. It’s not just about processes and tools; it’s about people.
Strategies to Foster Collaboration:
- Gemba Walks: This involves managers and leaders going to the production floor, observing processes, and interacting with employees. It fosters open communication and immediate feedback.
- Kaizen Events: These are focused improvement activities where a team comes together to solve a specific problem. It promotes teamwork and problem-solving.
- Cross-Training: By training employees in multiple skills, they gain a broader understanding of the process and can provide insights from different perspectives.
Future of Lean Manufacturing
Integrating advanced technologies like AI, AR, and blockchain can revolutionize lean manufacturing.
- Artificial Intelligence (AI): AI can predict equipment failures, optimize supply chains, and forecast market demands. For instance, AI algorithms can analyze historical data to indicate when a machine will likely fail, allowing for maintenance and reducing downtime.
- Augmented Reality (AR): AR can be used for training, allowing new employees to learn processes in a virtual environment. It can also assist in maintenance by overlaying digital information on physical equipment and guiding technicians through complex repair procedures.
- Blockchain: In lean manufacturing, blockchain can ensure transparency and traceability in the supply chain. Every component’s journey, from raw material to finished product, can be tracked, providing authenticity and reducing the chances of counterfeit products entering the supply chain.
By understanding and integrating these technologies, manufacturers can stay ahead of the curve, ensuring that lean manufacturing processes are efficient and future-ready.
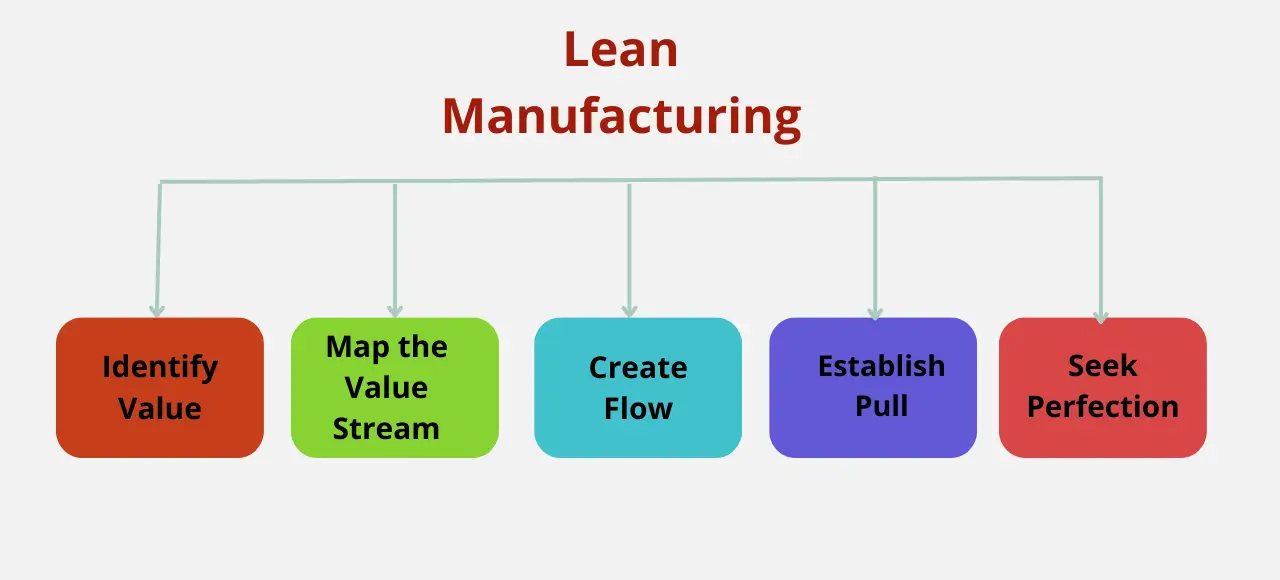
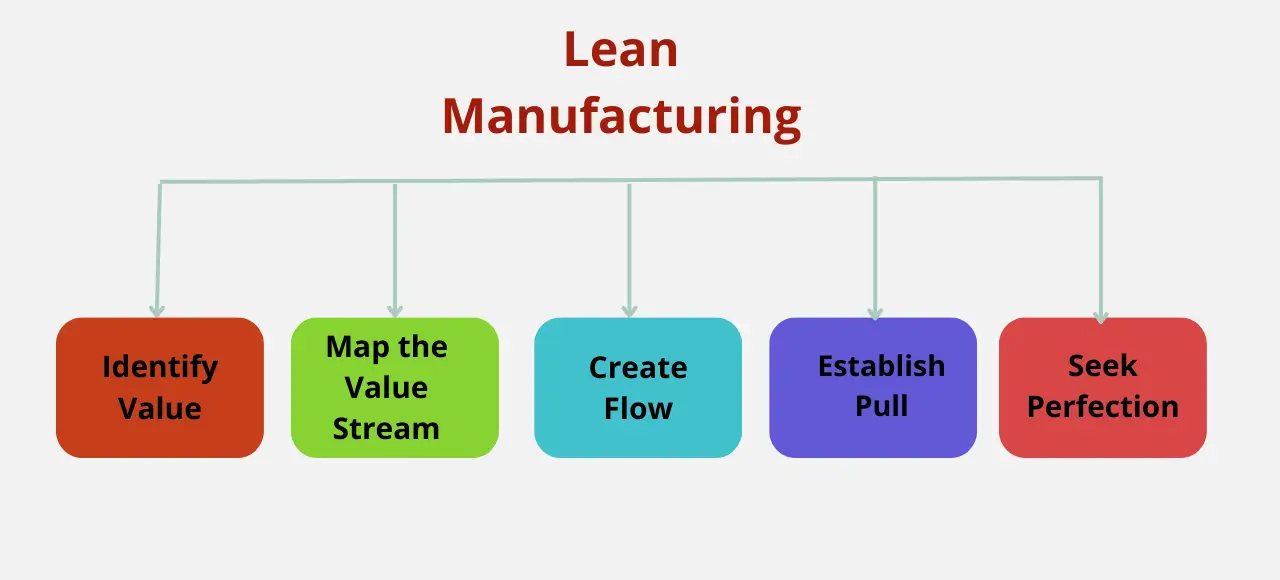
Lean Manufacturing in the Global Context
As businesses expand and globalization becomes the norm, lean manufacturing principles are being applied globally. This brings its own set of challenges and opportunities.
Global Supply Chain Management
Managing a supply chain across continents requires a keen understanding of local market dynamics, regulations, and cultural nuances. Lean principles can help streamline global operations, ensuring timely delivery of products and minimizing disruptions.
Cultural Considerations in Lean
Implementing Lean in a multicultural environment requires sensitivity to local work cultures. What works in one country might not work in another. Training programs must be tailored to address these cultural differences, ensuring that the essence of lean is communicated effectively.
Lean Manufacturing and Customer Experience
Beyond improving processes and reducing waste, lean manufacturing is pivotal in enhancing the overall customer experience.
Direct Feedback Loops
By implementing systems that capture customer feedback directly and in real-time, manufacturers can quickly adapt to changing customer needs and preferences. This ensures that the manufactured products always align with the customer’s desires.
Customization and Lean
Customers increasingly seek products tailored to their specific needs in today’s world. Lean manufacturing, emphasizing flexibility and quick response, allows manufacturers to offer customized solutions without significantly increasing costs or lead times.
Challenges in Implementing Lean
While the benefits of lean are numerous, implementing it has its challenges.
- Resistance to Change: One of the challenges is resistance from employees. Change can be daunting, and inertia often needs to be overcome.
- Short-term vs. Long-term Focus: While lean promises long-term benefits, it might sometimes require sacrifices in the short term. Balancing these short-term challenges with long-term goals is crucial for the successful implementation of lean.
In the ever-evolving manufacturing space, lean principles are pillars of efficiency and innovation. Zetwerk exemplifies this transformation, bridging traditional methods with modern approaches. As the industry landscape shifts, embracing these lean methodologies will be crucial for sustained success and delivering unparalleled value to customers.



FAQs
Lean manufacturing is centered around the relentless pursuit of continuous improvement, maximizing productivity while minimizing waste. It’s not just a method but a philosophy permeating every business aspect.
When applied to supply chain management, Lean principles can drastically reduce lead times, improve supplier relationships, and ensure a consistent flow of materials, leading to rapid responses to market changes and reduced inventory costs.
Though traditionally linked with software development, agile methodologies are relevant in manufacturing. They emphasize adaptability and swift response, allowing manufacturers to quickly adjust to changes by breaking projects into smaller tasks.
The Manufacturing Gantt Chart is a visualization tool crucial for project management. It provides a visual timeline of a project, aiding in resource allocation and ensuring alignment with project objectives and timelines.
While both aim to enhance efficiency and quality, lean focuses on eliminating waste from unnecessary processes, whereas Six Sigma targets waste resulting from process variations. When combined, they form ‘Lean Six Sigma.’