Plastic bushings
Plastic bushings, also known as plain bearings or sleeve bearings, are mechanical components used to provide a low-friction interface between moving parts and support shafts in various applications. They are designed to reduce friction, wear, and noise while supporting and guiding the moving parts. Plastic bushings offer several advantages over metal alternatives, including corrosion resistance, lightweight, self-lubrication capabilities, and lower cost. Choosing the best quality bushing plastic for various industrial needs is crucial to ensure machinery and equipment smooth and reliable operation. Bushings provide a low-friction surface between moving parts and support shafts.
Factors to Consider When Selecting the Best Quality Bushing Plastic for Industrial Applications
1. Material Selection
Several types of plastics are used for bushings, each with its own set of properties. The most common bushing plastic materials include:
- Nylon (Polyamide): Nylon is famous for its excellent wear resistance, low friction, and high strength. It can withstand high loads and operates well in various environments, making it suitable for general industrial applications.
- PEEK (Polyether Ether Ketone): PEEK is a high-performance plastic with excellent mechanical, thermal, and chemical resistance properties. It is suitable for extreme conditions and demanding applications.
- Acetal (Polyoxymethylene): Acetal offers good mechanical properties, low moisture absorption, and excellent dimensional stability. It is suitable for applications with moderate loads and speeds.
- PTFE (Polytetrafluoroethylene): PTFE is known for its exceptional low friction properties, chemical resistance, and wide temperature range. It is ideal for applications where lubrication is not feasible or desired.
- UHMWPE (Ultra-High Molecular Weight Polyethylene): UHMWPE exhibits high impact strength, excellent wear resistance, and low coefficient of friction. It is often used in applications with high abrasion potential.
The choice of material depends on factors like load, speed, temperature, environmental conditions, and specific industry requirements.
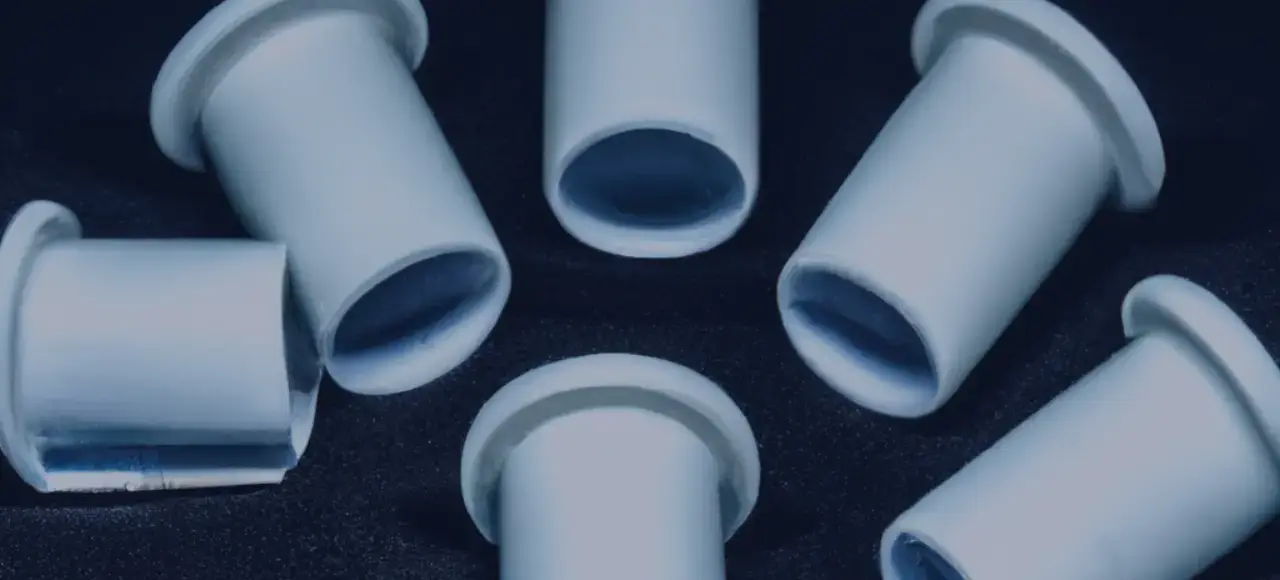
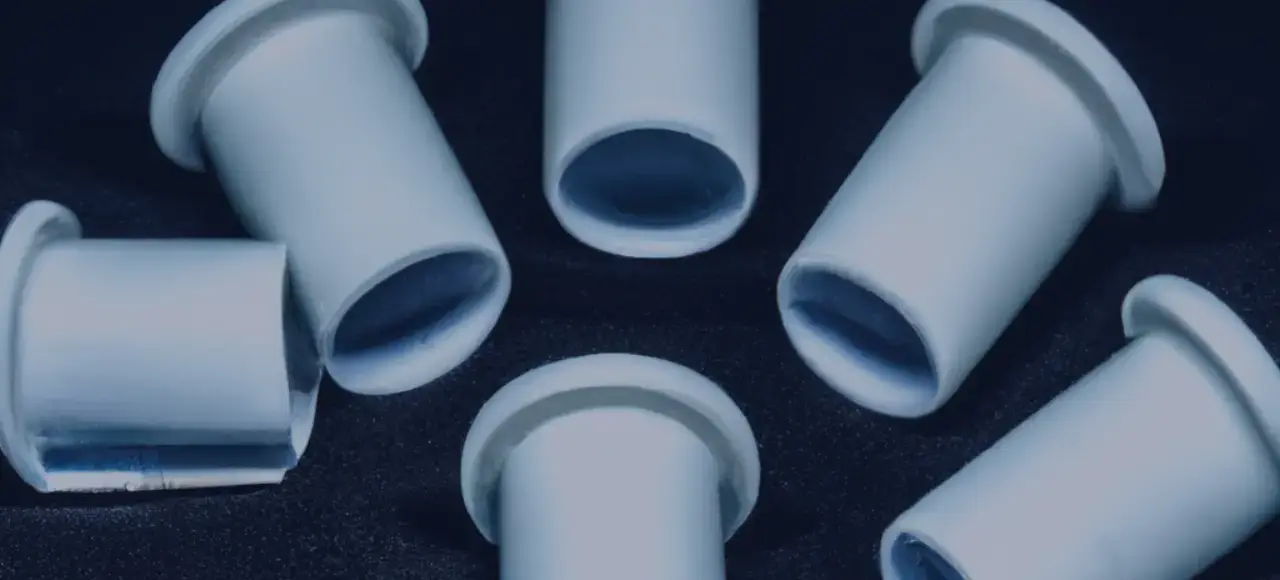
2. Load Capacity
Consider the expected load the bushing plastic will be subjected to during operation. High load capacities may require materials with superior strength and wear resistance, such as Nylon or PEEK.
3. Friction and Wear Properties
Low friction and wear are crucial for smooth and efficient operation. Select materials with self-lubricating properties or low friction coefficients, such as PTFE or UHMWPE, to reduce the need for additional lubrication and maintenance.
4. Temperature Range
Consider the operating temperature range of the application. Some plastics may lose their properties or become brittle at extreme temperatures, while others, like PEEK, can withstand high temperatures.
5. Chemical Resistance
Evaluate the exposure to chemicals, oils, or solvents in the operating environment. Choose a plastic material with appropriate chemical resistance to prevent degradation and premature failure.
6. Environmental Conditions
Consider factors such as humidity, UV exposure, and outdoor elements if the bushing will be exposed to such conditions. Some plastics are more resistant to environmental factors than others.
7. Dimensional Accuracy and Stability
Ensure the selected bushing plastic material provides good dimensional accuracy and stability to maintain proper fit and alignment.
8. Cost-Effectiveness
While prioritizing quality essential, consider the chosen material’s cost-effectiveness for the specific application.
9. Compliance and Certifications
Specific certifications or compliance standards may be required for certain industries or applications. Check if the chosen bushing plastic material meets those standards.
10. Supplier Reputation
Choose a reliable and reputable supplier that can provide high-quality bushing plastics with consistent performance.
Nylon Bushings
Nylon bushings are mechanical components made from Nylon, a synthetic polymer known for its excellent properties, making it a popular choice for various applications, including bushings. Nylon bushings are designed to reduce friction and wear between two moving parts, acting as a low-friction bearing surface.
Nylon bushings are used in various industries and applications, such as automotive, machinery, appliances, electronics, and more. They are commonly employed in hinges, pulleys, sliding mechanisms, and other moving parts, providing smooth and reliable operation. Here are some key characteristics and benefits of Nylon bushings:
- Corrosion resistance: Nylon is resistant to various chemicals and moisture, making it suitable for outdoor and harsh environments.
- Self-lubricating: Due to its low coefficient of friction, Nylon bushings exhibit self-lubricating behavior, which minimizes wear and extends the operating life.
- Insulating properties: Nylon is an electrically insulating material, making Nylon bushings suitable for applications where electrical conductivity should be avoided.
- Wear resistance: Nylon is a durable material that can withstand repeated use and abrasion, ensuring a long service life for the bushing.
- Low friction: Nylon has inherent lubricating properties, which reduce the need for additional lubrication and provide smooth movement between the mating parts.
- Lightweight: Nylon is a lightweight material, which can be beneficial in applications where weight is a concern.
To choose the best quality bushing plastic for various industrial needs, consider critical factors such as application requirements, friction characteristics, wear resistance, chemical compatibility, temperature range, load capacity, and environmental factors. Evaluate different plastic materials based on these criteria and select the one that offers optimal performance, longevity, and cost-effectiveness for your specific industrial application. Proper selection ensures smooth operation, reduced maintenance, and improved efficiency in machinery and equipment.




FAQs
Bushing plastics are mechanical components made from various plastic materials, such as Nylon, POM, and PTFE. They are used in industrial applications to reduce friction between moving parts, provide a low-friction bearing surface, and minimize wear and tear. Bushing plastics are chosen for their self-lubricating properties, wear resistance, chemical compatibility, and ability to withstand varying environmental conditions.
The temperature range varies depending on the type of plastic. Some plastics can withstand higher temperatures, while others have limitations. Consider materials like PTFE, which have excellent temperature resistance for applications with extreme temperature conditions.
Testing and prototyping are recommended whenever possible. Conducting tests under real-world conditions can help validate the performance of the chosen bushing plastic and identify any potential issues early on.
Look for suppliers with a strong reputation and experience providing bushing plastics for industrial applications. Check for certifications and customer reviews to ensure the supplier meets industry standards and delivers quality materials.