When you think of a warehouse, you likely envision a well-organized space where various goods are stored. However, not all warehouses operate in this way. Some have products haphazardly piled up in every corner. To combat this, many warehouse managers are now striving to improve their supply chain efficiency, product visibility, and overall productivity by streamlining their operations and storing goods more effectively.
One critical step in achieving this is using warehouse rack labels, which help ensure a smooth and efficient stock flow. As warehouses typically store a wide range of goods on racks, it is essential to categorize them with proper rack labels. This article will discuss warehouse racking, its installation methods, and the effective labeling strategies you can incorporate for organizing and protecting your product.
What Is Warehouse Labelling?
Warehouse rack labeling is essential for businesses shipping or storing products on racks within their warehouses. It is crucial in optimizing inventory management, minimizing errors, and enhancing overall efficiency. Warehouse racking labels come in various forms, such as barcoded labels, RFID tags, and magnetic labels, allowing businesses to choose the most suitable option based on their specific requirements and budget constraints. Regardless of the label type, the fundamental advantage remains consistent: the ability to swiftly and accurately locate products within the warehouse. So, implementing adequate warehouse rack labeling is necessary for businesses aiming to boost their operational efficiency and ultimately improve their bottom line.
How Do You Label a Warehouse Rack?
Labeling warehouse racks effectively depends on the warehouse’s unique requirements, making it a customized solution. Nevertheless, several general labeling tips can prove beneficial in most situations:
- Durable Materials: Use robust label materials to ensure longevity and readability, preventing premature wear and tear.
- Visible Placement: Position labels strategically for quick identification, enhancing efficiency, and reducing errors.
- Symbolic Coding: Employ symbols or colors on labels to categorize items or delineate different zones within the warehouse, aiding in easy navigation and organization.
By adhering to these guidelines, you can establish a well-organized and appropriately labeled warehouse.
Types of Warehouse Racks
There are wide varieties of racks available in the market for warehousing your product, such as:
- Pallet Racks: Designed for palletized goods, these racks offer efficient storage in rows and levels.
- Selective Racks: Common for general storage, these racks provide direct access to each pallet.
- Mobile Racks: Mounted on wheels or tracks, they allow for reconfigurable and space-saving storage.
- Double-Deep Racks: Blend accessibility and high-density storage by placing two pallets deep.
- Drive-In and Drive-Through Racks: Suited for high-density storage, allowing forklifts to enter and retrieve goods.
- Cantilever Racks: Ideal for long, bulky items like lumber or pipes, with open-fronted, horizontal arms.
- Pallet Flow Racks: Use a First-In, First-Out (FIFO) system, utilizing gravity to move pallets.
- Carton Flow Racks: Ideal for case-picking operations with a gravity-fed design.
- Push-Back Racks: Operate on a Last-In, First-Out (LIFO) system and offer high-density storage with fewer aisles.
- Mezzanine Racks: Create additional storage or workspace by adding a second level within the warehouse.
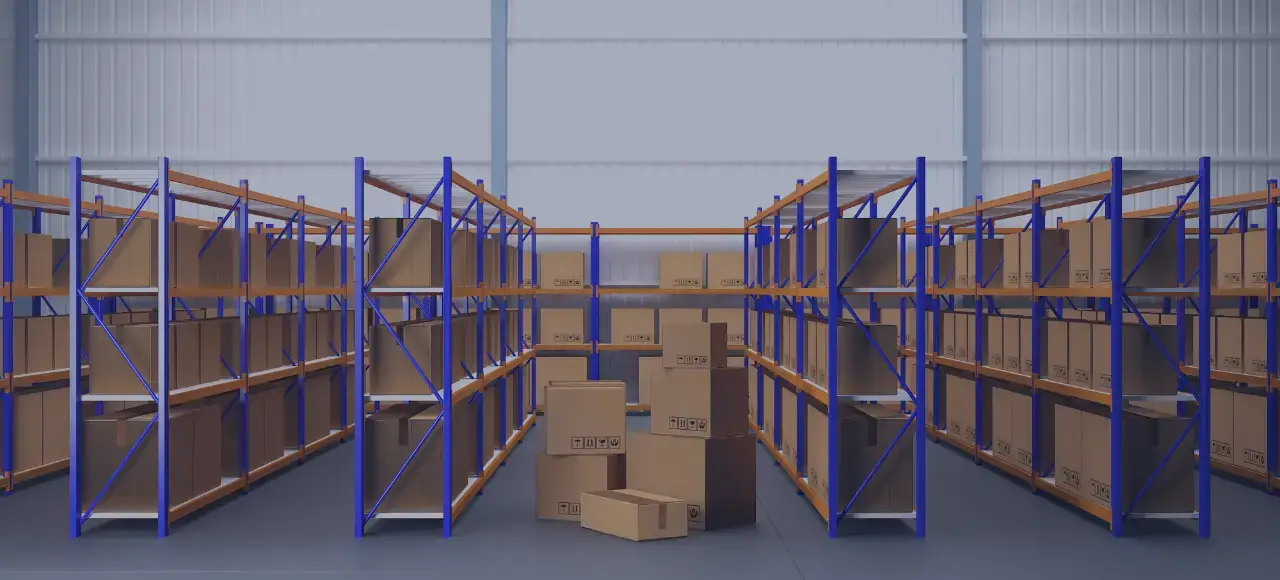
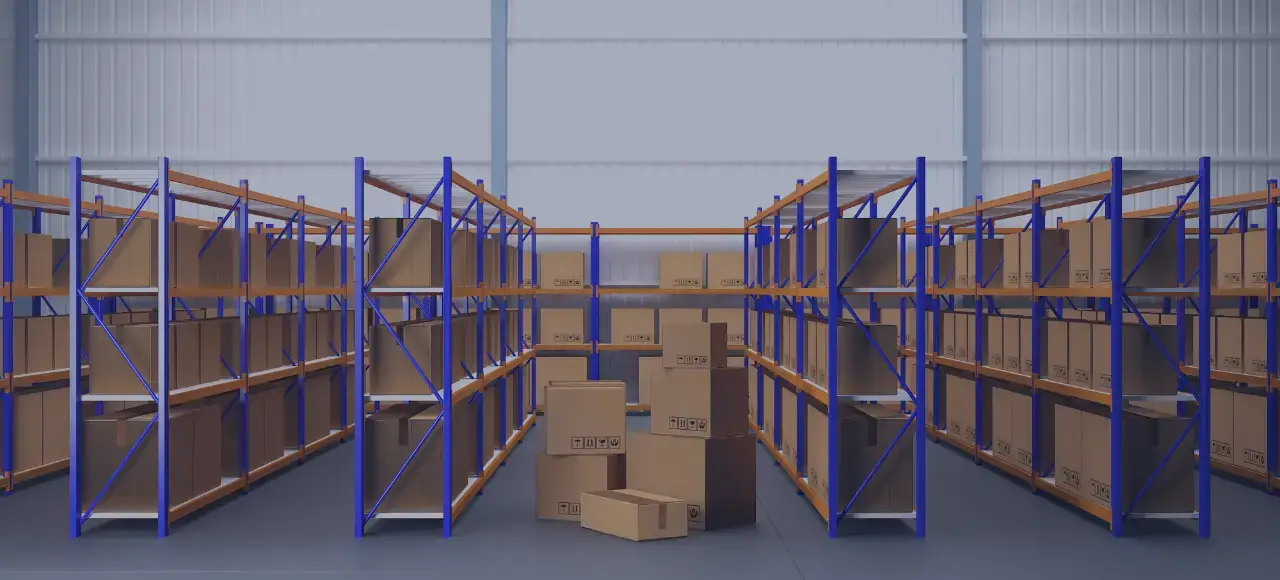
How to Design a Warehouse Racking Layout?
- Listen to Your Contractors & Managers: Before diving into your warehouse racking layout planning, consult with experienced professionals, including material handling experts, warehouse managers, and drivers. Share your goals and needs, and carefully consider their input and suggestions.
- Understand Your Storage Requirements: Your racking strategy begins with your storage system. Determine whether you store oversized pallets containing substantial goods or smaller pallets with individual or small items. Consider if you manage both high-flow and low-flow products. It’s crucial for your racking to align with your storage needs rather than altering them to fit the racking.
- Maximize Your Physical Storage: Designing an efficient racking system in a limited warehouse space means arranging racks in long rows, avoiding wall-stacked pallets, and eliminating inefficient layouts. Prioritize product access and optimize both floor and vertical storage.
- Plan for Expansion and Scalability: Plan for future warehouse storage expansion by opting for an adjustable and expandable modular racking solution. Alternatively, a tailored storage solution can now accurately predict and meet your current needs, reducing the likelihood of future overflow.
Practical Labeling Tips for Your Warehouse Racks
- Prepare Your Racks and Floor Spaces: Before labeling, ensure your racks are clean; otherwise, labels won’t adhere properly, wear faster, and visibility will diminish. Invest time in a thorough cleaning of both racks and warehouse space to optimize labeling effectiveness.
- Keep Your Layout and Labeling Plans at the Ready: Refer to your layout and plans as you rearrange racks. If you need to make significant changes, use them as references for product labeling. Avoid rushing, as oversights can lead to delays, slower shipping, and customer dissatisfaction, requiring additional corrective work.
- Use A Double-Digit Numerical Model When Labeling: When labeling your rack rows, start with “01” versus “1,” even if your warehouse racks don’t number in the double digits. This keeps the numbering conventions consistent and, as you grow, ensures you maintain that consistency as the number of racks and rises begins to scale.
- Label Your Warehouse Racks, Starting from the Bottom and Working Up: Start labeling from “01” at the bottom and progress upwards, considering standard or serpentine labeling. Consistency is vital, and if questions arise, seek guidance from your labeling provider for expert assistance.
Aspects to Consider for Warehouse Racking Installation
Safety First
Ensuring worker safety and uninterrupted operations in storage facilities necessitates compliance with local safety standards during warehouse racking installation. This is overseen by OSHA in the United States, while Brazil follows ABNT, and Mexico adheres to STPS regulations. Prioritizing load capacities, maximum rack heights, material quality, and post-installation inspections is vital for equipment longevity and accident prevention.
Materials or Goods Stored
A successful warehouse racking installation hinges on knowing the materials and goods to be stored. This informs the choice of racks, their arrangement, and the need for special storage conditions like cold rooms. Product characteristics, pallet types, and handling systems, such as FIFO for perishables, are vital in optimizing the process.
Types of Shelves
Choosing the right shelf type for warehouse racking installation is crucial based on space, indoor/outdoor placement, and goods’ needs. Options include conventional, narrow aisle, drive-in, drive-through, pallet flow, push-back, and double-deep racks tailored to specific storage requirements and accessibility preferences.
Equipment Needed
Warehouse racking installation requires specific equipment like forklifts, scissor lifts, and construction tools. Regulations, like ANSI standards in the U.S., mandate secure anchoring of shelving columns with base plates and quality anchor bolts to prevent accidents. Special tools such as concrete wedges are needed for concrete floors.
Facility Conditions
Assess property conditions before warehouse racking installation, considering load-bearing capacity, vehicle access, and clearance from safety systems. Taller buildings may necessitate new forklifts for top-level racks, potentially adding extra costs.
Final Words
Warehouse Rack Labeling not only reduces storage errors and improves traceability, but it also contributes to overall operational excellence. They promote better inventory management, helping maintain optimal stock levels and preventing overstock or stockouts. This enhances the facility’s productivity and saves costs by reducing waste and errors. Moreover, effective labeling systems can support quick decision-making, as staff can quickly identify product locations and monitor their movement throughout the warehouse. This ultimately translates into a more agile and responsive supply chain, meeting customer demands with greater precision and speed.
FAQs
Essential safety considerations include compliance with safety regulations, secure anchoring of racks, and ensuring the load-bearing capacity of the floor.
Determine the right shelf type by considering space, goods, and accessibility needs. Options include pallets, cantilevers, or selective racks.
Factors to consider during assessment encompass evaluating the facility’s suitability for specific storage requirements, examining temperature control needs, and determining if any modifications are necessary to accommodate the desired racking system.
Consistent numbering (e.g., starting with “01”) maintains uniformity as your warehouse expands, preventing numbering issues as the rack count grows.
Maintain labeling consistency by starting from the bottom and working upwards, considering standard or serpentine labeling, and seeking guidance from labeling providers for expert assistance when challenges arise.