Counterweights, often overlooked, hold a pivotal role within the industrial landscape, harmonizing the delicate balance between safety and productivity. Their meticulously engineered design serves a plethora of functions spanning diverse sectors such as construction, manufacturing, transportation, and entertainment. In this article, we shall embark on a comprehensive journey into the realm of counterweights, unraveling their myriad applications and their indispensable role in preserving equilibrium within our industrial domains.
Counterweights Applications Construction
Cranes and hoists
- Tower Cranes: Counterweights are often used on the opposite side of the load to balance the crane’s weight and prevent it from tipping over.
- Mobile Cranes: Counterweights can be added to the rear of mobile cranes to maintain stability while lifting heavy loads.
- Construction Elevators: Counterweights are used in construction elevators to balance the weight of the elevator cab and ensure smooth vertical movement.
- Concrete pump trucks: Counterweights are added to the rear of concrete pump trucks to stabilize the boom and prevent tipping while pumping concrete to elevated locations.
- Excavators and backhoes: Counterweights are integrated into the design of excavators and backhoes to offset the weight of the front-mounted digging bucket or attachment, ensuring stability during digging and lifting operations.
- Forklifts and telehandlers: Counterweights are often attached to the rear of forklifts and telehandlers to balance the weight of the lifted load, reducing the risk of tipping over.
- Aerial work platforms: Counterweights are often included in the design of aerial work platforms (e.g., cherry pickers, scissor lifts) to maintain stability when workers are elevated to perform tasks at height.
- Tunnel boring machines (TBMs): In tunnel construction, counterweights balance the massive cutting head of TBMs, ensuring that the machine remains stable while excavating tunnels underground.
Automotive Applications
- Engine balancing: Counterweights are often integrated into the crankshaft of internal combustion engines to balance the reciprocating motion of pistons and rods. This reduces vibrations, enhances engine longevity, and improves overall performance.
- Wheel balancing: Counterweights, typically in wheel weights, are used to balance the tires and wheels of vehicles. Proper wheel balancing ensures a smoother ride, minimizes tire wear, and improves fuel efficiency.
- Suspension systems: Counterweights are employed in suspension systems to balance the weight distribution between the front and rear axles. This improves handling, stability, and traction, especially in high-performance and off-road vehicles.
- Driveshaft balancing: In rear-wheel-drive and four-wheel-drive vehicles, counterweights are used to balance the driveshaft. This minimizes vibrations, reduces wear and tear on driveline components, and improves overall drivability.
- Anti-vibration mounts: Counterweights are sometimes incorporated into anti-vibration and engine mounts to minimize engine vibrations transmitted to the vehicle’s chassis, thereby improving ride comfort.
- Hybrid and electric vehicles: Counterweights are used in hybrid and electric vehicles to help balance the added weight of batteries and electric components, ensuring stability and handling are not compromised.
Aviation
- Aircraft control surfaces: Counterweights are often used in control surfaces such as ailerons, elevators, and rudders to balance the aerodynamic forces acting on these surfaces. This ensures stable and controlled flight, especially during maneuvers and changes in altitude.
- Flaps and slats: Counterweights are incorporated into movable flaps and slats on the wings of aircraft to facilitate take-off, landing, and control during various phases of flight. They help ensure proper deployment and retraction of these aerodynamic surfaces.
- Propellers and rotors: In propeller-driven aircraft and helicopters, counterweights balance the rotating components, reduce vibrations, and enhance overall performance. This is critical for smooth and efficient operation.
- Landing gear and gear doors: Counterweights can be used in landing gear and gear doors to assist in the extension and retraction processes, making them more reliable and efficient while minimizing the load on hydraulic systems.
- Cockpit instruments: Counterweights can be integrated into various cockpit instruments, such as gyros and indicators, to maintain accuracy and stability. This is essential for navigation, communication, and control.
- Rocket and space launch systems: Counterweights play a role in rocket propulsion systems to maintain stability during launch and flight. They help ensure that the rocket maintains its intended trajectory.
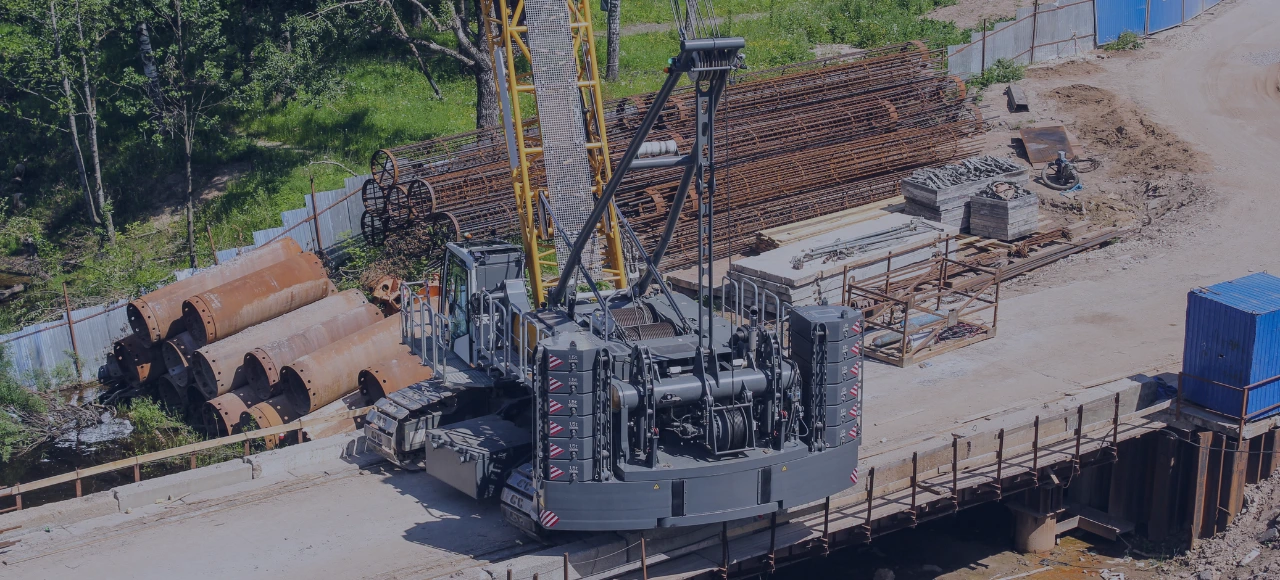
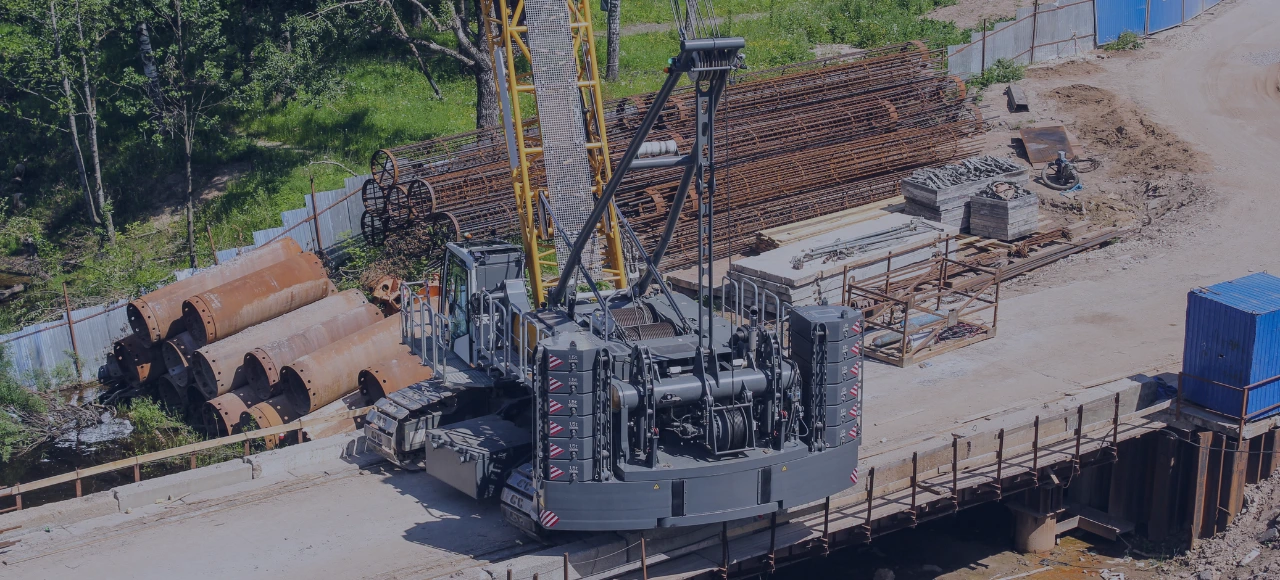
Material Handling and Manufacturing
- Conveyor systems: Counterweights are employed in conveyor systems to maintain tension in conveyor belts. This prevents slippage, ensures smooth material transport, and extends the life of the conveyor components.
- Elevators and escalators: Elevators and escalators utilize counterweights to offset the elevator car’s or escalator steps’ weight. This reduces the energy required for vertical transportation, improves efficiency, and ensures passenger safety.
- Rotating equipment: Counterweights are applied in rotary equipment like centrifuges and industrial mixers to counterbalance the eccentricities of rotating masses, minimizing vibrations and ensuring smooth operation.
- Damping systems: Counterweights are integrated into damping systems in manufacturing machinery to reduce oscillations and vibrations, which can lead to product defects and decreased machinery lifespan.
- Robotics and automation: Robots and automated systems often incorporate counterweights to balance their loads, improving accuracy and minimizing wear on robot joints and components.
- Pneumatic systems: Counterweights are applied in pneumatic systems to balance components like pneumatic cylinders, ensuring precise control of movement and positioning.
Renewable Energy
- Wind turbines: Counterweights are commonly used in wind turbines to balance the rotor blades and nacelle (the housing containing the generator and other components). Proper balance ensures the turbine operates efficiently and minimizes vibrations and wear on critical components.
- Solar tracking systems: Solar tracking systems, which follow the sun’s movement for optimal energy capture, often employ counterweights to balance and stabilize the movement of solar panels or mirrors. This maximizes the energy output of solar installations.
- Wave and tidal energy devices: Counterweights can be utilized in wave energy converters and tidal energy devices to help stabilize these structures and maintain their positions in the water, allowing them to capture energy from ocean movements efficiently.
- Hydroelectric power plants: In hydroelectric dams and power plants, counterweights are used in gate and valve systems to assist in opening and closing operations. They ensure precise water flow control, crucial for maintaining electrical generation and flood control.
- Geothermal well drilling: Counterweights are applied in drilling rigs used for geothermal well construction. They help balance the drill string, ensuring safe and efficient drilling operations.
- Energy-efficient building designs: Counterweights can be integrated into architectural designs, such as sun shades or louvers on buildings, to balance movable components and improve energy efficiency by optimizing natural lighting and shading.
Maritime Applications
- Ballast systems: Counterweights are widely used as ballast in ships to control stability, buoyancy, and trim. Ballast tanks are filled or emptied with water or other heavy materials to counterbalance the vessel’s weight, ensuring it remains upright and level.
- Hatch covers: Counterweights are used in hatch covers to assist in opening and closing, facilitating access to cargo holds while ensuring watertight integrity. This enhances cargo loading and unloading efficiency.
- Steering mechanisms: Counterweights are used in ship rudders to offset the hydraulic or mechanical forces required to turn the vessel. This ensures precise and responsive steering control.
- Mooring systems: Some mooring systems utilize counterweights to maintain tension in mooring lines and ensure that vessels remain securely anchored or berthed.
- Watertight doors: Counterweights are used in watertight and weathertight doors on vessels to facilitate easy opening and closing while maintaining a tight seal to prevent water ingress.
- Propulsion systems: Some ship propulsion systems incorporate counterweights to help balance rotating components, such as propellers or thrusters, reducing vibrations and enhancing efficiency.
In summary, counterweights’ versatile and essential role in various industries underscores their significance in modern engineering. Counterweights, such as those manufactured by companies like Zetwerk, continue to contribute to safety, stability, and efficiency from construction to automotive, aerospace, manufacturing, and even renewable energy. As industries evolve, the demand for innovative counterweight solutions will persist, making them indispensable components in the ever-advancing world of engineering and industry.




FAQs
Some advanced construction equipment may have systems that allow for dynamic adjustments of counterweights to adapt to changing loads or conditions, enhancing safety and efficiency.
Well-balanced components, including the crankshaft and wheels, can improve fuel efficiency by reducing friction and energy losses.
Yes, counterweights are used in electric and hybrid vehicles to optimize weight distribution and improve overall performance, just like in traditional internal combustion engine vehicles.
Counterweights are meticulously positioned and calibrated during manufacturing to ensure precise balance and performance. They undergo rigorous testing and quality control procedures.
Counterweights are essential in submarines and underwater vehicles to control buoyancy and depth, allowing for safe submersion and resurfacing.