Custom metalworks fuse artistry, engineering, and craftsmanship to create unique and functional pieces that adorn our world. From intricate sculptures to precision machinery components, this article delves into the technical journey of custom metal fabrication. Explore the process and challenges in turning concepts into finished metal masterpieces.
Conceptualization
- Inspiration and Vision: Every custom metal project begins with inspiration. This may be drawn from nature, architecture, art, or personal experiences. The vision for the project takes shape during this phase.
- Functional Requirements: Considerations like the purpose of the piece, its size, and intended use are essential. For instance, a custom metal railing for a staircase will have different requirements than a decorative metal sculpture.
- Budget and Materials: Determining the budget is crucial. It influences material choices, design complexity, and the project’s overall feasibility. Typical metals used include steel, aluminum, copper, and brass.
Design and Planning
- Sketching and Visualization: Translating the concept into a tangible design begins with sketches and drawings. Visualization tools like CAD (Computer-Aided Design) software enable precise design planning.
- Material Selection: Choosing a suitable metal alloy is essential for the project’s success. Factors such as durability, appearance, and cost affect material selection.
- Structural Engineering: Ensuring that the design meets structural and safety requirements is paramount. This involves calculations for load-bearing capacity and stress analysis.
- Design Iterations: The initial design may undergo several revisions to optimize aesthetics, functionality, and cost-effectiveness. Collaboration between the client and the metalworker is crucial during this phase.
Fabrication
- Cutting and Shaping:The chosen metal sheets or bars are cut and shaped according to the design. Techniques such as laser and plasma cutting or machining are employed for precision.
- Welding and Joining: MIG, TIG, or stick welding are standard custom metalwork methods.
- Bending and Forming: To achieve the desired shape, metal pieces are bent and formed using machinery like press brakes, rollers, or specialized dies. Precision is essential to ensure the final piece aligns with the design.
- Surface Finishing: The finish of the metal dramatically affects the final appearance. Options include polishing, grinding, sandblasting, and powder coating. Each finish technique imparts a unique texture and appearance to the metal.
- Assembly: If the project involves multiple components, they are assembled carefully, ensuring all parts fit seamlessly. This phase often requires meticulous attention to detail.
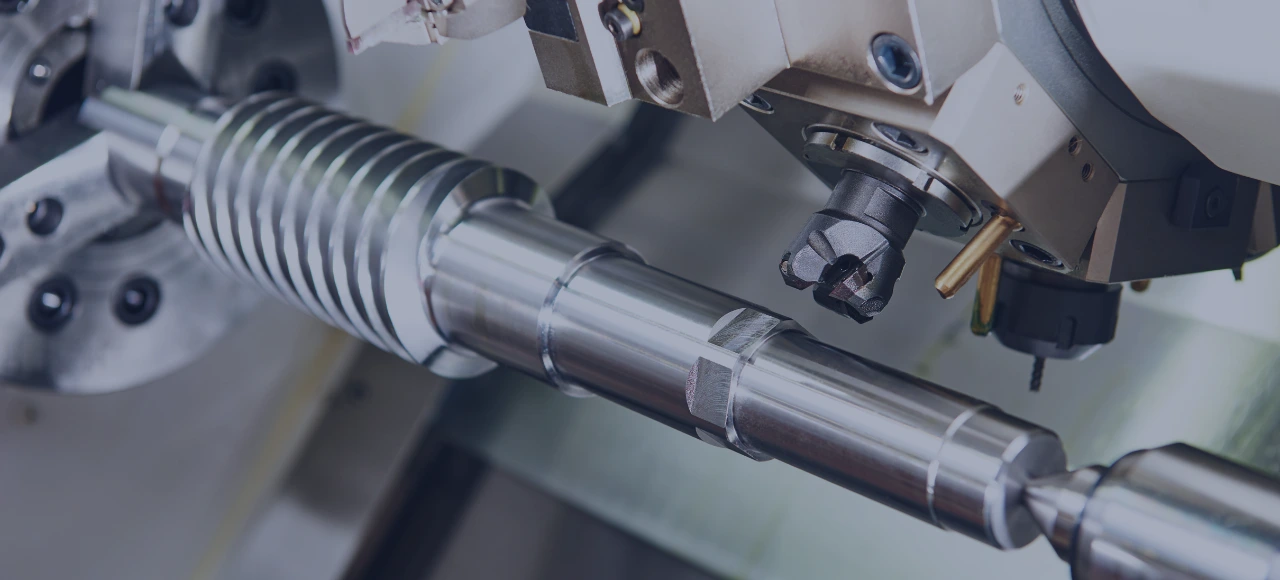
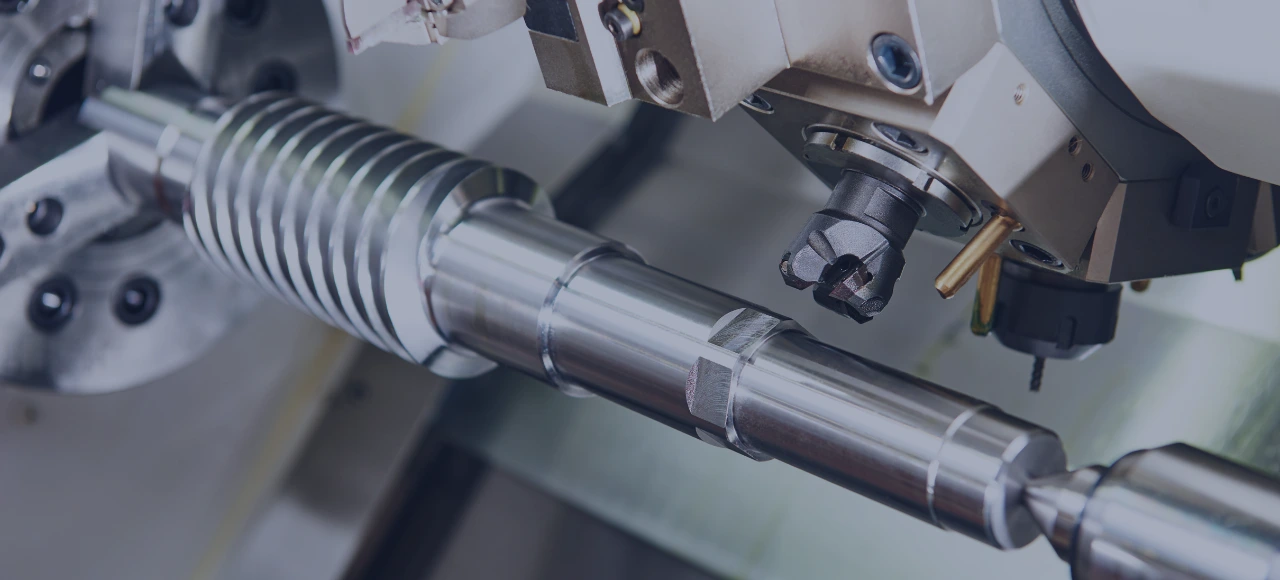
Quality Control
- Non-Destructive Testing (NDT): Techniques like ultrasonic and dye penetrant testing detect defects that may not be visible to the naked eye.
- Functional Testing: For components, functional tests are conducted to ensure they perform as intended. This might involve pressure testing, load testing, or thermal testing.
- Surface Inspection: The surface finish is examined for imperfections, and any required touch-ups or refinishing are performed.
- Client Approval: Before proceeding further, the client reviews the work to ensure it aligns with the initial vision. Any necessary adjustments or modifications are made at this stage.
Challenges and Considerations
- Material Selection: Choosing a suitable metal alloy is critical to meet performance requirements and budget constraints.
- Design Complexity: Complex designs may require advanced fabrication techniques and specialized equipment, which can increase costs and production time.
- Tolerances and Precision: Achieving precise dimensions and tolerances is crucial for functional components. This requires skilled craftsmanship and quality control measures.
- Environmental Factors: Outdoor installations must withstand weather conditions, so corrosion resistance and weatherproofing are essential considerations.
- Regulatory Compliance: Depending on the application, custom metalworks may need to adhere to industry-specific regulations and standards.
In summary, creating custom metal works, from concept to completion, is a meticulous journey marked by creativity, craftsmanship, and precision. Companies like Zetwerk play a pivotal role in this process, connecting clients with skilled artisans and ensuring the transformation of raw materials into functional artistry. This fusion of vision and skill produces not just available pieces but lasting works of art that impact clients and admirers alike.




FAQs
Metal sheet thickness is determined based on structural requirements, load-bearing capacity, and the intended use of the custom metal piece. Engineers and metalworkers calculate these factors to select the appropriate thickness.
Yes, custom metal works can include specialized features like embedded LEDs for lighting effects or kinetic components for dynamic movement. These features require careful integration and electrical expertise.
Yes, custom metal works can be combined with other materials to create unique designs. Metal and glass, for example, can be integrated to create striking architectural features.
Yes, there are industry standards for the thickness of protective coatings, such as ASTM (American Society for Testing and Materials) standards, which ensure proper protection against corrosion.