What is blockchain?
Blockchain, the digital record-keeping technology behind Bitcoin and other cryptocurrency networks, is not just a potential game-changer, but a revolutionary force in Finance and Supply chain management.
A blockchain is a distributed or decentralized ledger. It’s a digital system that records transactions among multiple parties in a verifiable, tamper-proof way. In the context of supply chain management, blockchain acts as a transparent and secure platform that allows for the efficient tracking of goods, verification of transactions, and prevention of fraud. The ledger can also trigger transactions automatically.
For cryptocurrency networks aimed at replacing fiat currencies, the primary function of a blockchain is to enable an unlimited number of anonymous parties to transact privately and securely without a central intermediary.
While the benefits of blockchain in supply chains are clear, it’s important to acknowledge the challenges. Higher computational overhead, managing decentralization, data complexity, buy-in with multiple parties, integrating with ERP applications, and application development complexity are all hurdles that need to be overcome for successful blockchain adoption.
Blockchain has already proven its potential to significantly enhance the performance of supply chains. Real-world examples of companies like Walmart Canada, IBM Food Trust, De Beers, Accenture, Barclays, Maersk, and Dubai are exploring the use of blockchain in intelligent logistics, paving the way for a future where this technology is the norm.
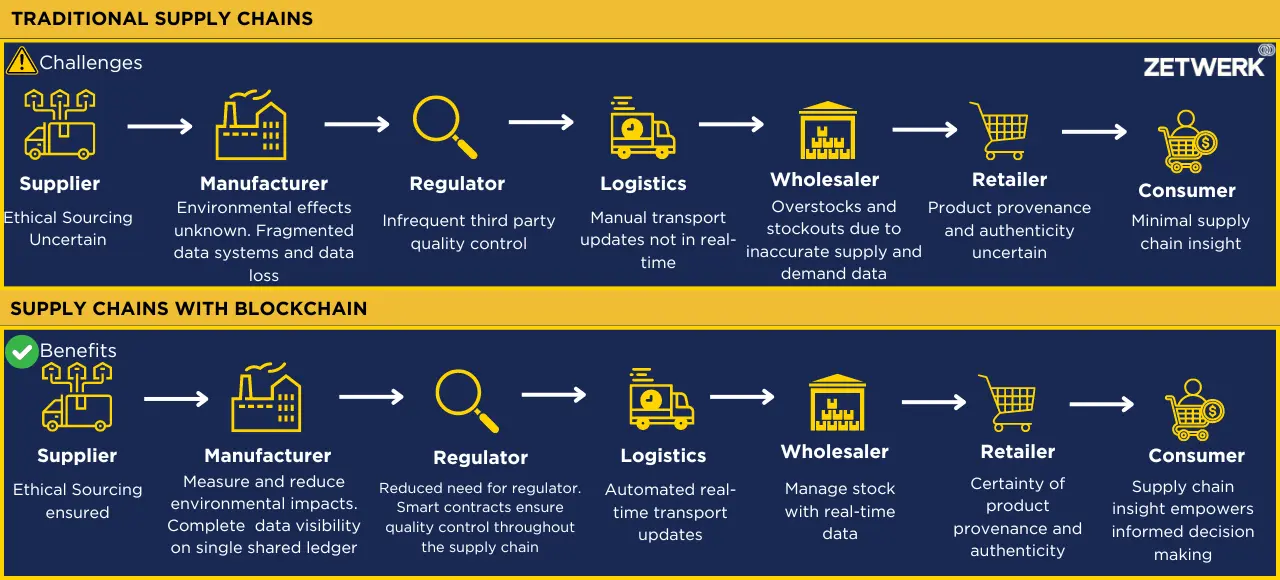
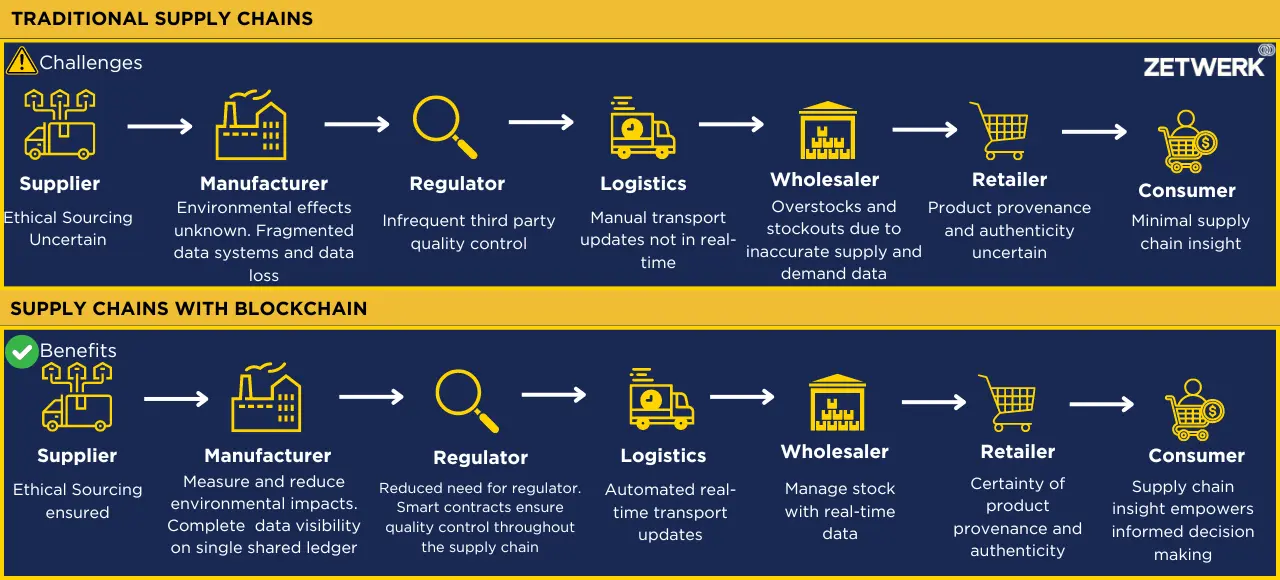
How blockchain helps supply chains: A hypothetical example
Consider a simple transaction involving a retailer who sources a product from a supplier and a bank that provides the working capital the supplier needs to fulfill the order. This transaction requires information, inventory, and financial flows.
However, note that not all three parties involved make financial ledger entries for a given flow. Current ERP systems, manual audits, and inspections cannot reliably connect these three flows, making it challenging to eliminate execution errors, improve decision-making, and resolve supply chain conflicts.
Existing financial ledgers and enterprise resource planning systems do not reliably allow the three parties involved in a primary supply chain transaction to view all relevant flows of information, inventory, and funds. A blockchain system can eliminate these blind spots.
Consider how the transaction in our example looks when represented on a shared blockchain (refer to exhibit 1). First, the retailer generates an order and sends it to the supplier. At this point, since no exchange of goods or services has taken place, there would be no entries in a financial ledger. However, with blockchain, the retailer records the digital token for the order.
The supplier then logs in the order and confirms to the retailer that the order has been received—an action that again gets recorded on the blockchain but would not generate an entry in a financial ledger. Next, the supplier requests a working capital loan from the bank to finance the production of the goods. The bank verifies the order on the shared blockchain, approves the loan and records the loan’s digital token on the identical blockchain. And so on.
Errors in execution—like getting inventory numbers wrong, losing shipments, or paying for the same thing twice—are often problematic to catch right away. Even if we find a problem later, it’s challenging and expensive to figure out where it came from or fix it by looking at the records of what happened.
ERP systems keep track of all kinds of movements, but it can be tricky to know which money transactions (like getting paid, paying bills, getting refunds, etc.) match up with which inventory moves. This is especially tough for companies that are doing lots of transactions every day with many partners and products.
To make things more complicated, supply chain tasks are often really complex. For example, orders, deliveries, and payments might not match up perfectly. An order might get split into different deliveries and bills, or several orders might get combined into one delivery.
A blockchain is valuable partly because it comprises a chronological string of blocks integrating all three types of flows in the transaction and captures details that aren’t recorded in a financial ledger system. Moreover, each block is encrypted and distributed to all participants, who maintain their own copies of the blockchain. Thanks to these features, the blockchain provides a complete, trustworthy, and tamperproof audit trail of the three categories of activities in the supply chain.
Blockchain thus dramatically reduces, if not eliminates, the ordinary execution, traceability, and coordination problems. Since participants have their own individual copies of the blockchain, each party can review the status of a transaction, identify errors, and hold counterparties responsible for their actions. No participant can overwrite past data because doing so would entail having to rewrite all subsequent blocks on all shared copies of the blockchain.
Applications and Advantages of Blockchain in Supply Chains
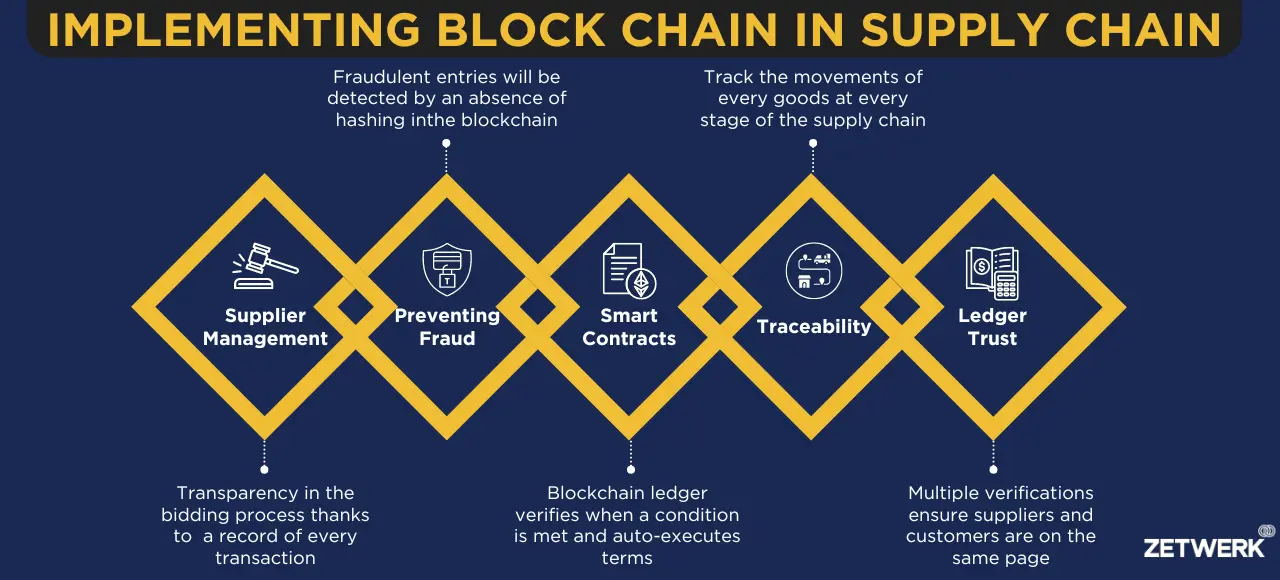
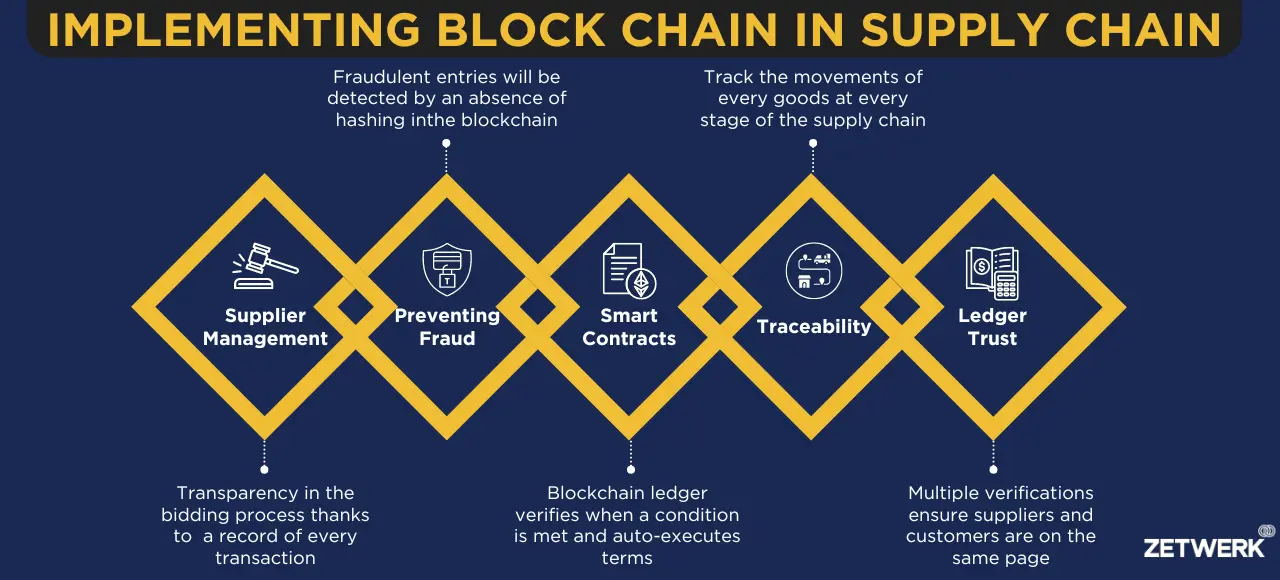
- Audit compliance
One common approach to improving supply chain execution is to verify transactions through audits. Auditing is necessary for ensuring compliance with contracts, but it’s of limited help in improving decision-making to address operational deficiencies.
For example, let’s take into account the problem a food company faces when its products reach the end of their shelf life in a retail store. A 2018 study in PubsOnline with a major manufacturer of packaged foods found that an audit or an inspection of inventory in a store can reveal the number of expired items, but it won’t explain the causes. Those can include glitches in any part of the supply chain, such as inefficient inventory management upstream, suboptimal allocation of products to stores, weak or sporadic demand, and inadequate shelf rotation (failure to put older products in front of newer ones). A record of all those activities can help reduce expirations.
- A valuable partner for traditional ERP systems
Led by companies such as Walmart and Procter & Gamble, considerable advancement in supply chain information sharing has occurred since the 1990s, thanks to enterprise resource planning (ERP) systems. However, visibility remains a challenge in large supply chains involving complex transactions.
Another way to strengthen supply chain operations would be to mark inventory with either RFID tags or electronic product codes that adhere to GS1 standards (globally accepted rules for handling supply chain data) and then integrate a company’s ERP systems with those of its suppliers to construct a complete record of transactions. This would eliminate execution errors and improve traceability. However, it’s important to note that integrating ERP systems is expensive and time-consuming.
Large organizations may have more than 100 legacy ERP systems—a result of organizational changes, mergers, and acquisitions over time. Those systems often do not easily communicate with one another and may even differ in how they define data fields. These challenges should be considered when planning to implement blockchain in supply chain management.
When blockchain record keeping is used, assets such as units of inventory, orders, loans, and bills of lading are given unique identifiers, which serve as digital tokens (similar to bitcoins). Additionally, participants in the blockchain are given unique identifiers, or digital signatures, which they use to sign the blocks they add to the blockchain. Every step of the transaction is then recorded on the blockchain as a transfer of the corresponding token from one participant to another.
- A caveat to blockchain adoption
It’s important to note that a blockchain would not replace the broad range of transaction-processing, accounting, and management-control functions performed by ERP systems, such as invoicing, payment, and reporting. Indeed, the encrypted linked list or chainlike data structure of a blockchain is not suited for fast storage and retrieval—or even efficient storage. Instead, the blockchain would interface with legacy systems across participating firms. Each firm would generate blocks of transactions from its internal ERP system and add them to the blockchain. This would make it easy to integrate various flows of transactions across firms.
Improving Financing, Contracting, and International Transactions
When companies use blockchain to share inventory, information, and money flows, it can lead to significant improvements in how supply chains work, especially for financing, making deals, and doing business globally.
Banks that lend money and offer credit to companies often struggle because they don’t have all the details about a company’s business, assets, and debts. Sometimes, a company might borrow money using the same thing as collateral from different banks, or it might get a loan for one thing and use it for something else. Banks try to manage these risks, but it ends up costing more, making it harder for small companies to get money when they need it.
Another area that could get better is managing what companies owe. It’s a complicated process involving sending bills, checking them against orders, keeping track of payments, and getting approvals at every step. Even though computer systems have automated a lot of this, people still have to step in a lot. And since both companies don’t always have all the facts, they often disagree.
Cross-border trade, like shipping things between countries, also needs to improve. It’s slow expensive, and there’s not much visibility into where things are.
But if companies use blockchain to share info about what’s being bought, sold, and paid for, it can make things a lot easier. When a supplier gets an order, a bank that’s part of the blockchain can quickly verify the same and make their payments. And when the buyer receives their material, the bank can quickly get paid back. Because there’s a clear record of what’s happened, and computers can handle a lot of the checking, there are fewer arguments between the bank and the company borrowing money.
Furthermore, many of these functions can be automated via smart contracts, in which lines of computer code use data from the blockchain to verify when contractual obligations have been met and payments can be issued. Smart contracts can be programmed to assess the status of a transaction and automatically take actions such as releasing a payment, recording ledger entries, and flagging exceptions in need of manual intervention.
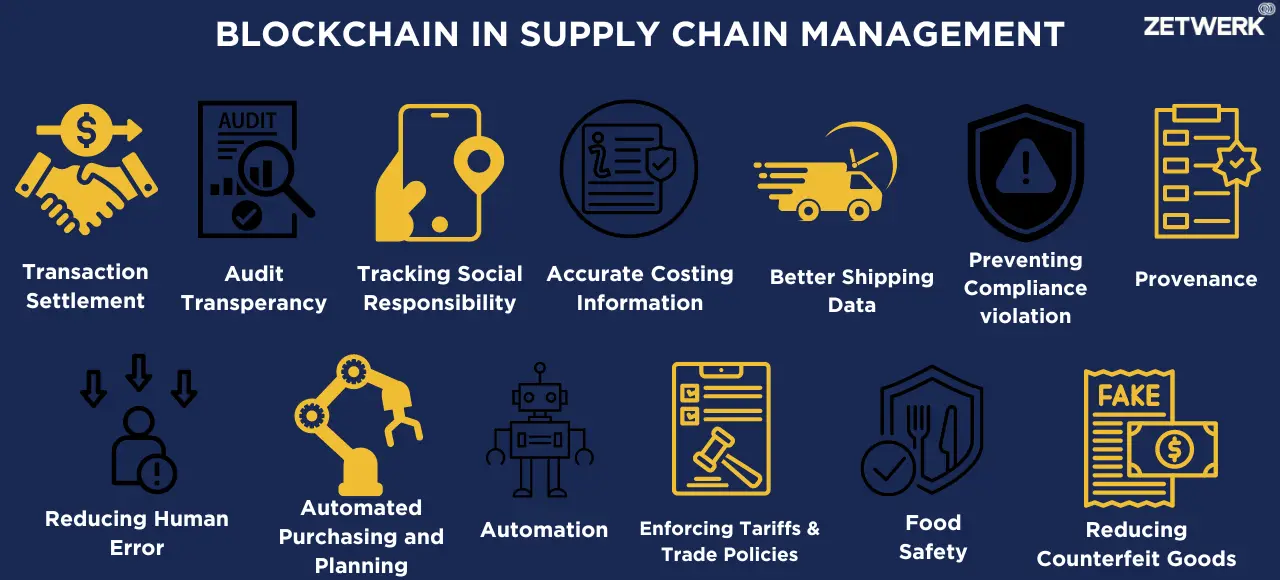
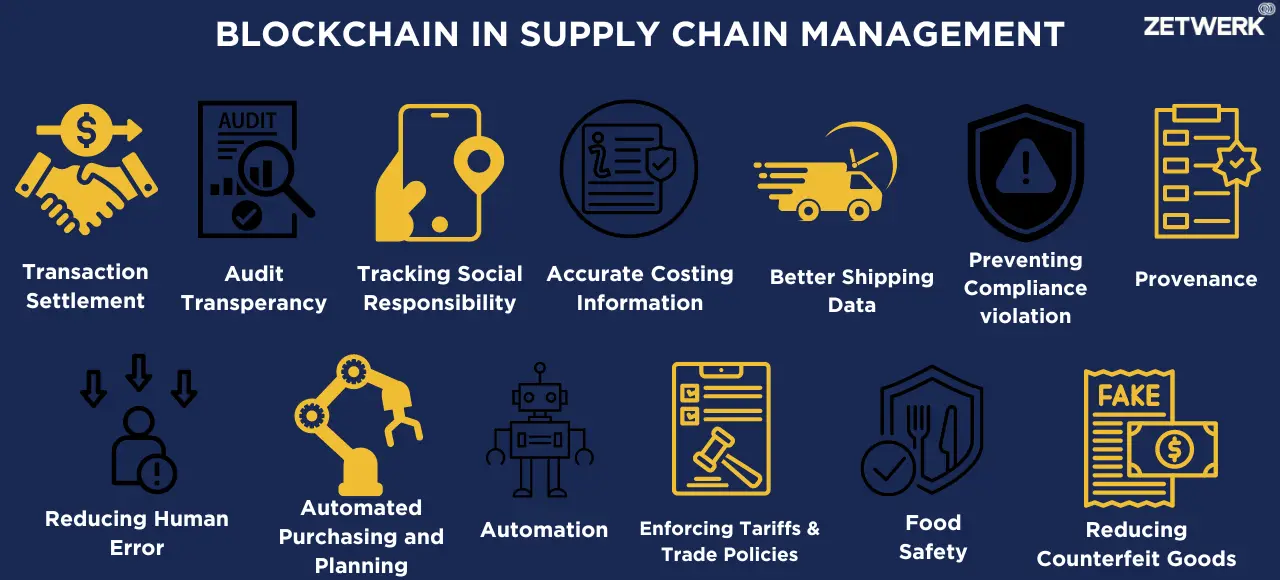
Real-world examples of blockchain being used
- Walmart Canada has already begun using blockchain with the trucking companies that transport its inventory. A shared blockchain makes it possible to synchronize logistics data, track shipments, and automate payments without requiring significant changes to the trucking firms’ internal processes or information technology systems.
- IBM Food Trust entered into a partnership with Walmart to use blockchain to trace fresh produce and other food products.
- De Beers mines, trades and markets more than 30% of the world’s supply of diamonds. The company plans to use a blockchain ledger for tracing diamonds from the mine to the customer purchase. This transparency will help the industry and anybody who wishes to verify, and confirm diamonds are free from conflict. (Source: forbes.com)
- With goals to boost efficiency and productivity within the insurance industry, Accenture builds blockchain solutions for its insurance clients. They translate key insurance industry processes into blockchain-ready procedures that embed trust into the system. (Source: forbes.com)
- Barclays has launched a number of blockchain initiatives involving tracking financial transactions, compliance and combating fraud. It states that “Our belief …is that blockchain is a fundamental part of the new operating system for the planet.” (Source: forbes.com)
- Maersk – The shipping and transport consortium has unveiled plans for a blockchain solution to streamline marine insurance. (Source: fortune.com)
- Dubai – Dubai has set its sights on becoming the world’s first blockchain-powered state. In 2016 representatives of 30 government departments formed a committee dedicated to investigating opportunities across health records, shipping, business registration and preventing the spread of conflict diamonds. (Source: zdnet.com)
- Kodak – Kodak recently sent its stock soaring after announcing that it is developing a blockchain system for tracking intellectual property rights and payments to photographers. (Source: kodak.com)
Challenges in Blockchain Adoption
Adopting blockchain for a supply chain application requires a lot of groundwork. IT managers and developers may be tempted to experiment with a proof of concept to gain a better understanding of the technology, but it won’t always disclose many of the underlying challenges in a real working solution.
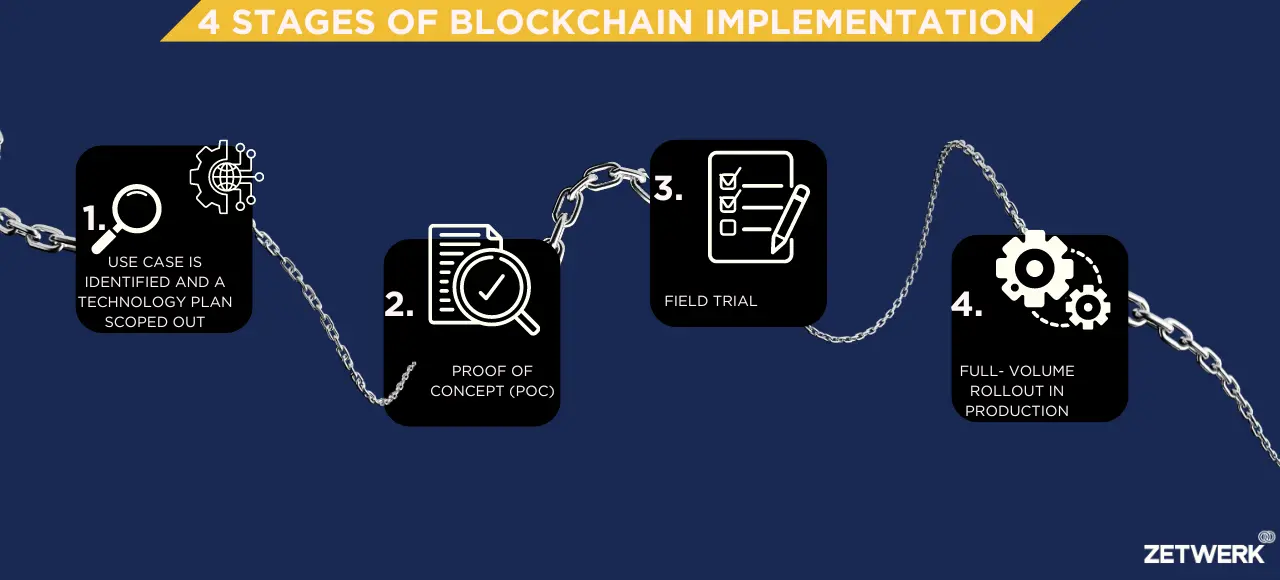
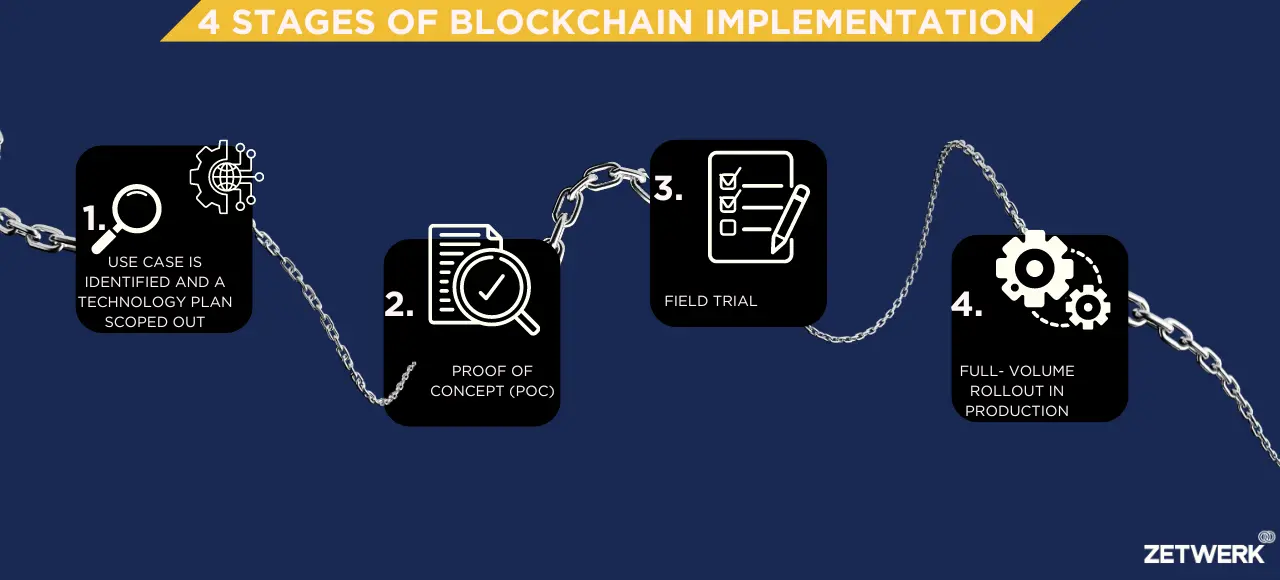
Here are some of the challenges associated with the adoption of blockchains in real-life supply chain applications:
- Higher computational overhead
Blockchain applications used in supply chains are far more efficient than currencies like Bitcoin, but they still require more computing resources — or overhead — than traditional databases. This means some of the operations of these applications, such as reading from the blockchain, may be significantly slower compared to those operations in traditional databases.
- Managing decentralization
Although blockchain technology could support decentralized applications managed by separate vendors, they most likely won’t be as easy to manage as more centralized, industry-focused exchanges.
Blockchain application exchanges may not be popular with enterprises at first, much like when music distribution services, including Apple Music, received pushback in the beginning. But, over time, enterprises may have to adapt to these new exchanges, just like the music industry did.
Control essentially plays a more prominent role in blockchain versus music because it relates to mission-critical transactions that are vital to the business.
- Data complexity
A blockchain application stores every transaction in a distributed ledger, which can add up, particularly when it is used by multiple parties. The cryptographic algorithms used to guarantee trust also add some data overhead. These factors can lead to more extensive data structures that each enterprise might have to manage. Enterprises can reduce the risk of such blockchain problems by finding an appropriate balance between data stored in a decentralized ledger and other data stored in more traditional data stores used by ERP systems.
- Buy-in with multiple parties
There are opportunities to improve process efficiency across enterprise boundaries. While blockchain can help on the technology side, putting it into practice requires a high level of technical and cultural coordination across all the concerned parties. Enterprises struggle with this today within a single organization.
- Integrating with ERP applications
Many of the security problems with cryptocurrencies aren’t found in the blockchain itself, but rather in how they interface with an existing payment infrastructure. Similar issues are likely to emerge as enterprises tie blockchain applications into existing ERP systems and supply chain applications.
- Application development complexity
Blockchain applications are written as smart contracts that could help streamline supply chain business processes that cross organizational boundaries. Many of the modelling and scripting languages available today are immature, often bug-ridden and require developers to work at a level of the stack many are no longer used to handling.
- Poor technology and use case fit
Blockchain and DLT represent a family of different approaches to creating supply chain applications with different properties around immutability, confidentiality, energy consumption and scalability. Lacking a proper understanding of how to correctly apply the technology to practical use cases will only lead to more blockchain problems.
Conclusion
There’s a lot we can do to make supply chains better, like tracking products from start to finish, delivering things faster, coordinating better, and managing money smarter. Blockchain could really help fix these problems. Now it’s up to supply chain managers to think about how blockchain could help their businesses. They need to start working with others to come up with new ways of doing things, try out different technologies, test them with small projects, and team up with other companies. It’ll take some time and money, but it should pay off in the end.
About Zetwerk
Zetwerk works with original equipment manufacturers in North America and worldwide, fulfilling their manufacturing requirements for customized components and assemblies. We act as a second brain to the OEMs. Our team of experts not just executes the customer’s manufacturing strategy, but adds tangible value at every step of the process, right from vetting designs to finding and managing the suppliers to quality control and logistics. Our customers regard us highly for our transparent and hands-on approach to manufacturing.
Zetwerk executes these projects through its network of partner suppliers spread across USA, India, China, Vietnam, and Mexico. These world-class facilities provide practically unlimited production processes, capacities, materials, part sizes, and weights as well as secondary operations, surface finishing, assembly, and related services. Importantly, we have our teams established in all these countries with an extensive presence in the US.
Zetwerk recently acquired Unimacts, a US-based manufacturing services company, providing further impetus to our commitment to serve North America as a primary market. We have more than 2,000 customers across North America, Asia-Pacific and the Middle East, and a network of more than 10,000 manufacturing partners worldwide. Founded in 2018, we are backed by some of the world’s leading venture capital firms including Sequoia, Kae Capital, Accel Partners, Lightspeed, and GreenOaks. As of 2023, Zetwerk was valued at US$ 2.8 Bn. Our manufacturing facilities employ the latest techniques and maintain all relevant certifications to ensure the highest quality control for our customers as well as compliance with all regulatory requirements, and legal practices. You can view our certifications here.
To know more about how we function, check this.
If you are looking for a global sourcing partner, look no further. Learn more about working with Zetwerk.



