Counterweights in heavy machinery are primarily employed to counterbalance the uneven weight distribution caused by the machine’s various components and attachments. These components may include the engine, hydraulic systems, operator’s cabin, and handling load. When a machine operates, its weight shifts dynamically, leading to instability, reduced lifting capacity, and an increased risk of tipping over. The critical functions of counterweights in heavy machinery include:
- Stability: Counterweights are strategically positioned to maintain the machine’s stability during operation. They counteract the dynamic forces generated as the machine moves, preventing it from tipping or toppling.
- Load Capacity: Heavy machinery often needs to lift or carry substantial loads. Counterweights enhance the machine’s lifting capacity by offsetting the weight of the load, allowing it to handle heavier objects safely.
- Balancing Components: As heavy machinery may have unevenly distributed components, such as a large engine at the front, counterweights balance the weight distribution across the machine, improving maneuverability.
- Reducing Stress: By evenly distributing the weight, counterweights reduce stress on the machine’s structural components, including the chassis and axles. This prolongs the lifespan of the machinery and reduces maintenance requirements.
Types of Counterweights
Gravity Counterweights
These are simple, traditional counterweights that use the force of gravity to balance an object. For example, a heavy weight is attached to a cord that runs over a pulley in a sash window. The weight counterbalances the window sash, making it easier to open and close.
Counterbalance Springs
These are often used in industrial machinery and equipment. Counterbalance springs exert a force opposite to the weight they balance, helping lift or lower heavy objects with less effort. They are commonly seen in garage doors, forklifts, and machinery.
Hydraulic Counterweights
Hydraulic systems can be used to create dynamic counterweights. By adjusting the hydraulic pressure, you can change the effective weight of the counterweight, making it versatile for various applications, such as in construction equipment like cranes.
Pneumatic Counterweights
Like hydraulic counterweights, pneumatic counterweights use air pressure to adjust the effective weight. These are used in various industrial applications and can be changed faster than traditional gravity counterweights.
Rotating Flywheels
Flywheels are rotating mechanical devices used as counterweights in specific applications, such as engine components. They store kinetic energy and help maintain rotational stability.
Magnetic Counterweights
Magnetic counterweights utilize magnets to create a magnetic field that opposes the gravitational force. They are sometimes used in precision equipment and scientific instruments.
Adjustable Counterweights
In some cases, counterweights need to be adjustable to accommodate changing loads. These counterweights can be modified to alter their weight as needed. They are often found in gym equipment, such as adjustable dumbbells.
Ballast Counterweights
These are commonly used in ships and aircraft to provide stability. Ballast counterweights consist of heavy materials like water or sand that can be shifted to balance the vessel or aircraft.
Electromagnetic Counterweights
These counterweights use electromagnets to adjust their weight dynamically. They are found in some high-tech applications where precise control over balance is necessary.
Liquid / Gas Counterweights
In some situations, liquid or gas-filled containers can be used as counterweights. For example, some industrial and scientific equipment use water or compressed gas tanks as counterweights.
Design Considerations For Counterweights
Weight and Mass
- Calculate the required weight of the counterweight based on the force it needs to balance or the motion it needs to control.
- Ensure that the counterweight’s mass is sufficient to counterbalance the load effectively.
Material Selection
- Choose materials with appropriate density, strength, and durability for the specific application.
- Common materials for counterweights include concrete, steel, lead, and cast iron.
Center of Gravity (CG)
- Position the counterweight’s center of gravity accurately to align with the load’s center of gravity.
- This ensures that the counterweight effectively balances the load without introducing additional forces or moments.
Mounting and Attachment
- Securely attach the counterweight to the system, considering factors such as mounting points, fasteners, and connections.
Environmental Factors
- Assess the environmental conditions in which the counterweight will operate. Consider temperature, humidity, and corrosion resistance when selecting materials and coatings.
Prototype and Testing
- Consider building and testing a prototype to validate the counterweight design before full-scale production or installation.
- Testing helps identify unforeseen issues and ensures that the counterweight performs as intended.
Load Variations
- Account for potential variations in the load being balanced or controlled and design the counterweight system to accommodate these variations.
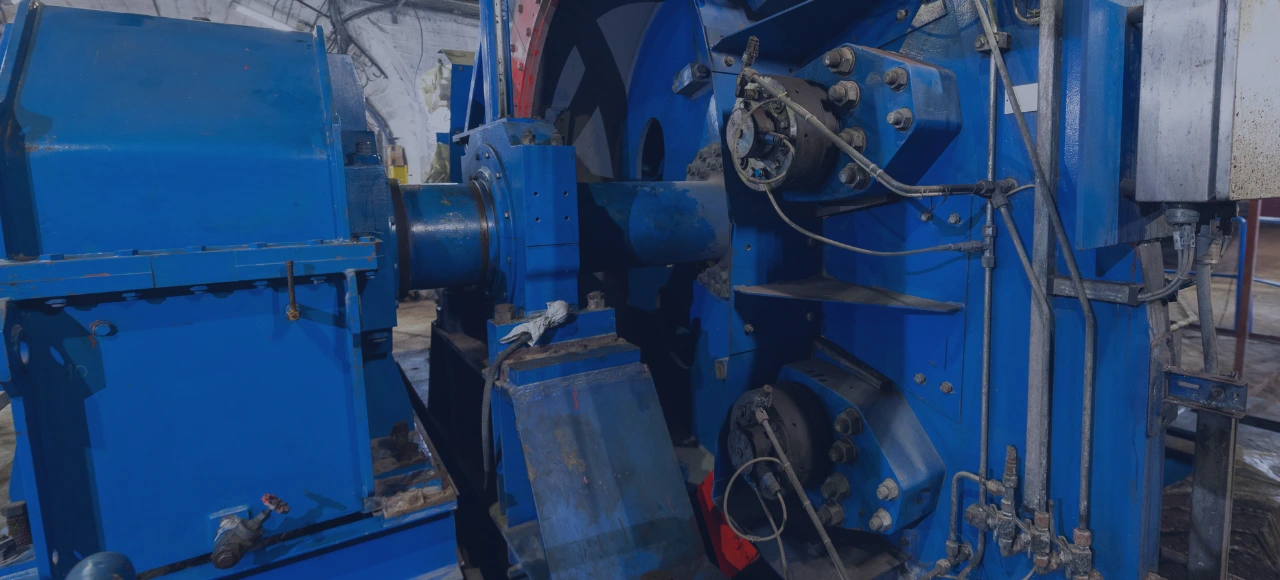
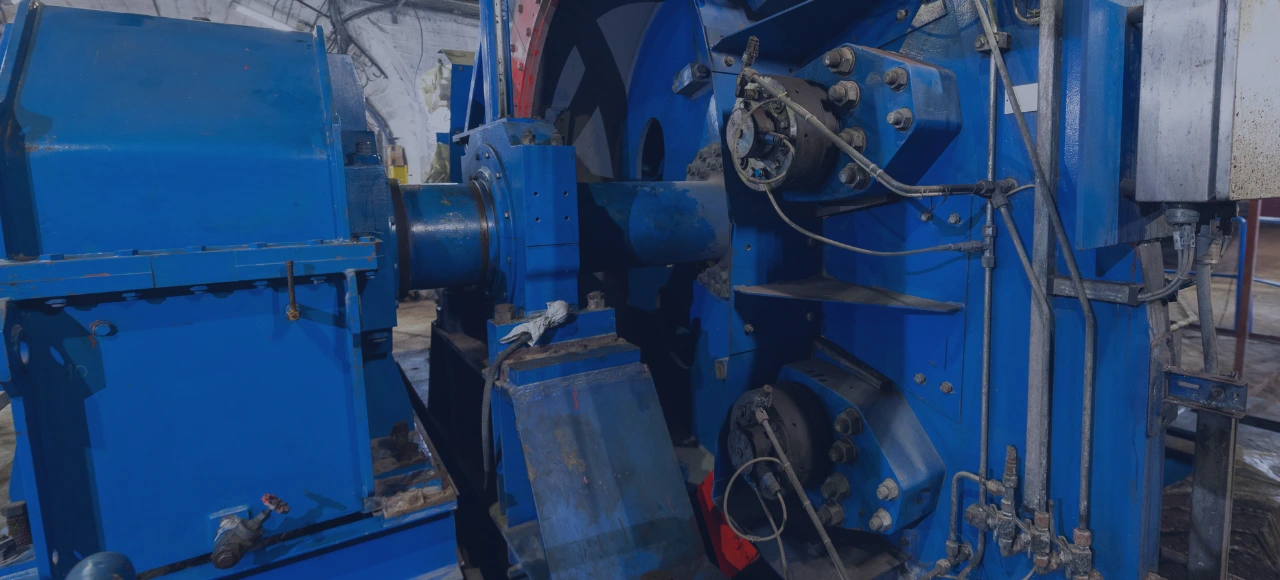
Examples Of Heavy Machinery Using Counterweights
Cranes: Cranes are among the most recognizable users of counterweights. Tower, mobile, and crawler cranes often employ massive counterweights to balance the weight of heavy loads being lifted and ensure stability while in operation.
Excavators: Excavators use counterweights to offset the weight of their excavating arms and buckets. This allows them to dig, lift, and swing their loads with precision and stability
Forklifts: Forklifts utilize counterweights to prevent tipping when carrying heavy loads. These counterweights are typically positioned at the rear of the forklift, opposing the weight of the load on its forks.
Agricultural machinery: Agricultural machinery, such as tractors and combine harvesters, often use counterweights to maintain stability when carrying heavy loads or operating on uneven terrain. These counterweights can be adjusted or added as needed.
Mining equipment: Massive earth-moving equipment like haul trucks and excavators in the mining industry rely on counterweights to handle enormous payloads and maintain stability on rough and challenging terrains.
Challenges and considerations
Space constraints: Heavy machinery often operates in tight spaces or confined environments. Designing counterweights that fit these constraints while providing the necessary balance can be challenging.
Dynamic loading: Heavy machinery is subjected to dynamic loads, such as sudden starts, stops, and changes in direction. Counterweights must be designed to handle these dynamic forces without compromising stability.
Vibration and shock absorption: Vibrations and shocks generated during machinery operation can affect the stability of the equipment. Counterweights should be designed to dampen these vibrations and absorb shocks to maintain stability and protect the machinery’s structural integrity.
Maintenance: Counterweights, like other machine components, require regular maintenance. This includes inspections for wear and tear, corrosion prevention, and occasional adjustments to maintain proper balance.
Conclusion
In short, counterweights are essential for heavy machinery, providing stability and safety. Their precision machining and quality control ensure these counterweights meet rigorous industry standards, bolstering equipment safety and operational reliability.
Zetwerk has optimized weight distribution and materials selection through advanced metallurgy and engineering, improving machinery stability and performance.
FAQs
Counterweights are typically securely attached to the machinery’s frame or structure using bolts, brackets, or other fastening methods. The attachment points are engineered to distribute the weight evenly and withstand the forces generated during operation.
The weight of a counterweight is calculated based on the machine’s design specifications, load capacity, and expected operational conditions. Engineers use mathematical calculations and simulations to determine the weight needed for stability.
Counterweights can be adjusted or reconfigured in some heavy machinery to accommodate different loads or working conditions. This adjustability can be achieved by adding or removing weight, altering the position of counterweights, or using hydraulic or pneumatic systems to change the effective weight.
Safety is paramount when dealing with heavy machinery and counterweights. Proper maintenance, inspection, and regular load testing of counterweights are essential. Operators and maintenance personnel should be trained to recognize and address any issues related to counterweights.
Balancing counterweights accurately is critical for machinery stability. Engineers use precision instruments, load cells, and computer simulations to verify that counterweights are correctly balanced during the design and manufacturing.