An automobile is a highly developed machine made up of several mechanical parts that work together to provide transportation. Every component serves a distinct purpose, whether you own a car or are considering starting a business to enter the marketplace for auto parts. Various materials are used to make auto parts. The choice of material is crucial since it affects the long-term suitability of the part for its intended use and influences the production technique. These materials are frequently utilized to create cars’ interior and external components.
Knowing the identities of the car parts would make it easier for owners to address issues caused by flaws or damages. It would help businesses focus on the best manufacturing method. The common types of automotive parts, their roles, and the production procedures are listed as follows;
Materials used in Car manufacturing
- Metals: Metals are the most frequently used materials in the production of vehicle parts. One reason is that metals have many desirable properties, including robust and stable, long-lasting and malleable, and adequate heat- and electricity-conductors. Steel, aluminum, and copper are the most frequently utilized metals in vehicle parts because of their durability and strength properties. Steel is commonly used in the production of bushings and bearings due to its low cost, wide availability, and machinability.
- Rubber: Rubber’s resistance to chemicals and abrasion makes it helpful in fabricating parts. Additionally, it can survive extremely hot and cold temperatures. Rubber is used to support the manufacturing of interior and exterior automotive parts, including ducts, bushings, and grommets.
- Plastics: Plastics are widely used materials in car production because they are lighter than metals; plastics are frequently used in the production of vehicle parts. They typically make up less than 15% of the total weight and can be used to create interior car componentry. Despite being light, plastics are strong and can be molded into intricate shapes. Polypropylene, which is used to make automobile bumpers, is an illustration of one such substance.






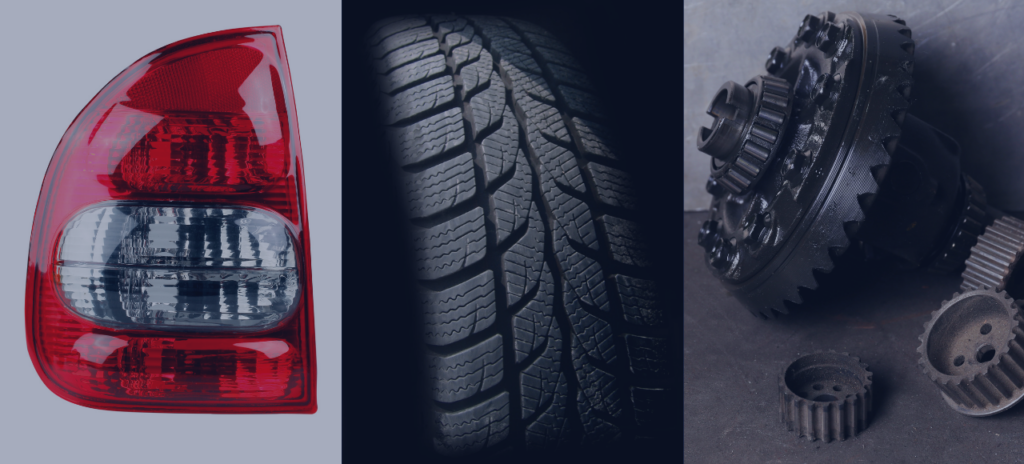
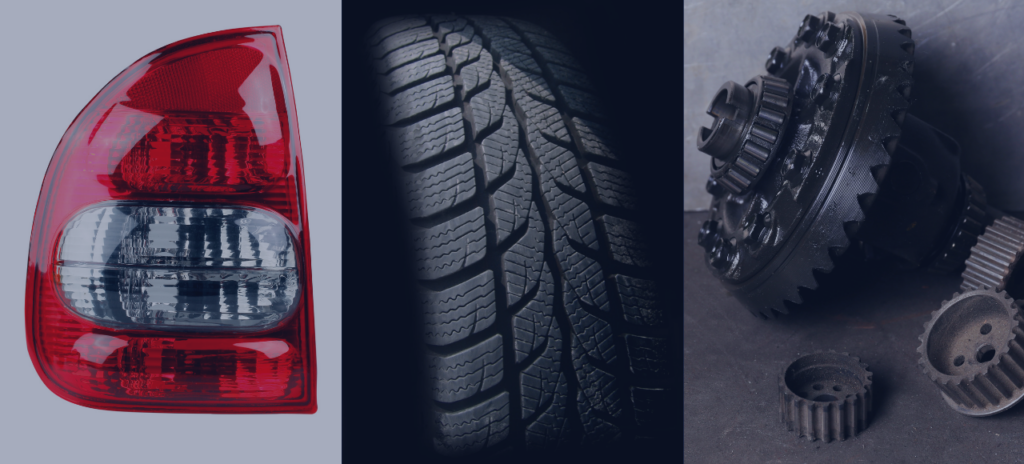
Types of Metal used in Car Manufacturing
A wide range of metals is employed in the production of automotive parts. Each metal has its own set of characteristics and benefits, making it suitable for a particular use. The most popular metals used in the production of automotive parts are examined here, along with some of their advantages and drawbacks.
Metal materials have long been employed as dependable, durable, and affordable materials for automotive components. They are particularly appealing for automotive parts mass production because metal is easier to fabricate than other materials. The types of metals used in car manufacturing are listed below.
Steel Used in Car Parts Manufacturing
Steel, one of the most widely used metals in automobile production, is used widely from the skeleton of car seats to engine blocks. It is a powerful, long-lasting metal that is simple to mold into the desired forms and sizes. There are numerous steel varieties, each with unique qualities that make them appropriate for various uses. The most popular types of steel used in autos are 10-carbon steels, which are used for a wide variety of parts and components.
Engineers choose the type of steel and its grade depending on the part’s intended application. The different types of steel are utilized to increase the performance and safety of automobiles. Body panels are made of high-strength low-alloy steels, whereas suspension parts are made of modern high-strength steels. Roll cages and other safety measures are usually made from ultrahigh-strength steel.
Iron Used in Car Parts Manufacturing
Iron can be readily melted, shaped, and forged and is more reasonably priced than many other metals. Iron is less expensive than other metals, making it a desirable alternative for auto manufacturers seeking to maintain price competitiveness while still producing high-quality goods. Iron is a material that can be used to produce a variety of automotive parts, including chassis, axles, wheels, and engine parts.
In the automotive industry, iron-based alloys are frequently used. They are produced by combining iron with other metals like copper, zinc, or nickel. As a result, the iron gains greater strength and corrosion resistance. Many auto parts, including cylinder heads, crankshafts, connecting rods, gears, and bearings, are made of iron alloys.
Titanium used in Car Parts manufacturing
Titanium is a robust and durable metal that can resist corrosion for a long time. Although it’s challenging to work with, technological advances have made it easier to process and manipulate. Parts that need to be sturdy and lightweight yet resistant to corrosion are often made from this metal.
Brake rotors and wheels are a few of the standard applications for titanium in the auto industry. Titanium components are frequently utilized instead of steel or aluminum components. This may result in lower emissions and better fuel efficiency. Racing vehicles are also built with titanium components.
Magnesium used in car parts manufacturing
Magnesium is a lightweight, corrosion-resistant metal that is difficult to shape or forge. It is frequently used in sports cars because it allows the car to be lighter while maintaining the appropriate strength and durability. The Corvette and Lamborghini employ it most often.
Despite the fact that magnesium does have some drawbacks compared to other materials (such as price and manufacturing difficulty), its overall advantages make it a desirable choice for many automotive applications. It is one of the metals used to make a car’s bonnet, doors, and chassis. Additionally, magnesium is perfect for producing customized vehicle components since it is simple to cast into intricate shapes.






Copper used in car parts manufacturing
Copper is a highly conductive metal, and its superior electrical and thermal conductivity makes it ideal for engine cooling systems and electrical components. In the automotive industry, alloys based on copper are frequently employed. They combine copper with other metals, including zinc, nickel, and silver. This gives the copper new qualities, including greater strength and resistance to corrosion.
Copper-based alloys are widely used in a range of products, including brake pads and exhaust systems. Copper-based alloys are suitable for high-heat applications due to their excellent thermal conductivity, superior strength, and durability.
Aluminum used in car parts manufacturing
The production of automobiles relies heavily on the use of aluminum. Aluminum is a light, robust, corrosion-resistant metal that is simple to deal with. The vehicle industry uses it most frequently for engine blocks, wheels, transmission housings, suspension systems, body panels, and interior trim. In headlights and taillights of automobiles, it is commonly employed as a reflector or heat shield.
Aluminum alloys are the majorly used type of aluminum used in the production of automobiles. Depending on the alloy used, aluminum can be either soft or hard. Many auto parts, such as wheels, engine blocks, gearbox housings, and engine mounts, are made of soft aluminum. Other components, including the car’s chassis, are made of more rigid aluminum alloys. Every metal has a variety of applications, and when coupled with other metals, it can produce the desired qualities.
Why is Aluminum most preferred in car manufacturing?
- Weight: Aluminum’s lesser weight than steel makes it a good option for automakers. Lighter vehicles use less energy to move around; thus, they are more efficient.
- Corrosion resistance: Aluminum’s excellent corrosion resistance is a major selling point. Rust breaks down steel’s structural integrity and shortens its useful life. In contrast, aluminum does not rust and can keep its form and color even after years of environmental exposure.
- Strength: Aluminum is stronger and more long-lasting than steel, although being considerably lighter. Its resistance to heat and stress makes it a good choice for use in the frame, body panels, and suspension of vehicles.
- Recyclability: Aluminum is one of the most easily recycled metals. It’s an eco-friendly option for automobiles because it can be recycled endlessly after melting down.
- Cost: Aluminum is more expensive than steel, but the benefits it provides more than offset the cost difference for automakers. It is a long-term investment that can save money due to its lighter weight, strength, corrosion resistance, and recyclability.
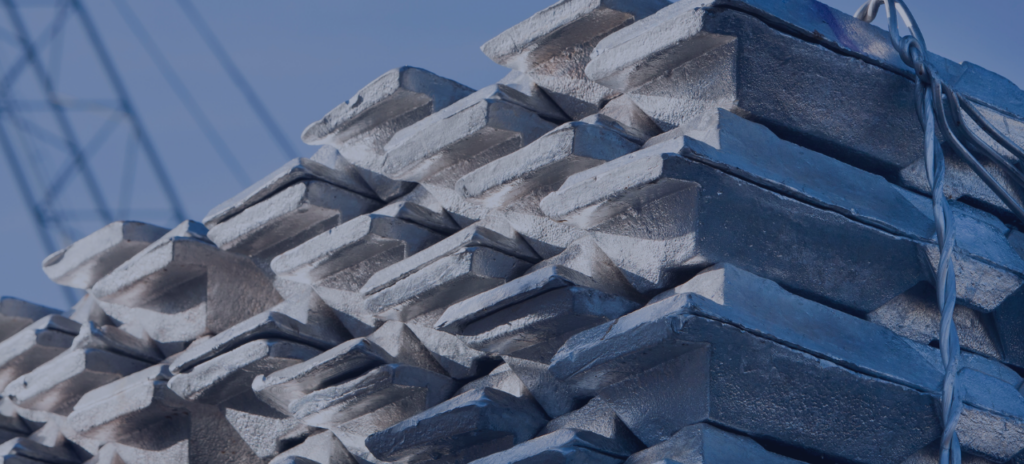
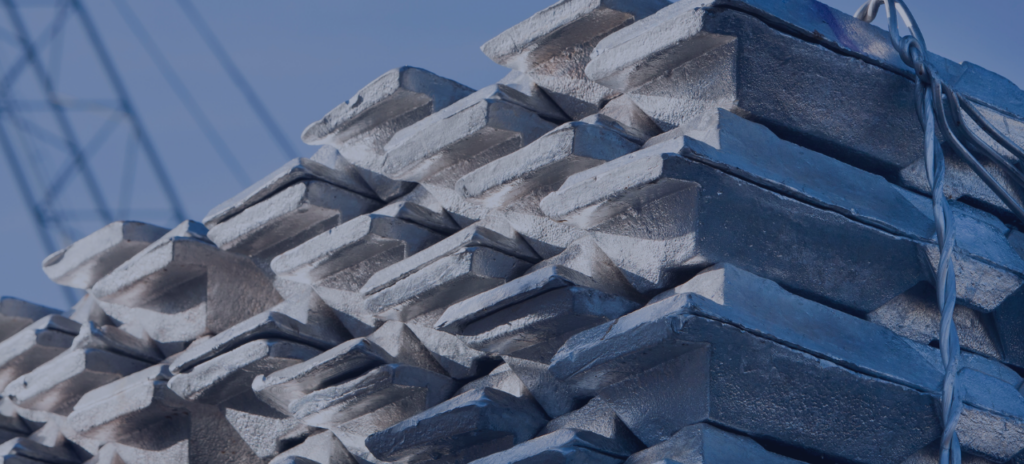