Foundries and molding methods are essential components of global production. These traditional industries are adopting technology for safety, efficiency, and production in the age of digital revolution. Automation, process control systems, integration platforms, and production scheduling tools connected with ERP systems increase the productivity of foundry operations. This article delves into the relevance of sand foundries, the power of molding sand, and the future of foundry operations.
Exploring Foundry Technologies
In the metal casting industry, foundry and molding processes play a critical role. There are numerous approaches accessible, each with its own set of benefits and drawbacks. The process used will be determined by the individual application and the required qualities of the casting.
Here are some of the main techniques used in foundry and molding:
1. Sand Foundry
Sand foundries are metal casting facilities that employ sand as the principal molding material. Sand is combined with water and other ingredients to form a mold that will be used to cast the metal.
Sand foundries are often used for casting heavy machinery like engine blocks and cylinder heads as well as tiny parts like gears and bearings.
2. Molding Sand
Molding sand is the sand that is used in the sand foundry process. It is typically made from silica sand, mixed with water and other additives to create a mold that can withstand the high temperatures of the casting process.
3. Green Sand Foundry
Green sand foundries are professional craftsmanship that uses a unique molding material known as “green sand” – a combination of silica sand, bentonite clay, and water. The goal is to keep its natural wetness and pliability. This technology is particularly effective in high-volume casting for industries such as automotive and heavy equipment. Investigate the craftsmanship of green sand foundries, which shape the machines we rely on.
4. Non-Ferrous Foundry
A non-ferrous foundry is a type of foundry that specializes in casting metals that are not iron or steel-based. Non-ferrous metals include aluminum, copper, zinc, and lead, among others. Non-ferrous foundries use various molding techniques, including green sand, resin sand, and shell molding.
Digital Transformation in Foundries
Foundries have entered a new era as a result of the digital revolution. The introduction of Industrial Internet of Things (IoT) devices and sensors has enhanced safety dramatically. Potential dangers can be identified and avoided proactively by monitoring processes in real-time and analyzing data.
Automation technology plays a crucial role in improving quality control processes in foundries. Automated systems can accurately measure and control pouring temperature, mold density, and metal composition. This ensures consistent product quality while reducing human error.
Process Control and Temperature Monitoring
Precision temperature control is crucial in achieving desired casting properties in foundry operations. Programmable Logic Controllers (PLCs) have emerged as a critical technology for streamlining process monitoring and maintenance.
Temperature regulation, cooling rates, and material flow are all automated using PLCs. PLCs maintain furnaces uniformly heated by switching the burners based on real-time temperatures, resulting in energy savings and better production efficiency.
Robotics in Foundries
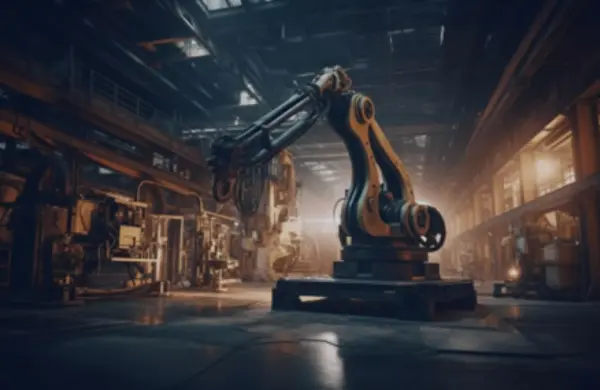
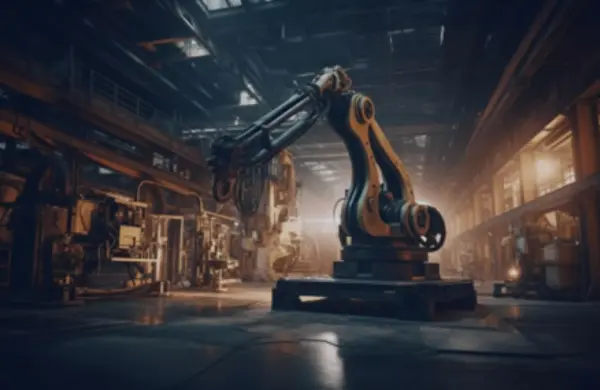
Robotics play a vital role in improving efficiency within foundry facilities. Vision systems combined with LiDAR technology enable robots to identify and locate objects accurately, ensuring precise handling and placement. Machine learning algorithms enhance their ability to adapt and learn from new scenarios.
Robots excel in palletizing, stacking, and material handling in foundries, relieving physical strain on employees and reducing the risk of injury. Their capacity to constantly perform repetitive tasks boosts productivity by increasing throughput rates.
Furthermore, robots automate material movement between workstations, removing the need for manual handling and shortening production cycles. Manufacturers benefit from faster turnaround times and higher overall output as a result of this efficiency.
Future Trends: 3D Printing Technology
3D printing technology has revolutionized various aspects of the manufacturing industry, including investment casting patterns and core equipment production in sand casting foundries.
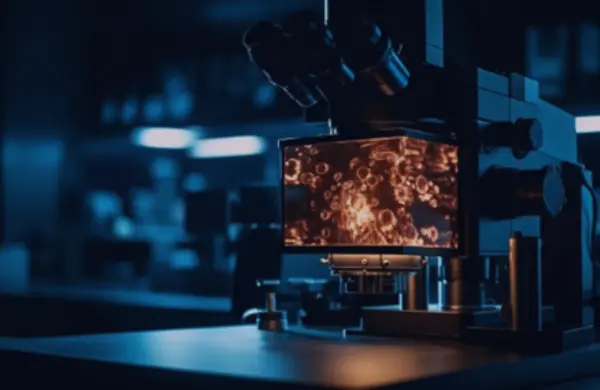
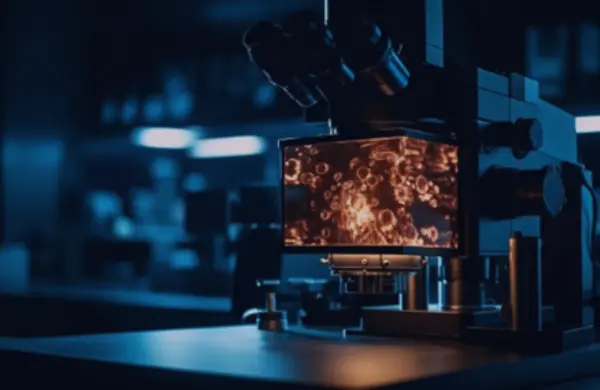
Traditional subtractive processes often require extensive machining and material wastage, whereas additive manufacturing through 3D printing allows for rapidly developing complex geometries with minimal material usage.
The benefits of 3D printing in sand casting foundries extend beyond reduced material waste. It offers shorter lead times than traditional methods, eliminating the need for tooling preparation. This leads to cost savings and improved time-to-market for manufacturers.
Key Takeaways
Foundries and molding techniques are vital components of modern manufacturing processes. As digital transformation continues to shape various industries, foundries have embraced automation, process control systems, integration platforms, and advanced technologies such as robotics and 3D printing to enhance safety measures, improve efficiency, and optimize productivity.
Using sand foundries, including green sand techniques and non-ferrous applications, allows for the production of complex shapes with cost-effective methods. By leveraging digital transformation and adopting emerging technologies, foundries can propel manufacturing to new heights while ensuring consistent quality and meeting customer demands.
At Zetwerk, we offer a wide range of comprehensive manufacturing services aligned with the latest advancements in foundry operations. Explore our website and discover more about the foundry through Zetwerk Knowledge Hub.




FAQs
Green sand foundry techniques are cost-effective compared to other casting methods as they require less equipment and energy consumption. They provide excellent dimensional accuracy with minimal shrinkage upon cooling due to their high compressive strength.
Non-ferrous foundries specialize in casting non-iron metals such as aluminum, copper alloys, zinc alloys, and brass. These find applications in automotive, aerospace, and consumer goods due to their lightweight properties, corrosion resistance, and excellent thermal conductivity.
Digital transformation enhances safety measures in foundries by integrating IoT devices and sensors for real-time monitoring and data analytics. This enables proactive identification of potential hazards and the implementation of preventive measures.
Robotics improve foundry efficiency by accurately handling heavy castings, reducing the risk of injuries associated with manual labor, performing repetitive tasks consistently, automating movement between workstations, reducing production cycle times, and increasing overall productivity.
3D printing revolutionizes sand casting processes by eliminating tooling preparation, reducing lead times, minimizing material waste, allowing for the rapid development of complex geometries, and enabling the production of intricate internal structures in complex core castings.