Non-ferrous casting processes are manufacturing techniques used to create metal parts and components from non-ferrous metals, which are metals that do not contain significant amounts of iron. Non-ferrous metals include materials like aluminum, copper, brass, bronze, and various alloys. These casting processes are essential in industries such as aerospace, automotive, electronics, and art, where the unique properties of non-ferrous metals are desired.
Few Common Non-Ferrous Casting Processes
Sand Casting
- Sand casting is one of the most versatile and widely used casting processes for both ferrous and non-ferrous metals.
- A pattern of the desired part is placed in sand to create a mold cavity, and then molten non-ferrous metal is poured into the cavity.
- Once the metal cools and solidifies, the mold is removed, and the part is cleaned and finished.
Investment Casting (Lost Wax Casting)
- Investment casting is a precision casting process used to create complex and intricate parts.
- A wax or plastic pattern is coated with a refractory material to create a mold. It is burned out or melted to leave a cavity.
- Molten non-ferrous metal is poured into the cavity, and after solidification, the mold is broken to retrieve the part.
Die Casting
- Die casting is suitable for high-volume production of intricate parts with tight tolerances.
- A metal die, or mold, is used to create the shape of the part. Molten non-ferrous metal is injected into the die under high pressure.
- The metal rapidly cools and solidifies, allowing for the quick production of parts with excellent dimensional accuracy.
Centrifugal Casting
- Centrifugal casting is used for producing cylindrical or tubular parts such as pipes, bushings, and rings.
- Molten metal is poured into a rotating mold. Centrifugal force distributes the metal evenly along the mold’s inner surface as it cools and solidifies.
Continuous Casting
- Continuous casting is used for producing long lengths of metal with a constant cross-section, such as rods, tubes, and strips.
- Molten metal is poured into a water-cooled mold, and as it solidifies, it is continuously pulled or rolled out.
Permanent Mold Casting
- In permanent mold casting, a reusable mold made of metal or refractory material is used.
- The mold is preheated, and molten non-ferrous metal is poured into it. After cooling, the mold is opened to remove the part.
Squeeze Casting
- Squeeze casting is a hybrid process that combines elements of forging and casting.
- It involves applying pressure to the molten metal as it solidifies in the mold, resulting in improved mechanical properties and reduced porosity.
Low-pressure Casting
- This casting process is similar to die casting but operates at lower pressures. It is used for producing large and complex non-ferrous parts with reduced porosity and improved mechanical properties.
Key Considerations In Non-Ferrous Casting
- Design For Manufacturability: The design of a casting greatly influences its manufacturability. Engineers must consider factors such as draft angles, fillets, and the avoidance of sharp corners to ensure a successful casting process.
- Material Selection: Choosing the right non-ferrous alloy is crucial. Factors to consider include mechanical properties, corrosion resistance, thermal conductivity, and cost.
- Mold and Pattern Making: The quality of the mold or pattern directly impacts casting quality. Molds must be made with precision, and patterns should allow for proper metal flow and cooling.
- Melting and Pouring: Maintaining precise temperatures during metal melting and pouring is essential. Alloy-specific procedures and equipment must be used to achieve the desired casting properties.
- Post-casting Processes: Finishing processes such as heat treatment, machining, and surface treatment may be necessary to meet the final product’s specifications and requirements.
- Quality Control: Rigorous quality control measures, including non-destructive testing and inspection, ensure that castings meet industry standards and specifications.
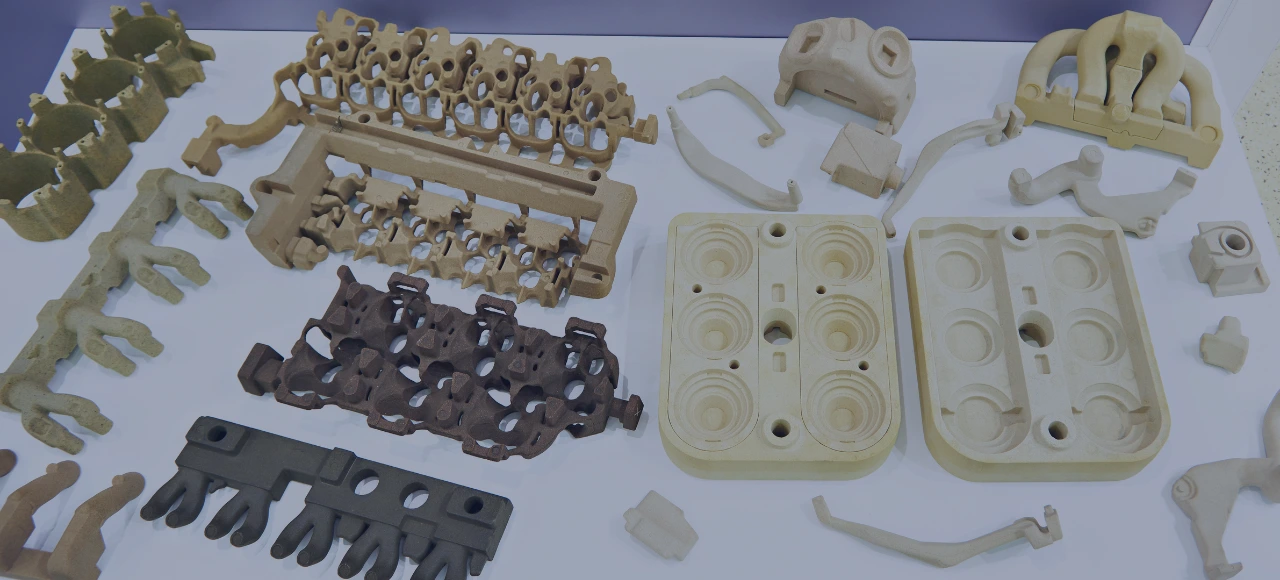
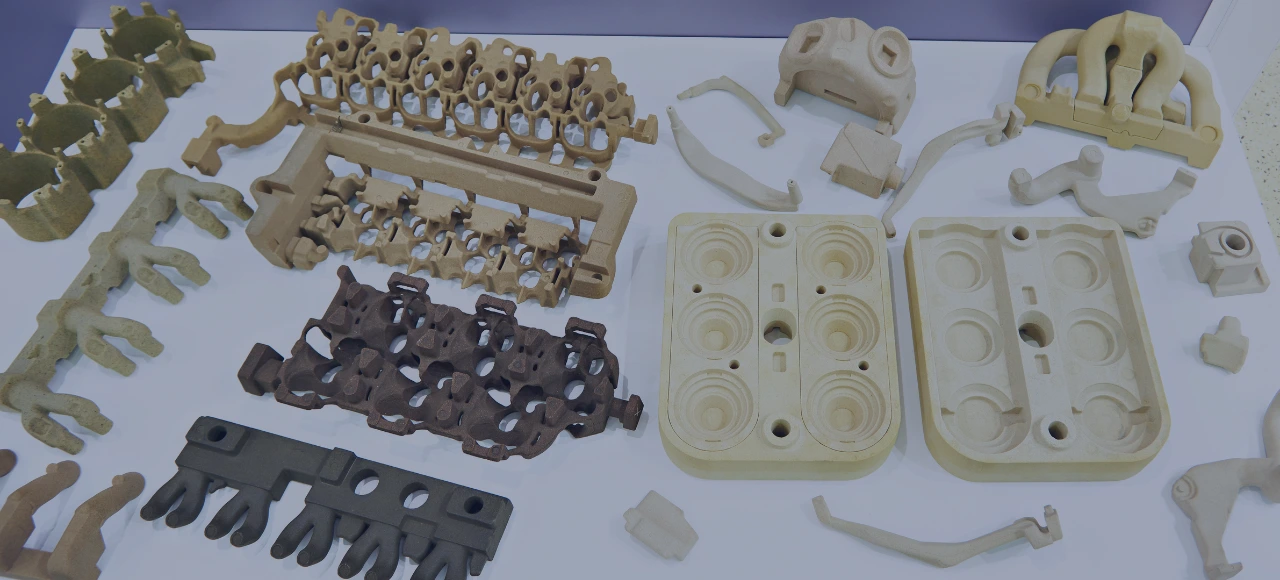
Applications Of Non-Ferrous Castings
Aerospace Industry
Non-ferrous castings are used in aircraft components such as engine parts, landing gear components, and structural elements due to their lightweight and corrosion-resistant properties.
Automotive Industry
Various non-ferrous alloys, such as aluminum, magnesium, and copper, are used for engine components, transmission parts, and lightweight structural components in modern automobiles.
Electrical and Electronics
Copper and aluminum castings are commonly used in electrical and electronic components, including wiring, connectors, heat sinks, and electrical enclosures.
Marine Industry
Non-ferrous castings are preferred in marine applications because they resist corrosion in saltwater environments. They are used for boat propellers, fittings, and ship components.
Construction
Aluminum and bronze castings are used in architectural applications, such as ornamental fixtures, decorative elements, and structural components, due to their aesthetic appeal and corrosion resistance.
Advantages Of Non-Ferrous Castings
- Corrosion Resistance: Non-ferrous metals like aluminum, copper, and bronze exhibit excellent corrosion resistance, making them suitable for outdoor and marine applications. This property helps extend the lifespan of components exposed to harsh environments.
- Lightweight: Many non-ferrous metals are significantly lighter than their ferrous counterparts, such as steel. This property is vital in industries like aerospace and automotive, where weight reduction can improve fuel efficiency and performance.
- High Electrical Conductivity: Copper has exceptional electrical conductivity. It is a preferred material for electrical wiring and components, ensuring efficient transmission of electricity with minimal loss.
- High thermal Conductivity: Non-ferrous metals like copper and aluminum also have high thermal conductivity. They are used in heat exchange applications, such as radiators and heat sinks, to efficiently dissipate heat.
- Recyclability: Non-ferrous metals are highly recyclable, which reduces the need for mining and refining of raw materials. This benefits both the environment and the economy, making them sustainable choices.
- Versatility: Non-ferrous metals can be alloyed with other elements to achieve a wide range of properties. This versatility allows manufacturers to tailor materials to meet specific performance requirements.
Challenges Of Non-Ferrous Castings
- Cost: Non-ferrous metals can be more expensive than ferrous metals, such as iron and steel. This can impact the overall cost of manufacturing processes, especially in industries with high material requirements.
- Melting Temperatures: Some non-ferrous metals have relatively high melting points compared to ferrous metals. For instance, aluminum and copper require higher energy input during melting and casting processes, which can increase operational costs.
- Casting Defects: Non-ferrous castings are susceptible to defects like shrinkage, porosity, and oxide inclusions. Proper casting techniques and quality control measures are essential to mitigate these issues and ensure the production of defect-free components.
- Alloy Complexity: While the versatility of non-ferrous alloys is an advantage, it can also be a challenge. Managing the complexity of alloy compositions, heat treatment, and casting parameters can require specialized knowledge and equipment.
- Environmental Impact: Although non-ferrous metals are recyclable, the mining and processing of some of these materials can have environmental consequences, such as habitat disruption and water pollution. Sustainable mining and recycling practices are critical to address these concerns.
- Tool Wear and Maintenance: The abrasive nature of some non-ferrous materials can lead to increased tool wear and maintenance costs during the machining and casting processes.
Conclusion
As technology continues to advance, the future of non-ferrous castings holds exciting possibilities for innovation and sustainability in manufacturing. Non-ferrous castings and nonferrous metal foundries are vital for industries due to their unique properties like corrosion resistance and lightweight.
Companies like Zetwerk, at the forefront of modern manufacturing, play a pivotal role with specialized expertise, streamlining production, and advancing the manufacturing landscape. With Zetwerk’s technology-driven platform facilitating seamless collaboration, the future of castings manufacturing is poised for innovation and efficiency, creating a brighter, more sustainable future for industries worldwide.




FAQs
Sand used in sand casting is mixed with binders and additives to improve its moldability and strength. It is then compacted around a pattern to create a mold.
Common non-ferrous alloys include aluminum-silicon alloys (e.g., A356), brass (copper-zinc), bronze (copper-tin), and various magnesium alloys.
Heat treatment is often used to improve the mechanical properties of cast non-ferrous components, such as hardness, strength, and ductility.
Porosity can be reduced by controlling the pouring temperature, using proper gating and riser design, and employing vacuum or pressure-assist techniques during casting.
Computer-aided design (CAD) and simulation tools
Cumulative manufacturing techniques, like 3D printing
Eco-friendly materials and energy-efficient processes to reduce environmental impact.