Navigating the space of metalworking, manufacturers find themselves amidst numerous methodologies, each with its signature wins and unavoidable trade-offs. In the world of part fabrication, two methods often compared are metal injection molding vs die casting. While similar in some ways, these methods differ in their working principles, costs, and the types of parts they can produce effectively. The blog comprehensively contrasts these processes, facilitating your project method selection.
What is Metal Injection Molding (MIM)?
Metal Injection Molding (MIM) constitutes a robust production methodology, ingeniously intertwining the design adaptability inherent in injection molding with the substantive advantages associated with powdered metallurgy. Complex, high-precision parts can be mass-produced via MIM. The MIM process involves four primary steps: mixing, injection molding, debinding, and sintering.
Challenges and Limitations
Though Metal Injection Molding’s perks are substantial in various applications, it is essential to acknowledge the existence of certain impediments and restrictions within its operational parameters. Assuring the integrity of the constituents demands a specialized understanding inherent to the process. Feedstock preparation, molding parameters, debinding, and sintering conditions must be carefully controlled.
Additionally, while MIM is excellent for small, complex parts, there may be better choices for larger parts or those requiring simple geometries. MIM proves cost-effective for bulk production but not for smaller runs due to steep tooling expenses. Despite hurdles, MIM’s potential in design flexibility, material efficiency, precision, and cost control can be fully harnessed with proper understanding and strategy.
What is Die Casting?
Die casting is another prolific metalworking process, especially popular in the automotive, aerospace, and consumer electronics industries. It forces molten metal under high pressure into a die or mold. The mold is created from two hardened steel dies, machined into the desired shape. Once the metal is injected into the die, it cools rapidly and solidifies, forming the part. The die gets opened, and the casting is ejected.
Die casting is preferred for manufacturing larger, less intricate parts in high volumes. It provides excellent dimensional accuracy and smooth surface finishes, often eliminating the need for secondary machining. However, die casting typically works with non-ferrous metals like aluminum, zinc, and copper alloys, limiting its material options compared to MIM.
Die Casting vs Metal Injection Molding: Key Differences
The distinctions between MIM and die casting lie in five primary areas: material options, part complexity and size, production volume, surface finish, and cost.
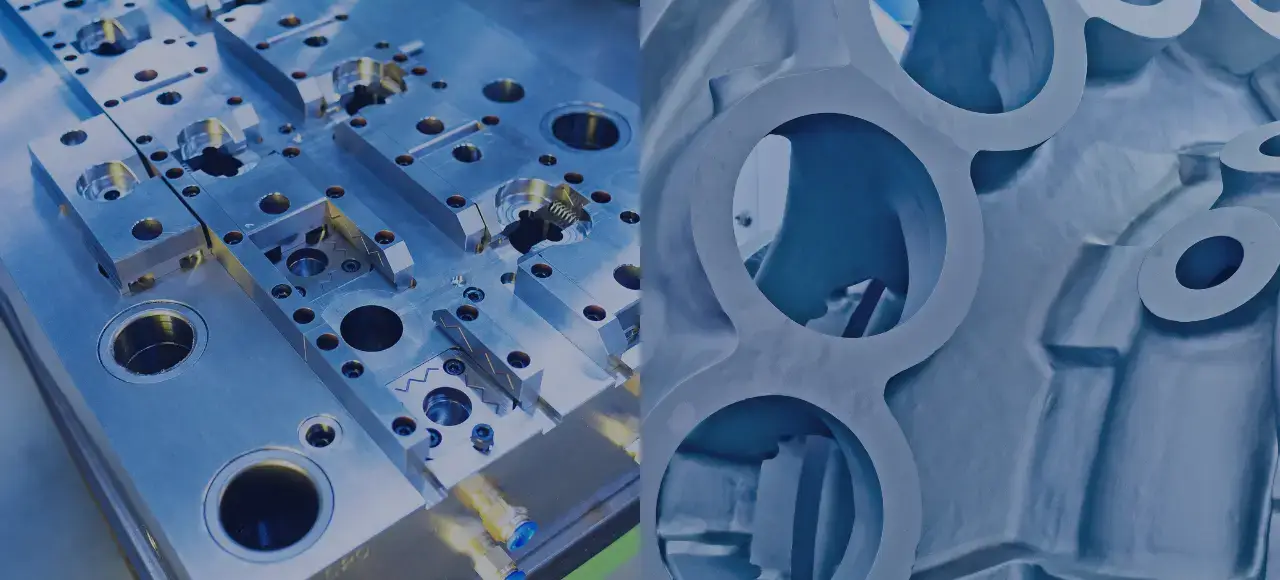
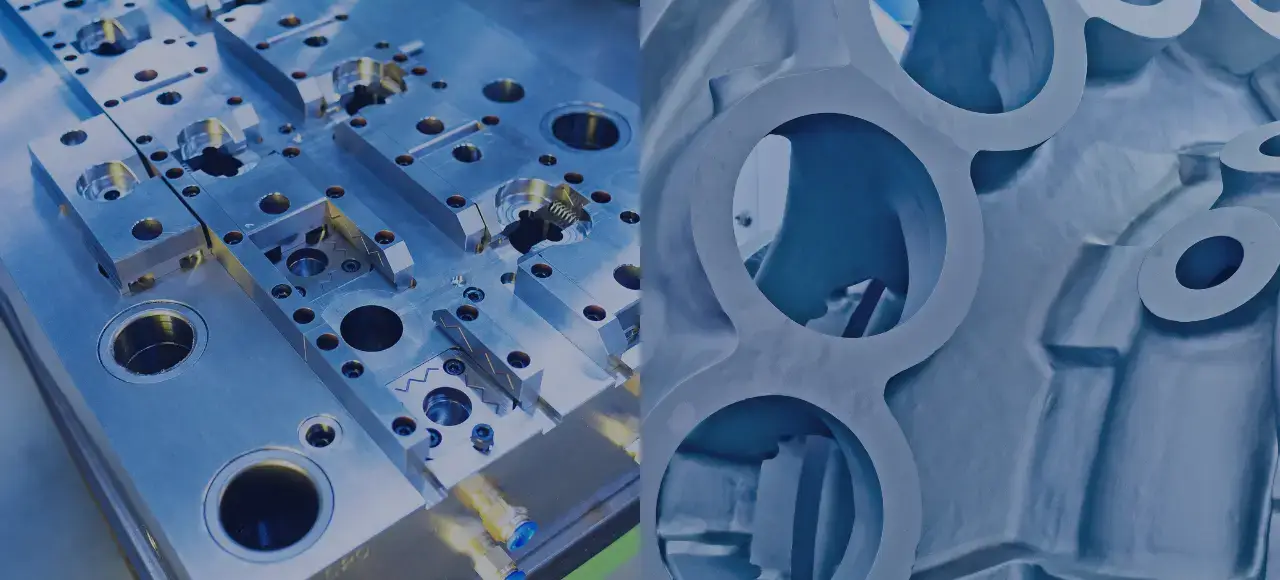
Material Options
MIM provides a broad range of material choices, capable of handling various metals and alloys, including stainless steel, titanium, and certain superalloys. In contrast, die casting is restricted to non-ferrous metals like aluminum, zinc, and copper alloys, limiting its use in applications where the strength and durability of ferrous metals are required.
Part Complexity and Size
MIM excels at producing small, complex parts with intricate details and tight tolerances. It is best suited for applications requiring high precision and complexity. On the other hand, die casting is an ideal choice for manufacturing larger, less complex parts, making it a preferred process in automotive and aerospace industries where strength, durability, and large production runs are standard requirements.
Production Volume
Die casting is faster, making it an incredible choice for high-volume production runs. The production speed means it can churn out large parts relatively quickly. While slower than die casting, MIM can still be an economical choice for medium to high-volume production, mainly when the parts are highly complex.
Surface Finish and Secondary Operations
Die-cast parts often come out of the mold with a smooth, high-quality surface finish, reducing the need for secondary operations. Conversely, MIM parts may require additional post-processing steps, such as machining or surface treatments, to achieve the desired finish or to meet specific dimensional tolerances.
Cost
The cost factor heavily depends on the project’s specifics. While MIM can be more expensive upfront due to higher material and process costs, it can provide overall cost savings for complex parts requiring extensive machining if produced using other methods. On the other hand, die casting can be more cost-effective for simpler, larger parts, particularly in high-volume production runs.
Final Thoughts
Choosing metal injection molding vs die casting hinges upon a project’s unique requirements. It is incumbent to consider an array of vital factors, including the piece’s complexity, size, material type, production quantity, and overall cost, as these elements are fundamental in reaching this essential decision.
You need to deeply understand each method’s details, which can be challenging. This is where Zetwerk, with its unwavering dedication to excellence and cutting-edge technological capabilities, rightfully commands a leadership position in the metal fabrication industry.
Zetwerk’s proficiency is not confined to Metal Injection Molding (MIM) and die casting but expands to incorporate assorted manufacturing processes tailored for specific industry demands. Irrespective of your project’s complexities or challenges, you can count on Zetwerk to guide you through the decision-making process, ensuring the chosen fabrication method aligns seamlessly with your project’s unique needs.




FAQs
No, MIM can use many metals, including stainless steel and titanium, while die casting primarily uses non-ferrous metals like aluminum, zinc, and copper alloys.
MIM is generally better for producing small, complex parts with intricate geometries and tight tolerances. Die casting is more suited to larger, less complex parts.
The cost-effectiveness depends on the specifics of the project. Die casting can be more economical for high-volume production of larger, simpler parts, while MIM can offer cost savings for complex parts that would require extensive machining otherwise.
Die-cast parts often have a good surface finish right out of the die. MIM parts may require post-process machining or surface treatment to achieve the desired finish.
Yes, Zetwerk’s team of experts can guide the best fabrication process for your needs, ensuring optimal results and a maximum return on your investment.