Metal Injection Molding (MIM) is a modern technology that is a popular choice in the manufacturing industry for good reasons! The Metal Injection Molding (MIM) industry is a groundbreaking field that merges innovation and precision manufacturing to produce intricate metal components. MIM utilizes the principles of powder metallurgy and plastic injection molding to achieve exceptional accuracy and complex geometries. Due to the ever-growing demand for efficient and cost-effective manufacturing methods, MIM has gained significant attention for its economic viability. This analysis explores the metal injection molding process, evaluating its feasibility as a commercially advantageous technique.
What is Metal Injection Molding (MIM)?
Metal injection molding, often called MIM, is a highly versatile manufacturing process that produces small, intricate, and complex metal components using a metal injection molding machine. It involves a four-step procedure: feedstock preparation, injection molding, debinding, and sintering. MIM primarily produces components from stainless steel, low-alloy steel, nickel alloys, and titanium.
The MIM Process: Step by Step
Feedstock Preparation
The MIM process begins with preparing feedstock, consisting of fine metal powders mixed with a thermoplastic binder system. The powders’ particle size and distribution play a crucial role in the success of the MIM process. The feedstock is often a mixture of metal powders, binders, and other additives, and it must possess proper flowability and rheological characteristics for successful injection molding.
Injection Molding
After the feedstock is prepared, it is loaded into an injection molding machine. The machine uses a heated barrel and a screw to melt and inject the feedstock into a precision mold cavity, creating a “green” part in the shape of the desired final component. The green part retains the thermoplastic binder, which provides cohesiveness during handling and molding.
Debinding
The green part is then subjected to a debinding process, where the thermoplastic binder is removed from the compacted metal powders. Debinding can be performed through various methods, such as solvent extraction, thermal debinding, or catalytic debinding. This step is crucial as it ensures the removal of any residual binder and prevents defects in the final part.
Sintering
After debinding, the green part is subjected to sintering, which involves heating the part in a controlled atmosphere at high temperatures (typically below the melting point of the metal). During sintering, the metal particles fuse, resulting in densification and shrinkage. The final part emerges with improved mechanical properties and near-net-shape geometry.
Materials Used in MIM
The choice of material plays a role in determining the success of a MIM project. Over the years, the range of materials compatible with MIM has expanded significantly:
- Stainless Steels: Stainless steels are among MIM’s most commonly used materials due to their corrosion resistance and mechanical properties.
- Titanium: Known for its strength-to-weight ratio, titanium is used in MIM for aerospace and medical applications.
- Specialty Alloys: These are used when specific properties, such as high-temperature resistance or magnetic permeability, are required.
Advantages of Metal Injection Molding
Complex Geometries and Design Flexibility
Unlike conventional metalworking techniques, MIM allows creating complex shapes and features, including undercuts, thin walls, and fine details, all in a single step. This level of design flexibility opens up new possibilities for product designers and helps reduce the number of components and assembly steps, ultimately leading to cost savings and enhanced functionality.
Material Variety and Customization
The metal injection molding process supports a wide range of materials, including stainless steel, low-alloy steel, titanium, tungsten alloys, cobalt-chromium, and more. Manufacturers can tailor the material properties, such as strength, hardness, and wear resistance, to suit specific application requirements. The ability to customize materials ensures that MIM parts can meet the stringent demands of different industries and deliver high-performance solutions.
Cost-Effectiveness and Reduced Waste
MIM can significantly reduce material waste compared to traditional metal manufacturing methods like machining or forging. The process is highly efficient, utilizing a fine metal powder feedstock mixture and a thermoplastic binder. The raw materials are used judiciously, minimizing material losses and contributing to cost-effectiveness. Additionally, MIM eliminates or reduces the need for extensive post-processing and machining, lowering production costs.
Consistent and Repeatable Quality
The metal injection molding employs a controlled production process, resulting in parts with consistent quality and dimensional accuracy. The automated nature of MIM ensures that each component adheres to strict tolerances, reducing the likelihood of defects or variations in the final product. This level of quality control is crucial for industries like aerospace and medicine, where precision and reliability are paramount.
Faster Time-to-Market
Traditional metal manufacturing techniques often involve multiple steps, extensive tooling, and lengthy lead times. Metal Injection Molding streamlines the production process by integrating various stages into a single operation. From design to finished part, the lead time for MIM is significantly shorter than conventional methods, allowing companies to bring their products to market faster and gain a competitive edge.
Lightweight and High Strength-to-Weight Ratio
MIM parts exhibit exceptional strength-to-weight ratios, making them ideal for applications where weight reduction is critical. This advantage is particularly significant in industries like automotive and aerospace, where lighter components lead to improved fuel efficiency and enhanced overall performance.
Excellent Surface Finish and Aesthetic Appeal
The injection molding process imparts MIM parts with a smooth and uniform surface finish. This level of surface quality eliminates the need for additional finishing processes like polishing or grinding, saving both time and resources. Moreover, MIM parts can be easily coated, plated, or painted, enhancing their aesthetic appeal and meeting the design requirements of various products.
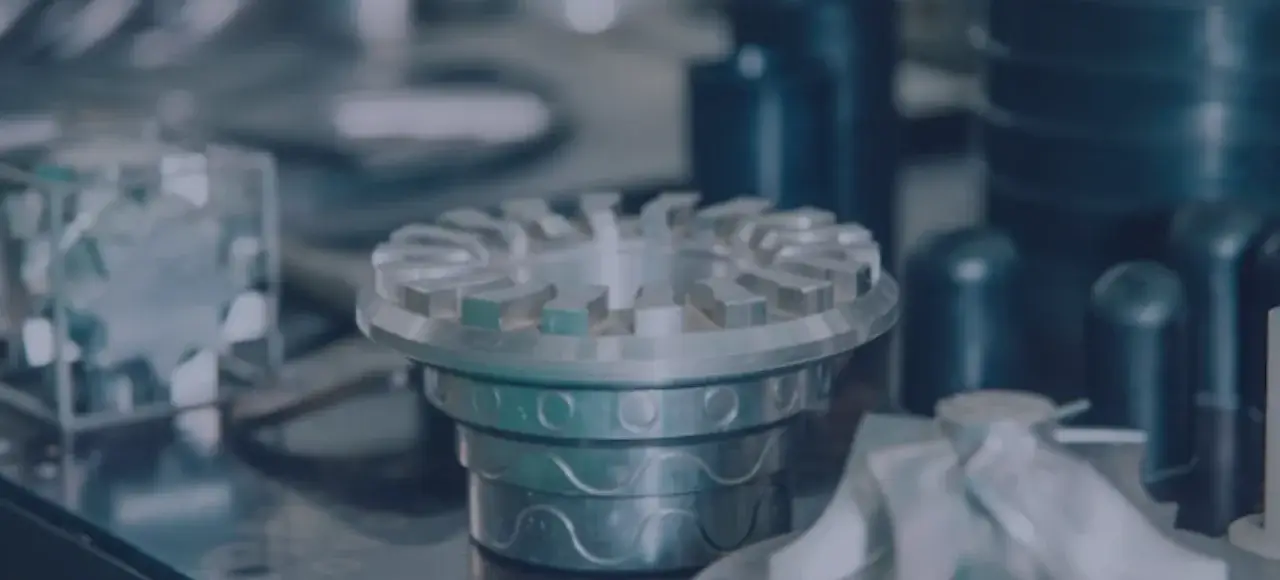
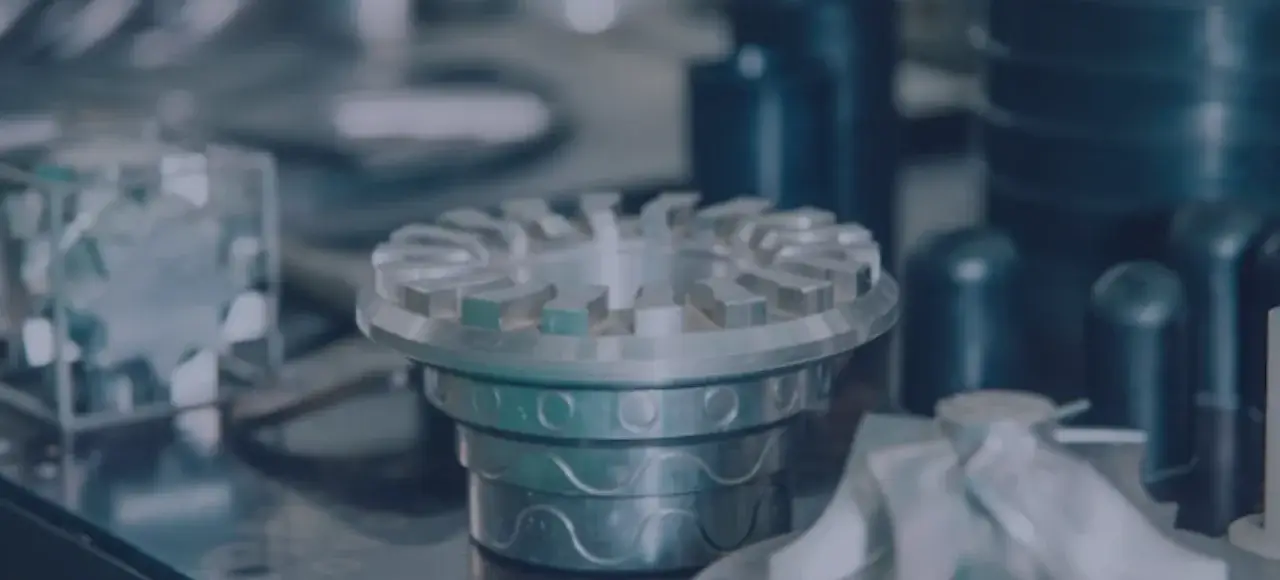
Applications of Metal Injection Molding
Automotive Industry
The automotive industry is one of the primary beneficiaries of metal injection molding due to the growing demand for lightweight and fuel-efficient vehicles. MIM is extensively used to manufacture components like transmission gears, fuel injectors, engine parts, and sensors. By using MIM, automakers can achieve complex geometries that are otherwise difficult or costly to produce using traditional methods. Additionally, MIM allows for integrating multiple features into a single part, reducing assembly time and enhancing overall performance.
Medical and Healthcare Devices
The medical and healthcare sector relies on precise and biocompatible components for various applications, from surgical instruments to dental implants. MIM excels in this field, as it can create intricate parts with high dimensional accuracy and exceptional surface finish. The ability to produce implantable devices from biocompatible materials such as titanium and stainless steel ensures that MIM improves patient outcomes and reduces recovery times.
Consumer Electronics
The consumer electronics industry demands compact, lightweight, and functional components, which can be easily achieved through MIM. Smartphones, wearables, and various electronic gadgets incorporate MIM-produced parts like connectors, hinges, and other intricate components. The combination of MIM’s mass-production capabilities and cost-effectiveness makes it a preferred choice for consumer electronics manufacturers.
For the production of intricate parts in a quick and efficient manner, the metal injection molding process is highly versatile and can be applied to a wide range of materials.
However, due to the complexity of MIM, it is crucial to have a dependable source that prioritizes quality and precision. Zetwerk is the leading expert in MIM, offering a comprehensive range of metal fabrication and part manufacturing services worldwide. Trust us to deliver the perfect components for your needs. Visit Zetwerk to get a quote for your metal injection molding project.




FAQs
Metal Injection Molding (MIM) is a net-shape process using metal powders mixed with binders, offering precision and complex shapes. Unlike traditional manufacturing methods, it minimizes waste and costly secondary machining, making it cost-effective for small to medium production runs.
MIM supports many materials, including stainless steel, low-alloy steel, nickel alloys, titanium, and copper alloys. The versatility in material selection allows engineers to choose the most suitable material for their specific application requirements, such as mechanical strength, corrosion resistance, and thermal properties.
Debinding is crucial in MIM, removing binders from the green part, leaving a porous structure. It must be controlled meticulously to ensure binder removal without defects. Proper debinding is vital for desired density and mechanical properties in the sintered part.
MIM parts match the mechanical properties of traditional methods. Sintering fuses metal particles, yielding a solid, dense structure with improved characteristics. Precise sintering control ensures desired hardness, tensile strength, and more in the final part.
MIM is eco-friendly, with efficient material use, near-net-shape components, and energy-saving sintering methods. Efforts to explore sustainable binders and recycling aim to improve their environmental impact.