Metal Injection Molding (MIM) is a highly efficient manufacturing process that offers numerous advantages over traditional metal forming techniques. With its ability to produce small, complex, and high-performance metal parts, MIM has become a cost-effective alternative for various industries. It offers design flexibility, scalability, and the ability to create unique alloys across various industries like automobile, aerospace, medical, firearm, etc. In this article, we will explore the advantages of metal injection molding and delve into its best use cases. Also, we will answer some commonly asked questions.
Metal Injection Molding: Definition and Process
MIM is an essential manufacturing process that combines the benefits of plastic injection molding with powdered metal technology. It involves mixing fine metal powders with binders to form a feedstock that can be injected into molds. The feedstock is then subjected to heat treatment processes that remove the binders and sinter the metal particles together to form solid components. The process steps involved in metal injection molding include:
- Homogenous feedstock preparation mixing fine metal powders with thermoplastic binders.
- Injection Molding with feedstock under high pressure using specialized machines.
- Debinding of the molded parts
Major Advantages of Metal Injection Molding
Metal Injection Molding offers several advantages that make it a preferred choice for manufacturing small, complex, and high-performance metal parts. Some of the key advantages are:
Cost-effective design flexibility and production scalability:
MIM allows for the production of complicated shapes that would be considered cost-prohibitive by other methods. It also enables the manufacturing of micro-sized parts in high volumes, making it an efficient option for mass production.
Ability to produce complex shapes and micro-sized parts:
MIM excels at producing components with intricate geometries, including features such as small holes, thin walls, fine surface detail, internal and external threads, and profiled holes with intricate surface textures like knurling or engravings.
Superior material properties, strength, and corrosion resistance:
The MIM process results in net shape features with an isotropic and homogeneous microstructure, leading to superior mechanical properties such as strength and corrosion resistance compared to conventional powdered metals or plastics.
Handling hard-to-process materials and creating unique alloys:
MIM can handle otherwise hard-to-process materials like Superalloys (e.g., Titanium) or create alloys that are not available in wrought or cast form. This provides designers with greater freedom to explore new material options for their applications.
Wide material variety, including ferrous and non-ferrous alloys:
MIM offers a wide range of material options, including various ferrous and non-ferrous alloys like titanium, copper, nickel, stainless steel, and more. This versatility allows manufacturers to select the most suitable material for their specific requirements.
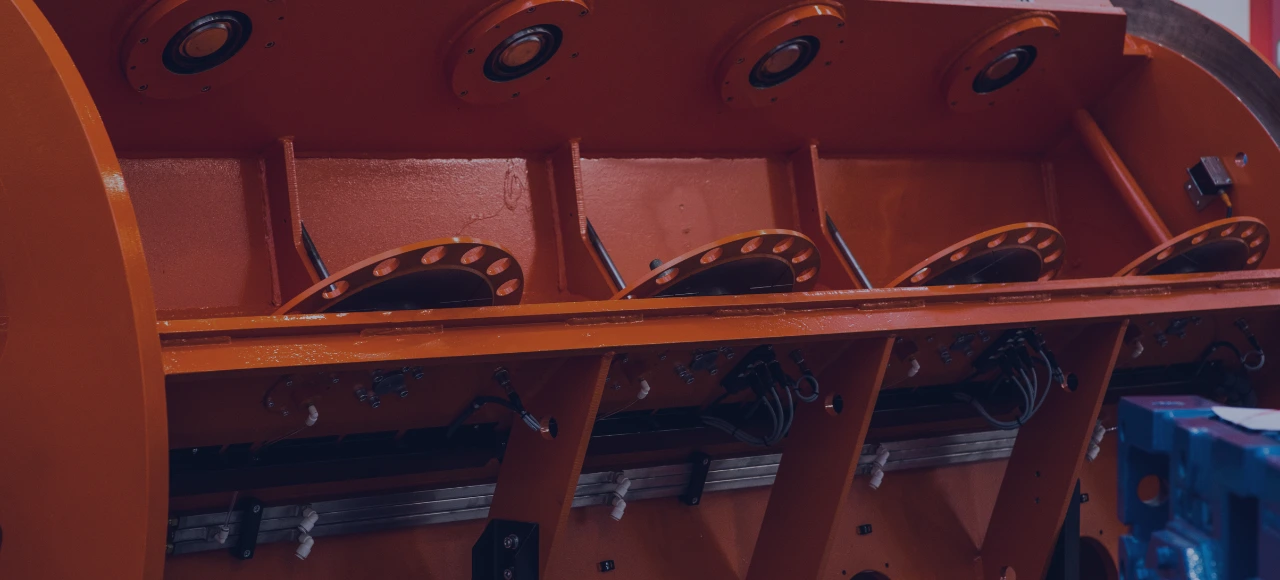
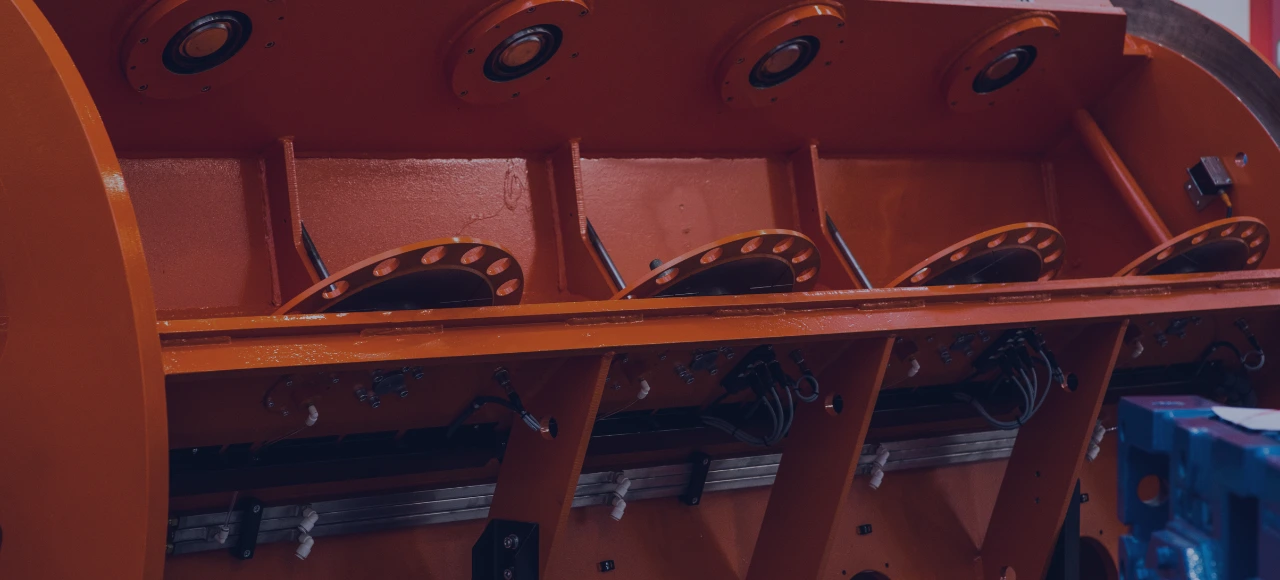
Applications of Metal Injection Molding in Various Industries
Metal Injection Molding finds applications in various industries due to its ability to produce small, complex parts with excellent mechanical properties. Some notable industries utilizing MIM include:
- Automotive components, aerospace, and electronics industry: Metal Injection Molded parts are used in automotive components like engine components, fuel injection systems, and transmission parts. The aerospace and electronics industries also benefit from MIM’s ability to produce intricate parts with tight tolerances.
- Medical equipment: MIM is widely used in the medical field for producing surgical instruments, orthopedic implants, dental brackets, and other medical devices with complex geometries and high precision.
- Firearms manufacturing: Metal Injection Molding is utilized in the firearms industry for producing lock components, triggers, firing pins, and other small firearm parts.
- Computer/electrical applications and soft magnetic components: MIM is suitable for manufacturing computer and electrical components such as connectors, terminals, and soft magnetic components like magnetic cores used in transformers or electric motors.
Explore Zetwerk’s Range of Manufacturing Services
Zetwerk offers a comprehensive range of manufacturing services to suit various industry needs. Whether you require precision machining or casting services to complement the metal injection molding process or have other manufacturing requirements, Zetwerk can provide customized solutions. Check out the Zetwerk Knowledge Hub for more articles on related topics like metal forging, die casting, and so on.




FAQs
A metal injection molding machine works by mixing fine metal powders with binders to create a feedstock that can be injected into molds under high pressure. The molded parts are then debonded and sintered to achieve their final shape and properties.
The key steps in the metal injection molding process include feedstock preparation, injection molding of the feedstock into molds, debinding of green parts to remove binders, and sintering at high temperatures to fuse the metal particles.
Metal Injection Molding can utilize a wide range of materials, including various ferrous and non-ferrous alloys such as titanium, copper, nickel, stainless steel, and more.
Metal Injection Molding offers advantages over traditional metal forming techniques like machining and investment casting. It provides cost-effective design flexibility. Also, it can produce complex shapes and micro-sized parts with superior material properties. Moreover, it can handle hard-to-process materials while creating unique alloys.