The injection molding industry is enjoying a boom with new developments and emerging trends revolutionizing the manufacturing landscape. The introduction of metal injection molding has assisted in mass production, allowing manufacturers to create large volumes of parts with consistent quality. Moreover, these new advancements in injection molding continue to push the industry forward. In this blog, we’ll discuss the top advancements in metal injection molding and how manufacturers can benefit from them.
Evolution of Metal Injection Molding (MIM)
Metal injection molding (MIM) has evolved from its inception in the 1970s to a sophisticated manufacturing process today:
- The 1970s-1980s: A concept emerged combining injection molding and powdered metallurgy.
- 1990s-2000s: Improved feedstock, binder formulations, and sintering techniques for better part properties.
- 2000s-2010s: Expanded material range (ferrous, non-ferrous, ceramics), diversifying applications.
- 2010s: Enhanced tooling, simulation for optimized designs; emphasis on quality control and certification.
- 2020s: Focus on sustainability, greener practices, and integration with Industry 4.0 for increased efficiency.
Advantages of Metal Injection Molding
- Complex Geometry: Metal injection molding (MIM) opens the door to crafting intricate and tough components that would be difficult or unfeasible to produce using conventional manufacturing methods. This capability is significant in the aerospace, medical devices, and electronics industries.
- Material Versatility: MIM supports many materials, including stainless steel, titanium, cobalt-chromium alloys, and more. This versatility allows manufacturers to select materials that suit the intended application’s requirements.
- Cost Efficiency: With modern technology comes cost-efficient production. Using MIM, manufacturing units can significantly reduce manufacturing costs, especially for parts that would require extensive machining or assembly. The ability to produce near-net-shape components minimizes material wastage and reduces the need for post-processing.
- Tight Tolerances: By employing metal injection molding, it becomes possible to manufacture parts with meticulous dimensions and stringent tolerances, thereby ensuring steadfast consistency and pinpoint accuracy in the eventual product.
- Reduced Lead Times: Thanks to its swift production cycle and the capability to generate multiple components in a single operation, MIM leads to reduced lead times compared to conventional manufacturing techniques.
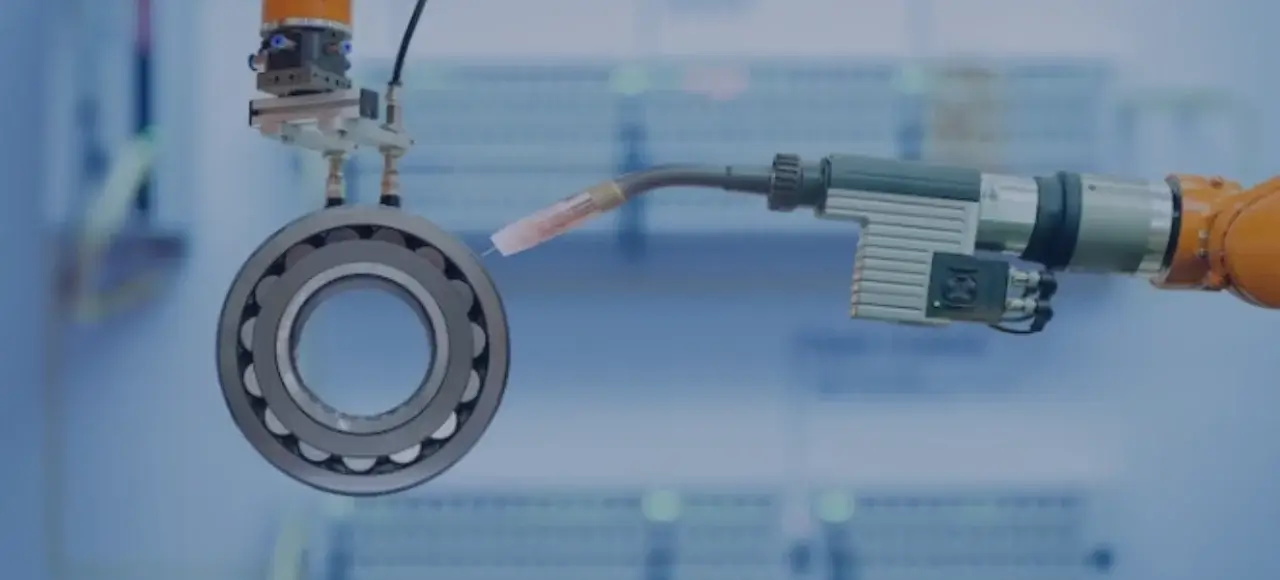
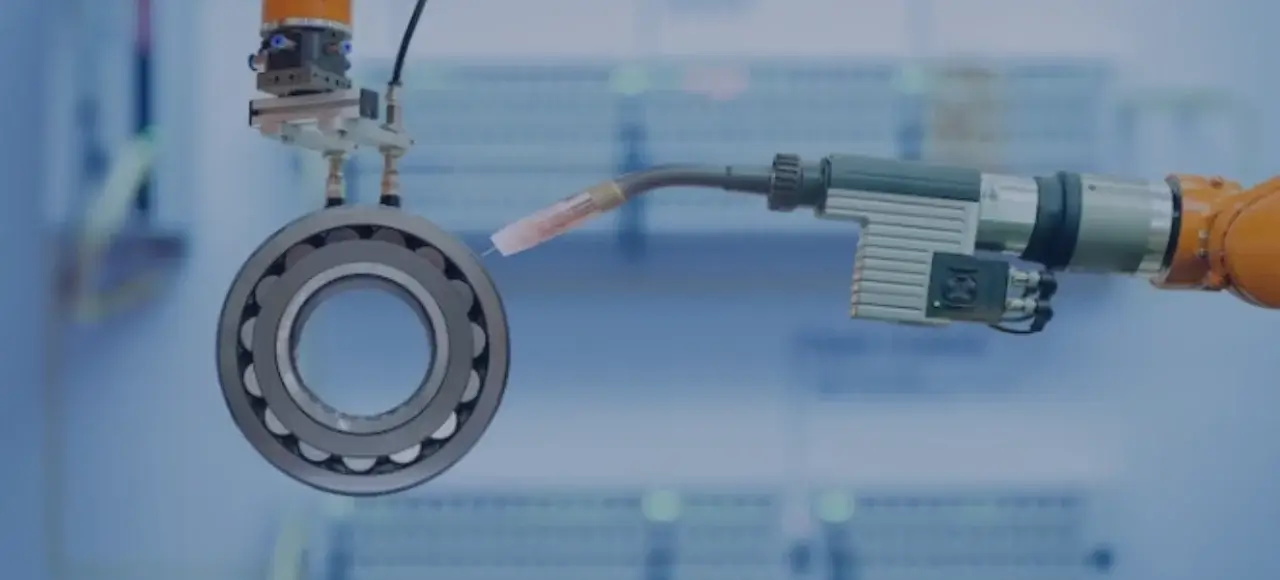
10 Innovations Driving MIM Forward
Advanced Materials
One of the driving forces behind MIM’s evolution is the expansion of available materials. Initially limited to stainless steels, MIM now encompasses many materials, including titanium, cobalt-chrome, and even ceramics. These materials offer improved mechanical properties, corrosion resistance, and heat tolerance, enabling manufacturers to produce previously unattainable components through conventional methods.
Nano-MIM
Nano-MIM, a groundbreaking innovation, involves producing nano-sized metal components using MIM metal injection molding technology. This allows for creating miniature parts with unparalleled precision and surface finish. Applications include medical devices, electronics, and optics, where size and precision are paramount.
Additive Manufacturing Integration
The fusion of metal injection molding with additive manufacturing techniques has resulted in hybrid processes that harness the strengths of both methods. Additive manufacturing can create intricate molds for MIM, reducing lead times and enhancing design flexibility. This integration also enables the production of complex geometries that were previously challenging to achieve.
Digital Twin Simulations
Digital twin simulations have revolutionized the design and optimization of MIM components. These simulations use computer modeling to predict a part’s performance under different conditions, allowing engineers to refine designs and identify potential issues before manufacturing begins. This not only reduces costs but also accelerates the development cycle.
Binder System Innovations
The binder system is a crucial component of MIM metal injection molding technology, as it determines the flow characteristics of the feedstock. Innovations in binder systems have improved debinding and sintering processes, resulting in higher-density components with enhanced mechanical properties. Reduced defects and better dimensional accuracy are among the benefits derived from these advancements.
Green MIM
Environmental considerations are increasingly shaping manufacturing processes. Green MIM focuses on sustainability by developing biodegradable binders, reducing waste, and employing energy-efficient production methods. This innovation aligns MIM with modern ecological values while maintaining its high-quality output.
Micro-MIM
While MOM has traditionally been associated with larger components, micro-MIM has opened doors to manufacturing tiny metal parts with intricate features. This innovation is transforming industries such as medical devices, telecommunications, and microelectronics, where miniature components are in demand.
Automation and Robotics
Automation has streamlined MIM production lines, increasing efficiency and reducing labor costs. Robotic systems are now used for parts handling, quality control, and even complex assembly processes. This innovation enhances productivity and ensures consistent quality across production runs.
Post-Processing Advancements
Post-processing plays a vital role in refining MIM components. Innovations in this area include advanced polishing techniques, surface coatings, and heat treatments that improve MIM parts’ aesthetics, durability, and performance. These advancements contribute to expanding the range of industries that can benefit from MIM.
Industry Collaboration and Standardization
The MIM industry has witnessed increased collaboration between manufacturers, researchers, and industry associations. This collaboration has established best practices, material standards, and design guidelines for MIM components. Standardization enhances the reliability and predictability of MIM processes, making it easier for industries to adopt this technology.
Closing lines: Challenges and Prospects
While metal injection molding offers numerous advantages, it also faces challenges like ensuring consistent powder feedstock quality, managing shrinkage during debinding and sintering, and maintaining tight tolerances for large-scale production. However, ongoing research and technological advancements continue to address these issues.
MIM is poised to expand its applications into renewable energy, consumer electronics, and 3D-printed metal components in the coming years. As additive manufacturing and materials science continues to evolve, the synergy between these fields and MIM could unlock new frontiers in component design and manufacturing.
Throughout its evolution and advancements, Zetwerk has been dedicated to providing customers with advanced solutions to cater to their every need, whether metal injection molding or machined parts. Zetwerk has established itself as a leading provider of cutting-edge solutions in the industry with an unwavering dedication to excellence and customer satisfaction.



FAQs
Metal injection molding (MIM) is a manufacturing process that combines the principles of plastic injection molding with powdered metal feedstock to create intricate and complex metal components. Unlike traditional methods like machining and casting, MIM enables the production of parts with complex geometries and tight tolerances, reducing material wastage and post-processing requirements.
MIM offers several advantages, including manufacturing components with complex geometries, a wide range of materials, cost efficiency due to near-net-shape production, tight tolerances, and reduced lead times. These benefits make MIM suitable for medical devices, automotive, aerospace, and electronics industries.
Metal injection molding is advancing towards more sustainable practices, often called “Green MIM.” This involves using sustainable materials, optimizing energy consumption during processing, and implementing recycling methods for metal powders and binders. As a result, MIM is becoming a more environmentally friendly manufacturing option.
Recent innovations in MIM include advancements in material development, integration with additive manufacturing techniques, improved simulation and modeling tools for process optimization, and the exploration of new applications in industries like renewable energy and consumer electronics.
Some challenges in metal injection molding include maintaining consistent powder feedstock quality, managing shrinkage during debinding and sintering, and ensuring tight tolerances for large-scale production. Ongoing research and technological advancements address these issues through improved process controls, material innovations, and enhanced simulation tools to predict and mitigate potential challenges.