As businesses strive to outperform competitors amidst the swiftly evolving global marketplace, the metal injection molding market emerges as a revolutionary manufacturing technology helping them outshine by producing premium quality components for their customers. The growing use of MIM is bridging the gap between traditional powder metallurgy and plastic-injection molding processes. Moreover, the scenario also doesn’t seem to show any changes soon.
According to the reports, in 2022, the worldwide market size for metal injection molding (MIM) was approximately USD 4.12 billion. Forecasts indicate that this market is poised to expand, reaching a value of about USD 8.02 billion by 2030. The injection molding market size growth trajectory is expected to follow a compound annual growth rate (CAGR) of approximately 8.68% from 2023 through 2030.
Metal Injection Molding
Metal injection molding is an advanced manufacturing process that combines plastic injection molding principles with metals’ material properties to produce highly complex, small to medium-sized metal components. It offers a cost-effective and efficient way to create intricate parts with precise geometries, tight tolerances, and excellent surface finishes, making it suitable for various industries and applications.
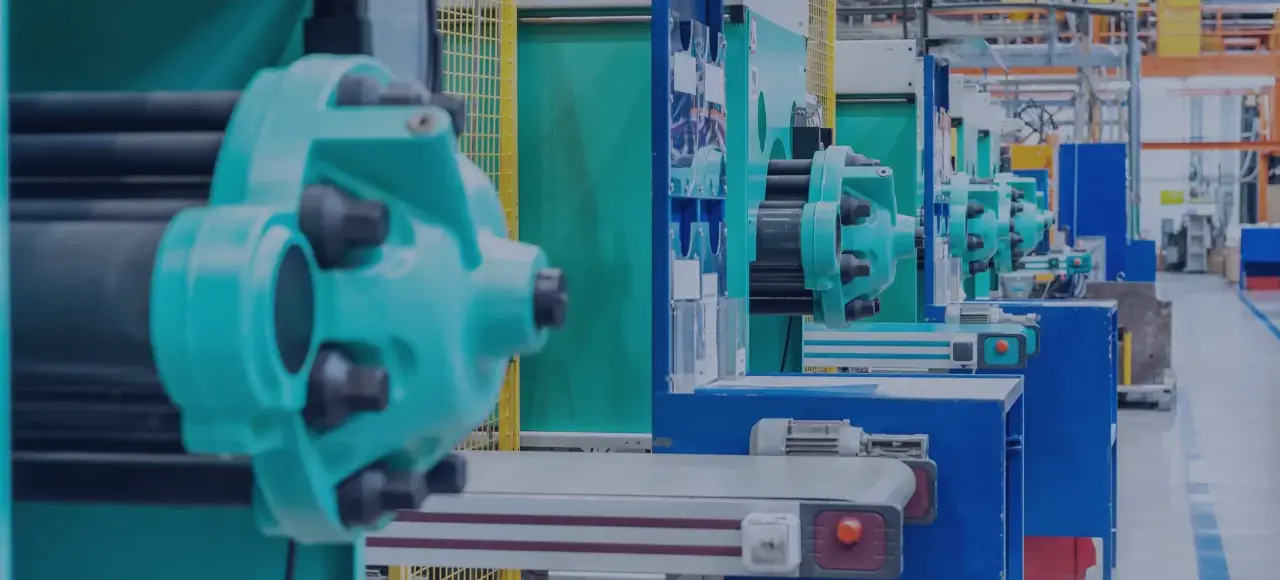
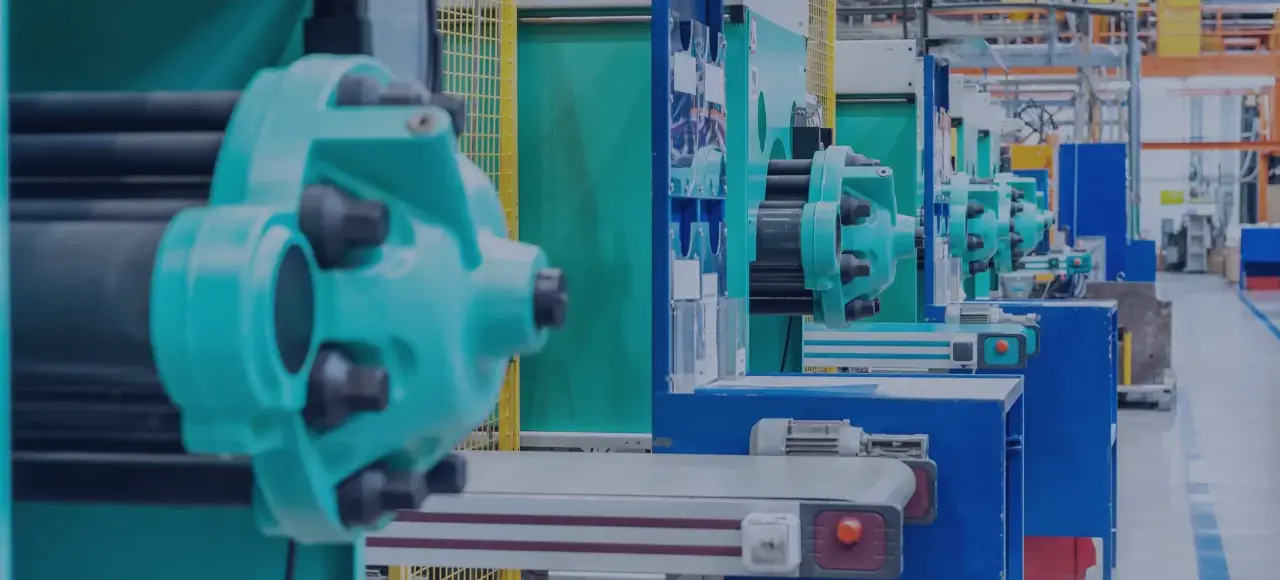
Emerging Trends in Metal Injection Molding
Material Advancements
One of the most significant trends in metal injection molding is the continuous exploration and development of new materials. As researchers and engineers delve deeper into the chemistry and metallurgy of alloys, we can expect to see MIM components with enhanced mechanical properties, corrosion resistance, and high-temperature capabilities. This evolution broadens the scope of applications and ensures that MIM compares favorably with traditional manufacturing methods.
Miniaturization and Complex Geometries
The ability of MIM to produce intricate and miniature components with high precision has caught the attention of industries demanding smaller and more complex parts. As electronic devices, medical implants, and micro-mechanical systems become increasingly prevalent, metal injection molding is poised to play a pivotal role in meeting these demands. The trend toward miniaturization also aligns with the growing demand for lightweight materials and space-efficient designs, further propelling the adoption of MIM.
Sustainability and Circular Economy
In an era of environmental consciousness, Metal Injection Molding stands out as a sustainable alternative to traditional manufacturing techniques. Reducing material waste, energy consumption, and the overall carbon footprint positions MIM as a contributor to the circular economy. The future of MIM will likely witness a heightened focus on optimizing processes to minimize waste and exploring eco-friendly materials, attracting environmentally-conscious industries and consumers.
Automation and Industry 4.0 Integration: Smart Manufacturing
The integration of the metal injection molding market into the realm of Industry 4.0 and intelligent manufacturing is a trend that holds immense potential. Automated systems, real-time monitoring, and data-driven decision-making can enhance the efficiency and quality of the MIM process. Predictive maintenance, quality control through AI-driven inspection, and adaptive manufacturing based on real-time feedback are likely to become standard practices. This integration streamlines production and ensures consistent output, reducing defects and rework.
Collaborative Research and Customization
The collaborative nature of the manufacturing industry is expected to extend into the MIM domain. Researchers, material scientists, and manufacturers are likely to join forces to develop tailored solutions for specific industries. Customized alloys, specialized coatings, and application-specific designs will drive injection molding market size penetration into new sectors. This trend fosters innovation and cross-industry synergies, enabling MIM to address broader challenges.
Cost-Effectiveness and Scalability
As the Metal injection molding market grows, advancements in tooling, process optimization, and economies of scale are expected to drive down costs. This cost-effectiveness and the ability to scale up production will attract more businesses to adopt MIM for their components. From startups to large corporations, MIM’s potential to provide high-quality, complex metal parts at a competitive cost will open doors to diverse industries and applications.
Regulatory Compliance and Quality Assurance
Industries such as aerospace, automotive, and medical devices demand rigorous adherence to quality and regulatory standards. MIM’s ability to consistently produce components with tight tolerances and exceptional surface finish positions it as a viable solution for these sectors. The future of MIM will likely involve further advancements in quality control measures, certifications, and traceability to ensure compliance with industry-specific regulations.
Metal injection molding is a promising solution for producing high-quality complex metal parts. With the ongoing advancements and technology growth, the metal injection molding market size is expected to find applications in different industries and will likely witness continued expansion and popularity. As a consumer-centric manufacturing unit, Zetwerk aims to meet the evolving market expectations and apply modern methods to produce supreme quality metal parts for customers.




FAQs
MIM offers several advantages, including the ability to produce complex shapes, a wide range of material options, cost-effectiveness for small to medium volumes, high precision, and versatility across various industries. Its unique properties make it a popular choice for aerospace, automotive, medical devices, electronics, and more applications.
The MIM process includes stages: feedstock prep, injection molding, debinding, sintering, and finishing. Mix metal powders with a binder, inject into mold, heat, and shape. Debind to remove the binder and sinter at high temp to fuse particles. Finish with machining and coating for desired properties.
The MIM process includes stages: feedstock prep, injection molding, debinding, sintering, and finishing. Mix metal powders with a binder, inject into mold, heat, and shape. Debind to remove the binder and sinter at high temp to fuse particles. Finish with machining and coating for desired properties.
MIM spans the aerospace, automotive, medical, electronics, defense, and consumer goods industries. It crafts precise parts like surgical tools, firearm components, electronics, gears, and intricate auto parts, ideal for high-performance applications.
Metal Injection Molding’s future is promising with advanced materials, miniaturization, complex shapes, sustainability, Industry 4.0 integration, customization, and quality compliance. It’s reshaping industries and fostering innovation across sectors.