One of the best parts about working for a precision casting parts supplier is that you work with an incredibly diverse range of businesses. From mining companies to automotive parts manufacturers, precision casting parts are in demand by a host of industries. By working here, you’ll be exposed to many different types of people and have the opportunity to build relationships with many customers.
Precision Casting: Overview
Investment casting is a process in which a wax model of an object is molded into a ceramic mold. Wax is used because it is easy to work with and can be melted down and recycled. A wax pattern is coated with ceramic powder and heated until the wax melts, forming a hard shell. The solid ceramic coating is turned upside down and heated again to melt the wax out, leaving a layer of ceramic powder which becomes a replaceable shielding material. Molten metal is poured into a mold and cooled. The cast metal is then knocked out of the finished mold.
Investment casting, also called the lost-wax casting process, is where a pattern is surrounded by refractory materials and then melted out, leaving a cavity for molten metal. This process results in very fine details and an excellent surface finish. Investment castings can be molded with thin walls and intricate internal transitions that cannot be made using other casting processes, such as sand casting. Net or near-net castings made from metal can reduce material, labor, and machining costs. These castings can be produced from various metals, including bronze, magnesium, aluminum, and stainless steel.
Precision castings are used to make a variety of products, including turbine blades for aircraft and power plants, medical devices such as knee replacements, firearm components like trigger mechanisms and bolts, tools used in manufacturing and construction, jewelry made from precious metals, and many other machine components with complex geometries.





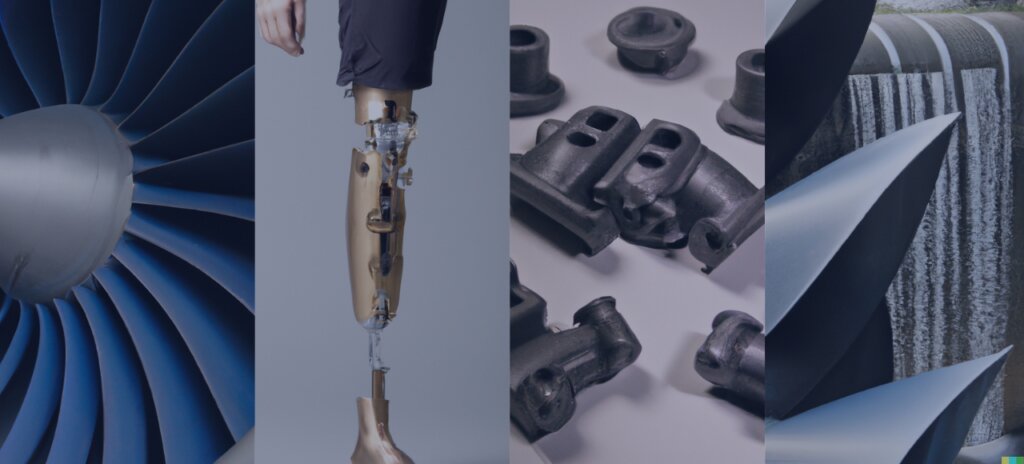
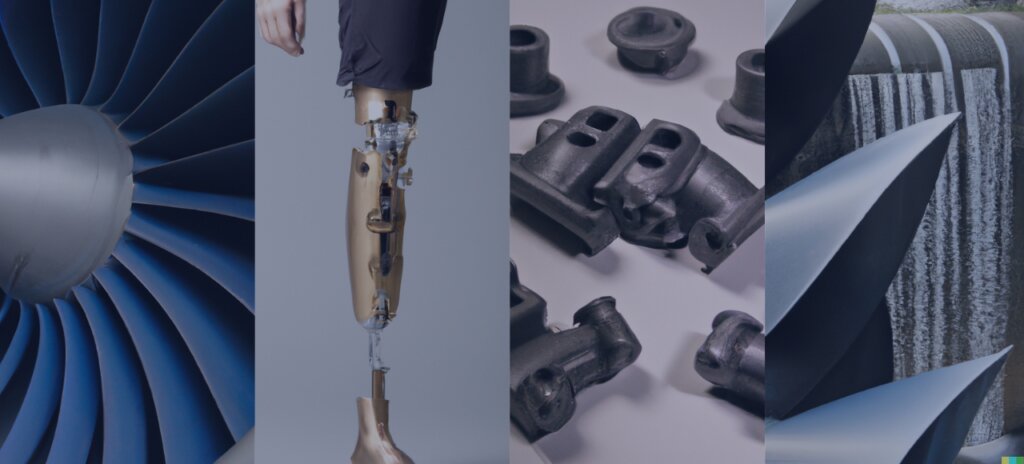
What Are The Steps Involved In The Investment/Precision Casting Process?
There are several steps involved in investment or precision casting:
- Create Metal Die : In casting, the wax model is destroyed by the heat of the molten metal, so a new wax model needs to be created for each casting. If investment casting is not used for small volumes, a wax pattern is required to produce mold or die. Careful calculations must be made when creating a mold to ensure that all the shrinkage factors on the metal casting, wax model, and ceramic material applied to that model are considered.
- Mold Creation : When you cast larger pieces, it’s easier to use a gate system. A gate system is a tree-like assembly of multiple wax models attached to a central wax gate. Molten metal is poured into the mold through a pouring cup, usually attached to the casting rods’ end. A ceramic coating is formed around the wax tree’s patterns and gating system. The wax tree is immersed in a silica suspension, which coats the wax with a ceramic shell, which is hardened once it dries. They then covered it with increasingly thicker layers of the same material until they achieved the desired thickness. The thickness of a ceramic shell largely depends on the casting’s size and weight and the temperature of the metal being poured. Usually, the wall thickness measures around 0.375 inches (9.525 mm). To create the shell, melted wax is first poured into a mold lined with a ceramic slurry. The slurry hardens and dries, forming a hollow shell.
- Finishing : After casting, parts may be sandblasted or ground to remove imperfections and smooth surfaces near holes. Depending on the metal type, it has to be heat-treated to harden the final part.
- Produce Wax Pattern : Wax models are used in the casting process. One wax model is created for every part that will be cast. Wax is melted and injected into a mold or die and hardens. A core may be required to develop internal functions. The resulting wax model is an exact copy of the manufactured part. Every wax model made equals a new cast; the two processes are similar, but wax is used instead of molten metal.
- Pouring : The ceramic mold is heated to between 550 and 1100 degrees Fahrenheit. This process strengthens the mold and removes residue, such as wax or dirt, from the mold material. The molten metal is poured into the mold while it is still hot. The metal flows into each mold cavity through a central gating system. The heated mold allows the metal to flow easily through delicate, detailed parts, producing a casting with better dimensional stability as it cools and shrinks.
- Cooling : When metal is poured into a mold, it cools and hardens, becoming rigid. The cooling time varies depending on the material being cast and the thickness of the casting.
- Shakeout : When the ceramic mold hardens, it breaks, and the castings can be removed. The mold is often broken manually or with water jets. Once removed, the castings are separated from the gating system by burning, sawing, cutting, manual impact, or cold breaking with liquid nitrogen.