Investment Casting: A Precision Manufacturing Process
Investment casting, commonly referred to as lost wax casting, is a manufacturing procedure where a mold is made from a wax design and then filled with molten metal to form the finished product. This process is renowned for manufacturing complicated pieces with high levels of precision and surface quality. Several industries, including aerospace, automotive, medical, and jewelry manufacturing, frequently use investment casting. The technique is adaptable and can create pieces from a variety of materials, including titanium, steel, and aluminum.
Investment Casting Process
Investment casting, also referred to as lost-wax casting, is a highly accurate and adaptable manufacturing technique that has been employed for a long time to produce a wide variety of goods. Investment casting can create pieces with remarkable accuracy and surface polish for anything from elaborate jewelry to complicated aerospace components. A wax pattern accurately represents the finished item that is first made. A mold is then made by covering this pattern with a ceramic substance and letting it cure.
After that, the wax pattern is melted or burned out of the mold, leaving a gap in the finished item’s shape. Molten metal is poured into the desired mold, solidifies, and forms a void. The ceramic mold is removed to expose the finished result when the metal has cooled. The capacity to create pieces with incredibly complicated shapes and minute features is one of investment casting’s main advantages.
Because of this, it is perfect for manufacturing intricate parts with precise tolerances, such as those used in the aerospace and medical industries. Different variety of metals, including steel, aluminum, titanium, and even rare alloys, can be used in investment casting. This adaptability enables the production of parts for a wide range of applications, from lightweight aviation components to robust industrial machinery components.
The capacity of investment casting to manufacture pieces with a high-quality surface finish is another advantage. Unlike other casting techniques, investment casting does not require machining to get the necessary polish. Instead, the smooth surface of the wax pattern is transferred to the finished product, producing a polished, smooth finish that requires minimal post-processing.
Additionally, investment casting is renowned for its effectiveness and cost-effectiveness. The procedure can manufacture products with extremely precise tolerances, hence minimizing the need for costly machining and post-processing. Moreover, investment casting is highly automated, lowering the manual labor demand and boosting production speed and precision.
Investment casting is an exact and versatile manufacturing technique that offers a variety of advantages, such as the capacity to make delicate and complicated parts, a high-quality surface finish, and cost-effectiveness. Whether you are in the aerospace, automotive, medical, or jewelry-making industries, investment casting is a tried-and-true method for manufacturing high-quality goods.





Investment Casting Cost: How Much Does It Cost to Cast an Investment Casting
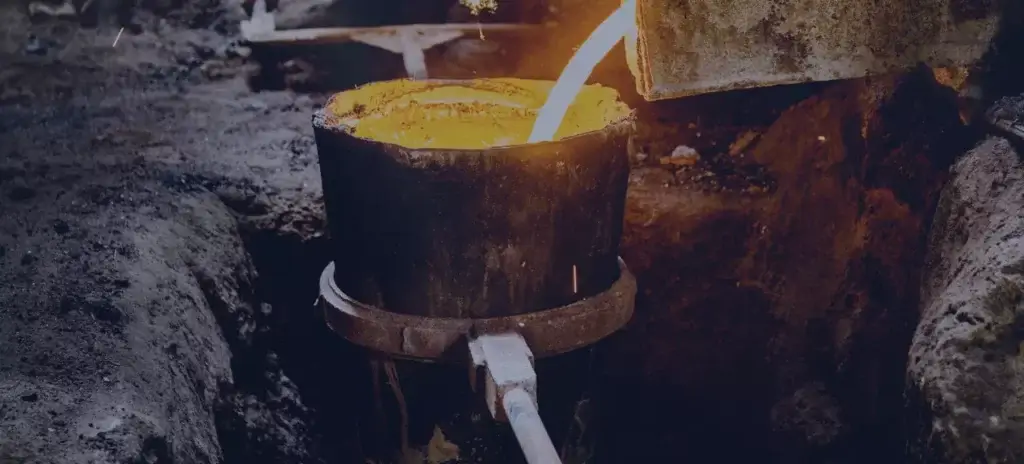
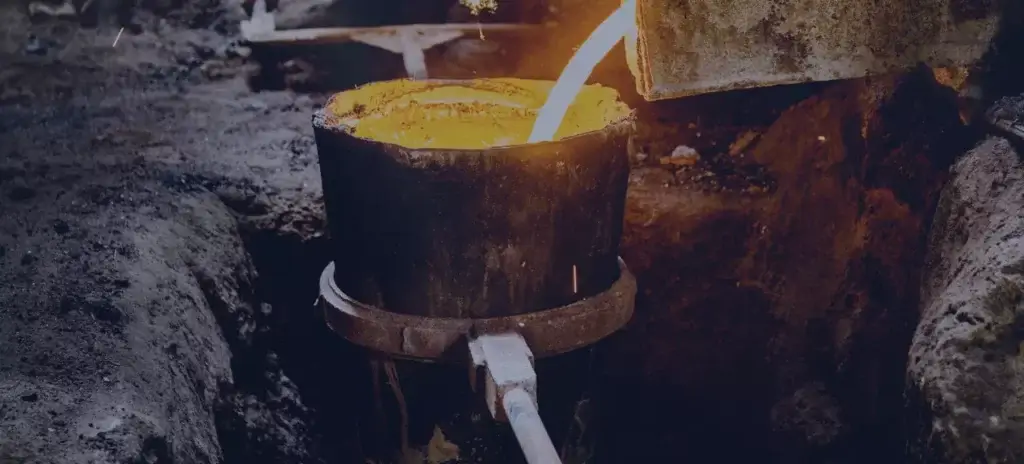
Several variables affect the casting prices, including the size and complexity of the component being cast, the material employed, and the number of pieces produced. Due to the process’s time-intensive nature and the materials’ expense, investment casting is generally more expensive than other casting methods. Among the primary elements that affect the cost of investment casting are the following :
- Part design and complexity: Components that have intricate shapes, tight tolerances, or specific requirements, such as internal passages or undercuts, will require more time and materials to make and, as a result, will cost more than those that do not have these characteristics.
- Material: Varying materials have different melting temperatures and require additional equipment and procedures to cast, which can impact the project’s cost.
- Tooling costs: Costs associated with tooling Investment casting necessitates the production of a mold, often known as a “tool,” for each individual part that is cast. Although the tooling price will change based on the size and intricacy of the component, it may constitute a sizeable fraction of the total cost.
- Quantity: The number of parts produced directly correlates to the cost per unit, which tends to drop as production volume rises. This is because of economies of scale as well as a reduction in the requirement for physical labor as the process becomes increasingly automated.
- Post-processing: The cost of post-processing, which may include machining, sandblasting, or polishing, will also have an impact on the final price of investment casting.
In general, the cost of investment casting can range anywhere from a few dollars per part for basic parts when producing them in considerable quantities to several hundred dollars or more per item for producing complex parts in low volumes. It is vital to work closely with an investment casting provider in order to receive an accurate estimate of the cost of a particular casting project. This can only be accomplished through tight collaboration.
Zetwerk is a manufacturer that offers a variety of Investment Casting Cost optimization options. Our proficiency in design for manufacturability and supply chain management enables us to produce investment cast parts of superior quality at a competitive price. Zetwerk utilizes cutting-edge manufacturing techniques to produce complex geometries with tight tolerances and exceptional surface finishes.
Our streamlined procedure permits quick turnaround times and effective production. In addition, Zetwerk offers end-to-end project management services, from material selection to finishing, to ensure that customers receive the highest quality products at the most competitive prices. By partnering with Zetwerk, customers can meet project objectives within budget.




