A356 Investment Casting: Properties, Design, Finish, & Quality Control
Due to its excellent strength and lightweight qualities, A356 aluminum alloy is preferred for investment casting. This aluminum-silicon alloy contains silicon, magnesium, iron, copper, and other trace elements, contributing to its distinctive physical and mechanical properties. The high strength-to-weight ratio of A356 aluminum alloy is one of its most prominent characteristics. This makes it an excellent material for aeronautical and automotive components that require both strength and lightweight. In addition, its ductility and formability make it easy to cast into complex shapes and sizes, as well as crack-resistant.
Another essential attribute of A356 aluminum alloy is its excellent corrosion resistance. This is due to the presence of silicon, which produces a protective oxide layer on the material’s surface, preventing the spread of corrosion. This makes A356 an excellent choice for components that will be exposed to corrosive fluids or hostile environments. In terms of thermal stability, A356 aluminum alloy has a relatively very low coefficient of thermal expansion, meaning that its size and form are not significantly affected by temperature fluctuations. This feature makes it appropriate for applications requiring dimensional stability, such as high-precision components or parts.
A356 aluminum alloy offers excellent machinability and weldability, making it simple to produce and adapt as necessary. This is particularly advantageous for applications where pieces must be altered or corrected after casting. Overall, the features and characteristics of A356 aluminum alloy make it an excellent material for investment casting, particularly for applications requiring a high level of strength, low weight, and dimensional stability. Its resistance to hostile conditions and corrosion and its formability and machinability make it a versatile and cost-effective material for various applications.
Design Consideration for A356 Investment Casting
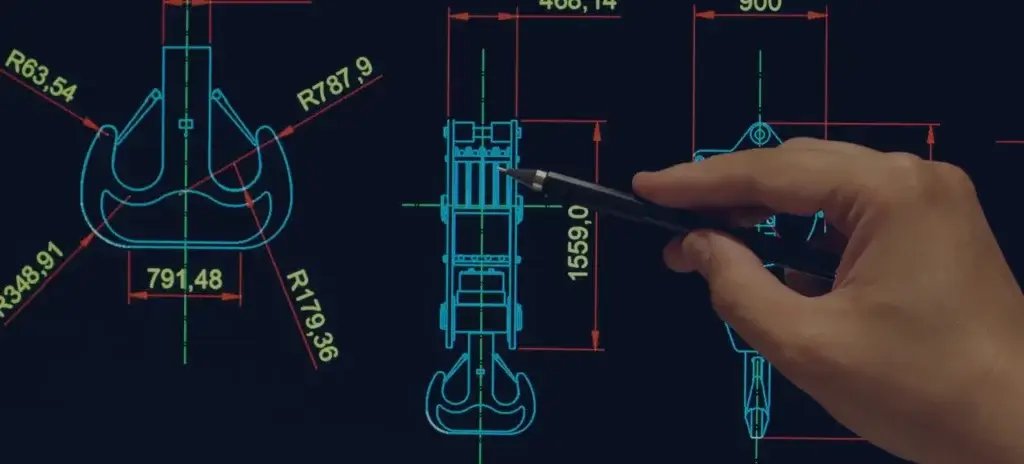
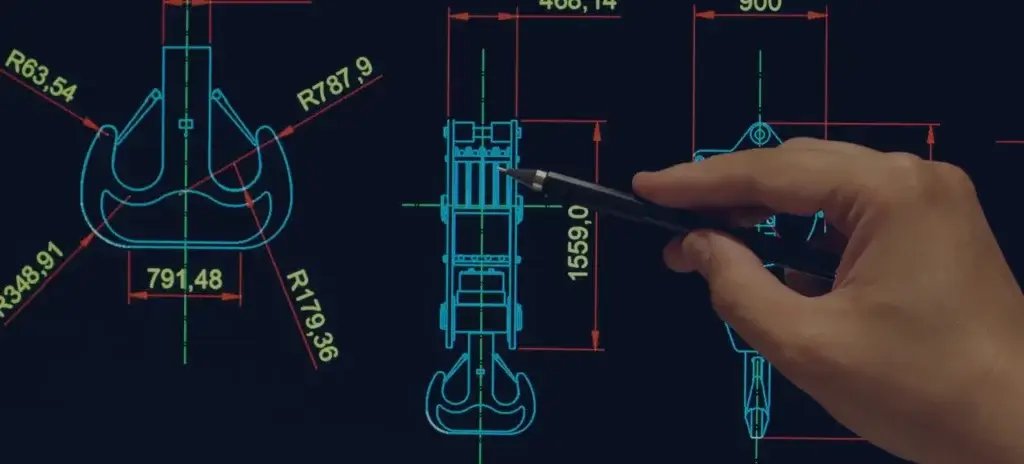
To ensure a good output, the design of parts and components for A356 investment casting involves carefully considering several crucial aspects. Among the most vital design factors for A356 investment casting are:
- Wall Thickness: The thickness of the part’s walls must be adequate to assure its strength and longevity but not so thick as to cause casting difficulties or add extra weight.
- Draft Angle: During the casting process, the draught angle, which is the slope of the part’s walls, must be designed for easy release from the mold. The minimum draught angle advised for A356 investment casting is 1 degree.
- Surface Finish: The part’s surface finish is crucial for its appearance and functionality. Complex geometries may necessitate additional post-processing processes to achieve the necessary surface finish on A356 investment castings with a smooth surface finish.
- Fillets and Radii: The use of fillets and radii can aid in evenly distributing stress across the part, hence increasing its overall strength.
- Size and Complexity: The size and complexity of the part can affect the casting process; therefore, it is essential to design components within the investment casting companies capabilities.
- Undercuts: Undercuts are sections of a part that cannot be extracted from the mold without causing damage to the part. Avoiding undercuts can simplify the casting process and enhance the final product’s quality.
Engineers and designers can optimize the casting process and manufacture parts that fulfill their standards by considering these design concerns. In addition, it is usually advised to work closely with the investment casting foundry to ensure that the design is viable and that the final product will fulfill the required performance specifications.





Post-Processing Techniques for A356 Investment Castings to Improve Surface Finish
When designing parts and components, the surface finish of A356 investment castings is a key issue to consider. A smooth, uniform surface finish can enhance a component’s appearance and function by decreasing friction and wear. A356 castings can be finished using a variety of surface finishes and post-processing processes to get the desired result:
- Shot Peening: Shot peening utilizes high-velocity metal shot to improve the part’s surface polish and fatigue strength.
- Sandblasting: Sandblasting can eliminate rough patches or surface flaws, resulting in a smoother and more consistent finish.
- Anodizing: Anodizing is a process that produces a thick protective oxide coating on the surface of a component, thereby enhancing its corrosion and wear resistance.
- Polishing: Polishing can generate a highly reflective and smooth surface, making it suitable for cosmetic components.
- Grinding: Grinding can be used to eliminate any remaining rough areas or surface flaws, resulting in a highly smooth surface finish.
Depending on the exact application, these post-processing procedures can be utilized to generate a variety of surface finishes for A356 investment castings. When selecting a surface treatment choice, it is essential to examine the part’s intended application and associated performance requirements, such as wear and corrosion resistance. In addition, it is crucial to collaborate with the investment casting facility to establish the viability of the desired surface finish and to verify that the finished product satisfies the required specifications. Engineers and designers can enhance the appearance and performance of their A356 investment castings by carefully selecting the proper surface finish option and post-processing technique.
Zetwerk offers end-to-end services for A356 Investment Casting bespoke projects, from design and prototype through production and finishing. They have an experienced team of engineers and technicians who can optimize your design for the A356 Investment Casting process to assure high-quality, cost-effective production. Additionally, Zetwerk offers a variety of material alternatives and finishing services to satisfy your project’s individual needs. Zetwerk is a dependable partner for your unique project because of our modern facilities and stringent quality control procedures.




