Injection molding is a highly cost-effective process used for mass-producing plastic parts with tight tolerances. Industries like automotive, healthcare, etc., often need it to streamline their work process. However, whether for an individual or a business learning the injection molding cost is significant before opting to manufacture. Moreover, understanding the factors that influence injection molding cost is crucial for businesses in the manufacturing industry. It helps them estimate and regulate the expenditure. In this article, we will discuss these details. Learn advanced and comprehensive information on various aspects influencing the cost of injection molding. In addition, readers will get an idea of the average injection molding cost.
Factors that Determine Injection Molding Cost
Several factors influence injection molding costs. These factors would help you regulate the expenditure at different phases of injection molding. The major factors are:
Equipment Cost
Smaller desktop machines are suitable for low-volume production but may not be cost-effective for larger quantities. Industrial-sized machines are necessary for high-volume production but require more stringent facility requirements and skilled labor, increasing operation and maintenance costs.
Machine Type | Cost Range |
Desktop | $5,000-$15,000 |
Small-Scale Industrial | $15,000-$50,000 |
Large-Scale Industrial | $50,000-$500,000+ |
Thus, the size and complexity of the machine, depending on the production needs, influence the injection molding cost. It’s important to select the right equipment that aligns with your needs to optimize costs. This involves considering factors such as production volume, part complexity, material requirements, and cycle time efficiency.
Mold/Tooling Costs
Injection mold cost is another significant factor in injection molding expenses. The method of mold fabrication affects the overall cost. There are various methods available, such as CNC machining, electrical discharge machining (EDM), and 3D printing. CNC machining offers precise results but can be time-consuming and expensive for complex molds. EDM provides excellent accuracy but requires skilled labor and is suitable for intricate designs. On the other hand, 3D-printed molds offer a low-cost option for low-volume production runs due to their quick turnaround times.
Mold Fabrication Method | Advantages |
CNC Machining | Precision, High Quality |
Electrical Discharge | Accurate, Intricate |
Machining(EDM) | Designs |
3D Printing | Low Cost, Quick Turnaround Times |
Additionally, mold design plays a crucial role in determining the overall injection molding cost. An optimal design can reduce cycle time, material waste, and labor costs. It’s essential to work closely with experienced mold designers to ensure a cost-effective mold design that meets your specific requirements.
Material Costs
Material choice significantly influences the cost of injection molding. Prices for plastic resins used in injection molding vary based on the type of resin. Different plastic resins have varying performance characteristics and price ranges.
Plastic Resin Type | Price Range per Pound |
Polypropylene(PP) | $0.90-$1.20 |
Polystyrene(PS) | $1.00-$1.50 |
Polyethylene(PE) | $1.10-$1.40 |
Acrylonitrile Butadiene | $2.00-$2.50 |
When selecting materials for injection molding, it’s essential to consider both performance requirements and budget constraints to optimize the injection molding cost.
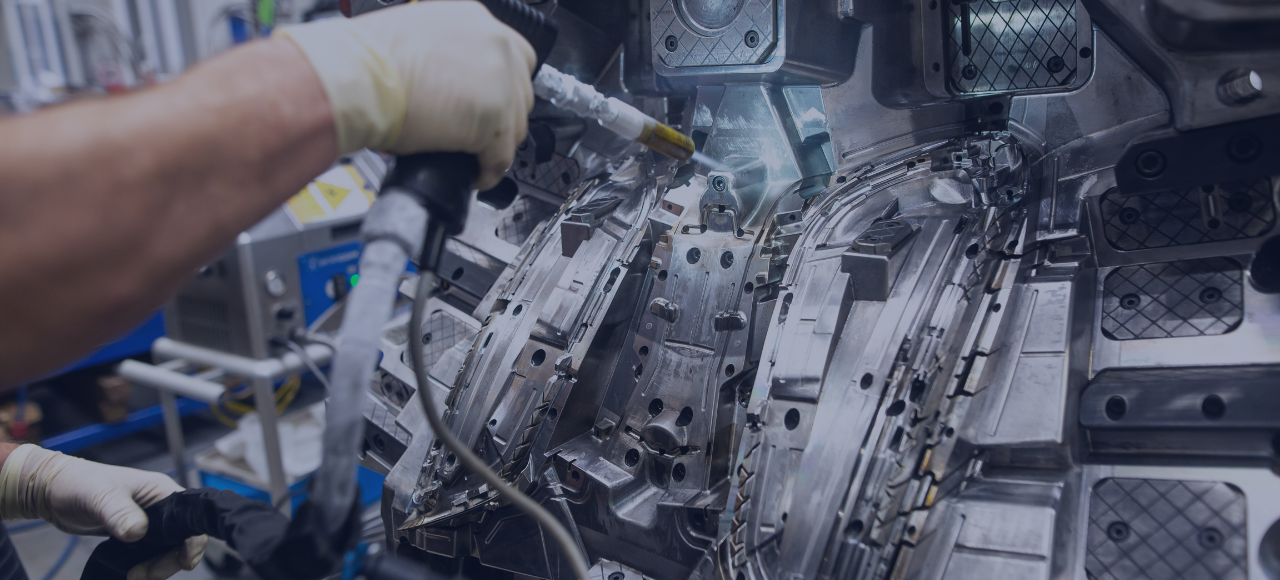
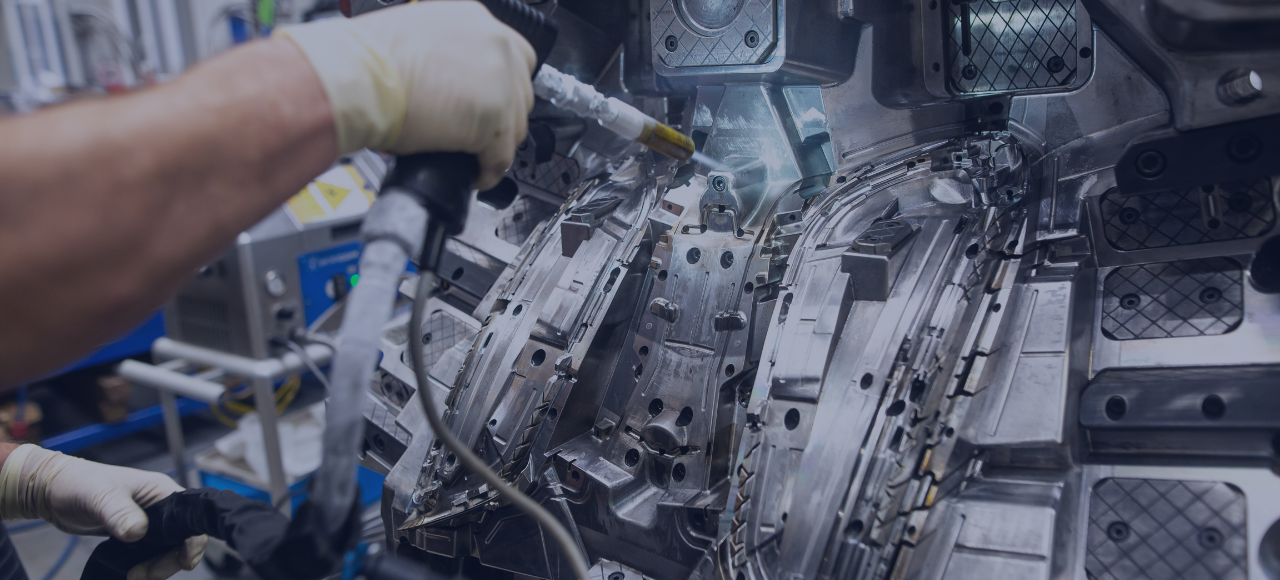
Labor or Service Costs
Labor or service costs associated with injection molding include setup/configuration costs, repair costs, and monitoring costs during the production process. Pre-Installation costs involve preparing molds for production runs, which can vary depending on the complexity of the part and the mold. Repair costs may be incurred due to maintenance or occasional mold damage or wear. Monitoring costs is essential to ensure quality control and prevent defects, ensuring that the final product meets specifications.
How to Reduce Injection Molding Cost
Due to a restrained budget, you might want to save money on injection molding. Here is how you can do it. Reducing the cost of injection molding can be achieved through design for manufacturing (DFM) principles. By optimizing the part design to eliminate unnecessary features and minimize complexity, it is possible to reduce material waste, cycle time, and labor costs. Thus, you can save money on injection molding.
Final Words
Thus, equipment costs, mold design, material selection, labor or service costs, and design considerations all play significant roles in determining the overall cost of injection molding. Whether you want it for household products or need it in your electronics business, learn about the cost and decide accordingly. By selecting the right equipment, optimizing mold designs with suitable materials, managing labor costs, and applying DFM principles, manufacturers can optimize the injection molding cost. Also, in this process, they can maintain high-quality production outcomes.
Looking for low-cost injection molding solutions? Zetwerk offers a wide range of manufacturing services, including injection molding. Explore the company’s expertise and comprehensive solutions for your business needs. Readers, please visit the Zetwerk Knowledge Hub for more articles related to injection molding costs and other manufacturing processes,




FAQs
While reputable manufacturers are transparent about costs, there might be potential hidden costs related to mold maintenance, design changes after mold construction, or unexpected production issues. Clear communication with the manufacturer is crucial to avoid surprises.
Injection molding cost calculators are valuable tools for estimating specific part costs. Additionally, online quotes from service providers can provide benchmark pricing based on your requirements.
The decision between upfront tooling investment and per-part costs depends on the specific project goals. For large production runs, higher upfront investment in quality tooling might be beneficial. For smaller runs, focusing on per-part costs might be more sensible.
Common pitfalls that increase mold costs include complex part designs with undercuts or textured surfaces, excessive cosmetic finishes or appearances, and the need for long, thin tools or multiple molds.
Zetwerk offers competitive pricing for its manufacturing services, including injection molding, aluminum extrusion, etc. By leveraging its extensive network of qualified suppliers and optimized processes, Zetwerk delivers high-quality products at affordable prices.