Regarding component manufacturing, rubber and metal hold indispensable positions across various industries, including automotive, aerospace, electronics, and more. These industries continually aim to elevate the standards of their product quality, longevity, and overall performance, which can only be achieved with the advancement in materials and technologies. Over the years, substantial progress has been witnessed in refining the manufacturing techniques for these essential materials, yielding enhanced efficiency, precision, and environmentally conscious practices. This blog explores the latest rubber and metal component manufacturing advancements and their implications for various industries.
Advancements in Rubber Component Manufacturing
Material Innovation
Rubber component manufacturing has come a long way, from natural rubber to the synthetic rubber compounds that dominate the market today. Advancements in material science have led to the development of specialized custom rubber parts tailored for specific applications, such as silicone rubber for medical devices and EPDM for automotive seals. These materials offer improved performance, durability, and resistance to environmental factors.
Injection Molding
Injection molding has revolutionized rubber component manufacturing. This process allows for high precision and consistency in producing complex shapes and intricate details. Moreover, it reduces material waste, making it a more sustainable option. Recent developments in injection molding technology have further improved cycle times and energy efficiency.
3D Printing
Additive manufacturing techniques, including 3D printing, have expanded into rubber component manufacturing. This technology enables rapid prototyping and customization, reducing lead times and costs. Researchers are also exploring using 3D printing for rubber-metal hybrid components, opening up new possibilities for design and functionality.
Smart Rubber
Integrating sensors and smart materials into custom rubber parts is another exciting development. Innovative rubber can monitor and respond to environmental conditions, making it valuable for civil engineering applications like structural health monitoring or real-time tire pressure monitoring in automotive.
Recycling and Sustainability
As environmental concerns grow, manufacturers increasingly focus on recycling and sustainable practices. Rubber recycling technologies are improving, allowing for the reuse of rubber materials in new components. Sustainable sourcing and production methods are also gaining traction in the rubber industry.
Nanotechnology in Rubber Compounding
Nanotechnology has found its way into rubber component manufacturing, allowing for the development of nanocomposite rubber materials. By incorporating nanoparticles into custom rubber parts, manufacturers can achieve remarkable improvements in mechanical properties, such as tensile strength and abrasion resistance. These nano-reinforced rubber materials are particularly beneficial in applications requiring extreme performance, such as high-performance tires and conveyor belts.
Rubber Recycling and Circular Economy Initiatives
Environmental sustainability is a growing concern, and the rubber industry is actively addressing it. Manufacturers are increasingly focused on recycling and reusing rubber materials to reduce waste and minimize the environmental impact. Some companies are exploring closed-loop systems to ensure that end-of-life rubber products are recycled and incorporated into new components, contributing to a circular economy.
Biodegradable Rubber
As the demand for eco-friendly materials rises, researchers are developing biodegradable rubber compounds. These materials are designed to break down naturally over time, reducing the long-term environmental impact of rubber products. Biodegradable rubber has applications in various industries, including agriculture (biodegradable mulch films) and healthcare (biodegradable medical implants).
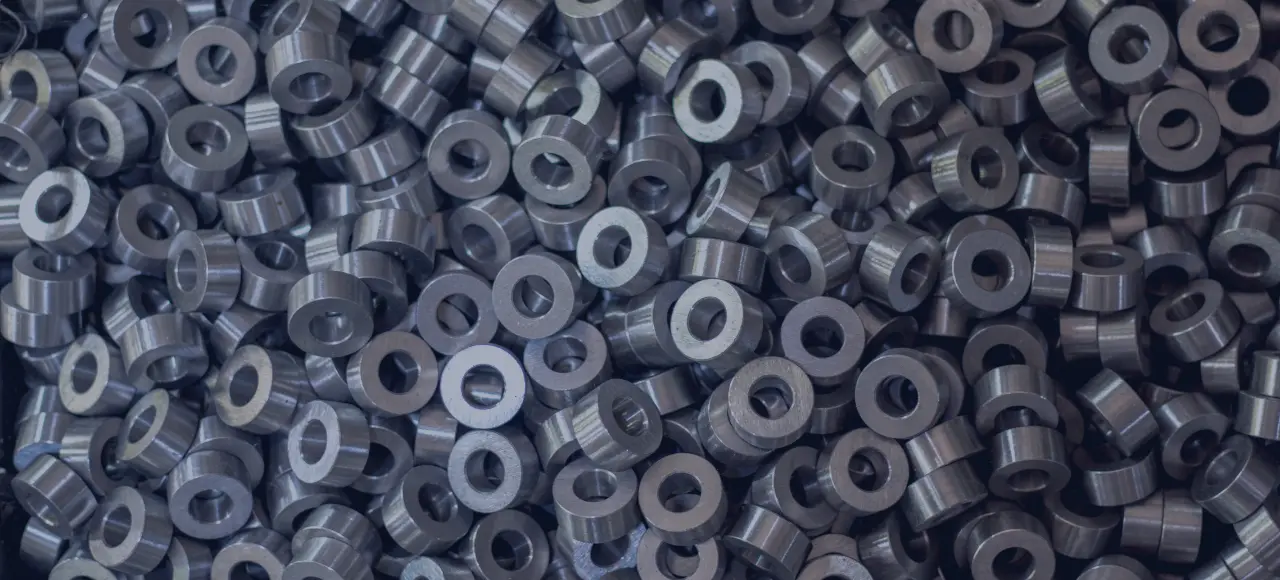
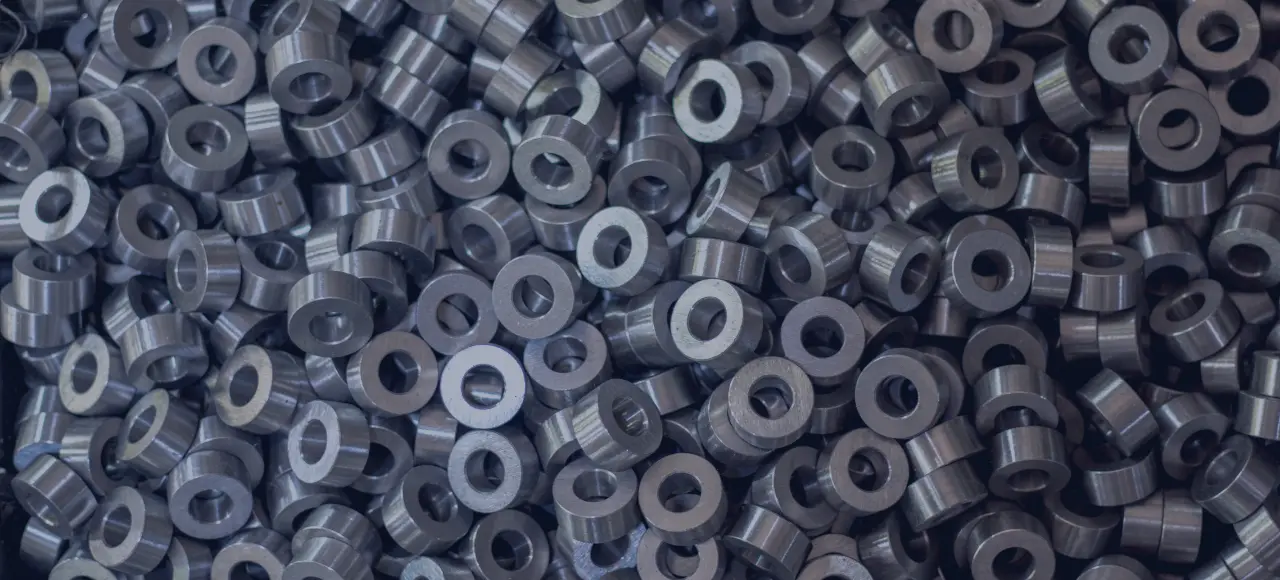
Advancements in Metal Component Manufacturing
Advanced Alloys
The development of new metal alloys has expanded the possibilities for small metal parts manufacturing. High-strength, lightweight alloys are particularly significant in industries like aerospace and automotive. For example, titanium alloys offer exceptional strength-to-weight ratios, while aluminum alloys are prized for their corrosion resistance.
Precision Machining
Precision machining techniques, including CNC and multi-axis milling, have become more sophisticated. These technologies enable the production of highly intricate and complex metal components with tight tolerances. Integrating artificial intelligence (AI) and machine learning has improved process control and efficiency.
Metal Additive Manufacturing
As with rubber, 3D printing has made significant inroads into metal component manufacturing. Metal additive manufacturing allows the production of complex, lightweight structures previously impossible to create through traditional methods. This technology is utilized in aerospace for turbine components and healthcare for custom orthopedic implants.
Surface Finishing
Surface finishing processes have seen advancements that enhance the performance and aesthetics of metal components. Techniques such as electroplating, anodizing, and powder coating improve corrosion resistance, wear resistance, and decorative options.
Digital Twins and Simulation
Digital twin technology, which involves creating a digital replica of a physical component or system, is being used to simulate and optimize metal component manufacturing processes. This reduces trial-and-error iterations and leads to more efficient production.
Hybrid Manufacturing
Hybrid manufacturing combines traditional subtractive processes (e.g., machining) with additive manufacturing techniques (e.g., 3D printing) in a single setup. This approach allows for creating highly complex metal components with intricate internal structures. For example, parts can be 3D printed with internal cooling channels, reducing the need for additional machining and improving heat dissipation in applications like aerospace and energy.
Digitalization and Industry 4.0
Small metal parts manufacturing has embraced Industry 4.0 principles, including integrating digital technologies, automation, and data analytics. Smart factories use sensors and data analysis to monitor and optimize the production process, improving efficiency, reducing downtime, and better quality control. This digital transformation profoundly impacts metal component manufacturing’s competitiveness and flexibility.
High-Performance Coatings and Surface Treatments
Advances in coatings and surface treatments have expanded the capabilities of metal components. These treatments enhance corrosion resistance, hardness, and friction reduction. For instance, PVD (Physical Vapor Deposition) and CVD (Chemical Vapor Deposition) coatings protect cutting tools and improve the wear resistance of critical components in industries like automotive, aerospace, and manufacturing.
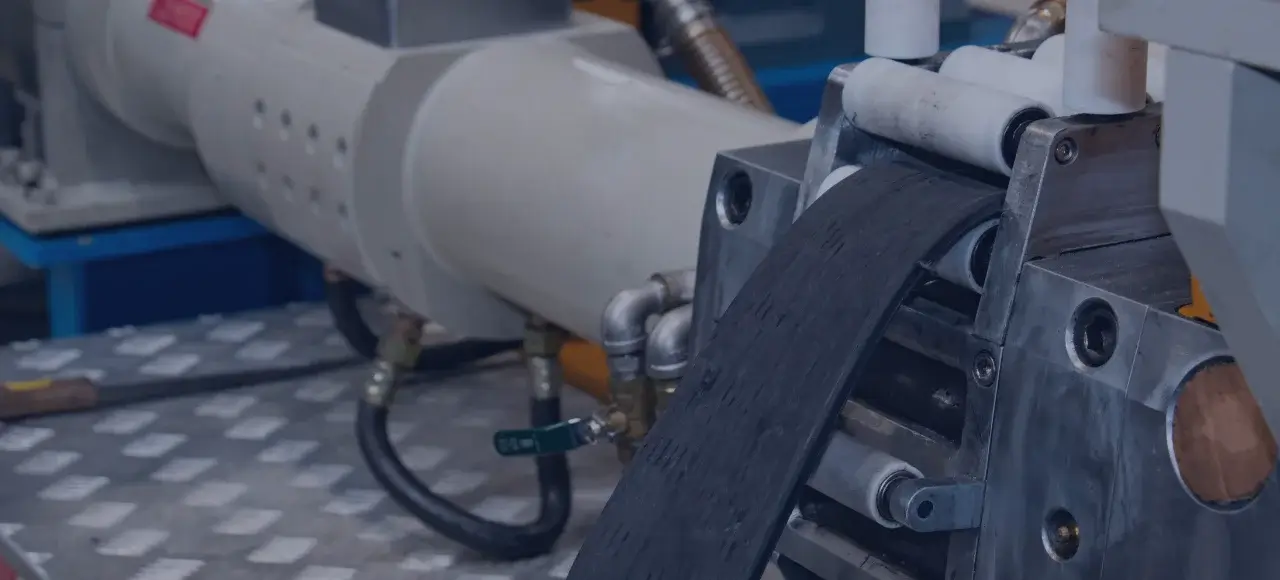
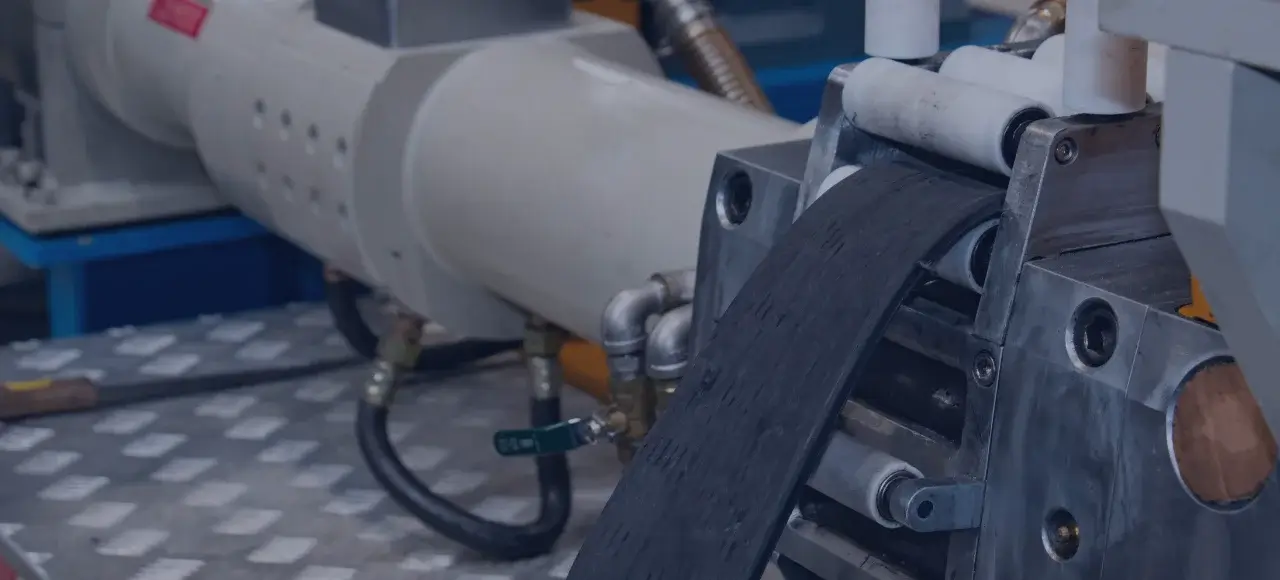
Implications For Industries
Automotive
Rubber and metal component manufacturing advancements have led to lighter, more fuel-efficient vehicles with improved safety and comfort features. Electric and autonomous vehicles also benefit from these advancements, requiring specialized components with unique properties.
Aerospace
The aerospace industry benefits from lightweight yet robust metal components and advanced rubber seals and gaskets that can withstand extreme conditions. Additionally, additive manufacturing reduces the weight of aircraft parts, leading to improved fuel efficiency.
Medical Devices
Rubber and metal component manufacturing advancements in the medical field have led to more reliable and biocompatible devices. 3D printing is used for creating customized implants, and smart rubber sensors enhance patient health monitoring.
Construction
The construction industry benefits from durable rubber seals and gaskets in infrastructure projects. Advanced metal components contribute to the strength and longevity of buildings and bridges.
Electronics
The miniaturization of electronic components relies on precision metal manufacturing techniques. Rubber components are also crucial in protecting sensitive electronics from environmental factors.
Conclusion
As the manufacturing landscape evolves, introducing better materials and technologies will be the key to further rubber and metal component processing advancements.
Zetwerk, one of the leading manufacturing units, walks on the path to adapting advanced technologies and best practices to meet the ever-changing needs of our clients. To learn how their services can positively impact your business’s bottom line, contact Contact Zetwerk for Services and Company Information today.




FAQs
3D printing offers several advantages, including creating complex geometries, reducing material waste, and customizing components for specific applications. In metal manufacturing, it allows for lightweight and intricate structures. In rubber manufacturing, it enables rapid prototyping and the production of custom seals and gaskets.
Advancements in rubber recycling technologies reduce the environmental impact of rubber manufacturing by allowing for the reuse of rubber materials. This contributes to sustainability by reducing the demand for new raw materials and minimizing the disposal of rubber waste in landfills.
Nanotechnology is used to create nanocomposite rubber materials that exhibit enhanced mechanical properties. These materials are more robust, durable, and have improved resistance to wear and tear. They find applications in high-performance areas like tires, conveyor belts, and industrial seals.
Digitalization and Industry 4.0 principles lead to more innovative, more efficient metal component manufacturing. They enable real-time monitoring of processes, predictive maintenance, and data-driven decision-making. This results in improved quality control, reduced downtime, and increased productivity.
While advanced metal alloys offer numerous benefits, it’s essential to consider safety. Some high-strength alloys may be more challenging to machine, requiring specialized equipment and safety precautions. Additionally, safety protocols must be followed when handling and disposing of certain alloying elements. Manufacturers should prioritize worker safety and environmental responsibility when working with advanced alloys.