Steel selection plays a pivotal role in the forging process, directly influencing the end products’ quality, performance, and durability. As a critical component of numerous industries, from automotive to aerospace, forging requires careful consideration of the steel properties to ensure optimal results. The suitable steel can enhance the strength, toughness, heat resistance, and machinability of the forged components while mitigating the risk of corrosion. Steel forging manufacturers play an important role in fulfilling business requirements through the right choice of steel.
Know About Selecting the Right Steel for Forging : Factors to Consider
Forging process and its significance in manufacturing
Forging is a manufacturing process that involves shaping metal through localized compressive forces. The material is deformed into the desired shape by heating the metal to the forging temperature and applying compressive forces. This process is widely used in various industries to create vital, durable, and intricate metal components.
Significance of forging:
- It lies in its ability to produce parts with exceptional mechanical properties, including high strength, toughness, and fatigue resistance.
- Forging refines the grain structure, resulting in improved mechanical properties and internal integrity.
- Forging offers precise dimensional accuracy, tight tolerances, and excellent reliability, making it ideal for demanding applications.
Material Selection in Forging Process
- Material selection plays a crucial role in the success of forging. The chosen material directly influences the final properties and performance of the forged components. The suitable material ensures the desired mechanical characteristics, heat, and corrosion resistance required for the specific application.
- When selecting materials for forging, it is important to consider factors such as composition, microstructure, and properties like strength, flexibility, and machinability, as different materials respond differently to the forging process.
- Optimal selection ensures that the material possesses the plasticity, malleability, and thermal stability to undergo deformation without failure. By carefully selecting materials that align with the forging requirements, manufacturers can effectively produce high-quality forged components that meet specifications and performance standards.
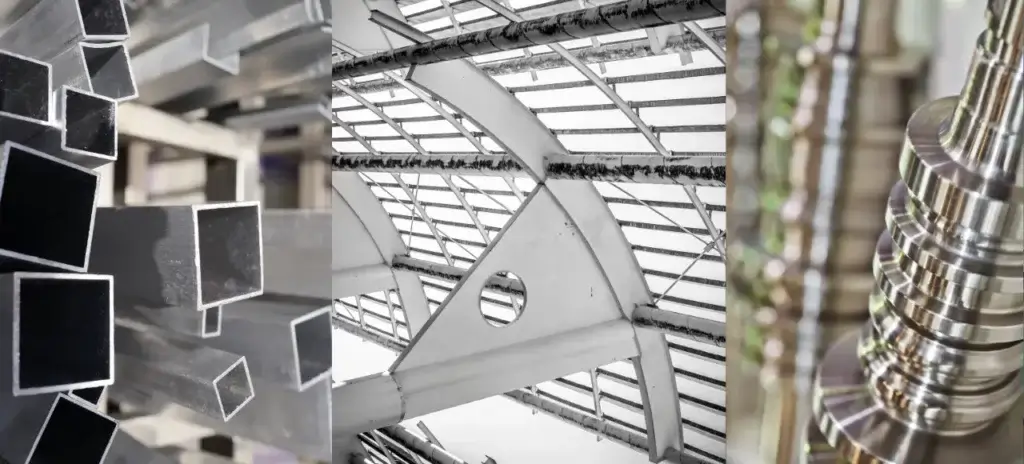
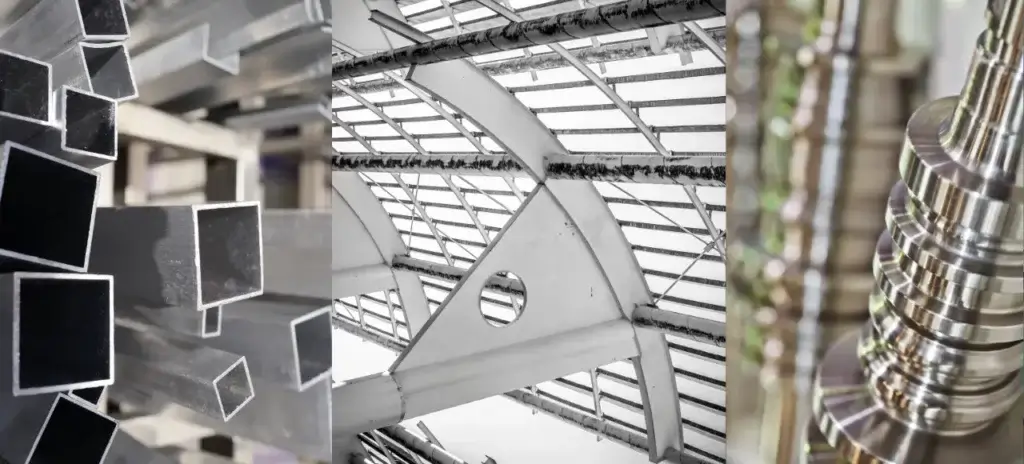
Key Factors to Consider in Steel Selection for Forging
Strength and Toughness
High strength and toughness are crucial properties in forged steel products. Strength refers to the material’s ability to withstand applied loads without deformation or failure, while toughness refers to its ability to absorb energy and resist fracture. In demanding applications, such as automotive or aerospace components, forged steel parts must withstand heavy loads, impacts, and dynamic forces. High strength ensures the structural integrity and durability of the components, while toughness helps prevent brittle fractures and enhances resistance to cracks or fractures under stress. When selecting steel for forging, specific properties contribute to achieving high strength and toughness. These include:
- Tensile strength represents the maximum amount of tensile stress a material can withstand before breaking. Look for steel grades with high tensile strength for robust and durable forged products.
- Yield strength refers to the stress level at which the material exhibits permanent deformation. Opt for steel with a high yield strength to ensure the forged components can withstand heavy loads and forces without plastic deformation.
- Impact toughness measures the material’s ability to absorb energy under impact loading. Seek steel grades with excellent impact toughness to enhance resistance against sudden shocks or impacts.
- Hardness is not directly synonymous with strength, it can indicate a steel’s ability to withstand wear and deformation. Optimal hardness levels contribute to the overall strength and toughness of the forged steel products.
Heat Resistance and Thermal Stability
Heat resistance and thermal stability are crucial when choosing steel for forging applications. The forging process involves subjecting the metal to elevated temperatures that exceed its critical temperature. Selecting steel that can withstand these high temperatures without significant degradation, such as softening or deformation, is vital.
Heat resistance ensures the material can maintain its structural integrity and mechanical properties under the demanding conditions of the forging process. Furthermore, thermal stability is essential to prevent premature failure, distortion, or structural changes in the forged components when exposed to prolonged high temperatures. It ensures that the forged parts retain their desired shape and performance, even in high-temperature environments.
Several steel alloys are renowned for their superior heat and thermal stress resistance, making them ideal for forging applications. For example, tool steels such as H13 and D2 are known for their high heat resistance and retention of hardness and strength at elevated temperatures.
Stainless steel grades like 304 and 316 offer good heat and corrosion resistance, making them suitable for forging applications exposed to high temperatures and aggressive environments. Alloy steels such as 4140 and 4340 are valued for their exceptional strength, heat resistance, toughness, and resistance to thermal stress. They are commonly used in demanding forging applications. High-speed steels like M2 and M42 are designed for high-temperature applications and cutting tools, providing excellent heat, hardness, and wear resistance.





Machinability and Formability
Machinability and formability are vital considerations when selecting steel for forging processes. The ease with which a material can be machined and formed directly impacts the efficiency and cost-effectiveness of the forging operations. Steel grades with excellent machinability can be efficiently shaped and modified, reducing machining time and minimizing tool wear.
Similarly, high formability allows for creating intricate and complex shapes during forging, enabling the production of components with precise specifications. Low-carbon steels, such as 1018 and A36, are known for their excellent machinability and moderate formability, making them versatile for various forging applications.
Additionally, specific steels like free-cutting steels, including 12L14, have additives that enhance their machinability, improving chip formation and reducing tool wear. Hot-work tool steels, such as H11 and H13, exhibit good formability and machinability while maintaining high heat resistance, making them suitable for forging dies and tooling.
Corrosion Resistance
Corrosion resistance is critical in selecting steel for forging applications, particularly when the forged components are exposed to corrosive environments. Steel with high corrosion resistance ensures the longevity and reliability of the forged parts by preventing degradation and structural damage caused by oxidation, moisture, or chemical exposure.
Stainless steel grades like 304, 316, and 17-4 PH are widely recognized for their exceptional corrosion resistance and are commonly used in forging applications where corrosion is a concern. These stainless-steel grades offer reliable protection against various corrosive agents and environments.
Furthermore, specialized corrosion-resistant alloys such as Inconel, Monel, and Hastelloy find application in demanding forging environments requiring exceptional corrosion resistance, such as aerospace, chemical processing, and marine industries. Choosing steel alloys with superior corrosion resistance guarantees the durability and performance of forged components, minimizing the risk of premature failure and reducing the need for frequent maintenance or replacement.
Conclusion
Selecting the right steel for forging is crucial to ensure optimal results. By considering factors such as strength, durability, heat resistance, and composition, forging steel manufacturers can make informed choices. The correct steel choice not only meets business requirements but also contributes to the overall success of the forging process. With careful consideration of these key factors, manufacturers can achieve high-quality, durable forged products.
By thoroughly evaluating the requirements and collaborating with experts, Zetwerk forging manufacturers can ensure the optimal selection of steel, leading to forged components that meet performance expectations, withstand operational conditions, and have extended lifespans. Steel selection serves as the foundation for successful forging, unlocking the full potential of the process and driving competitiveness, reliability, and overall manufacturing success.





FAQ’s
The main benefits include improved structural integrity, durability, resistance to heavy loads and dynamic forces, enhanced machinability and formability, heat resistance, thermal stability, and corrosion resistance.
Strength and toughness can be determined by reviewing technical specifications, consulting material datasheets, and seeking guidance from steel manufacturers or suppliers. Key indicators include tensile strength, yield strength, impact toughness, and hardness.
Stainless steel grades like 304, 316, and 17-4 PH offer excellent corrosion resistance. Specialized corrosion-resistant alloys like Inconel, Monel, and Hastelloy are also suitable for demanding forging environments.
Good machinability reduces machining time and tool wear, enabling efficient shaping and chip formation. High formability allows for creating complex shapes and intricate designs during forging, resulting in precise components.