Rolled Ring Forging Materials & Process
Rolled ring forging is a metal-forming process commonly used to manufacture seamless rings, shafts, and gears. The procedure involves heating a cylindrical metal billet to a high temperature and then forging it between two revolving rolls into a circular shape. The rolls form the billet into a ring, resulting in a robust and flawless component.
Rolled ring forging is frequently utilized for high-stress components requiring exceptional strength and toughness, including turbine blades, discs, gears, and flanges. The resulting component is seamless and uniform, making it excellent for high-pressure and high-temperature applications.
Rolled ring forgings are also renowned for their enhanced fatigue resistance, making them excellent for use in repeated loading applications. Depending on the purpose, the material used in rolled ring forging can vary greatly, but popular materials include carbon steels, alloy steels, stainless steels, and nickel-based alloys. The material selection will rely on the component’s operating conditions and needs, such as strength, tensile strength, and corrosion resistance.
The forged rolled ring takes multiple phases, including heating the billet, forging it between the rolls, and finally, cooling and finishing the component. The billet is heated at a temperature above the recrystallization temperature in a furnace, making it simpler to form. The billet is then positioned between rolls that revolve in opposite directions to generate a circular shape. During the forging process, the metal’s grain structure is aligned in the same direction as the ring’s radial axis, producing a component with superior strength and abrasion resistance.
Following the completion of the forging process, the part is cooled and then finished to the required specifications. Rolled ring forging is a versatile and efficient metal forming technique commonly employed in fabricating high-strength components. The method yields a durable, seamless part with enhanced fatigue resistance, making it suitable for use in demanding applications. The large variety of materials utilized in rolling ring forging enables the fabrication of components that satisfy specific requirements, such as strength, toughness, and corrosion resistance.
Challenges faced by rolled ring forging suppliers and the potential solutions
Rolled ring forging is a crucial step in the production of high-quality precision forging components, but it also presents unique challenges for suppliers. From growing costs of raw materials to increased rivalry, suppliers must anticipate the future to be successful. The good news is that solutions exist to assist forging suppliers in overcoming these obstacles and thriving in this competitive industry.
From streamlining production processes to investigating new materials and technologies, suppliers can employ a variety of techniques to stay ahead of the curve. Forging companies may overcome the constraints of the rolled ring forging business and continue to deliver the high-quality components that customers need if they adopt the appropriate strategy. Consequently, whether you’re a seasoned supplier or just entering the market, don’t let these obstacles deter you — find answers!
Future outlook and growth opportunities for the rolled ring forging market
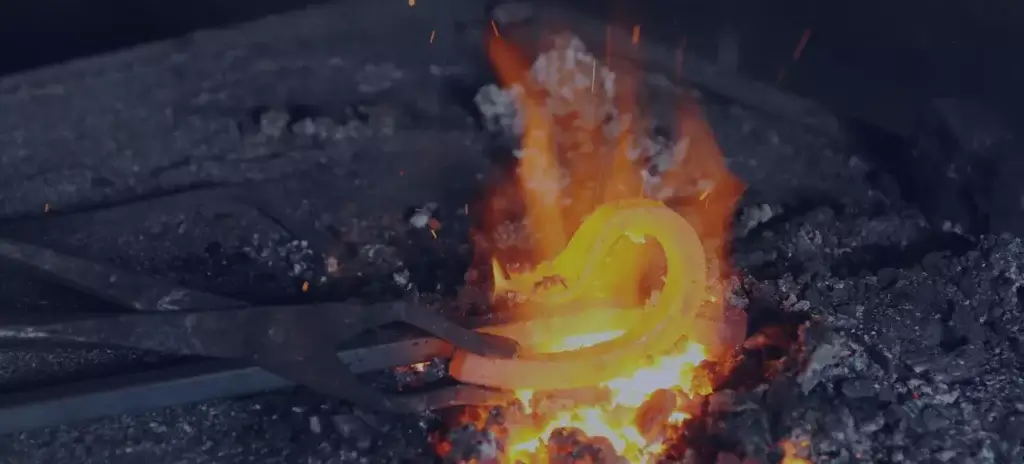
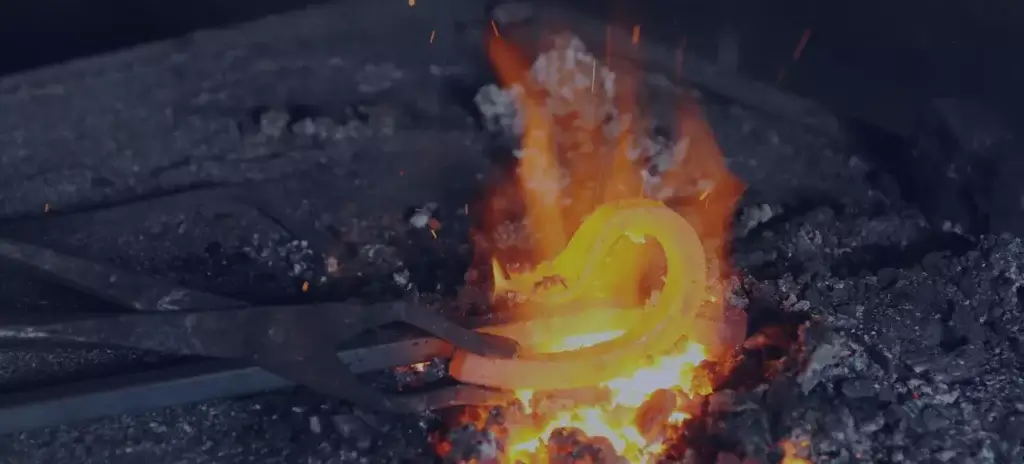
In the foreseeable future, numerous growth potentials exist for forged parts suppliers and manufacturers in the rolled ring forging market. Demand for high-quality, dependable components in areas such as aerospace, defense, and energy continues to fuel market growth. In addition, the rising demand for energy-efficient and eco-friendly products is anticipated to fuel the market’s expansion.
Suppliers and manufacturers must embrace new technologies and materials to capitalize on these development prospects and remain ahead of the curve. Due to their higher strength and resistance to corrosion, modern materials such as nickel-based alloys and titanium are gaining popularity. In addition, the deployment of digital technologies, such as Industry 4.0, is transforming the production process, making it more efficient and economical.
The market for rolled ring forging is also expanding due to the rising demand for bespoke components. As sector specialization increases, clients seek customized parts that meet their needs. This allows vendors to differentiate themselves by providing custom solutions and outstanding services.
The market for forged rolled ring is anticipated to expand in the upcoming years, presenting several chances for suppliers and manufacturers to prosper. Suppliers can stay ahead of the curve and expand in this dynamic market by embracing new technologies and materials and offering customized solutions. Therefore, if you are in the industry of rolled ring forging, the future seems promising; take a moment and make your imprint!





Benefits of Rolled Ring Forging Components
- Improved strength and toughness: They have a homogeneous grain structure that runs in the radial direction, which offers them superior and tensile strength in comparison to other metal forming processes.
- Fatigue resistance: Compared to other components, rolled ring forgings have superior fatigue resistance, making them excellent for applications that are subject to repetitive loads.
- Seamless construction: Due to their seamless design, rolling ring forgings are suited for high-pressure and high-temperature applications.
- Reduced lead times: Compared to conventional metal forming techniques, rolled ring forgings can be manufactured in substantially shorter lead times, minimizing downtime and boosting productivity.
- Versatility: Rolled ring forgings can be manufactured from a variety of materials, such as carbon steels, alloy steels, stainless steels, and nickel-based alloys, making them suitable for a vast array of applications.
- Consistent quality: The repeatability of the rolling ring forging method ensures that each component is of consistent quality, minimizing the chance of flaws and enhancing dependability.
- Improved dimensional accuracy: Due to their improved precision, rolled ring forgings are suited for use in applications requiring exact measurements.
- Cost-effectiveness: Rolled ring forging is cost-effective because it takes less raw material than other metal-forming techniques.
Zetwerk is a leading supplier company specializing in rolled ring forging for custom projects catering to particular industry needs. Our experienced engineers work closely with clients to understand the customer’s unique requirements and provide customized solutions that optimize performance and cost-effectiveness. From material selection to final inspection, Zetwerk’s rigorous quality control processes ensure that every rolled ring meets or exceeds industry standards. Whether you are in aerospace, oil, and gas, or any other industry, Zetwerk has the knowledge, expertise, and resources to deliver top-quality rolled rings that will exceed your expectations.




