Selecting a forging parts manufacturer for a product can be long and complex. Businesses often find that a seemingly perfect manufacturer can turn out to be the complete opposite. Researching and ensuring that you are selecting the right manufacturer for your product is essential. A good manufacturer will be able to produce your product promptly, in a high-quality fashion, and for a price that makes sense for your business. There are many different things you should look for when selecting a forged parts manufacturer. Before committing to one, do your due diligence and evaluate potential partners.
Zetwerk provides high-quality Forging Components and all secondary operations.
Submit the relevant part drawings, 3D files, and other information by clicking on the button below.





Welded Vs. Forged Parts
Forged and welded parts are both commonly used in manufacturing and construction, but they are made using different processes and have other properties and characteristics.
Forged parts are created by shaping metal using high-pressure hammering or pressing. This process involves heating the metal to a temperature where it becomes malleable and then shaping it using mechanical force. Forged parts are known for their strength and durability, and they are often used in applications where high load-bearing capacity is required.
On the other hand, welding parts are created by joining two or more metal parts together using heat and pressure. This process involves melting the edges of the metal parts and fusing them to form a single piece. Welded components can be made using various techniques, including MIG welding, TIG welding, and Stick welding.
There are several critical differences between forged parts and welded parts:
- Strength: Forged parts are generally stronger than welded parts, as the forging process creates a uniform, homogeneous material with no weld seams. On the other hand, welded parts may be weaker than forged parts due to the weld seams, which can be a source of stress and weakness.
- Ductility: Forged parts are often more malleable than welded parts, which can deform under stress without breaking. This makes them well-suited for applications where the parts may be subjected to high levels of stress or strain.





- Cost: Welded parts are generally less expensive to manufacture than forged parts, as the welding process is less labor-intensive and requires less specialized equipment. However, forged parts may be more cost-effective in the long run due to their superior strength and durability.
- Appearance: Forged parts often have a smoother, more refined appearance than welded parts, as the forging process produces a more uniform material. Welded parts may have visible weld seams and may not have the same finish level as forged ones.
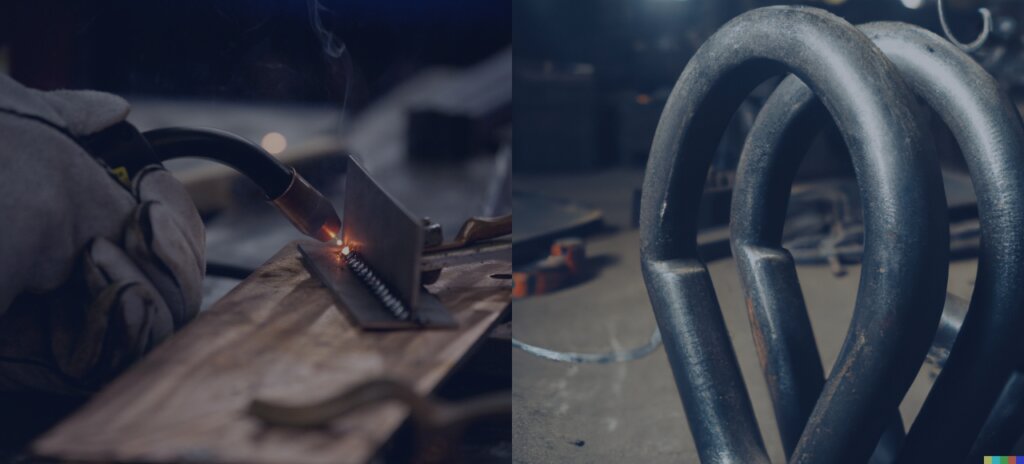
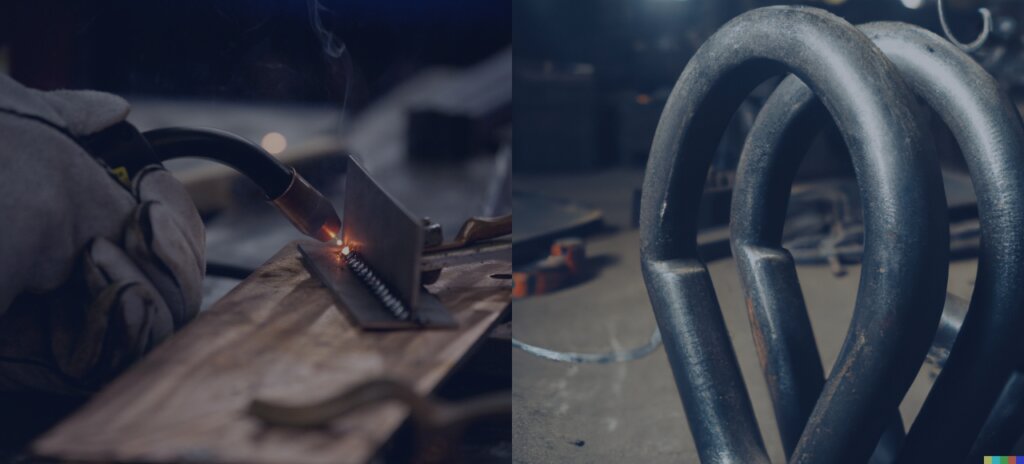
Common Forging Parts & Their Applications
There are many different types of forged parts, and they are used in a wide range of applications across various industries. Some common forging parts and their applications include:
- Shafts are long, cylindrical parts that transmit rotary motion. They are commonly used in motors, pumps, and other mechanical systems.
- Flanges are circular plates connected to pipes, valves, and other equipment. They are commonly used in constructing pipelines and other industrial and commercial applications.
- Spindles are slender, pointed parts that support and rotate other parts. They are commonly used in machine tools, such as lathes and grinding machines.
- Bolts and nuts are mechanical fasteners that hold parts together. They are used in various applications, including construction, automotive, and industrial machinery.
- Bearings are mechanical components that reduce friction and wear between moving parts. They are commonly used in motors, pumps, and other machinery.
- Gears are mechanical components that transmit power and motion between rotating shafts. They are used in various applications, including automotive, aerospace, and industrial machinery.
- Connecting rods are long, rod-like parts that connect the pistons of an engine to the crankshaft. They are a critical component in internal combustion engines.
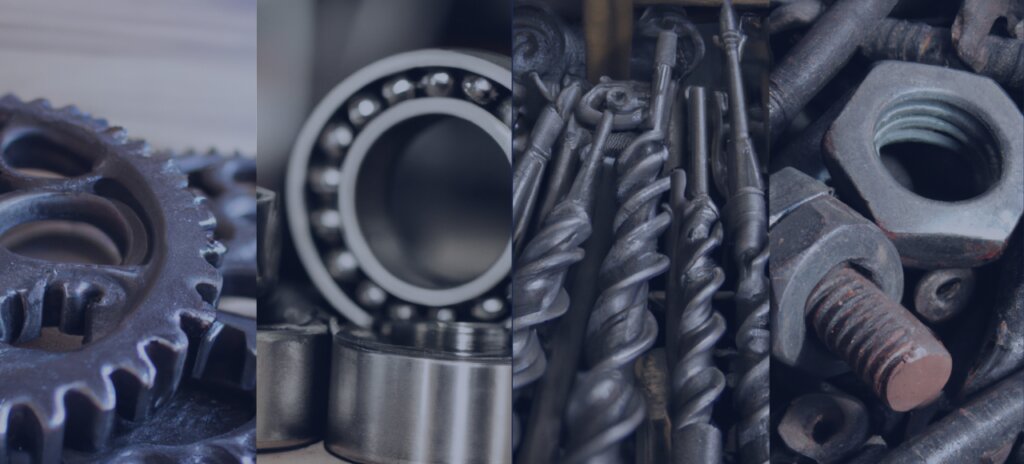
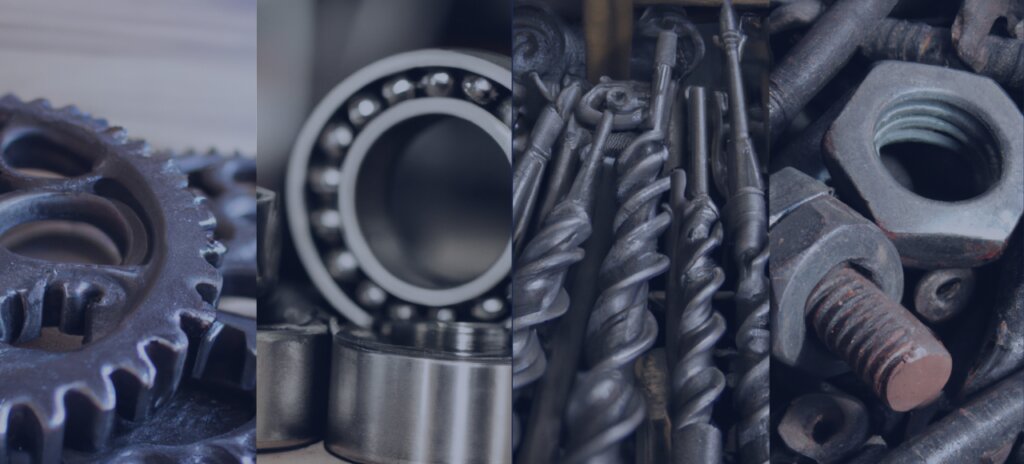
Advantages of Using Forged Parts in Manufacturing
There are several reasons why a manufacturer might choose to use forged parts:
- Strength and durability : Forged parts are typically more potent and durable than parts made using other manufacturing methods, such as casting. This makes them well-suited for use in applications where the parts will be subjected to high levels of stress or strain.
- Structural integrity : The forging process can improve the structural integrity of metal parts by eliminating weak points and promoting a more even distribution of stresses throughout the part.
- Customization : Forging allows manufacturers to create custom metal parts tailored to their specific needs. This can be particularly useful for manufacturers that require unique or complex parts that cannot be easily made using other methods.
- Cost-effectiveness : Forging can be a cost-effective manufacturing method, particularly for large production runs. The initial setup costs may be higher than in other ways, but the price per unit can be lower due to the increased production rates achieved with forging.
- Energy efficiency : Forging can be an energy-efficient manufacturing process, as it typically requires less energy to produce a given amount of material than other methods, such as casting.
Ultimately, your business’s best forging parts manufacturer will depend on your specific needs and requirements. It’s essential to research and choose a company with the manufacturing capabilities and experience to meet your needs and produce high-quality products.




