Forging Dies: A Guide to the Latest Trends and Technologies
Forging dies are a vital component of the metal forging industry since they provide the equipment for shaping and forming metal into intricate and complex patterns. With technological improvements, the market for forging dies is continually expanding, giving new solutions to satisfy the requirements of modern manufacturing. To stay abreast of the most happening trends and technologies, it is crucial to comprehend the principles of forging dies and the innovations reshaping the industry. The utilization of sophisticated materials is a recent development in forging dies.
The use of high-performance alloys such as tool steel and tungsten carbide has expanded in recent years. These materials’ enhanced hardness, wear resistance, and endurance makes them perfect for high-volume production and complex forging applications. In addition, the use of ceramic materials in forging dies has grown in popularity due to their superior heat resistance and dimensional stability.
The rising use of computer-aided design (CAD) and computer-aided manufacturing (CAM) software is another development in the forging die market. These technologies enable the construction of intricate and accurate die designs that can be adjusted for production efficiency and quality. By utilizing these technologies, firms can drastically reduce design and development time, allowing them to provide new items to the market quickly. In recent years, the forging die business has also emphasized automation more. Automated technologies, such as robotic forging cells, can significantly boost production efficiency and decrease the likelihood of operator error.
In addition, introducing sensors and real-time monitoring systems can provide forging die manufacturers with valuable die wear and performance data, enabling them to make educated maintenance and replacement decisions. Finally, it is crucial to note that sustainability and environmental effect are gaining importance in the market for forging dies. As a result, manufacturers are investigating methods to decrease waste and improve energy efficiency in their operations. This involves using environmentally-friendly materials, such as biodegradable polymers, and the establishment of recycling programs for spent forging dies.
The forging die market is continually evolving, driven by technological developments and changing client needs. By understanding the latest trends and technology, producers may stay ahead of the curve and satisfy the needs of modern manufacturing. Whether utilizing modern materials, computer-aided design tools, automation, or environmental initiatives, the future of forging dies is bright and full of prospects.
What To Know About Forging Dies
Forging dies are a crucial component in the metal forging process, providing the tools to shape and form metal into the appropriate shape. Whether you are a manufacturer, engineer, or someone interested in the metal forging sector, you should be aware of a few essential facts concerning forging dies. First, forging dies are available in various sizes and forms, depending on the application. Some forging dies are plain and simple, while others are elaborate and sophisticated, developed for more specific applications.
When selecting a forging die, it is essential to evaluate the project’s particular needs, such as the size and shape of the metal component, the forging process employed, and the production volume. The material from which forging dies are constructed is an additional crucial factor. Due to their hardness, wear resistance, and dimensional stability, tool steel, tungsten carbide, and ceramic materials are often utilized for forging dies. The choice of material will rely on the project’s specifications, and the die’s estimated service life and performance.
An additional consideration while working with forging dies is the significance of maintenance and upkeep. During the forging process, forging dies are subjected to high levels of stress and wear, which, over time, can lead to lower performance and increased downtime. To avoid this, it is essential to inspect and maintain your forging dies regularly and replace them as necessary to ensure optimal performance.
In addition to classic forging dies, there are now many creative solutions available in the market that can increase the efficiency and quality of the forging process. This includes computer-aided design (CAD) and computer-aided manufacturing (CAM) software and automated forging systems, such as robotic forging cells. By embracing these technologies, firms may optimize their operations and reduce the risk of operator error.
Finally, it’s worth emphasizing that sustainability is becoming increasingly crucial in the forging die business. As a result, many manufacturers are researching ways to reduce waste and boost energy efficiency, such as employing environmentally-friendly materials and developing recycling programs for spent forging dies. Forging dies play a vital part in the metal forging process, and it is essential to comprehend the aspects that influence their selection and performance. By learning the fundamentals of forging dies, whether you are a manufacturer, engineer, or industry enthusiast, you can ensure that your operations are optimized and efficient.





The Deciding Factors When Selecting Forging Dies For Your Company
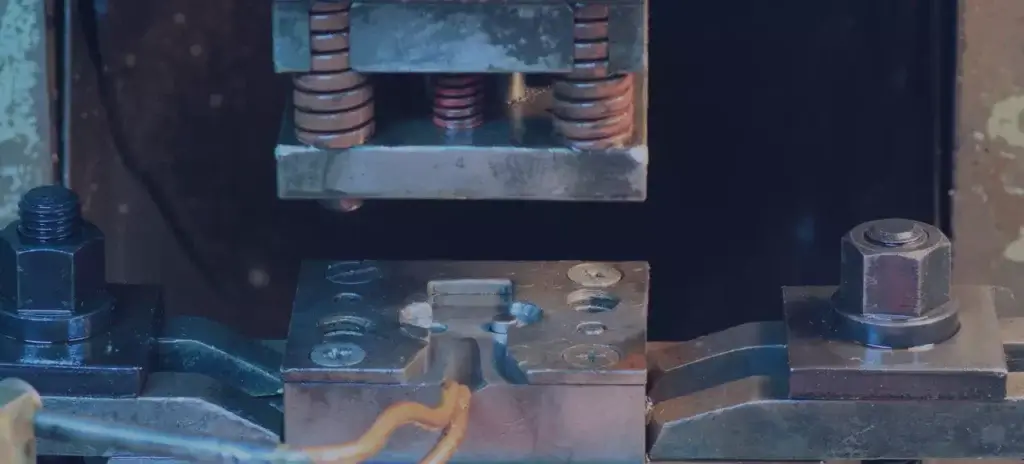
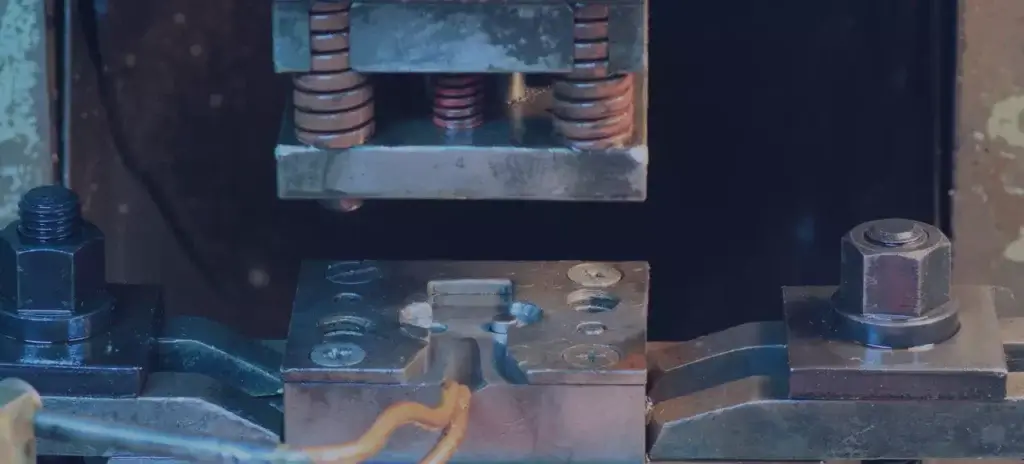
Several aspects must be addressed when purchasing forging dies for your firm to guarantee that you make the optimal decision for your specific requirements. Whether you are a factory trying to optimize your operations or an engineer looking for the correct tooling for a project, the following three variables are essential for making the right decision.
- Material Requirements: The initial thing to evaluate is the project’s material requirements. Various materials, including tool steel, tungsten carbide, and ceramics, are used to construct forging dies. The choice of material will depend on the forging technique used, the metal component’s size and shape, and the die’s projected service life and performance. It is essential to select a material with the required hardness, wear resistance, and dimensional stability for your application.
- Production Volume: When selecting forging dies, it is crucial to consider the operation’s production volume. A die built for high production efficiency and little maintenance is often the ideal choice for high-volume production. In contrast, a die intended for adaptability and accuracy may be preferable for low-volume production.
- The complexity of Design: The design of the forging die is also essential. Typically, a simplistic design is sufficient for simple forging applications. However, a die built for precision and versatility may be necessary for more complex applications. Additionally, computer-aided design (CAD) and computer-aided manufacturing (CAM) software can be immensely beneficial in optimizing the technique of complicated forging dies.
While picking forging dies for your business, you must examine the material specifications, manufacturing volume, and design complexity. Considering these three deciding criteria, you can ensure that you make the optimal decision for your requirements and that your operations are maximized for efficiency and quality. By understanding the significance of these aspects, whether as a manufacturer or an engineer, you can make decisions that will improve your operations and help you reach your objectives.
Zetwerk is a leading manufacturer that provides customized solutions for forging die production. With our facilities and cutting-edge technology, we can produce forging dies of the highest quality tailored to your project’s specifications. The seasoned engineers and designers at Zetwerk work closely with customers to comprehend their needs and design forging dies that are optimal for their application. The forging die manufacturing expertise of Zetwerk enables customers to achieve superior product quality, precision, and dependability. Our end-to-end capabilities, which include die design, engineering, and fabrication, allow clients to obtain a comprehensive solution from a single source. Due to our dedication to quality, on-time delivery, and customer satisfaction, Zetwerk is a reliable manufacturing partner for forging dies.




