Introduction
In the realm of engineering and manufacturing, precision and durability are paramount. Forging is a time-tested method for crafting robust components among the various available techniques. Forged parts have cemented their position as key players in diverse industries, from automotive to aerospace. This comprehensive guide delves into the characteristics that set forged parts apart, explores their advantages, and sheds light on the broad spectrum of applications they cater to.
Characteristics of Parts Made by the Forging Process
Forged parts gain strength through a unique process involving high pressure that compresses and shapes metal. This process eliminates voids, refines grain structure, and enhances toughness. Unlike cast parts, forged components have uninterrupted grain flow, boosting structural integrity. Key forged component characteristics include:
- Exceptional Strength and Durability: Forged parts are renowned for their unmatched strength, making them ideal for applications requiring robust components that can withstand high stress and loads.
- Improved Grain Structure: Forged components showcase finer and more uniform grain structures, contributing to their enhanced mechanical properties and reliability.
- Reduction of Porosity and Inclusions: The forging process minimizes internal defects such as porosity and inclusions, resulting in parts with improved structural integrity and performance.
- Enhanced Structural Integrity: The forging process imparts a refined microstructure, strengthening the overall structural integrity of the parts and reducing the likelihood of cracks or fractures..
- Consistency in Mechanical Properties: Forged parts offer a consistent and predictable set of mechanical properties, ensuring reliability and uniform performance across various applications.
- Fine Surface Finish: Forged surfaces often exhibit smoother finishes than other manufacturing methods, enhancing aesthetics and functionality
Advantages of Forged Parts
Unparalleled Strength and Durability
Forged parts excel in strength and durability due to the forging process. Under pressure and shaping, metal’s molecular structure transforms, yielding robust components that withstand stress and loads. From machinery to aerospace, forged parts prove their resilience.
Enhanced Structural Integrity
The parts post-forging have enhanced structural integrity from meticulous forging. Controlled shaping eliminates internal irregularities, yielding uniform microstructure. This resilience wards off cracks and anomalies under demanding conditions, ensuring reliability in the aerospace and power sectors.
Optimized Grain Flow
Forged parts achieve exceptional durability by optimizing grain flow during forging. For example, aerospace turbine blades have aligned grain structures for improved fatigue resistance. Controlled grain flow prevents cracks, ensuring longevity and reliability in demanding conditions, which is crucial for mission-critical sectors.
Better Fatigue Resistance
In engineering, fatigue resistance drives component choice. Forged parts shine here, enduring cyclic loading due to forging’s internal consistency, aligned grain flow, and structural integrity. Such fatigue resistance positions forged parts as reliable assets in demanding applications requiring unwavering performance under repeated stress cycles.
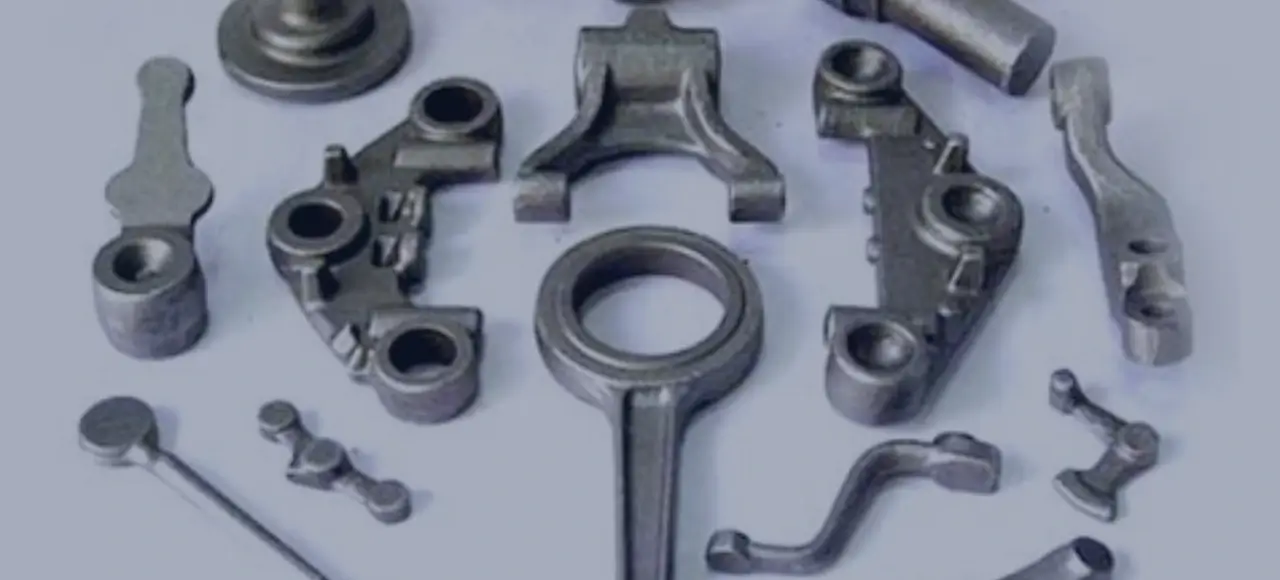
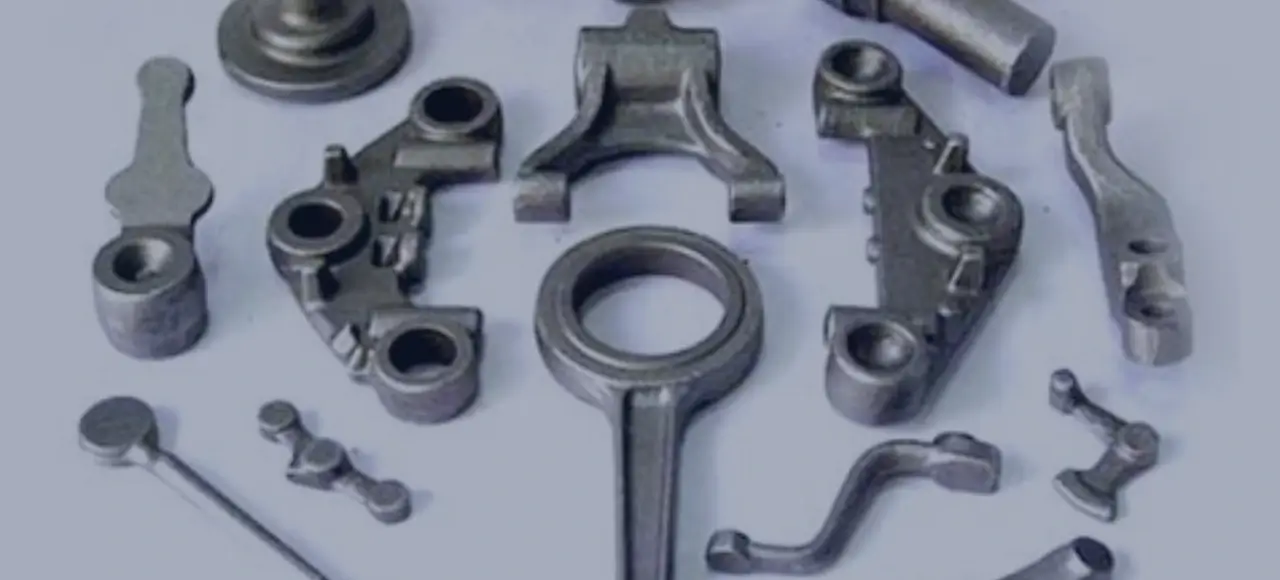
Common Applications of Forged Parts
Forged Parts in Various Industries
Industry | Applications |
Automotive | Crankshafts, connecting rods, axle beams |
Aerospace | Landing gear, turbine disks, structural components |
Oil and Gas | Valves, flanges, drilling equipment |
Power Generation | Turbine blades, generator shafts, power generation components |
Heavy Machinery | Construction equipment, mining machinery, industrial gearboxes |
The versatility of forged parts extends across industries, contributing to various applications:
- Automotive: Forged parts find their place in critical automotive components such as crankshafts, connecting rods, and axle beams, where strength and durability are paramount.
- Aerospace: Aerospace engineering relies on forged parts for components like landing gear, turbine disks, and structural elements that must endure extreme conditions.
- Oil and Gas: In the oil and gas sector, forged parts are used in valves, flanges, and drilling equipment, where reliability under high pressure and temperature is crucial.
- Power Generation: Turbine blades, generator shafts, and other power generation components benefit from forged parts’ inherent strength and precision.
- Heavy Machinery: Construction equipment, mining machinery, and industrial gearboxes rely on forged parts for their robustness and longevity.
Manufacturing Process and Quality Controls
Forging involves several methods tailored to the component’s design and material. Open-die forging and closed-die forging are standard techniques. Open-die forging shapes the workpiece between two flat dies, allowing for more intricate designs. On the other hand, closed-die forging involves shaping the metal within a die cavity. Both methods include heating the material to a specific temperature for enhanced formability. Quality control in forging is of paramount importance. Ultrasonic testing, magnetic particle inspection, and other non-destructive testing methods ensure the absence of defects. Dimensional accuracy is meticulously maintained through precision tooling and careful monitoring.
Conclusion
Forged parts are the embodiment of strength, precision, and durability. Their impact is undeniable, from their unique characteristics that result from the forging process to the myriad advantages they bring across industries. As technology and engineering continue to advance, the journey of forged parts evolves alongside, weaving innovation and excellence into the very fabric of modern manufacturing.
Zetwerk: Your Forging Partner
Zetwerk emerges as your trusted manufacturing partner when materializing your forged parts needs. With a commitment to quality, innovation, and a wide array of forging capabilities, Zetwerk simplifies turning your designs into reality. By harnessing cutting-edge forging technologies and adhering to stringent quality control, Zetwerk ensures that your components meet and exceed industry standards.




FAQs
Yes, advanced techniques like open-die and closed-die forging allow for intricate and complex shapes with precision.
While forging may involve higher upfront costs, the superior strength and durability of forged parts often lead to cost savings over the component’s lifecycle.
While there are size constraints, forging can produce a wide range of sizes, from small components like bolts to large parts such as turbine discs.
Quality control includes monitoring forging parameters, inspecting material integrity, and conducting non-destructive testing to ensure components meet required standards.