Custom Steel Forging: What You Need To Know
Custom steel forging is an industrial process in which heated steel is produced by hammering or pressing. A variety of steel products, including gears, shafts, and structural elements, are made using this technique. To start the process, steel is heated to about 2,200 degrees Fahrenheit.
Steel becomes flexible and able to be molded at this temperature. The steel is heated before being placed in a forging press or hammer, where it is pressed into a die or formed by a series of blows. The steel is then hardened by being quenched in a liquid, such as water. Extra heat treatment may further increase the steel’s hardness and strength.
The two most popular styles of steel forging are closed die and open die forging. Steel is forged in closed die forging between two dies that come into contact with the metal. This forging method is used to create precise and complicated forms. The steel is forged using a single die or directly hammered in an open die. Using this forging technique, extensive, simple shapes are produced.
The steel forging method is effective and cost-effective when creating steel products. Its versatility includes the capacity to fabricate steel products in various shapes and sizes. Furthermore, forged steel is often more durable and long-lasting than cast or machined steel. A range of steel products is produced using the crucial manufacturing process of steel forging. Compared to other production techniques, it is a more economical and practical technology that yields more substantial and lasting products.
Zetwerk provides high-quality Custom Steel Forging Components and all secondary operations.
Submit the relevant part drawings, 3D files, and other information by clicking on the button below.





Custom Steel Forging Process
Steel is treated at a very high temperature and later shaped with a hammer or press during the custom steel forging process. The steel is heated to between 2000 and 2,200 degrees Fahrenheit, which makes it malleable and moldable. After that, the steel is put in a forging press or hammer and shaped by repeated strokes or forced into a die. The steel is then cooled and quenched in a liquid, like water or oil, to harden it. The steel may undergo a second heat treatment to achieve the required hardness and tensile strength. An economical and successful method of making steel goods is custom steel forging. Since it can produce a wide range of steel product forms and sizes, it is also highly adaptable.





When do you need Custom Steel Forging for your business?
- Complex shapes: Forging enables the manufacture of precise and sophisticated geometries that may be difficult or impossible to realize using traditional manufacturing methods. This is very advantageous for components with intricate designs or exact tolerance requirements.
- Low volume production: Custom forging is frequently more affordable for low-production volume runs. It removes the need for expensive tooling and enables the production of distinctive and customizable parts.
- High precision: Forging can provide the dimensions needed for several niche markets, including the aerospace, defense, and medical sectors.
- Meeting specific requirements: Custom forging enables manufacturers to satisfy certain specifications, such as enhanced strength, improved corrosion resistance, or unique surface treatments.
- High-strength and durable parts: Custom forging improves the strength and longevity of steel products in comparison to typical manufacturing procedures. This makes it the ideal material for components subjected to high loads or extreme stress.
- Materials with high strength: Forging is particularly good for high-strength materials such as titanium alloys, stainless steels, tool steels, nickel-based alloys, aerospace alloys, and stainless steels.
- Environmentally friendly: Compared to other production processes, custom forging produces less waste and pollution. This makes it more environmentally friendly.
How To Work With Custom Steel Forging Experts
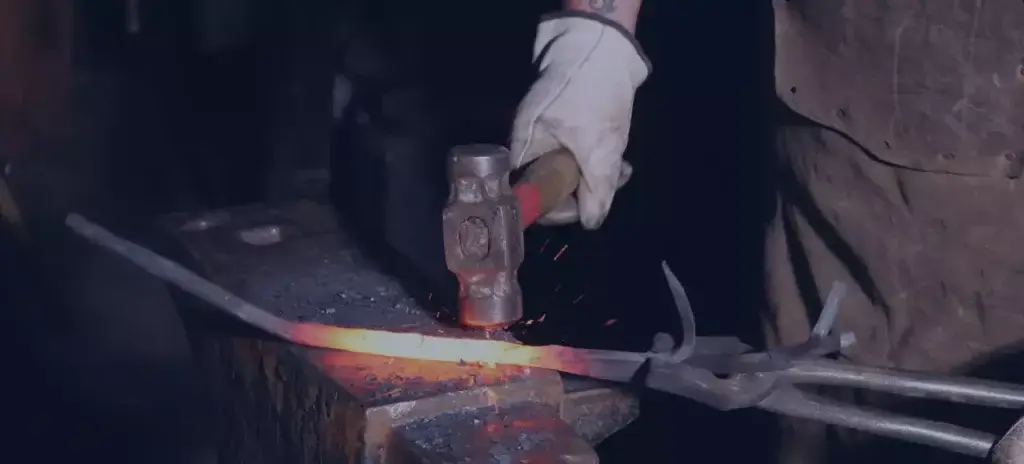
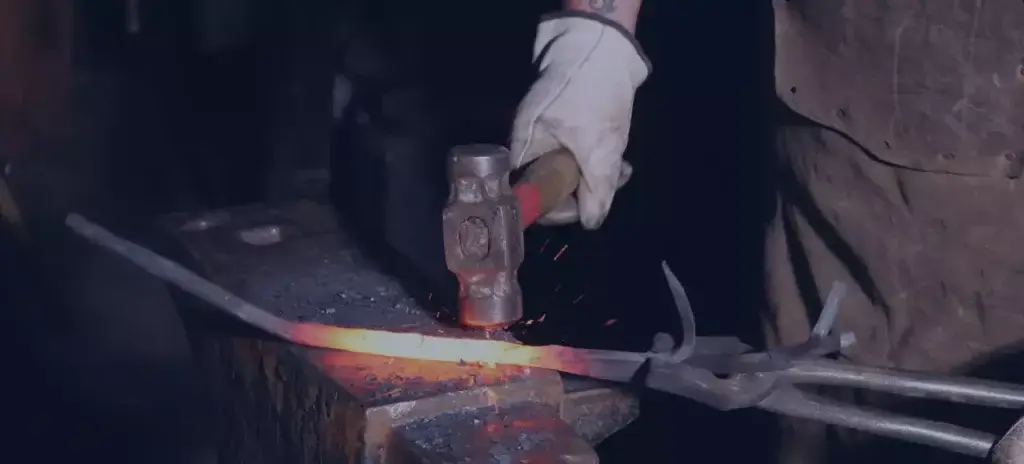
There are various steps to working with custom steel forging professionals:
- Define your needs: Clearly state your demands and criteria for the project, including the ultimate product’s ideal size, shape, strength, and material.
- Research potential suppliers: Evaluate potential custom steel forging providers’ capacities, backgrounds, and costs.
- Request quotes: To obtain the best price for your job, request quotes from several potential vendors and compare them.
- Review sample parts: Examine sample parts from prospective suppliers to gauge their caliber and ensure they satisfy your needs.
- Monitor the production process: Make sure the supplier follows their quality control methods and that you are satisfied with the final product by keeping an eye on the production process.
- Finalize the design: Work with the supplier to complete the product’s design, making any necessary alterations or enhancements.
- Perform final inspection: Check the product one last time to ensure it satisfies your needs and is free of flaws.
- Review the production schedule: To make sure the project will be finished on time, review the production schedule and delivery date with the supplier.
- Maintain a good relationship: Keep a positive relationship with the supplier to ensure that any upcoming projects go successfully.
- Discuss your project: To ensure the provider is aware of your needs and capable of offering the right solution, go over your project in depth with them.
Zetwerk is a manufacturer that specializes in providing end-to-end solutions for a broad spectrum of industrial manufacturing requirements, including forged steel projects. Zetwerk can assist clients in all phases of the custom steel forging process, from design and prototyping to production and delivery, thanks to a team of skilled engineers. Our proficiency in material selection, heat treatment, and precise machining enables us to manufacture each component to the highest standards. In addition, Zetwerk’s advanced quality control measures and project management tools ensure that the final product is delivered on time and meets the client’s exact specifications.




