The rise of custom metal forgings in modern manufacturing
In recent years, the utilization of custom metal forgings in modern manufacturing has increased significantly. This is due to a number of causes, including technological improvements, the growing need for high-quality and complex metal components, and the increasing need for manufacturing precision and efficiency.
The forging process shapes metal into specified designs and forms to create custom metal forgings. This procedure entails heating the metal at a high temperature and then pressing it into the required form. The metal is then cooled and consolidated, resulting in a robust and lasting component.
The increasing need for high-performance components in numerous industries, such as aerospace, defense, and transportation, is one of the key causes driving the growth of bespoke metal forgings. These sectors require components that can survive harsh environments and tremendous weights, and custom metal forgings are an ideal solution. They possess superior tensile and tensile strength, as well as a high level of precision and accuracy, making them suitable for these demanding applications.
The development of new and improved forging technologies also contributes to the increase in custom metal forgings. With the advent of computer-controlled forging technology, it is now possible to make elaborate and complex structures with greater precision and efficiency than ever before. This has allowed producers to construct previously impossible-to-manufacture components and opened up new possibilities for using custom metal forgings in many applications.
The adaptability of custom metal forgings has also contributed to their increased demand. They can be fabricated from various metals, such as steel, aluminum, and titanium, and apply to a vast array of applications, from structural components to sophisticated mechanical elements. The increase of custom metal forgings in modern production can be ascribed to a number of causes, including the increasing need for high-performance components, the development of new and improved forging processes, and the adaptability of these components. As a result, custom metal forgings are gaining popularity among manufacturers and engineers who want robust, accurate, and long-lasting components for their applications.
Custom Metal Forgings: The Key to High-Performance Engine Components
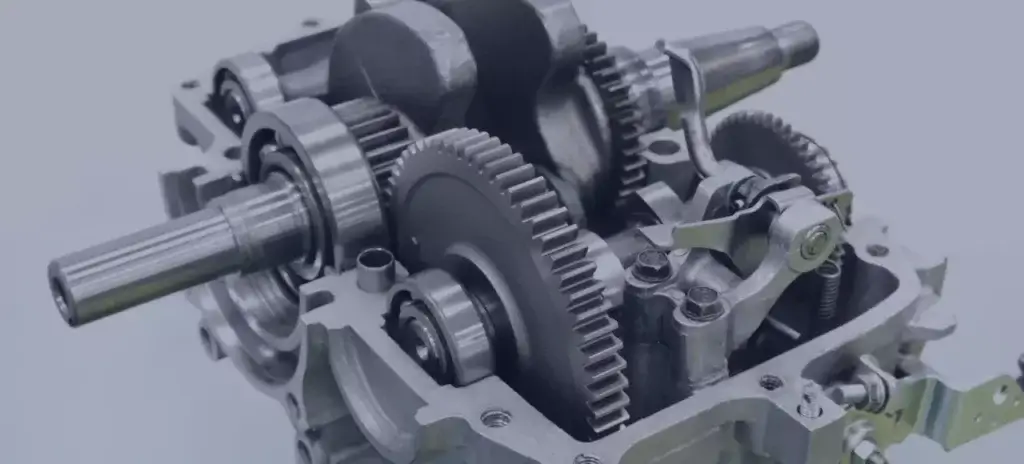
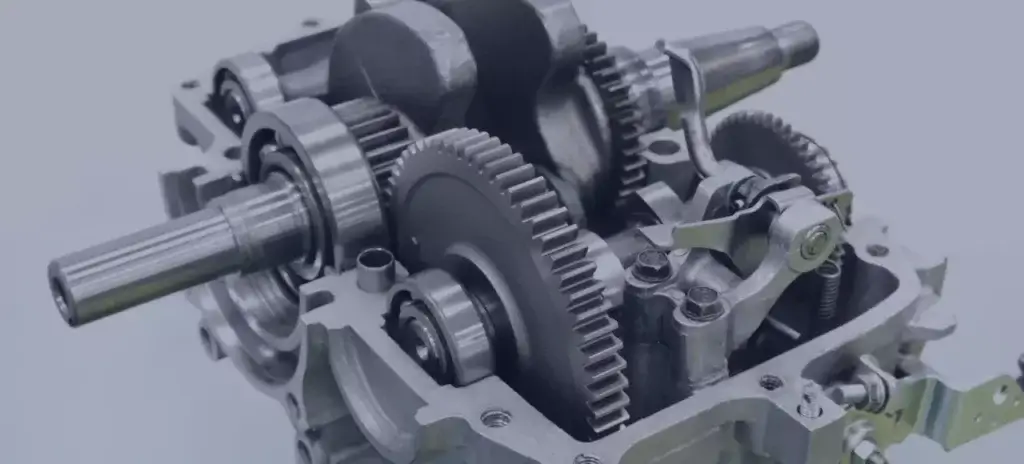
In recent years, the usage of bespoke metal forgings in the fabrication of high-performance automotive and aerospace components has grown in popularity. This is because custom metal forgings offer various advantages, such as strength, durability, precision, and uniformity. Crankshafts, connecting rods, and drive shafts, among other high-performance engine components, are frequently manufactured using custom metal forgings in the automotive industry. These forged components are subjected to high degrees of stress and must be robust and long-lasting in order to function properly. Custom metal forgings are ideally suited to meet these requirements due to their superior strength, longevity, precision, and accuracy.
Custom metal forgings manufacture vital components like landing gear, structural components, and engine parts in the aircraft sector. These components must survive harsh conditions, such as high stress and temperatures, and must be manufactured according to stringent standards. Custom metal forgings are appropriate for these applications because they can be manufactured to extremely tight tolerances and are exceptionally strong and durable.
Utilizing custom metal forgings to manufacture high-performance automotive and aerospace components is also cost-effective. The production of custom metal forgings eliminates the need for costly and time-consuming machining techniques. This leads to a more efficient and economical manufacturing process, which can significantly benefit manufacturers and suppliers in these industries.
Consistency is another advantage of using custom metal forgings in the production of high-performance automotive and aerospace components. Controlled and repeatable techniques are used to manufacture custom metal forgings, resulting in parts with consistently high quality and performance. This consistency is essential for the performance and safety of these components, and it helps to ensure that they function reliably in real-world settings.
Bespoke metal forgings in producing high-performance automotive and aerospace parts offer various advantages, such as strength, durability, precision, consistency, and cost-efficiency. These advantages make custom metal forgings an increasingly attractive option for manufacturers and engineers in the automotive and aerospace industries who require durable, precise, and dependable application components.
How Technology is Revolutionizing Custom Metal Forgings
In the coming years, technology and innovation will continue to play a significant role in determining the future of bespoke metal forgings. Technology advancements have enabled manufacturers to build unique metal forgings with higher precision and accuracy, resulting in more robust and resilient components. Utilizing computer-controlled forging equipment is one of the most significant technological advances in the bespoke metal forging sector. This technique permits producers to build elaborate and complex shapes with high precision and consistency. This has created new opportunities for using custom metal forgings in many applications and enabled producers to produce previously impossible-to-manufacture items.
Technology and innovation are also significantly impacting the creation of new and sophisticated alloys. These alloys have enabled manufacturers to make stronger, lighter, and more durable parts than ever before. This has the potential to revolutionize the usage of custom metal forgings in a vast array of applications, including automotive, aerospace, medical, and industrial.
The technology and innovation also contribute to automating the custom metal forging process. Utilizing robotics and automation has helped firms to boost production efficiency, cut costs, and maintain high levels of precision and quality. This has made custom metal forgings an increasingly attractive choice for producers seeking cost-effective and efficient production of high-performance components.
Technology and innovation will continue to shape the future of bespoke metal forgings. Manufacturers will be able to make custom metal forgings with higher efficiency, precision, and quality than ever before due to developments in computer-controlled forging equipment, the development of new alloys, and the growing automation of the forging process.
Zetwerk can produce high-quality forged metal components with precision and efficiency. Zetwerk’s expertise in metal forging enables it to cater to a wide range of industries, including aerospace & defense, automotive, and construction. Our dedication to quality and customer satisfaction ensures that each project is completed to the highest standard. Zetwerk’s custom metal forging capabilities include open-die forging, closed-die forging, and ring rolling. Our ability to create unique and complex shapes makes us a trusted partner for businesses seeking reliable and effective solutions for their metal forging needs.



