Aluminum Forging Capabilities
The production of aluminum components of high quality that will endure a long time can be accomplished through the process of aluminum forging. To complete the procedure, aluminum billets must first be heated to their respective melting points before being shaped into the required shapes under intense pressure. Compared to other techniques of producing aluminum, this one results in a single piece that has improved mechanical properties. These improvements include increased strength, reduced weight, and improved durability.
One of the key benefits of using bespoke aluminum forging is the capacity to construct sophisticated designs that are difficult or impossible to build using other processes. Because of this, it is a good choice for usage in various industries, including aircraft, for automobile parts, the defense, and power generation industries. A further advantage of aluminum forging is that it can be adapted to fulfill the exact requirements of any given project, ensuring that the result is optimal for the use to which it will be put.
Forging aluminum is a crucial advantage for several reasons, one of which is that it offers a cost-effective alternative for high-volume production cycles. Because of this method, no material is wasted, and the finished product needs minimal machining, which results in significant time and cost savings.
In addition, the finished product’s exceptional toughness and longevity make it an excellent selection for products that will be subjected to heavy use and stress, such as components for engines and structural components. This type of application is suitable for the material. Because it is adaptable and economical, custom aluminum forging is becoming an increasingly popular choice across many industries.
This is due to the fundamental fact that it can be used to manufacture high-quality aluminum components. It is an ideal material for applications that require both lightweight and robust parts due to its capacity to be manufactured into intricate shapes, enhanced mechanical capabilities, and sturdiness.
Forged Aluminum vs Other Metals
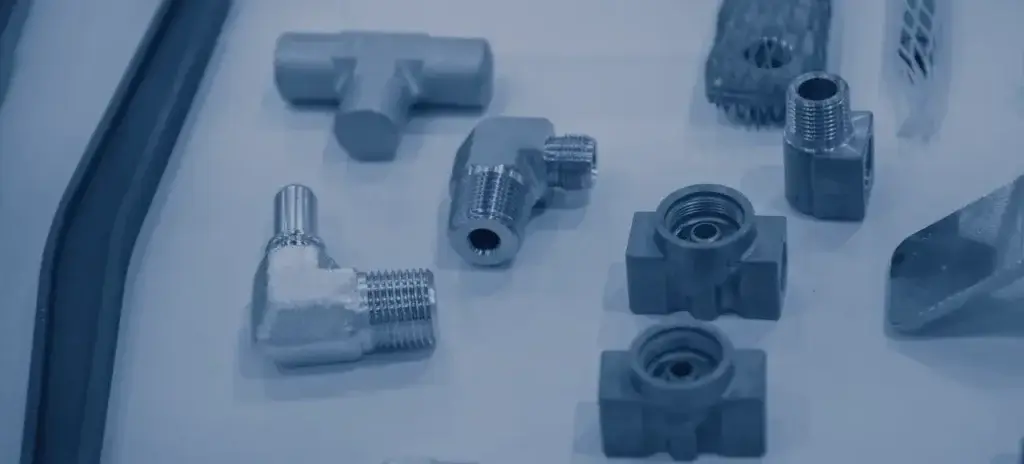
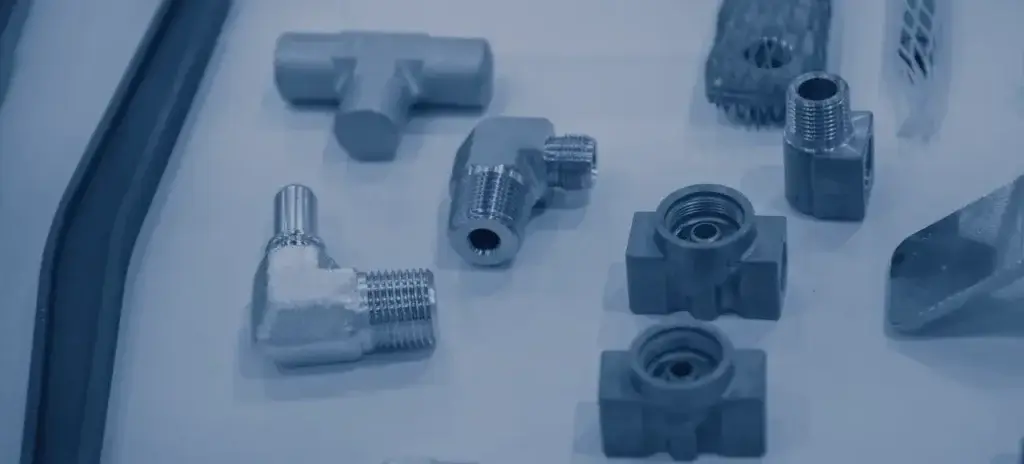
Aluminum that has been forged is the material of choice for a wide variety of industrial applications because of its exceptional mix of properties, including low weight, resistance to corrosion, conductivity, and the capacity to be recycled. However, other metals can be utilized; titanium and steel both have their benefits and might be used instead.
Forged aluminum is ideal for applications where compact, readily transported parts are necessary, such as in the aerospace and automotive industries. Because it is lighter than steel and titanium, forged aluminum is the lighter of the three. Aluminum can be utilized in the chemical and maritime industries. This is possible due to the metal’s excellent resistance to corrosion. Because of its high thermal and electrical conductivity, aluminum is an ideal material for use in various wiring and ventilation applications.
On the other hand, steel and titanium are well-known for having exceptional wear resistance and greater strength. They see widespread use in fields requiring extraordinary tensile power, such as the construction industry and the armed forces. However, they are significantly heavier than aluminum and have a poorer resistance to corrosion, which makes them unsuitable for specific applications because of their weight and resistance.
Because it decreases the amount of material waste and the amount of time required for machining, forged aluminum is a cost-effective material for high-volume production operations. Because it can be recycled easily, aluminum is an environmentally responsible material that can be put to a wide variety of uses. The decision between using forged aluminum or one of the other available metals will be based on the weight, strength, conductivity, and cost factors relevant to the application. Other materials, such as steel and titanium, are more suited for applications requiring high strength and resilience to wear and tear. However, forged aluminum is a lightweight alternative that is cost-effective, resistant to corrosion, and can be used in various applications.





Advantages of Using Aluminum in Forging
The advantages of using aluminum in forging are:
- Improved Strength: Forging, in contrast to the procedures used in the production of aluminum, improves the mechanical attributes of the final product, particularly its strength and durability.
- Lightweight: Aluminum is one of the lightweight metals on earth, making it an excellent choice for applications that call for lightweight components, such as those in the aerospace and automotive industries.
- Corrosion Resistance: Due to aluminum’s excellent corrosion resistance, it is suitable for use in harsh environments, such as those in the chemical and maritime sectors.
- Conductivity: Because of its high thermal and electrical conductivity levels, aluminum is an excellent material for use in applications involving the transport of electricity and heat.
- Complex Shapes: Forging makes it possible to create intricate designs that would be difficult to start using any other method. These intricate shapes would be challenging to construct.
- Cost-Effective: Forged aluminum is a solution that reduces the amount of material waste and the amount of machining that is required, making it a cost-effective choice for high-volume production runs.
- Recyclability: Aluminum is one of the most recyclable metals, making it a material of choice for many applications that are conscious of its environmental impact.
- Versatility: Aluminum forging offers versatility in that it may be adapted to fulfill the requirements of a particular project, so ensuring that the finished product is optimally suited for the function for which it was designed.
When making high-quality aluminum components, aluminum forging offers numerous benefits that can’t be overlooked. Aluminum forging is a suitable alternative for applications that require both strong and lightweight parts because of its ability to manufacture complicated shapes, high mechanical qualities, and adaptability.
Zetwerk is a manufacturer specializing in custom aluminum forging, which is the process of shaping and forming aluminum using high temperatures and pressure. We provide various forging services to fulfill the specific needs of our customers, including the design, prototype, and production of custom aluminum components for multiple industries.
Engineers and technicians with extensive experience at Zetwerk work closely with clients to guarantee that your aluminum forging demands are addressed efficiently and effectively. We use cutting-edge technology and machinery to manufacture aluminum components with tight tolerances and superior finishes. We also offer value-added services such as heat treatment, machining, and surface finishing to provide a comprehensive manufacturing solution for our clients. Overall, Zetwerk’s competence in custom aluminum forging assists our clients in achieving their production objectives and meeting your particular specifications.




