In the field of metalworking, cold forging is considered a remarkable technique that combines precision, strength and efficiency. Unlike hot forging, cold forging uses mechanical pressure and force at room temperature to shape and transform metals into complex parts. From automotive components to aerospace applications, the process has found wide application in various industries. In this blog post, we dive into the world of cold forging and explore its benefits, applications, and the factors that contribute to its success. Cold forging is a flexible and efficient manufacturing process that offers many advantages such as improved mechanical properties, dimensional accuracy, material conservation and the ability to manufacture complex parts. Its applications span a wide variety of industries, making it an important technique in modern metalworking.
Cold Forging Process
The cold forging process involves several steps that enable the shaping and forming of metal at room temperature. Here is an overview of the typical cold forging process:
- Material Selection: The process begins with the selection of a suitable metal for cold forging. Metals with good ductility, such as steel, aluminum, and copper alloys, are commonly used due to their ability to withstand deformation without cracking.
- Billet Preparation: The chosen metal is obtained in the form of a cylindrical billet. The billet is typically pre-cut to the desired length and diameter, based on the specifications of the final part.
- Lubrication: Lubrication is essential in cold forging to reduce friction between the metal and the forging tools. It allows for easier deformation of the metal and helps prevent excessive wear on the tools. Lubricants also aid in the removal of the forged part from the die after the process.
- Die Design: A die, consisting of two halves, is designed to match the desired shape of the final part. The die contains cavities and features that impart the desired shape, dimensions, and details to the metal during the forging process. The die is typically made from hardened steel to withstand the high pressures involved.
- Forging Operation: The lubricated billet is placed into the die cavity. A mechanical press exerts high pressure on the billet, causing it to deform and take the shape of the die. The pressure applied can range from several tons to several thousand tons, depending on the size and complexity of the part. The pressing force is typically applied in a gradual manner to ensure proper filling of the die cavity and to minimize defects.
- Finishing Operations: After the initial forging, additional operations may be performed to refine the shape and dimensions of the part. These operations can include trimming excess material, piercing holes, coining (creating embossed features), or other secondary forming processes. Finishing operations helps achieve the final desired shape and dimensional accuracy of the part.
- Heat Treatment (Optional): In some cases, cold-forged parts may undergo heat treatment processes, such as annealing or tempering, to enhance their mechanical properties and remove any residual stresses.
- Surface Treatment (Optional): Depending on the requirements and application of the part, surface treatments such as plating, coating, or painting may be applied to enhance corrosion resistance, aesthetics, or other functional properties.
- Inspection and Quality Control: The finished cold-forged parts undergo thorough inspection and quality control measures to ensure they meet the required specifications and standards. This may include dimensional checks, hardness testing, visual inspection, and other non-destructive or destructive testing methods.
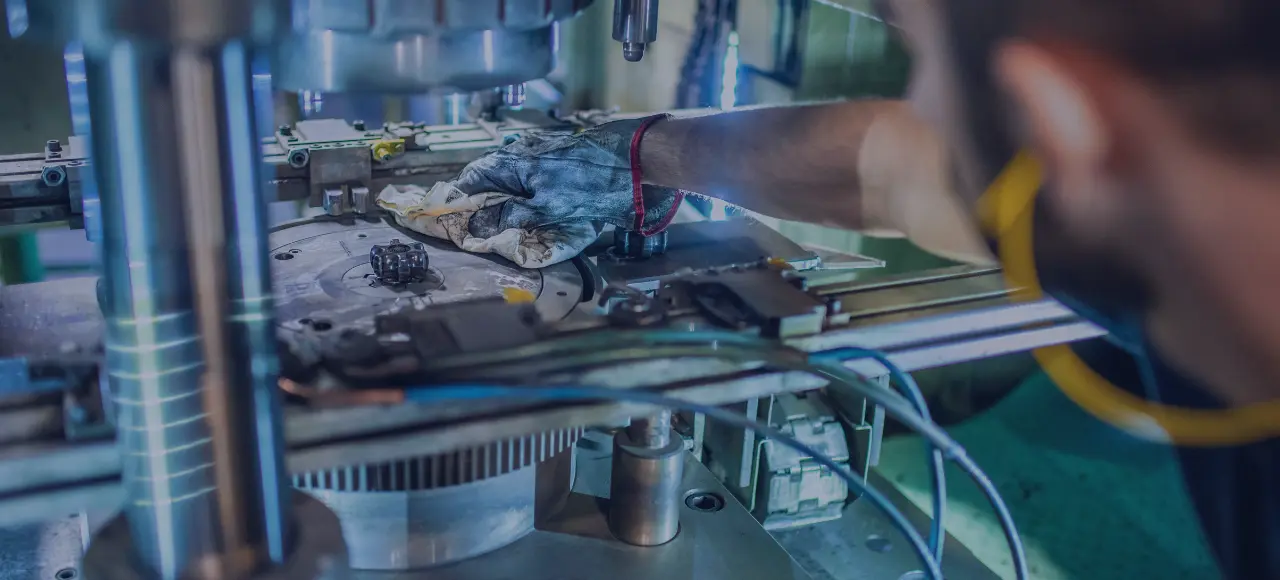
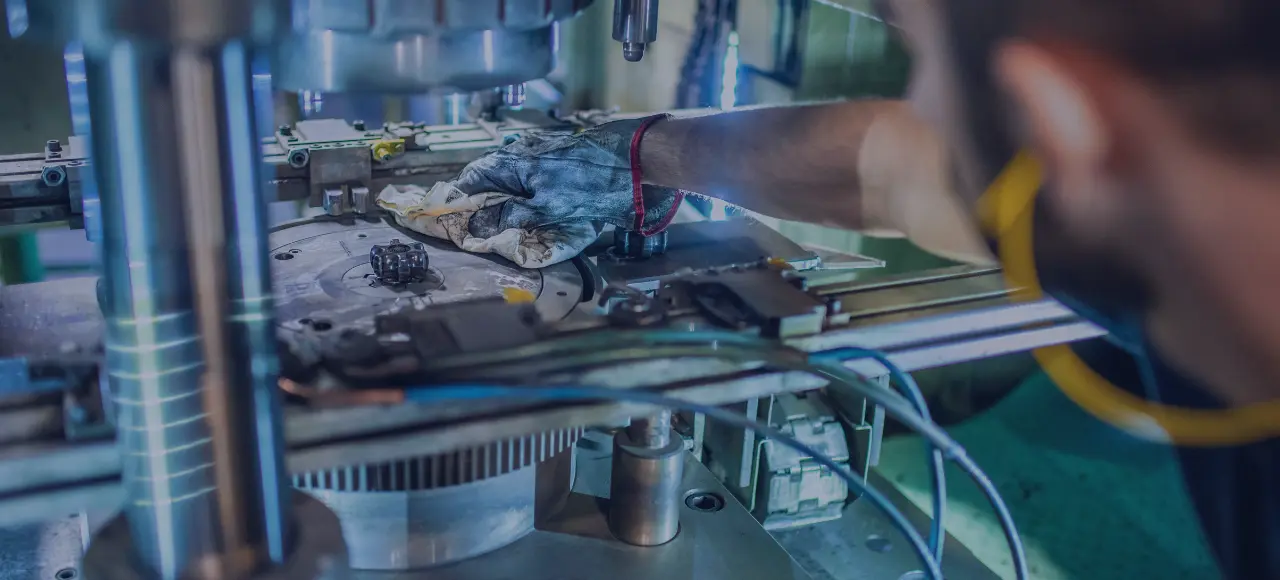
Advantages Of Cold Forging
- Enhanced Mechanical Properties: Cold forging results in parts with superior mechanical properties. The process refines the grain structure of the metal, leading to increased strength, toughness, and wear resistance. These properties make cold-forged components highly desirable for applications where reliability and durability are paramount.
- Dimensional Accuracy and Surface Finish: Cold forging facilitates the creation of intricate shapes and tight tolerances with exceptional precision. The absence of high temperatures prevents material distortion and allows for finer detailing. Additionally, the process yields excellent surface finishes, reducing the need for additional machining or polishing.
- Material Conservation: Cold forging minimizes material waste compared to hot forging. Without the need for elevated temperatures, there is no scale formation or oxidation, reducing material loss. This makes cold forging an environmentally friendly and cost- effective choice.
- Complex Part Production: The versatility of cold forging enables the creation of complex parts that are otherwise challenging to manufacture. The high pressure applied during cold forging allows for intricate geometries, including internal features, threads, and undercuts. This opens up new possibilities for designers and engineers, enabling innovative and efficient product designs.
Applications of Cold Forging
- Automotive Industry: Cold-forged components play a crucial role in the automotive sector. From engine and transmission parts, such as gears, shafts, and bearings, to suspension and steering system components, like tie rods and ball joints, cold forging delivers high-performance solutions. The strength and precision of cold-forged parts contribute to improved vehicle safety, fuel efficiency, and overall reliability.
- Aerospace and Defense: In the demanding aerospace and defense sectors, where reliability and weight reduction are paramount, cold forging finds extensive usage. Aircraft engine components, landing gear parts, fasteners, and missile components are just a few examples of applications that benefit from the exceptional strength and dimensional accuracy achieved through cold forging.
- Electronics and Electrical Industry: Cold forging is employed in the production of electrical connectors, terminals, and other intricate parts for the electronics industry. The precise shaping capabilities of cold forging ensure optimal electrical conductivity, mechanical stability, and long-term reliability.
- Construction and Infrastructure: Cold-forged anchor bolts, fasteners, and structural components find their place in construction and infrastructure projects. The high strength and dimensional accuracy provided by cold forging ensure structural integrity, durability, and ease of installation.
Cold forging has emerged as a vital process in the world of metalworking, offering a unique set of advantages that cater to the demands of various industries. With its ability to produce high-strength, precision-engineered components at room temperature, cold forging has revolutionized the manufacturing landscape. From automotive and aerospace to electronics and construction, the applications of cold forging are diverse and far-reaching. As technology and innovation continue to advance, cold forging is poised to play an even more significant role in shaping the future of manufacturing.




FAQS
Cold forging involves shaping metal or alloy materials at room temperature or slightly below, while hot forging involves heating the material to high temperatures before shaping it.
Cold forging finds applications in various industries such as automotive, aerospace, construction, electrical and electronics, medical devices, and consumer goods.
Cold-forged components include gears, shafts, engine parts, fasteners, landing gear, structural components, bolts, screws, connectors, terminals, heat sinks, surgical instruments, implants, orthopedic components, locks, hinges, and hand tools.
Cold forging is commonly performed on metals with good ductility, such as steel, aluminum, copper, and their alloys, which can undergo plastic deformation without fracturing.