The impact of Automation and technology on closed die forging companies
Automation and technology have considerably impacted closed die forging operations in recent years. The metal-forming technique of closed die forging includes molding metal components by applying pressure to the material between two or more dies. The application of automation and technology in closed die forging has significantly enhanced productivity, precision, and quality assurance.
Enhanced efficiency is one of the primary benefits of automation in closed die forging. Automated forging systems can run 24 hours a day, seven days a week, decreasing downtime and enabling improved production rates. This has enabled businesses to address the rising need for customized and high-precision components in the aerospace, automotive, and energy industries. Automated systems eliminate the need for manual labor, hence lowering the likelihood of workplace accidents and enhancing overall safety.
Improved precision is another advantage of automation and technology in closed die forging. Automated systems can perform exact procedures with consistent repeatability, lowering the possibility of human error. This improves product quality and consistency, which is particularly crucial for businesses that demand precision custom components. Automated systems also provide real-time monitoring and control of the forging process, enabling adjustments to be made immediately if necessary.
Automation and technology have had a positive effect on quality control in closed die forging operations, in addition to enhancing productivity and precision. During the forging process, automated systems can perform quality control inspections, lowering the possibility of flaws and ensuring that the final products satisfy industry requirements. This helps organizations maintain their reputation for producing high-quality products and assures customers that the components they purchase will fulfill their specifications.
The influence of technology and automation on closed die forging enterprises has been overwhelmingly good. Automated systems have enabled businesses to increase productivity, precision, and quality control while decreasing downtime, labor expenses, and workplace hazards. As technology continues to evolve, we may see additional advances in closed die forging, resulting in even more significant advantages for businesses and customers.
The Benefits of closed die forging over other metal forming techniques
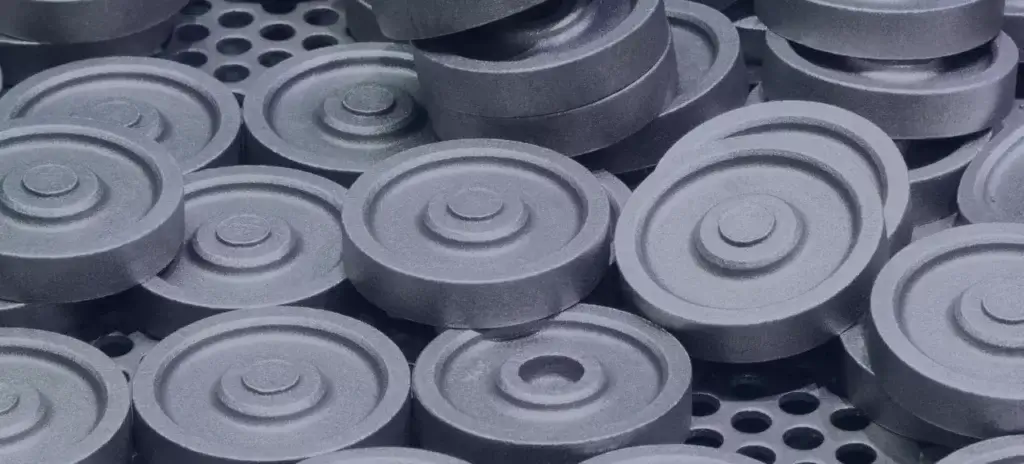
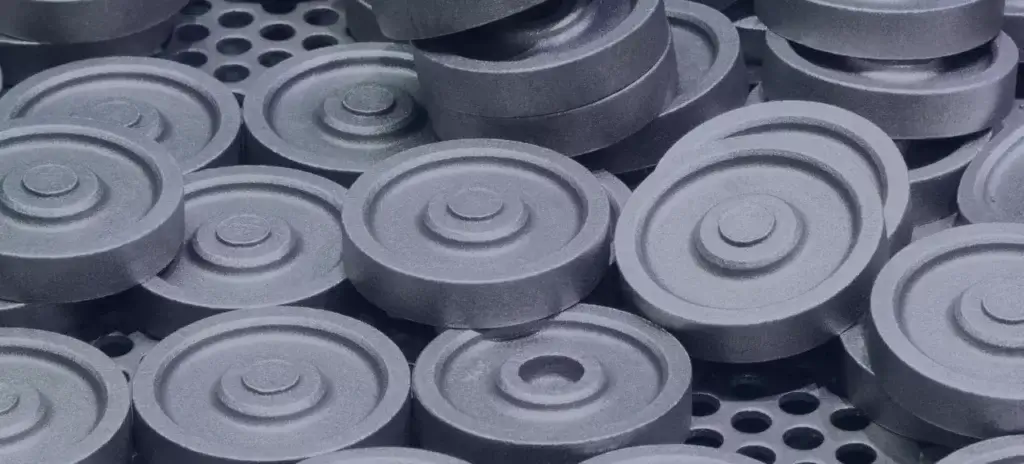
Closed-die forging is a metal-forming technique with various advantages over other metal-forming methods. In closed die forging, metal components are shaped by exerting pressure between two or more dies. This method is utilized to manufacture high-precision components for the aerospace, automotive, and energy industries.
One of the primary advantages of closed die forging is the ability to construct complex, precise shapes. In contrast to other methods of metal forming, closed die forging may manufacture components with complicated geometries, tight tolerances, and accurate measurements. This makes it excellent for creating parts with tight tolerances and high precision, such as automotive and aerospace components.
Another advantage of closed die forging is its longevity and strength. Closed die forging creates stronger and more durable components than other metal forming processes. This is because the process involves subjecting the material to high pressure, which results in a denser, more uniform structure. This makes the components produced by closed die forging more resistant to wear, fatigue, and corrosion, giving customers confidence that their parts will match their specifications.
Additionally, closed die forging is more efficient than other metal forming processes. This method can produce high-precision components faster than conventional metal-forming procedures, hence decreasing downtime and increasing productivity. This makes it perfect for sectors requiring high-volume specialized component production.
In addition to its durability, accuracy, and efficiency, closed die forging is a cost-effective metal-forming technique. This method utilizes less raw material than conventional metal-forming processes, hence reducing material costs. In addition to eliminating the requirement for secondary functions, the approach reduces production costs and lead times.
Finally, closed die forging is an eco-friendly metal-forming technique. The procedure generates less waste than conventional metal-forming techniques, lowering the production’s environmental effect. This makes it excellent for industries that want to reduce their environmental footprint without sacrificing component quality.
The advantages of closed die forging over alternative methods of metal formation are evident. The process offers excellent precision, strength, durability, efficiency, cost-effectiveness, and environmental friendliness, making it the ideal option for sectors that require components with high accuracy. As technology thrives on evolving, we will see additional advances in closed die forging, resulting in even more considerable advantages for businesses and customers.





Benefits of Closed Die Forging Parts for your project
Closed die forging is a metal forming method that offers several benefits for projects that require high precision components. The process involves shaping metal parts by applying pressure to the material between two or more dies. This results in strong, durable, and precise components, making it unique for a wide range of applications.
One of the critical benefits of closed die forging is the ability to produce high precision parts. The process allows for tight tolerances and precise dimensions, making it ideal for projects that require intricate shapes and tight tolerances. The method also eliminates the need for secondary operations, reducing lead times and ensuring that components are delivered on time.
Another benefit of closed die forging is its strength and durability. The process involves applying high pressure to the material, which results in a denser, more homogeneous structure. This makes the components produced through closed die forging more resistant to wear, fatigue, and corrosion, assuring customers that their parts will meet their requirements.
Closed die forging is also more efficient than other metal forming techniques. The process can produce high precision components faster than other metal forming techniques, reducing downtime and increasing productivity. This makes it ideal for projects that require high volume production of custom made components.
In addition to its strength, precision, and efficiency, the closed die forging process requires less raw material than other metal forming techniques, reducing material costs. The process also eliminates the need for secondary operations, reducing production costs and lead times. Closed die forging is an environmentally friendly method of metal forming. The process produces less waste than other metal forming techniques, reducing the environmental impact of production. This makes it ideal for projects looking to reduce their ecological footprint while still producing high quality components.
Closed Die Forging is one of the industrial techniques in which Zetwerk’s team of skilled specialists specializes. We ensure that the project’s specifications and quality standards are met. Our systems for quality control ensure that the forgings are rigorously tested and conform to industry requirements. In addition, Zetwerk’s digital platform makes communication and project status easily available, ensuring that the project is carried out smoothly and efficiently. Overall, Zetwerk Closed Die Forgings company possessed manufacturing skills and knowledge can assist you in efficiently producing superior quality.




