The Production Process of Brass Forging and its Capabilities
Forging brass is a metal-forming process that includes molding brass into complex forms and patterns using high pressure. Beginning with the selection of raw materials, the production process for brass forging consists of heating, forging, and finally finishing. Brass billets or bars are used as the raw material when producing brass forgings. Brass billets are heated to a high temperature to make them pliable, then placed in a forging press where they undergo repeated hammering, punching, or rolling to achieve the desired shape. After the metal has been cooled, it is tested for quality and uniformity.
One of the primary advantages of brass forging is the ability to create intricate shapes and patterns that would be impossible to achieve with other metal forming techniques. The technique of high-pressure forging develops a dense and consistent grain structure in the metal, resulting in robust and lasting components. In addition, the method permits fine control over grain orientation, which can increase the metal’s mechanical characteristics and corrosion resistance. Brass forging manufacturers have the ability to produce a vast array of goods, ranging from minor components and fittings to significant industrial parts. Additionally, they can offer customization possibilities, allowing customers to design their own items to match particular demands and specifications.
Quality control is an essential component of the brass forging process, and manufacturers implement stringent quality control methods to guarantee that their products satisfy industry standards and client expectations. This comprises routine raw materials inspections, checks during production, and final inspections before shipping. Brass forging is a versatile and efficient metal-forming method that offers a number of benefits, including the capacity to manufacture intricate shapes and designs, robust and long-lasting components, and high-quality products. Brass forging manufacturers are beneficial partners for companies needing high-quality brass components because they can produce various products and offer customization choices.
Pricing and Cost Competitiveness of Brass Forging Components
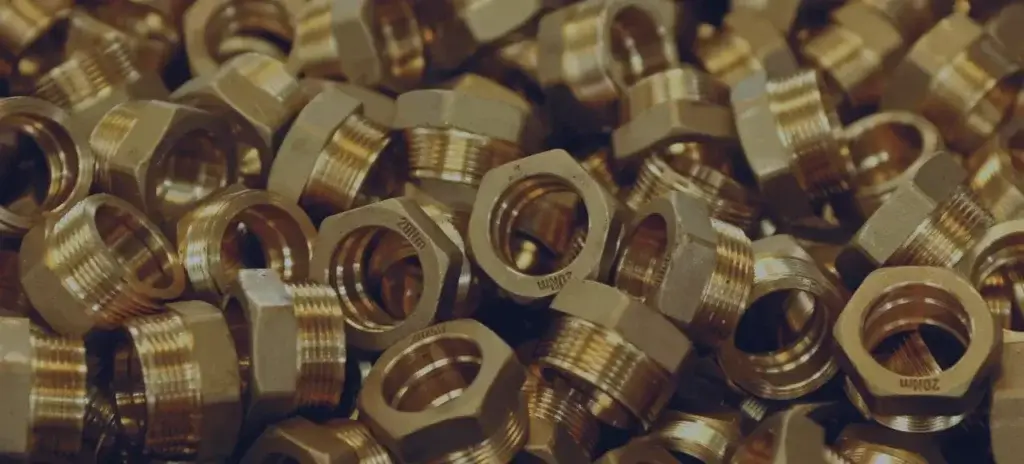
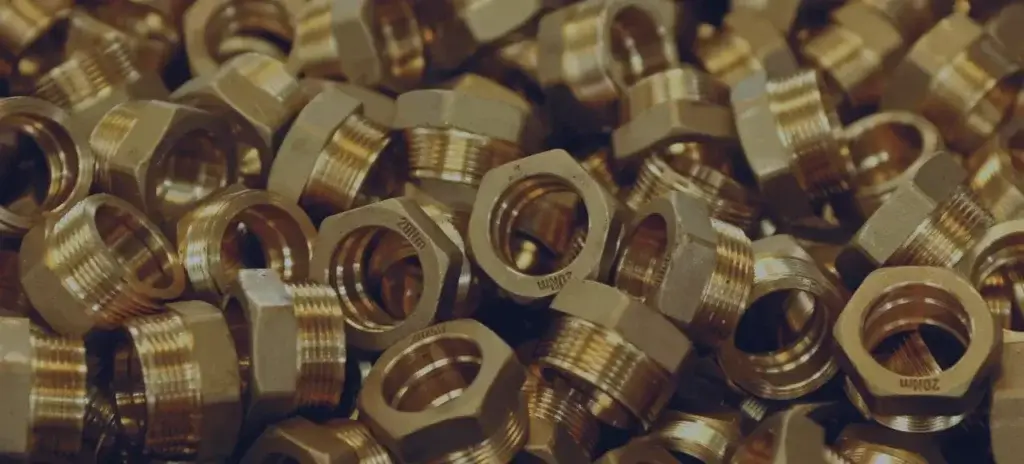
Pricing and cost competitiveness is crucial to the success of any firm, particularly in the brass forging industry. Due to intensifying worldwide competition, brass forging manufacturers are under enormous pressure to sell their goods at competitive pricing. Cost competitiveness can be accomplished in several ways, including reducing production costs, enhancing efficiency, and expanding automation in the manufacturing process.
Manufacturers of brass forgings can reduce costs by purchasing raw materials at the most competitive pricing. Market demand, production expenses, and geopolitical events can affect raw materials prices, and producers must keep a constant eye on these variables to reduce costs. Moreover, enterprises can reduce production costs by enhancing their production methods and boosting efficiency. This can be accomplished by utilizing modern equipment and technologies and adhering to lean manufacturing principles.
The degree to which the production process is automated is another aspect that influences cost competitiveness. Automation may boost productivity, decrease waste, and improve product quality consistency, resulting in lower costs and more competitive prices. However, the use of automation might incur initial expenses, and manufacturers must evaluate the return on investment before modifying their production processes.
Pricing and cost competitiveness of brass forged components are crucial success elements in the current industry. Manufacturers of brass forgings must strike a balance between giving competitive prices and retaining profitability. This can be accomplished by reducing manufacturing costs, boosting efficiency, and increasing the use of automation, among other strategies. By keeping these considerations in mind, makers of brass forgings can remain competitive and flourish in the current market.





Industrial Application of Brass Forging
- Electronics and electrical: In the electronics and electrical sectors, brass forgings are utilized for applications such as connectors, terminals, and electrical components.
- Medical equipment: In medical equipment, including surgical tools, orthopedic implants, and dental equipment, brass forgings are utilized.
- Building and construction: Brass forgings are extensively used in plumbing and heating systems and door and window hardware in the building industry.
- Aerospace and defense: In the aerospace and defense industries, brass forgings are utilized for applications such as hydraulic and pneumatic systems and structural components.
- Energy and power generation: Brass forgings are utilized in energy and power generation, including components for power plants, transformers, and switchgear.
- Marine and offshore: Brass forgings are utilized in marine and offshore applications, including ship components, oil platform components, and other offshore constructions.
- Industrial equipment: Forgings of brass are utilized in a variety of industrial equipment, such as pumps, valves, and pressure vessels.
- Sports and recreation: Forgings of brass are utilized in sports and recreation equipment, such as fishing reels, golf clubs, and musical instruments.
- Automotive and transportation: Components forged from brass are utilized extensively in the automotive and transportation industries, including engine components, hydraulic connections, and gear components.
- Heavy machinery: Brass forgings are utilized in heavy machinery, including construction equipment, agricultural machinery, and mining equipment.
Zetwerk is a global manufacturer that provides high-quality brass forging solutions. With our superior technology and knowledge of the industry, Zetwerk is able to efficiently produce precision forging components made of brass that conform to the needed specifications and standards. We use a variety of forging techniques, including hot forging, cold forging, and warm forging, to make brass products that meet our customers’ specifications. In addition, we use cutting-edge machinery and tools to ensure precision and accuracy throughout the manufacturing process. The dedication of Zetwerk to quality, innovation, and client satisfaction make it a credible partner for organizations seeking dependable and efficient brass forging solutions.




