Forging: Key to Strong and Lightweight Automotive Parts
The automotive parts forging is constantly evolving, emphasizing manufacturing lighter and more durable vehicles to match consumers’ shifting demands. Forging, which has become an integral element of the automobile production process, is one of the effective procedures utilized to attain this objective. This article will examine the increasing demand for lightweight and high-strength automotive components manufactured through forging and how this trend is influencing the industry’s future.
The forging process produces a more robust metal suitable for usage in the automotive sector. In the automotive industry, forging is used to make a variety of components, including engine components, transmission components, and suspension components, among others. Due to the importance of these components to the performance and safety of cars, they must be as strong and durable as possible.
The desire for lightweight and high-strength automobile parts has increased the industry’s use of forging. One of the primary benefits of forging is that it permits the manufacturing of lightweight and durable components. This is made possible via a technique known as near-net shaping, which enables the production of parts optimized for strength and weight. In addition to its strength and lightweight, forging offers the automotive sector many other advantages.
Forging, for instance, is a highly efficient process with a low waste rate and minimal production downtime. It also permits the development of sophisticated shapes and designs, making it perfect for high-performance manufacturing components. As the demand for lightweight and high-strength automotive components continues to rise, it is evident that forging will play an ever-increasing role in the industry. Advanced forging technologies, like 3D printing and computer-aided design (CAD), enable the creation of progressively more complicated and precise parts, hence accelerating the industry’s growth.
In addition, the increasing popularity of eco-friendly and sustainable automobiles contributes to the demand for lightweight and durable components. The use of lighter materials, such as aluminum and magnesium, reduces the overall weight of cars, resulting in enhanced fuel economy and fewer emissions. Forging is a significant enabler of this trend, as it enables the manufacture of lightweight and sturdy components, making it an indispensable tool in the development of environmentally friendly cars.
The demand for lightweight and high-strength automotive components is driving the expansion of the forging industry, making it an indispensable component in the creation of the next generation of automobiles. Along with the trend towards eco-friendly and sustainable automobiles, modern forging & alloying industries will continue to fuel the need for forging in the automotive sector for many years. Forging will play an increasingly crucial role in determining the future of the automobile industry due to its numerous advantages and rising popularity.
Quality Control & Industry Standards: The Cornerstone of Successful Automotive Forging
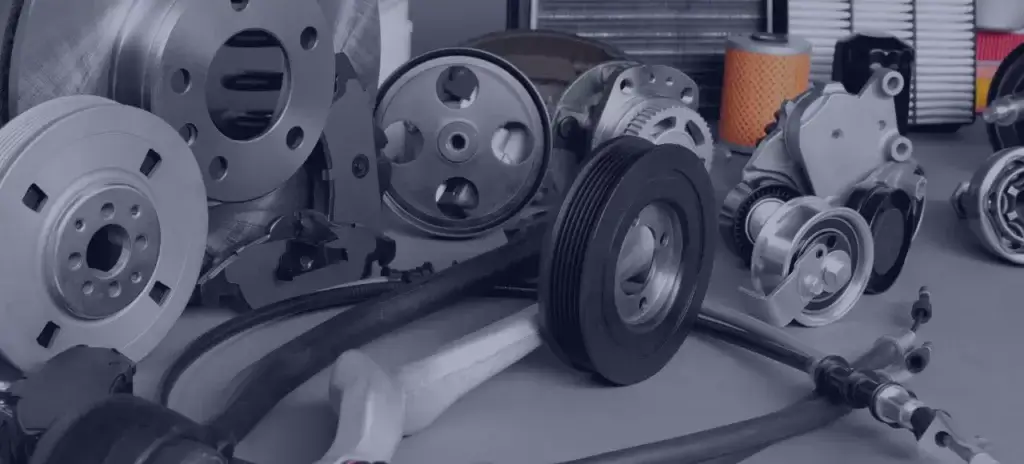
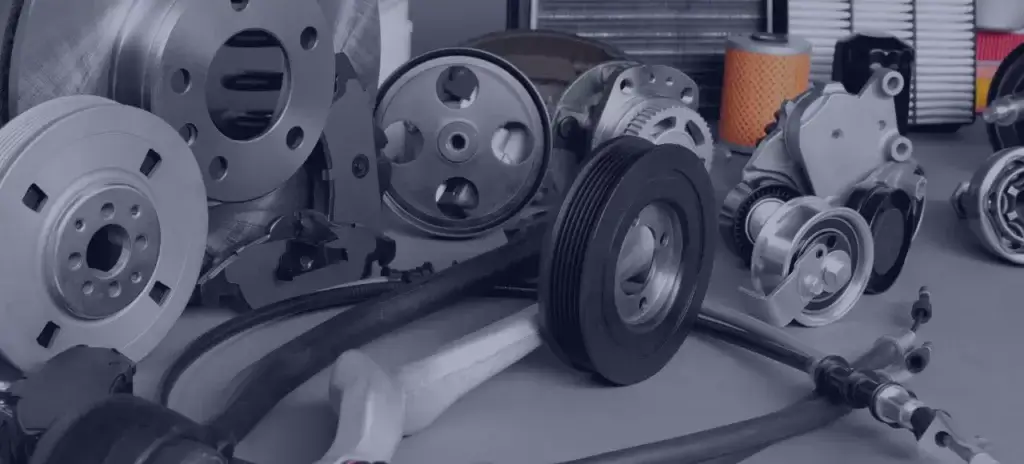
The automotive business is a highly competitive field, and manufacturers always seek to enhance their goods’ quality and performance. Forging is an essential manufacturing process that plays a crucial role in the production of top quality automotive parts. However, the fabrication of high-quality automobile components involves more than simply forging; it also requires a dedication to quality control and industry standards.
The Importance of Quality Control in Automotive Forging Quality control is an essential feature of the forging process, requiring the application of a variety of methods to ensure that parts are manufactured to the highest possible standards. This includes utilizing cutting-edge technology and equipment and stringent testing and inspection methods. By providing that quality control procedures are in place, manufacturers can ensure that every manufactured component fulfills the specified specifications and is of the highest quality.
A fundamental advantage of a robust quality control program is that it aids in the prevention of defects and failures in automobile parts. Defects can lead to costly repairs and even safety issues; thus, they must be recognized and rectified prior to vehicle usage. Quality control also ensures that components are constant in strength and longevity, giving producers and consumers peace of mind.
The Importance of Sector Standards in Automotive Forging Industry standards is vital in the automotive forging industry since they provide producers with consistent norms and specifications for producing high-quality parts. These standards are produced by industry organizations and are intended to ensure that all manufacturers produce parts with a consistent degree of quality. One of the primary advantages of industry standards is that they facilitate the interchangeability and versatility of vehicle parts. This is crucial for the automobile sector because it enables greater flexibility and decreases the time and expense associated with locating replacement parts.
Industry standards also ensure that components are compatible with one another, lowering the likelihood of failure and enhancing the vehicle’s overall performance. Quality control and industry standards are crucial to manufacturing high-quality automobile components. By using stringent quality control procedures and adhering to industry standards, manufacturers can ensure that every manufactured part fulfills the specified specifications and is of superior quality. This is a vital component of the forging process since it improves car safety, performance, and dependability.





Reducing Emissions, Improving Efficiency: Forging’s Role in Sustainable Automotive Production
The automobile industry is transitioning to manufacturing environmentally friendly and sustainable vehicles. The manufacture of these vehicles relies heavily on forging in this endeavor. Forging is a manufacturing process that creates durable and robust products while reducing waste and energy usage. This makes it an excellent technology for manufacturing eco-friendly and sustainable automotive components. Forging also involves the use of lightweight, high-strength materials, such as aluminum and magnesium, that are stronger than traditional materials and help reduce the vehicle’s overall weight.
This weight reduction improves fuel economy and reduces emissions, making it a crucial component in the manufacture of environmentally friendly automobiles. In addition, the use of advanced technology and automation in the forging process enables the efficient manufacture of high-quality parts while limiting the need for manual work and the possibility of human error. This not only adds to the sustainable production of automobiles but also improves the manufacturing process’s overall efficiency and output. The contribution of forging to the creation of eco-friendly and sustainable automobiles demonstrates the significance of this production method in the automotive sector.
Zetwerk specializes in creating custom forged parts that meet the unique needs of individual industries. Whether a small-scale project or a large-scale production run, we have the expertise to deliver top-quality products on time. Our focus on innovation and customer satisfaction has made us a trusted partner for various industries, including automotive, aerospace, and defense. Zetwerk’s commitment to quality and attention to detail ensures that every forged part we produce is durable, reliable, and ideally suited to the needs of our customers.




