Aluminum Alloys and their Applications in Forging Technology
Aluminum alloys are utilized extensively in the forging industry because they combine strength, durability, and low weight. There are numerous varieties of aluminum alloys, each of which has distinct qualities that make it useful for a variety of uses. Several parameters, including strength requirements, thermal characteristics, and corrosion resistance, influence the selection of aluminum alloy for a specific forging application.
6061 aluminum is the most frequently utilized aluminum alloy by aluminum forging manufacturers due to its excellent mix of strength and formability. This alloy is frequently employed in the production of structural components, such as frames and suspension components, as well as parts for the aerospace and defense industries. Its great strength and hardness make it excellent for use in high-stress applications, including as aircraft components and high-performance sports equipment.
In recent years, the increasing demand for creating novel aluminum alloys with enhanced qualities, such as higher strength, thermal resistance, and corrosion resistance. These alloys are being developed using sophisticated metallurgical processes, such as powder metallurgy and solid-state processing. They are anticipated to play a more significant role in the forging industry in the near future.
Using these new aluminum alloys in forging technology enables producers to build lighter, stronger, and more durable components. This is especially significant in forging car parts and aerospace hardware, where reducing weight and enhancing performance are crucial aspects. In addition, the use of new aluminum alloys in forging enables producers to produce components with enhanced surface finishes, which can improve the appearance of completed goods.
The Future Outlook for Aluminum Forging in the Automotive Sector
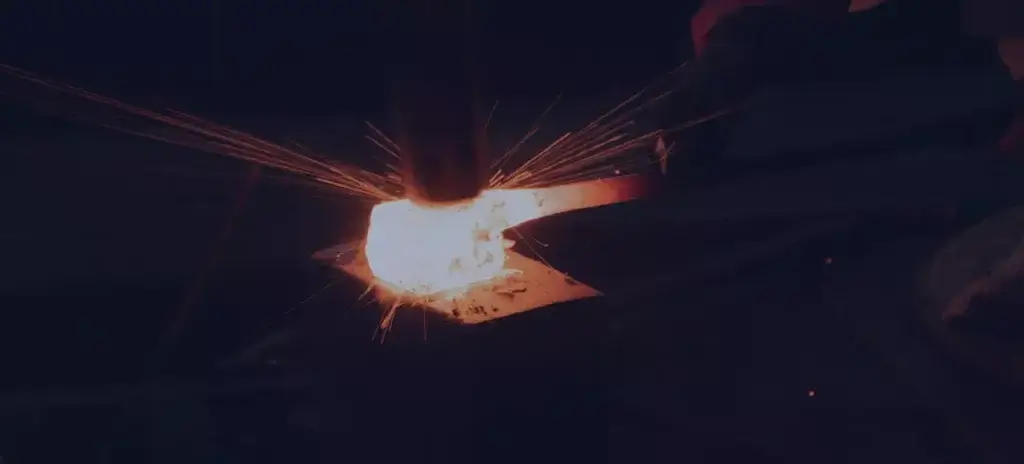
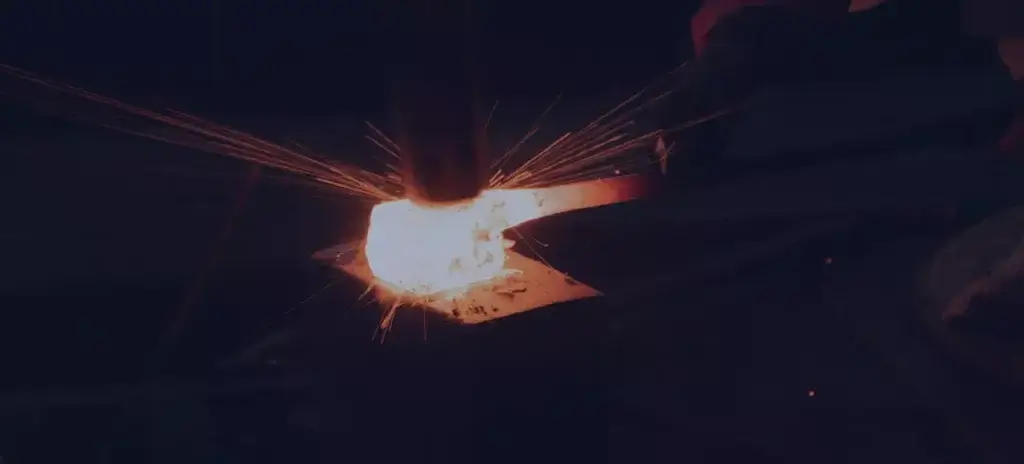
The capacity of aluminum forging to impart strength, durability, and lightness to the components used in automobiles has made it a crucial component of the automotive industry. Aluminum’s use in the automobile industry has expanded considerably in recent years, as automakers have sought to lower the weight of vehicles to boost fuel efficiency and decrease emissions. Aluminum’s broad acceptance in the automobile industry has resulted in a growth in demand for aluminum forging producers, who are well-equipped to meet this demand due to their superior forging capabilities.
In the vehicle sector, aluminum forging has numerous applications, including engine components, suspension systems, and structural pieces. Aluminum engine components are lighter, more durable, and offer superior heat dissipation than those constructed from other materials. This improves the engine’s overall performance and reduces fuel consumption. Similarly, aluminum suspension systems increase the vehicle’s handling and stability while reducing weight. Aluminum structural components are also lighter and more robust than those created from other materials, enhancing driver and passenger safety and performance.
As the need for fuel-efficient and environmentally friendly automobiles develops, it is anticipated that the use of aluminum forging in the automobile sector will continue to rise. Developing new aluminum alloys with enhanced strength and endurance is also expected to contribute to industry expansion. In addition, production technology and automation advances will enable aluminum forging producers to make components more effectively, thereby cutting costs and enhancing product quality.
However, expanding the automotive industry’s aluminum forging sector is challenging. It is anticipated that the high cost of raw materials will continue to rise in the coming years, posing a significant obstacle for manufacturers of aluminum forgings. This is expected to have a negative impact on the profitability of aluminum forging firms and may restrict their capacity to invest in new technologies and infrastructure. Moreover, competition from other materials, such as composites, is anticipated to be a future obstacle for the aluminum forging sector.
In the coming years, the demand for fuel-efficient and environmentally friendly automobiles is projected to continue to drive the growth of aluminum forging in the automobile sector. The creation of new aluminum alloys and technological advances in manufacturing will fuel the expansion of the aluminum forging sector. To remain competitive in the market, businesses must overcome obstacles such as growing raw material costs and competition from alternative resources.





Initiatives and Practices of Modern Aluminum Forging Manufacturers
In recent years, manufacturers of contemporary aluminum forgings have made substantial gains in incorporating sustainability strategies and procedures. These initiatives have been motivated by a rising awareness of the environmental impact of manufacturing and a desire to cut costs and increase market competitiveness.
Energy efficiency is one of the primary sustainability projects on which many aluminum forging producers concentrate. This involves deploying energy-efficient production processes, such as high-efficiency heating and cooling systems, and using renewable energy sources, like wind and solar energy. By decreasing their energy consumption, aluminum forging producers can reduce their carbon footprint and environmental impact.
Utilizing recycled materials is another critical endeavor explored by several aluminum forging makers. Using recycled aluminum in the forging process not only contributes to the reduction of waste but also reduces the demand for virgin aluminum, which consumes significant energy. This, in turn, reduces the carbon footprint of the manufacturing process and enhances the industry’s overall sustainability.
In addition to these measures, several aluminum forging manufacturers are also employing best practices to reduce waste and increase efficiency in their production processes. This includes implementing just-in-time inventory systems and utilizing computer-aided design (CAD) and computer-aided manufacturing (CAM) systems. Aluminum forging manufacturers can cut costs and increase market competitiveness by eliminating waste and increasing efficiency.
Lastly, numerous aluminum forging producers are investing in R&D to increase the sustainability of their manufacturing methods. This includes the development of new aluminum alloys with enhanced characteristics and innovative manufacturing processes that decrease waste and improve energy efficiency.
By investing in R&D, aluminum forging manufacturers may remain at the forefront of their industry’s sustainability initiatives. Contemporary aluminum forging manufacturers are attempting to embrace sustainability programs and practices. These initiatives, which include a focus on energy efficiency, using recycled materials, implementing best practices, and R&D investments, are assisting the industry in reducing its carbon footprint and enhancing its market competitiveness.
Zetwerk is a global manufacturer that can assist with an Aluminum Forging project by offering access to a wide variety of knowledgeable and dependable manufacturing specialists who specialize in Aluminum Forging. The digital platform provided by Zetwerk enables the project to efficiently and transparently manage the whole supply chain, from raw materials procurement to the shipment of finished goods. The team of professionals at Zetwerk can also provide technical direction and support to ensure the project’s success. Overall, the Zetwerk platform and resources can expedite the Aluminum Forging manufacturing process, resulting in higher quality, faster delivery, and cost savings.




