Zinc die casting involves molten zinc alloys being injected into a prepared die casting mold. Zinc alloys are very helpful in producing parts because of their ductility, impact resistance, and low melting point. Furthermore, casting occurs at lower temperatures because the material has a low melting point. Thus, the “hot chamber die casting process” was coined. Additionally, using the hot chamber method also extends the life of the die, reduces the frequency of retooling, and reduces costs in comparison to conventional die casting materials.
The high-pressure zinc die casting process is performed on automatic equipment designed to withstand high pressure. The liquid metal is forced into a two-part steel die with one or more cavities; each cavity is an exact inverse copy of the components. The mechanical properties of pressure zinc die casting are typically superior to those of conventional casting processes due to the rapid cooling and solidification that occurs when the liquid metal contacts the cooler steel side. Zinc can be cast using both hot chamber and cold chamber die casting process.
Zinc Hot Chamber Die Casting Process
For zinc hot chamber die casting, a hot chamber machine’s injection tool is submerged in a molten zinc bath within a metal holding furnace. This process is necessary for casting the zinc. The plunger will be pulled out once the metal inside the chamber has fully solidified. The die opens, and the casting falls out. Metal feeding mechanisms known as goosenecks are utilized to join the furnace to the processing equipment. There are up to six shot outputs per minute possible with zinc hot chamber die casting methods.
Zinc Cold Chamber Die Casting Process
The Cold chamber die casting process is almost similar to the hot chamber process. Instead of pumping molten metal into the machine, as is done in hot chamber die casting, molten metal is ladled from the furnace and poured via a pouring hole into the shot chamber. The cold chamber machine is quite similar to the hot chamber in terms of its intended purpose; however, it is horizontally oriented and does not have a gooseneck.
Why are Zinc alloy die casting parts best?
Zinc die casting is used for building and industrial parts, but its most prevalent use is in the automobile industry. Die casting was initially developed for the automobile sector to make car parts. Die casting with zinc alloys facilitates the creation of sturdy, long-lasting goods while streamlining production. Due to its durability, ductility, and stability, zinc has a longer lifespan than other materials. Zinc’s high flexibility makes it an ideal material for die casting, which requires a substance that can endure pressure and expansion without cracking.
- Superior Precision: Aluminum may be the lighter material, but zinc casting makes it far easier to achieve pinpoint accuracy. Other materials typically require additional machining, whereas zinc can be die cast to the exact requirements of the final product. Zinc is easier to form, and zinc alloys are simpler to a machine if additional work is required following die casting.
- Value for Money: Zinc materials are initially more expensive than other materials because of the alloy’s outstanding quality. This is the case because other elements necessitate cold chamber die casting, which is less efficient than hot chamber die casting. Not only will zinc die casting be less expensive, but these components will also endure longer, so you will gain more excellent value for your money. Zinc alloys are also economical for manufacturing small parts.
- Better Tool Life: Zinc is considerably more rigid and robust than other elements, which means that tools made from it last significantly longer. Due to this, zinc die cast tools have a far longer lifespan than other elements. The lifespan of these parts can be extended by a factor considering the advantage of using Zinc alloys. Because of this, less material will need to be produced, saving businesses money in the long term.





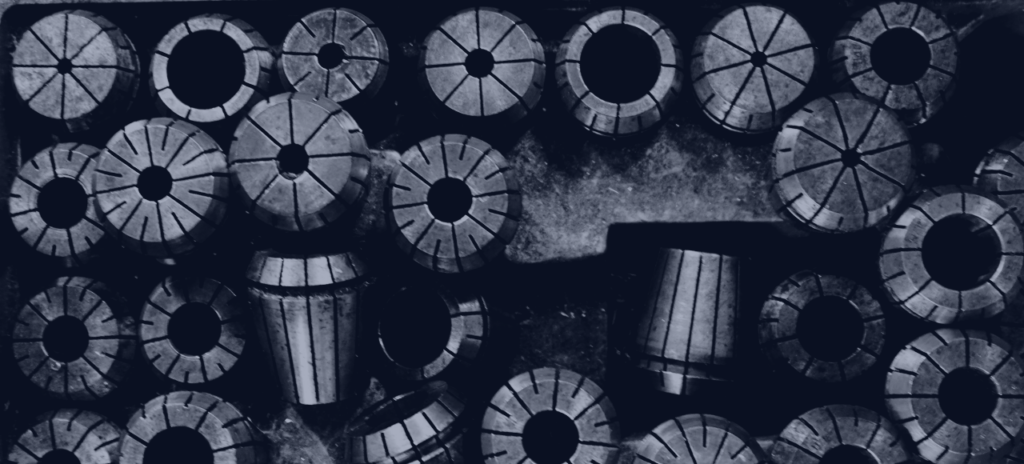
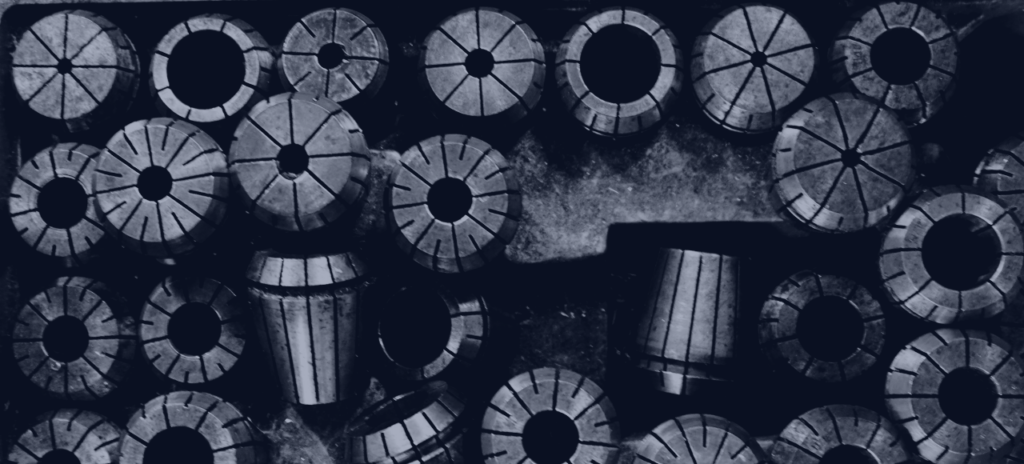
Types of Zinc alloys used by manufacturers in die casting
Zinc alloys are commonly used in the die casting process due to their excellent casting properties, ease of casting, and good mechanical properties. There are several types of zinc alloys that diecast manufacturers may use, including:
- ZAMAK 3: Due to its combination of overall strength, impact strength, and ductility, it is the most popular and commonly used Zamak alloy. In addition, it has superior plating options and consistent finishing properties. Additionally, long-term casting stability is given. To this day, ZAMAK 3 remains the most widely employed zinc alloy for die casting. With its high degree of purity and high-quality mechanical qualities, it may be used in a variety of settings.
- ZAMAK 5: One disadvantage of the increased copper concentration is the decreased ductility, which makes it more difficult to shape than other alloys. The increased aluminum content of the ZAMAK 5 alloy, compared to ZAMAK 3, increases its strength and hardness. This material is frequently employed in demanding settings.
- ZAMAK 2: A higher Copper percentage makes the alloy substantially stronger than other Zamak alloys, but it may need to be more durable. Additionally, it is the most expensive zinc alloy. Casting is the primary use for Zamak 2 due to its excellent creep performance, which enables it to tolerate the pressure applied during the die casting process. Compared to ZAMAK 3, ZAMAK 2 alloy’s high copper content makes it more robust and corrosion-resistant. It has many uses outdoors, particularly in the sea and other marine contexts.
- ZAMAK 7: This zinc alloy has the highest ductility of any zinc alloy. Considerations like the casting material’s decreased magnesium content and higher fluidity are essential in light of this.Allows for the production of more complex components with the option of casting thinner walls inside them.
- ZAMAK 9: The increased copper and aluminum content of ZAMAK 9 alloy, compared to ZAMAK 3, results in greater strength, hardness, and corrosion resistance. It has many uses outdoors, particularly in the sea. Besides these typical zinc alloys, producers sometimes resort to others for more niche uses. Zn-Ni alloys, for instance, are used due to their enhanced corrosion resistance, while Zn-Ti alloys are utilized due to their enhanced strength and flexibility. In general, the strength and corrosion resistance required, the cost and the availability of the alloy all play a role in deciding which zinc alloy to use in a given application.
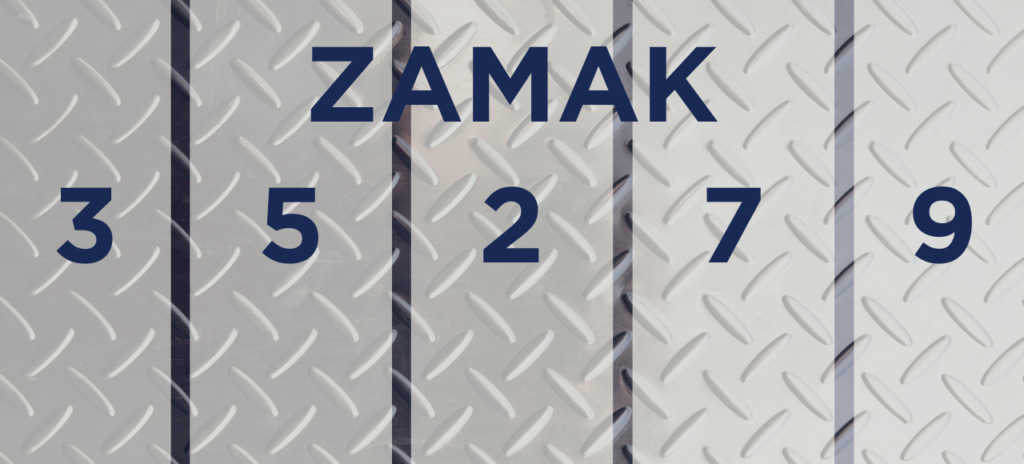
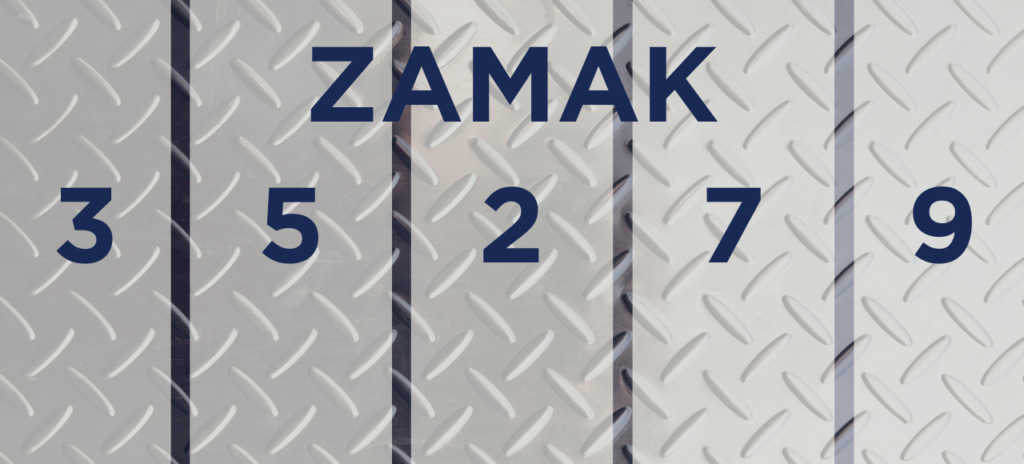
Zinc alloy die casting is just one of the many services offered by Zetwerk, a manufacturer. ZAMAK 3, ZAMAK 5, and ZAMAK 7 are just a few of the zinc alloys that Zetwerk can use to make high-quality die cast parts. Professional engineers and technicians on staff can lend a hand during the design and development phases, and cutting-edge tools and methods are put to use throughout the process to guarantee accuracy and high quality.
Zetwerk provides a wide range of manufacturing services, including zinc alloy die casting, CNC machining, surface finishing, and assembly. Zetwerk has a solid reputation for delivering high-quality components on time and at reasonable costs to various industries, including the automotive, aerospace & defense, and medical sectors. If you’re looking for zinc alloy die casting services, Zetwerk could be a great choice.




