Introduction
Vacuum die-casting, also known as Vacuum-assisted High-pressure die-casting, is an advanced version of traditional pressure die casting. This process utilizes a vacuum die casting system to remove the air entrapped within the die cavity, resulting in improved quality and reduced defects in the final product.
By creating a vacuum during the process, vacuum die-casting ensures uniform filling of molten metal into all recesses of the die cavity. This article provides in-depth knowledge about vacuum die casting for industry professionals, highlighting its advantages over traditional methods such as increased production capacity and enhanced part durability.
Vacuum Die-Casting
Vacuum die-casting is a technique that aims to eliminate air entrapment within the die cavity during the casting process. Similar to traditional die-casting methods, vacuum die-casting involves injecting molten metal into a pre-designed mold or die cavity under high pressure. However, unlike traditional techniques, vacuum die-casting utilizes a vacuum to remove air from the cavity before injection.
There are three primary ways to create a vacuum during the process:
- Injecting metal after vacuum creation
- Simultaneous injection of metal and vacuum creation
- Actuation of metal injection and vacuum creation with sensors
These methods ensure that molten metal fills all recesses evenly while reducing defects caused by air entrapment.
Vacuum Die-Casting Process
The vacuum die-casting process consists of several steps that enable the production of high-quality, defect-free parts.
Metal Melting
The first step involves melting the desired metal alloy using either electric resistance heating or induction heating techniques.
Mold Preparation
Once the metal is molten, it is transferred to a shot chamber using a plunger or ladle based on whether it’s a hot chamber or cold chamber die-casting machine. The mold or die cavity is cleaned and coated with a release agent to prevent sticking.
Vacuum Creation
After the mold is ready, a vacuum is created within the mold cavity using one of the three methods mentioned earlier. This ensures the proper removal of entrapped air.
Metal Injection
Once the vacuum is established, molten metal is injected into the die cavity under high pressure. The vacuum aids in filling all intricate details and recesses uniformly.
Solidification and Ejection
After injection, the metal cools and solidifies within the mold. Once it reaches sufficient strength, the part is ejected from the mold for further processing or finishing.
Advantages of Vacuum Die-casting
Vacuum die-casting offers several advantages over traditional methods:
- Reduced porosity in castings due to minimal air entrapment
- Elimination of surface defects like blisters and blowholes caused by air entrapment
- Improved mechanical properties due to reduced porosity
- Ability to cast thin walls without miss-run issues
- Increased production capacity by reducing post-processing operations
- Minimized waste due to fewer defective parts
- Enables heat treatment and welding for certain metal alloys
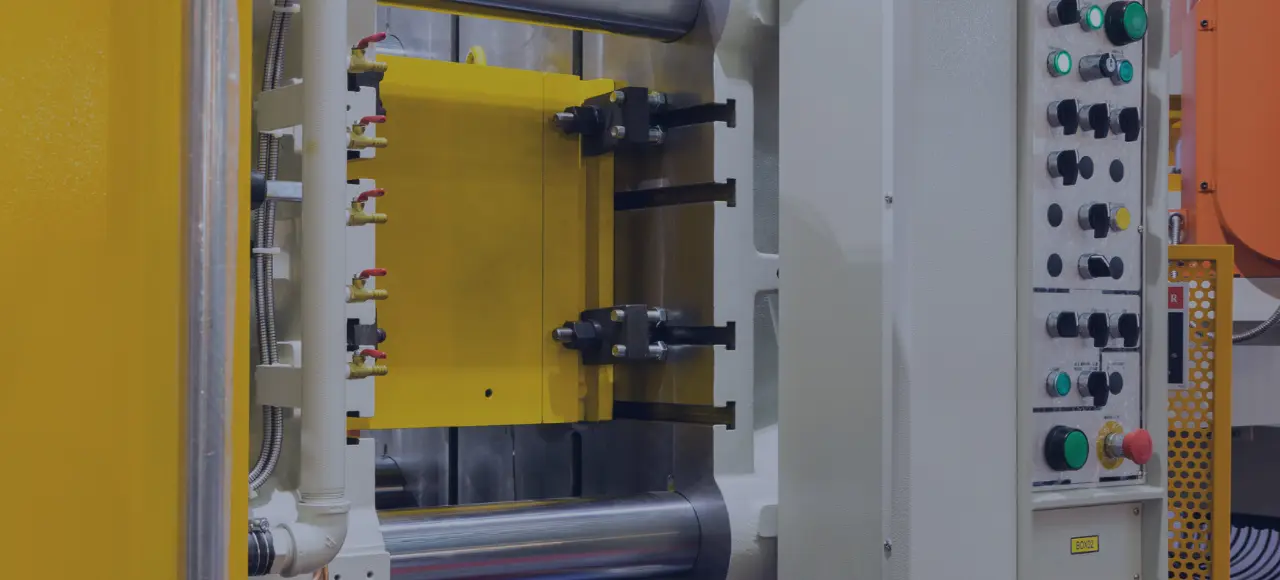
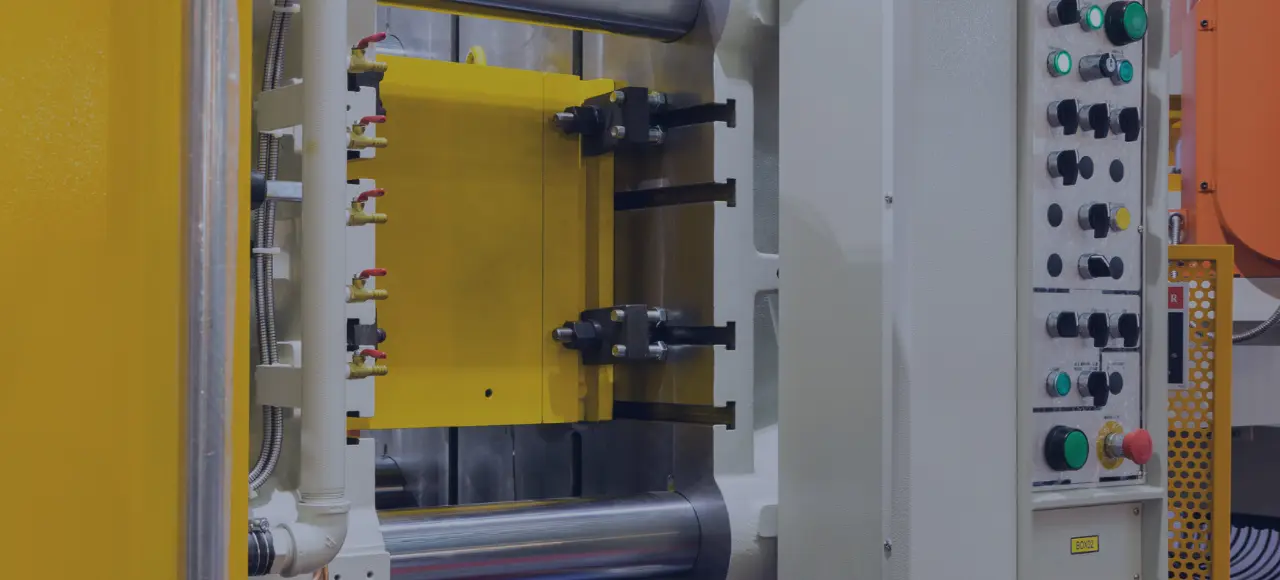
Industrial Applications of Vacuum Die-Casting
Vacuum die-casting finds extensive applications across industries that demand high-quality and durable parts. vacuum die-casting techniques, these industries can ensure the production of high-quality parts that meet specific requirements for strength, precision, and durability. Here are some notable sectors that commonly utilize this advanced casting technique:
Automobile Industry
Vacuum die-casting plays a crucial role in automotive manufacturing, producing components such as engine blocks, transmission cases, intake manifolds, suspension components, and more. These parts require high precision, dimensional accuracy, and excellent mechanical properties.
Aerospace Industry
Vacuum die-casting aluminum meets stringent requirements for aerospace applications by producing parts like turbine blades, structural components, fuel system parts, and more. The process ensures reliable performance under extreme conditions while maintaining weight reduction goals.
Military Sector
In military applications, vacuum die-casting is used to manufacture critical components like weapons systems, armor plating, and other defense-related parts that require precision and durability.
Marine Industry
Vacuum die-casting produces marine components such as propellers, engine parts, and ship fittings. The process provides high-quality parts with excellent corrosion resistance for enhanced performance in harsh marine environments.
Construction Sector
Vacuum die-casting is utilized to produce construction components such as brackets, connectors, and structural elements. These parts need to be strong, durable, and capable of withstanding heavy loads.
Key Takeaway
Vacuum die-casting offers numerous advantages over traditional die-casting methods. By creating a vacuum during the process, this advanced technique reduces defects caused by air entrapment and ensures uniform filling of molten metal into intricate details. This results in improved part quality and mechanical properties while reducing porosity in castings.
With its ability to produce thin-walled components without miss-run issues and increased production capacity by minimizing post-processing operations, vacuum die-casting is a valuable solution for industry professionals seeking high-quality parts. Consider implementing this advanced process to enhance your manufacturing capabilities.
If you’re interested in learning more about vacuum die-casting and other advanced manufacturing processes, check out Zetwerk’s Knowledge Hub. Discover articles that provide comprehensive information on various techniques used in the industry. Expand your knowledge and stay updated with the latest advancements in manufacturing.




FAQs
A vacuum-assisted die-casting system is an upgraded version of traditional pressure die-casting that uses a vacuum to remove the air entrapped within the die cavity, resulting in improved casting quality and reduced defects.
The vacuum die-casting process differs from traditional methods by incorporating a vacuum during the process. This helps in removing air from the die cavity, ensuring uniform filling of molten metal, reducing porosity, and improving the mechanical properties of castings.
Using a vacuum in die-casting offers several advantages, including reduced porosity, elimination of surface defects caused by air entrapment, improved mechanical properties due to reduced porosity, increased production capacity by reducing post-processing operations and minimized waste due to fewer defective parts.
Yes, vacuum die-casting can be used for aluminum alloys. Vacuum-assisted high-pressure die-casting is suitable for various materials including aluminum alloys, offering improved quality and reduced defects compared to traditional methods.
Some challenges or limitations of vacuum die-casting include unsuitability for materials sensitive to heat or pressure, potential shrinkage issues resulting in parts being too thin or too thick, relatively slower speed for large-scale production runs, and limitations for high-temperature applications.